In this interview, Matthew Beecham talked with Arnaud Gandon, chief engineer, global powertrain cooling and heat exchangers, Delphi Thermal.
just-auto: What are the factors driving the automotive powertrain cooling sector? e.g. cost reduction pressures, engine down-sizing, emission standards, etc.
Arnaud Gandon: There are several factors driving changes in the powertrain cooling sector. From a technology standpoint, the increasing demand for more diesel, turbo-charged engines and hybrids is driving new and improved technology along with more efficient transmissions that sometimes require heating as well as cooling. Global regulations on fuel economy and CO2 emissions are also impacting powertrain choices.
From a packaging point of view, Delphi expects that there will be a need to combine heat exchangers like the combicooler as well as wider use of charge air coolers. There is a legislative push to capture the heat from the exhaust and use it for cabin heating or transmission heating. For hybrids, there is also a need for a new heating source like an immersion PTC heater which drives electronics for operation and safety.
Finally, the increased automotive demand in Brazil, Russia, India and China along with the growth of global mega platforms also demand changes in the powertrain cooling sector.
just-auto: Demands on powertrain cooling product performance are continually increasing. In addition, automakers expect economical solutions that help reduce emissions from cars and trucks. With these demands in mind, how have you responded?
How well do you really know your competitors?
Access the most comprehensive Company Profiles on the market, powered by GlobalData. Save hours of research. Gain competitive edge.
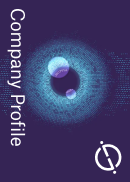
Thank you!
Your download email will arrive shortly
Not ready to buy yet? Download a free sample
We are confident about the unique quality of our Company Profiles. However, we want you to make the most beneficial decision for your business, so we offer a free sample that you can download by submitting the below form
By GlobalDataArnaud Gandon: Both Delphi’s new radiator portfolio and aluminum in-tank oil cooler portfolio have best in class heat transfer per mass performance.
just-auto: As you know, packaging is becoming tighter in the vehicle front-end resulting in the requirement for more efficient heat exchangers. How have you responded to that?
Arnaud Gandon: Delphi has consistently worked to improve technology packaging. As a result, radiator development over the last decade has decreased core depth by almost 50% for equal heat transfer. Additionally, development of compact clinch technology has reduced the manifold (tank and header) package depth by over 40%. Finally one of the most valuable space savers has been the introduction of remote oil coolers, which significantly reduces tank depth by eliminating the need for in-tank oil coolers.
just-auto: I guess other changes regarding the increasing pressure cycle has led to design changes to the radiator itself. Is that correct? What changes have occurred there?
Arnaud Gandon: Delphi has developed a new series of high strength aluminum alloys to meet these new OE customer requirements.
just-auto: In what ways have you addressed the trend for two stage turbocharging applications?
Arnaud Gandon: First, it is important to remember the meaning of dual-stage turbocharging.
Depending on customer demand (drivability or performance), there are two different ways to manage dual-stage turbo charging. In both cases, system architecture is a combination of two turbochargers placed in a series:
In order to achieve better drivability, the first stage (usually small turbo) is used to decrease turbo lag during transient behaviour while the second stage is acting without compromising the maximum boost output and engine power. The transition between the first and second is managed using a bypass valve.
Other configurations do not use the bypass valve. It helps to increase the boost pressure and consequently the engine power. In this case, the pressure ratios of the two compressors are multiplied.
Delphi is currently working on several twin charger applications. On one application, the customer is looking for drivability and performance on the same system. The system is made of a Full Face combined charge air cooler divided into two sections (the first section represents one third of the total surface and the second two thirds). The outlet of the first section is connected to the inlet of the second one by a valve. The Low Pressure Turbo (LPT) is acting during the transient phases. In this case, the charge air mass flow is cooled by the first CAC and goes to the second CAC through the valve. When the power is requested, the charge air mass flow already cooled by the first section is compressed again by the High Pressure Turbo (HPT), and cooled on the second CAC by bypassing the valve. Delphi will develop this CAC with the valve located on the plastic tank.
just-auto: In what ways does the EGR impact on the engine cooling system? i.e. for instance, is there a need for additional engine cooling due to the load the EGR puts back into the engine coolant.
Arnaud Gandon: EGR drives a need for increased cooling capacity. In addition, it also drives the need for high-temperature corrosion resistant alloys and non-fouling heat transfer surfaces.
just-auto: I guess the need to realize cooling of the EGR, either for emissions benefits on a diesel engine or fuel economy improvement in a gasoline engine, has a significant impact on the cooling system. How do you achieve that?
Arnaud Gandon: Environmental pollution caused by the engine combustion process is leading automotive manufacturers to search for emission reduction solutions. Driven by successive legislation, NOx generation during combustion is a concern for all OEMs. Many system architectures can be implemented in order to meet stringent NOx targets: a pre-treatment technique, which consists of limiting NOx production by pre-conditioning the air mixture that is delivered to the engine combustion chamber and a post-treatment solution which reduces the quantity of NOx after its formation by means of SCR or NOx trap systems.
Numerous architectures and components are possible with the pre-treatment technology, including a high and/or low pressure EGR loop and air-to-air or liquid cooled charged air cooler. One possible pre-treatment architecture, developed by Delphi, consists of a combination of EGR cooler and liquid cooled charged air cooler where both heat exchangers are cooled down by a secondary coolant loop for which the 50/50 water/glycol media temperature is lower than the engine coolant. Results demonstrated a significant improvement in NOx reduction, sufficient to meet the Euro 6 target.
just-auto: Although hybrids have not really created a substantial change in the heat transfer philosophy of the engine, has this technology created the need for additional product on the electronic side of things?
Arnaud Gandon: Delphi has and continues to develop a wide variety of heat exchangers to manage these new thermal loads. We continue to develop combi-coolers, low temperature radiators, chillers, heat sinks for electronics cooling to address the needs of hybrids.
just-auto: Generally speaking, in respect of fuel economy, is there a trend toward more use of electronics to try to more closely monitor engine temperature for maximum efficiency? i.e. perhaps using electronic thermostats and electronic water pumps to completely take control of the heat rejection itself. But I guess there is always a trade-off the carmaker must make between adding weight and cost (through electronics) and saving fuel.
Arnaud Gandon: There is a trend to monitor engine temperature. Delphi has responded to that trend by developing temperature measurement capability on heat exchangers.
just-auto: With pedestrian safety laws swinging into force in Europe, how does that impact on engine cooling system design? i.e. smaller modules, thinner radiators, etc.
Arnaud Gandon: Delphi has developed thinner heat exchangers. This has enabled vehicle front end designs to be compatible with government regulations.
just-auto: The popularity of diesel engines in the European market coupled with the new emission standards is presumably causing new developments in charge air coolers. Any observations there in terms of what is happening with charge air coolers? And how has Delphi responded in terms of innovations?
Arnaud Gandon: To meet these new standards, Delphi has developed more effective charge air coolers and is developing more effective EGR coolers. For example, a new range of liquid cooled charge air coolers (LCCACs) from Delphi will help global vehicle manufacturers of both gasoline and diesel engines produce environmentally-friendly vehicles with better engine performance. Compared to existing air-cooled units, the new coolers offer better packaging, improved engine response, faster warm-up and lower losses.
The versatility of Delphi’s LCCAC technology allows the coolers to be incorporated into the ducting between the turbo/super charger and the engine or integrated into the intake manifold, minimizing air-pressure losses through the cooler and improving engine bay layout. To provide vehicle manufacturers with additional packaging flexibility, Delphi’s wide range of heat exchangers can be modified for specific applications to fit any size and shape of engine.
Unlike an air-to-air charge cooler, a LCCAC requires no large diameter elastomeric tubing to route the charge air to and from the cooler, further improving packaging and eliminating large diameter connectors that can lead to warranty problems. Engine response to sudden throttle demand is improved because of the smaller volume of intake air between the boosting device and the engine in a liquid cooled system. Additionally, the intake air stays cooler during acceleration because the liquid cooled charge cooler heats up more slowly. This higher thermal capacity also helps to limit peak NOx emissions during transient driving conditions by maintaining cooler inlet air temperatures.
Further emissions benefit is derived under cold start conditions, as coolant flow to the LCCAC can be limited to increase engine warm-up rate. On gasoline engines, during partial load conditions when engine efficiency falls due to throttling losses, coolant flow can also be limited to heat the intake air, reducing its density and allowing a greater opening of the throttle valve and, hence, reducing the losses.