Continuing just-auto’s series of interviews with tier one manufacturers, Matthew Beecham spoke to James Zizelman, engineering director gasoline powertrain, Delphi about fuel injection systems and Andrew Lasley, director electronic controls advanced engineering, Delphi about electric vehicles.
In terms of trends in injector technologies, what are you seeing at the moment?
James Zizelman: One key development is Delphi’s laser processing method for spray hole formation. This technique offers increased hole formation flexibility, improves precision through reduced variability, and offers excellent surface finish characteristics for lower injector deposit formation tendency and superior spray preparation.
A second key development is in the area of spray and fuel control. Combining injector design and control schemes we continue to improve our capability to deliver multiple, closely-spaced and carefully placed small fuel pulses. Recent engine management system work shows very promising results for meeting the Euro 6 PN standard in a 4-cylinder turbocharged GDi engine with side-mounted injectors.
A third area of development is our activity to provide increased fuel system pressure. Customers are showing increased interest in systems with increased fuel pressure primarily for better control of toxic emissions. Our development efforts include pumps and injectors optimised for operation at fuel pressures of 350+ bar. Start of production for Delphi fuel systems with 350+ bar capability is scheduled for 2016.
What developments is Delphi doing with respect to injector technologies for alternative powertains?
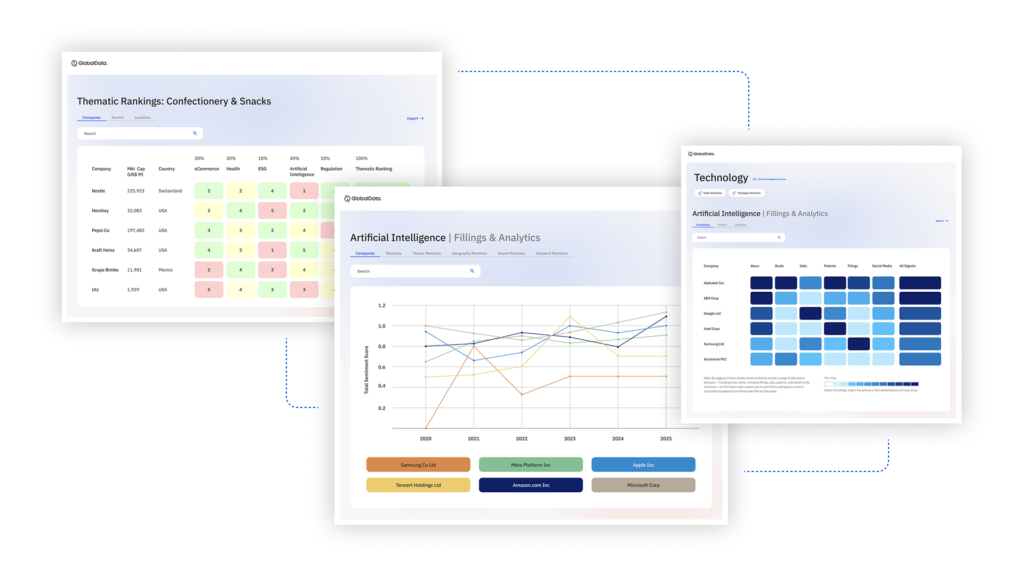
US Tariffs are shifting - will you react or anticipate?
Don’t let policy changes catch you off guard. Stay proactive with real-time data and expert analysis.
By GlobalDataJames Zizelman: We are working strongly in the area of CNG. We have introduced a very effective injector applied as a conventional port fuel injector. It provides extremely high precision and durability, and enables the powertrain to deliver approximately 25 percent improvement in CO2 emissions as compared to a standard gasoline engine with port fuel injection.
We have in development a direct injection CNG injector as well. This injector provides all of the benefit of conventional CNG injectors, but additionally allows the OE to address the torque loss associated with most CNG applications, addressing the performance concern that arises utilising this type of fuel.
We continue to develop injection systems for a number of alternative powertrains, including those for alcohol application, stratified charge applications, as well as our GDCI combustions system.
Delphi is first to market with a heated tip engine cold start system that includes an innovative fuel injector and a control system for ethanol-fueled vehicles. Delphi’s Multec Heated Tip Cold Start System rapidly heats ethanol to dramatically improve its vaporization characteristics. The system controller regulates power to a thermal conductor contained within each injector. The injector heaters quickly raise the temperature of the delivered ethanol during the engine crank and initial run. When these heated injectors are employed in conjunction with engine management system enhancements, ethanol cold start performance is similar to that of gasoline, eliminating the need for a redundant fuel system. By enabling reduced fueling during engine warm-up, these injectors also offer significant reductions in engine and tail-pipe emissions.
It appears that OEMs are slow to adopt gasoline particulate filters. Why is that?
James Zizelman: When considering emissions performance, it is important to understand that a systems approach offers the best, most cost effective solution. For GDi engines, meeting the proposed particulate number (PN) standard is a key challenge for Euro 6. For cost and performance reasons, it is preferred to meet the PN standard without a gasoline particulate filter. Careful injector design and controls to enable multiple closely-spaced and carefully-placed small fuel pulse capability within the overall engine management strategy is a critical enabler for PN levels required to meet the Euro 6 standard. Additionally, injectors that resist deposits are also essential to ensure low PN emissions over the full lifetime of the fuel system.
In the US, California LEV-III and proposed EPA Tier 3 standards require very low toxic emissions. The proposed reduction of sulphur concentration in gasoline to 10 ppm (max) is very important to ensure exhaust aftertreatment systems maintain high conversion efficiency and fast light off capability over their entire lifetime. Additionally, as emissions standards get tighter, ensuring very low cold start emissions is critical. GDi systems offering precise, well-placed fuel control are therefore essential.
In the longer term, I guess that stratified DI, alternative combustion systems and gaseous DI are all potential candidates for further CO2 reduction?
James Zizelman: Yes, all are being considered and developed by engine developers. Each technology will need to be considered for effectiveness and value while keeping in mind infrastructure and implication to the vehicle architecture. As we see global execution of the more stringent CO2 and fuel economy standards, each of these will play a role in helping the OEs meet the requirements established by government and demanded by customers.
It is clear that HCCI technology offers superior fuel efficiency and emissions control compared to the conventional spark ignition gasoline engine. Yet what is not so certain is the ability of these engines to deliver characteristics inexpensively and reliably over the life of the vehicle. What is your opinion of how HCCI technology can meet the requirements?
James Zizelman: HCCI is a fundamentally sound technology. The larger issue is how effective the technology can be in truly delivering the fuel economy savings. In HCCI, the engine will operate in a standard mode and the HCCI mode. When operating in the standard mode, there are effectively no fuel economy savings achieved. Unfortunately, for HCCI, the engine speeds and loads over which HCCI is usable is limited, reducing the overall improvement in economy from this technology. OEs are still developing and driving a broader operating range. The limitation has also driven new technologies like Delphi’s GDCI (Gasoline Direct injection Compression Ignition) which has proven itself to operate over a much broader range of engine speeds and loads.
Whichever way you look at it, electric vehicles remain expensive despite government grants being offered yet still give motorists range anxiety with just 100 miles between charges. What needs to happen to EV batteries to improve this situation?
Andrew Lasley: Cost and charging times need to come down dramatically. Tesla has proven that if you put enough battery on board that you can reduce range anxiety, but it comes at a price. For wider use you also need to improve upon the extended charge times required by present day EVs. The bottom-line for batteries though is cost, cost and cost.
What needs to happen to make electromobility affordable? Presumably that includes things like standardisation of components?
The remainder of this interview is available on just-auto’s QUBE Global light vehicle engine technologies market- forecasts to 2030