There are many factors shaping the global tyre market. Over the last 20 years, the popularity of sport utility vehicles, minivans and crossover vehicles has steadily increased, prompting manufacturers to redesign their tyres. Indeed, the increasing segmentation of the car market has led directly to a more complex tyre market. In response, manufacturers have focused on ways in which to improve tyre dimensions, weight, rolling resistance, noise, and fuel efficiency. Social environmental awareness and advances in tyre technology is also playing an increasingly important role in the definition of tomorrow’s tyres.
In this interview, Matthew Beecham talked with Chuck Yurkovich, Cooper Tire’s vice president of global technology about the future for TPMS, run-flats, intelligent tyres and the company’s unique tool to predict in-vehicle tyre sounds.
just-auto: What is the future for TPMS technology? Do you think that indirect TPMS will become a standard feature on future ESC systems?
Chuck Yurkovich: In Europe, COM 2008/316 – ‘Vehicle Safety & Environment Directive’ has been implemented. The objective of the directive is to lay down harmonised rules on the construction of motor vehicles with a view to ensuring the functioning of the internal market while at the same time providing for a high level of safety and environmental protection. The proposal aims at enhancing the safety of vehicles by requiring the mandatory fitting of some advanced safety features. The proposal also aims at enhancing the environmental performance of vehicles by reducing the amount of road noise and vehicle CO2 emissions from tyres. Finally, the proposal contributes to the competitiveness of the automotive industry by simplifying the existing vehicle safety type-approval legislation, improving transparency and easing administrative burden.
This legislation impacts both vehicle and tyre manufactures. From 2012, all new passenger vehicles will need to have the following systems fitted as standard:
- Electronic Stability Control
- Lane Departure Warning System
- Advanced Emergency Braking System
- Tyre Pressure Monitoring System
Also, tyre manufacturers will need to comply with minimum values in the following criteria:
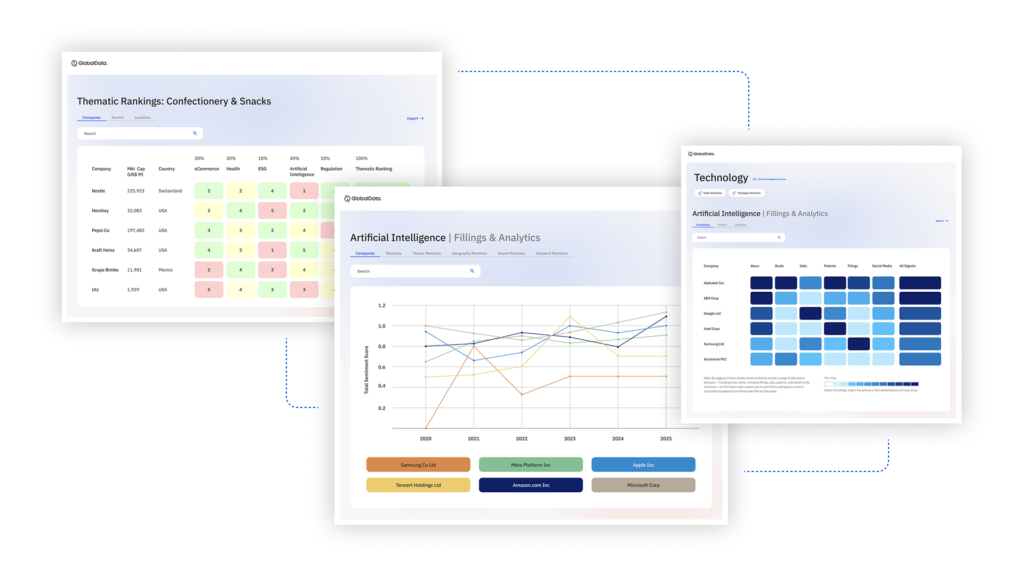
US Tariffs are shifting - will you react or anticipate?
Don’t let policy changes catch you off guard. Stay proactive with real-time data and expert analysis.
By GlobalData- Noise
- Rolling resistance
- Wet grip
Essentially this piece of new legislation will address both the environmental impact of vehicles and tyres and the safety issues as well. So, in Europe, TPMS will be on every new vehicle and it will be up to vehicle and tyre manufacturers to exploit new technologies associated with this enforced legislation.
Indirect systems have several advantages over direct sensor systems including lower initial cost and much lower maintenance costs. They also provide the motorists with much more flexibility and choice for replacement tyres since indirect systems are very tyre neutral. Indirect systems are also very compatible with electronically controlled suspension systems because they utilise the same types of tyre information. On the other hand, indirect systems can’t provide the wealth of tyre specific data that direct sensors, despite their high costs and maintenance issues, are capable of.
In the future, we see tyre sensor technology merging with RFID technology to provide a low cost, low maintenance solution. Instantaneous tyre pressure is only one dimension of the tyre’s operating condition that can be monitored and reported. Tyre ID, running temperature, revolution count, tyre pressure history, including severe under-inflation and overloading, etc., are examples of other types of data that can be monitored, reported or archived by embedded chips and then reported to on-board vehicle systems or external monitoring systems – such as at tyre dealerships. The electronic technology is already here. Cooper has patented technology which we continue to pursue in this field. What is needed are better defined data format standards so that vehicle manufacturers and tyre manufacturers can continue to develop their independent technologies, but so that all components can share the same types of data through common formats.
just-auto: As I understand it, TPMS technology is evolving to the point where one scenario could be this: As soon as the TPMS tells you that your tyre needs servicing, the nearest licensed service station will be automatically alerted through your car’s GPS, giving you directions to a site where qualified personnel will be awaiting your arrival. How far away are we from achieving this?
Chuck Yurkovich: The GPS technology is here today. Regardless of whether or not the tyre service centre is informed of your vehicle’s condition, I’d certainly want my tyre service centre advertised in the GPS software. If a GPS system can show the driver where the nearest fast food restaurant is, it can certainly direct him to the nearest tyre service centre. As a result, we could see this opportunity occurring anytime with consumer awareness.
just-auto: Runflats have also done a lot to improve vehicle safety yet come with a high price tag. Do you see technological evolution bringing runflat and self-inflating tyres into the cheaper mainstream?
Chuck Yurkovich: To the best of our knowledge, there is no new low cost material technology in the short term that can provide the material property performance requirements for stiffness, low hystersis, and fatigue that can make run-flat technology affordable to the mainstream market. It should be pointed out that the current self-supporting, run-flat technology typically carries a 20-30 percent weight penalty for the additional materials used to make the run-flat, self-supporting (inserts). These materials are expensive and must be passed on to the consumer to maintain profitability for the tyre companies.
In the longer term, non-pneumatic tyre technology, which takes a completely different approach, is continuing to advance due to new design concepts and the utilization of non-standard tyre industry polymers such as polyurethanes and thermo-plastic elastomers. This technology, due to its lighter weight construction and potentially lower material costs, could one day become available at a price that is reachable to all consumers.
just-auto: In addition to driver safety, the current focus is to find ways in which to reduce CO2 emissions. As 25% of all CO2 emissions are generated by road traffic and about 20% – 30% of a vehicle’s energy consumption can be attributed to tyres alone, measures to improve rolling resistance remains a top priority. Could you draw on an example of a recent tyre innovation which demonstrates how your company has reduced rolling resistance?
Chuck Yurkovich: In 2009, Cooper Tire introduced its GFE product line which stands for “Greater Fuel Efficiency.” This low rolling resistance tyre takes advantage of the latest technology for design/materials and typically offers fuel efficiency improvements over conventional replacement tyres of 4 – 6 percent. This tyre features optimal tyre shape, traction compensating sipes, and ultra low rolling resistance tread formulation utilizing silica-silane with functionalised polymer technology. It should be noted as greater emphasis is placed on fuel efficiency in the future, this technology will eventually become the mainstay for all products in the industry.
just-auto: As we see it, most tyre manufacturers offer a low rolling resistance tyre in their range yet few currently advertise the use of the silica-silane technology in their commercial vehicle ranges. Why is that?
Chuck Yurkovich: Utilisation of silica-silane technology in commercial vehicle tyres typically will not provide as much of as advantage for rolling resistance as it does for light duty vehicles due to the differences in polymer systems currently used for the treads. Commercial vehicles typically use 100 percent natural rubber polymer in the tread due to heat build-up and durability performance requirements. In comparison light duty vehicle tyres typically use 100 percent synthetic polymers in the treads to achieve its performance requirements of wear and traction. Natural rubber is inherently highly resilient (low hystersis) so the rolling resistance improvements observed with silica-silane technology are minimal in comparison. As a result, you probably do not see the advertisement of silica-silane technology for the commercial vehicle industry since the benefit at this time is not great enough to warrant its use and compensate for the trade-offs of higher costs and poorer tread wear.
just-auto: In addition to low rolling resistance, low tyre/road noise are requirements imposed on modern tyres for environmental and economic considerations. Could you draw on an example of a recent tyre innovation which demonstrates how your company has reduced rolling tyre noise, perhaps highlighting certain new processes or developments?
Chuck Yurkovich: Like many tyre characteristics, successfully reducing tyre/road noise often involves overcoming other performance trade-offs. Since a significant amount of the tyre-related portion of tyre/road noise is generated by the tread pattern, we spend considerable t
ime and effort in determining proper tread groove placement, depth and pitch sequencing in order to optimize the balance of tyre/road noise and wet traction. To do this effectively, we’ve invested in development of both predictive and testing tools. For example, we have developed a tool that enables prediction of in-vehicle tyre sound quality characteristics from the test data of a single tyre in an indoor noise chamber. We are also developing methods to further extrapolate that indoor, single tyre test data to predict performance on the pass-by noise test specified by many regulations. This enables us to optimize tyre noise for both the customer and the environment.
just-auto: In what ways will information on the new EU tyre regulatory standards provide a better service for the end consumer?
Chuck Yurkovich: The labelling proposal will ensure the supply of “standardised information” not only on fuel efficiency, but also on wet grip and rolling noise so that consumers and end-users can make an informed choice between tyre manufacturers.
Also, tyre labelling will provide a means for European consumers to make better purchase decisions based on what’s most important to them: brand, product performance, price, warranty, contributions to fuel efficiency, or contribution to vehicle noise.
In the end, this new legislation may actually give consumers less choice if the vehicle manufacturers stipulate that in order to maintain the CO2 emission of the vehicle, they will have to fit a replacement tyre with the same rolling resistance grading.
just-auto: In your view, what tyre regulatory information needs to be communicated to the consumer?
Chuck Yurkovich: The E-mark in conjunction with the W and S marks signifies on the tyre’s sidewall that the tyre has been type approved to the ECE regulations. The most appropriate means to communicating consumer information is at the point-of-sale where consumers can understand the information prior to purchasing tyres.
just-auto: As I understand it, truck tyres are included in the requirement for tyre labelling. Would you agree that, given the importance of truck tyres to the economy of fleet transport, purchasers of truck tyres should receive greater clarity through the use of labelling?
Chuck Yurkovich: Communicating labelling information is very important to the commercial tyre sector and should be made readily available for fleets to make educated purchase decisions based on several criteria that are most important to them: product performance/brand, tread wear, retreadability, price, warranty, contributions to fuel efficiency, contribution to vehicle noise, etc.
just-auto: Ultimately, I guess if the information on the tyre sidewall was easier to read, it could be a better method of communicating information instead of sticky pictogram labels which could be dirty, incorrect or even missing at the point of sale. Would you agree?
Chuck Yurkovich: The best method is to inform the consumer prior to purchasing their tyres. I would agree that labels are not an effective way to communicate this information to the consumer prior to sale, but having the information engraved into the sidewall of the tyre won’t be any more effective. The consumer will typically not see the label on the tread or the sidewall of the tyre prior to their purchase. The information needs to be available to the consumer either prior to the sale or at the point-of-sale so they can make a well-informed decision on what tyre will best meet their needs.
Lastly, there is a proposal that the receipt given to the consumer after they have purchased their tyres should contain the rolling resistance and wet grip grades along with the noise value of the tyre they have purchased. If adopted, this would be an additional communication method that could serve to permanently document the tyre label regulatory information.
just-auto: In the medium term, is RFID a better solution?
Chuck Yurkovich: RFID tags are used in some motorsport applications to understand the forces that tyres see during usage. Other companies use them for processing tyres through the manufacturing plant. There is also some usage in truck tyres to monitor tyre performance. However, there does not seem to be a move to more widespread use of RFID chips. Cost, practicality and the usefulness of the information generated still has not been fully determined and we currently do not see this as a better solution towards communicating consumer information ratings on rolling resistance, noise and wet traction.
just-auto: People talk of the intelligent tyre as vehicles change. With newer forms of propulsion, in what ways will the tyre change and adapt to such technology?
Chuck Yurkovich: I foresee two parallel paths on how tyres will change: 1) tyres for what I’ll call ‘evolution of conventional vehicle platforms,’ and 2) tyres for ‘new, revolutionary mobility platforms.’
In the first case, the modern pneumatic tyre and the internal-combustion engine powered automobile have co-evolved over decades. They will continue to evolve together under the evolutionary pressures of increased performance demands (traction, rolling resistance, noise, etc.) and their development will explore the limits of materials and tyre construction technology within the boundaries (tyre size constraints, drive trains, vehicle mass) of these types of vehicle platforms.
Simultaneously, we are seeing a variety of new types of vehicles and alternative drive trains that open up possibilities for revolutionary tyre concepts. Not all of these new concepts will reach market viability. Some of these new vehicle technologies will, however, find a niche and new opportunities for tyre technology will emerge such as the non-pneumatic Resilient-NPT concept being co-developed with Cooper.
An example of the types of engineered materials that I envision are just around the corner are polymers and fillers that respond dynamically to the instantaneous energy environment of the tyre, providing low hysteresis (i.e., energy absorption and heat generation) at steady state highway speeds, but a high rate or energy dissipation during braking. A number of technologies are under development to improve the durability – both in maximum speed and mileage range – of conventional pneumatic ‘run-flat’ tyres through advanced tyre constructions and materials. Our Cooper run-flat products already exceed European standards.
Our European technical centre in the UK is taking the lead in our technology development focused on optimizing the balance of tyre performance characteristics required to meet the EU regulations that take effect in just a few years. While ‘nano-technology’ and ‘smart materials’ are probably overused buzzwords, I expect that we will continue to see the commercialization of new reactive polymers and filler systems that are engineered to work together in composite structures to provide levels of tyre performance that far exceed the performance based on the use of any of these materials alone.
Cooper Tire & Rubber manufactures passenger, light truck, medium truck, motorsport and motorcycle tyres which are sold nationally and internationally in the replacement tyre market to independent tyre dealers, wholesale distributors, regional and national retail tyre chains and large retail chains that sell tyres as well as other automotive racing products. In terms of Cooper Tire & Rubber’s overseas operations, the company has a manufacturing facility, technical centre and distribution centre and its European headquarters office located in the UK. In addition, the company operates five distribution centres and fives sales offices in Europe. It also has two manufacturing facilities, 18 distribution centres, a technical centre, two sales offices and an administrative office in China. The company also has a purchasing office in Singapore. In Mexico, Cooper Tire & Rubber has a sales office and four distribution centres. The company says it is expanding its operations in what are considered low-cost countries. These initiatives include the Cooper Kenda Tire manufacturing joint venture in China, the Cooper Chengshan joint venture in China and its investment in a manufacturing facility in Mexico.