Driver-in-the-loop simulation is becoming more widespread among automotive OEMs and Tier 1 suppliers, not least because the latest data gathering and modelling methods mean virtual road test routes can be created more quickly and accurately. Dutch company, Cruden, is a leader in the design and manufacture of vehicle simulators for automotive testing as well as the building of road, tyre and vehicle models. just-auto spoke to Nico Kruithof, a computer scientist working at the forefront of developments to make motion simulators an essential part of the vehicle dynamics evaluation programme.
What are the big changes you see in the automotive industry?
It is now possible for OEMs to test their vehicle models in the simulator, using a very meaningful, accurate model of their real local road test route. Previously, it would not have been possible to process the data of a typical 30 km road route and they had to use off-the-shelf, fictive roads and scenarios. It’s no surprise that test drivers didn’t think much of simulators when presented with those visuals.
But now we have LIDAR scanning techniques, 64 bit computers, more expertise and new levels of automation to process all the data. Moreover, the costs for all this are coming down so it’s more affordable for OEMs to validate their vehicle models using roads that they know. Using LIDAR data in a simulator adds realism to the driving experience in the simulator.
This means key decisions can be taken earlier in the design process. Simulation can help engineers to make educated choices about fuel tank locations for example without the need to build a mule. This is all great news for driver-in-the-loop simulation.
We’ve taken the approach of modeling from motorsport into the automotive sector. We have produced many international race tracks to the levels of accuracy required for the highest levels of motorsport, including Formula 1. Now it’s all about scale.
How well do you really know your competitors?
Access the most comprehensive Company Profiles on the market, powered by GlobalData. Save hours of research. Gain competitive edge.
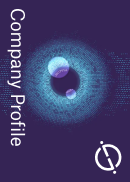
Thank you!
Your download email will arrive shortly
Not ready to buy yet? Download a free sample
We are confident about the unique quality of our Company Profiles. However, we want you to make the most beneficial decision for your business, so we offer a free sample that you can download by submitting the below form
By GlobalDataBut modeling roads must be a lot different from race tracks?
Absolutely. You could be talking between 5 and 10 times more data because of the length of the route. Plus roads have more bumps to define and the area of the road is much bigger. You have to use mobile scanning methods for the roads, which we can’t close off to the public, whereas we have static, more accurate scanning equipment for a track. As a result, we need to be clever with how we process the less accurate data from a mobile scan. I am not saying that all the learning has been done yet. But we are learning and improving day by day.
What happens when you get all the data?
We take the scans of every 100-150 mm of the road and align them to create a huge point cloud, a 3D model of the entire track. We then pre-process this model, filtering the data to remove ‘noise’ and to enhance it. I build the algorithms to do that.
You have to be careful to avoid losing important small details when eliminating the noise – we don’t want to lose that detail. If you do too much filtering, you might lose the road markings or bumps that are crucial to the test driver’s experience. On the other hand, we need to tell the model that the spikes of grass in a verge should not give the effect of driving over a hard metal spike! It can be quite a manual process sometimes, seeing the behaviour of the points and how they come together to form a surface.
What is the most crucial part of road modeling?
It’s as the driver feels the interaction of the road surface through the tyres – the height of the wheel over the track and its relative position, the hit routine and tyre contact patch as the different parts of the tyre runs over the data. In the end, this is where the extra realism is added to the driving experience. You can invent all kinds of smart algorithms for road interaction, but in the end the driver only feels how the car responds and this is more realistic thanks to LIDAR data.
Why is it important for Cruden to do all this work itself?
The remainder of this interview is available on just-auto’s QUBE Global light vehicle steering market- forecasts to 2030