Though today’s new vehicle development programmes are more comprehensive than ever, using exhaustive virtual and ‘real world’ testing, issues can still escape into the market place. just-auto spoke to Mark Findlay of UK engineering consultancy Drive System Design about a new approach to reducing warranty costs.
How significant are warranty costs to the OEM and why?
Warranty costs typically account for 3 to 5 percent of vehicle total costs, equivalent to EUR200-1000 per vehicle. Having driven down other cost sources through advanced design techniques and efficient manufacturing processes, warranty remains a key area for additional savings. Shrinking timescales for model introduction increase the likelihood of warranty issues while the wider use of global platform sharing increases their impact.
How have warranty issues changed in recent years?
Consumers increasingly perceive refinement as a sign of quality and we have found that, as reliability has increased, a growing number of warranty issues are now down to NVH. The problem has been compounded by the expansion of hybrid and electric vehicles in the market, where the deletion of the internal combustion engine has made reaching acceptable NVH levels a challenge for engineers. These are often late emerging issues so solutions are normally a patch rather than a complete re-design.
How does a consultancy like DSD differ from an OEM in its approach?
How well do you really know your competitors?
Access the most comprehensive Company Profiles on the market, powered by GlobalData. Save hours of research. Gain competitive edge.
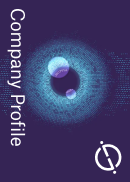
Thank you!
Your download email will arrive shortly
Not ready to buy yet? Download a free sample
We are confident about the unique quality of our Company Profiles. However, we want you to make the most beneficial decision for your business, so we offer a free sample that you can download by submitting the below form
By GlobalDataWe see more variety through working with such a wide range of vehicle manufacturers and tier one suppliers on their driveline systems. Whatever technical issues arise, we have probably solved something similar before, so already understand the root causes. By contrast, as the number of completely new platforms and powertrains reduces through platform sharing, the range of experience gained by individual OEM engineering departments is falling.
What’s new about your approach? Surely there’s no magic bullet?
There is no magic bullet, certainly; the source of a warranty issue could be traced to the introduction of a new technology, the requirement for uprated performance from an existing system, or even the production of an established design at a new manufacturing site. What’s new is the recognition by customers that our ability to support them extends beyond providing concept design and analysis, to routinely addressing urgent issues on vehicles already in production. I think they are often surprised by our grasp of the practical manufacturing issues and the speed with which we can react.
Can you cite some examples?
In one example, an OEM was experiencing an abnormally high total failure rate of production vehicles (end of line test and warranty returns) due to unacceptable vibration of the gear selector lever. We assessed the performance of ‘good’ and ‘bad’ sample units by rig testing and exhaustive analysis of the production tolerances and established that a complex combination of run-out and backlash was leading, in some cases, to oscillation of a particular selector sleeve. By recommending tighter tolerances in the critical areas, we eliminated the issue and the client is now implementing the changes in production.
In another case, we visited a customer’s dealerships to observe and improve how the warranty team approached its diagnostics. We were able to identify a sub-system that was causing an issue and tracked this back in to the production line, where an electric tool that allows accurate torque control of bolt tightening, was not specified. This was replaced for a tool with better torque control and as a result five common customer concerns were resolved.
Sometimes the trend towards flexible global manufacturing, intended to reduce costs, may lead to failure to precisely replicate the validated production processes at every plant. In one example, the process of changing manufacturing facilities for a transfer case resulted in a spate of warranty returns. We designed a low level repair kit to allow dealerships to implement a cost-effective warranty repair.
In an era when testing has never been more comprehensive and quality systems are more robust than ever, how is it that some issues can still reach the customer, resulting in warranty claims?
The remainder of this interview is available on just-auto’s QUBE Global light vehicle steering market- forecasts to 2030