Dow Automotive Systems is a provider of polyurethanes, elastomers, films, fluids, adhesives, emissions solutions and acoustic-management materials to the global transportation industry. Matthew Beecham spoke to Eugenio Toccalino, Director of Strategic Marketing, Dow Automotive about structural foams and adhesives and the ways in which the supplier is helping OEMs make cars lighter.
What new and potential automotive applications are there for structural foams?
Foam filled structures have been evaluated across many automotive manufactures for years and are still in place today, hence we consider the technology proven and robust. New impulse to adoption is driven by recent introduction of stringent crash requirements, such as NAA IIHS small off-set frontal test and vehicle roll-over – including new bus requirements enforced in China. We see increasing interest in the crash body repair channel beyond first fill, therefore we have developed new formulations and small packaging (e.g. Betafoam SR not requiring fixed capital investments) allowing easy prototyping/testing and perfect fit with smaller built or commercial transportation, crash body repair needs. Dow automotive has developed expertise, CAE design criteria and simulation tools that can enable customer integrating structural foam early on in vehicle design, maximising its benefit.
As we understand it, Dow Automotive worked with Faurecia to develop a new type of foam for vehicle seat backrest. What triggered this innovation and what’s different about it? Is there potential for its use in other seating applications?
The main market driver is to achieve the best seating comfort at the lowest foam density, meeting the most stringent cabin air quality requirements. As a leading polyurethane supplier, Dow participates in all technology spaces – i.e. MDI and TDI – being truly unbiased. Faurecia approached us looking for the best solution. We identified the unmet need in TDI-based foam addressing comfort and low density requirements, yet missing on key low emission requirements. The solution is Specflex Activ, an additive polyol enabling a dramatic decrease in overall volatile organic compounds (VOC)/odor for TDI foams. Specflex Activ eliminates all amine emissions and maintains excellent physical and mechanical properties including humid ageing. Other significant process improvements include the possibility to blend with other polyols / additives, easy handling with EH&S restrictions, open and easy to crush foams, and excellent flow and moulding. We found Specflex Activ can help address the most challenging emission requirements, beyond those originally targeted (German OEMs), and can also experience improved performance beyond seating applications. This is a perfect example of collaboration with our customer in a partnership mode to address major industry unmet needs.
To what extent are bonding solutions taking over from conventional fastening applications such as fixing screws?
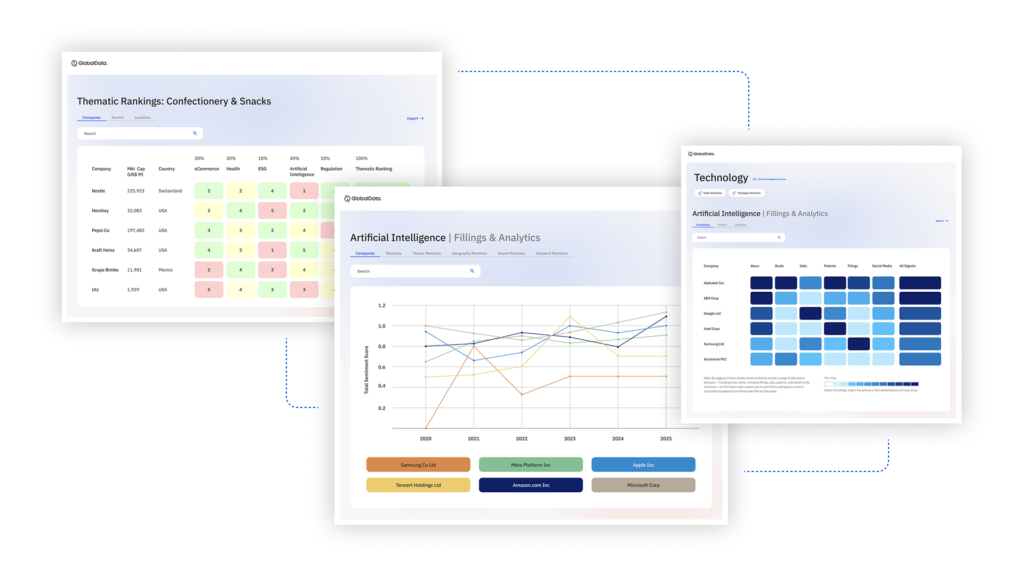
US Tariffs are shifting - will you react or anticipate?
Don’t let policy changes catch you off guard. Stay proactive with real-time data and expert analysis.
By GlobalDataFirst of all, the most commonly used assembly technology in automotive body construction is spot welding. In metal-intense construction, we don’t expect bonding solutions to immediately substitute, but instead complement conventional fastening. Bonding solutions can be used to lower the number and location of conventional fastening and joining, mitigate galvanic corrosion between dissimilar materials such as steel and aluminium, and increase the load carrying ability at a lighter weight while improving ride, handling, comfort and safety. Crash durable structural adhesive is an essential enabler of multi-material and/or light weight substrates assembly, that cannot be welded or where mechanical fastening would induce cracks leading to loss of load carrying ability or fatigue damage. Dow brought structural adhesive assembly to the automotive market at the end of the ’90s, and as the market and technology leader to date we have demonstrated the superior performance across major OEMs and vehicle lines globally. Our most notable recent innovation examples include the BMW i3 carbon fibre composite occupant cell, bonded with Betaforce in the trim shop (without additional mechanical fastening) and the 2015 Ford F150, whose innovative military grade aluminium is assembled using Betamate in the body shop.
Making a vehicle body structure lighter from dissimilar materials makes good sense, of course. Yet to what extent does that pose challenges when joining increasing number of different types of structural materials? And what are the considerations?
You are perfectly right the potential is significant, as are the challenges. From a technical stand point some of the challenges include surface energy, wetting and adhesion compatibility to multiple materials, dimensional stability before and after full cure of adhesives, differences in coefficient of thermal expansion and galvanic potential … just to name the main ones. I am very optimistic though. Over the last 15 or so years, we have collected tremendous know-how and expertise that we have built into robust processes and capabilities underpinning our formulation methodology. Capabilities like CAE modelling, scale up, manufacturing across our development canters of excellence, customer service labs and production facilities spread across all active OEM geographies support our global customers. That is the reason why when lead customers are confronted with development challenges they call us. With adhesives being designed initially into so many vehicles, a critical need is to include them in the appropriate repair protocols. That’s why we are routinely developing customised repair solutions capable of bringing a vehicle back to its original performance after a professional repair.
Finding ways in which to make cars lighter has been the focus of automakers for decades. Some would argue that the easier-to-implement routes to shedding weight have already been done. So I guess that using structural adhesives to bond lightweight materials is now the focus in order to achieve the 2025 CAFE standards. What is your view?
I agree with you that low hanging fruits have in part been harvested, and now each new kilogram saved is more difficult to deliver. At the same time with “cheap gas” we are witnessing a boom of large SUVs, pick-up trucks and premium vehicles making customer buying preference more affordable, and the consequence has been a slow down in the rate of CO2 and MPG improvement at fleet level versus recent years. This trend has accelerated OEMs pressure to more aggressively drive sustainable solutions, along with light weighting All that said, OEMs cannot compromise on vehicle performance, and this means that while they reduce mass to meet fuel economy targets, solutions must be developed that meet the safety, noise and vibration requirements as well. I remain very confident since Dow and our customers have developed the right tools to integrate and maximise structural adhesive impact early on in vehicle development. The untapped potential of advanced high strength steel grades, lightweight alloys and carbon fibre composites is still all in front of us, with huge opportunities coming from true adoption of multi-material assembly. We have multiple customer projects in different stages of development to truly enable “the right material at the right place” in large volume productions, ideally integrating the assembly early on in the body shop.
Generally-speaking, is there a premium that OEMs will pay for weight reduction? Maybe there is a bifurcation to this question: (a) what premium have OEMs been willing to pay up until today, and (b) what future premium is expected as 2020 CO2 regulations draw near?
The remainder of this interview is available on just-auto’s QUBE Global vehicle lightweighting – technology, trends and the future