Now that European legislation is coming in to make tyre pressure monitoring systems (TPMS) mandatory, the motorist no longer has to pay extra. Matthew Beecham talked with Franco Annunziato, senior vice president, technology, Bridgestone Europe about the future for TPMS, run-flats and the so-called intelligent tyre.
just-auto: What is the future for TPMS technology? Do you think that indirect TPMS will become a standard feature of on future electronic stability control systems?
Franco Annunziato: We fully support accurate TPMS, firstly as an important safety factor, reducing the numbers of failures due to running at low pressure, and secondly, because it can maintain the tyres’ optimum rolling resistance when the pressure is correctly adjusted.
The indirect TPMS system relies on the ABS sensors which are fitted to almost 100% of all cars today. The electronics evaluate any difference in the speed of rotation of one tyre versus the others so detecting a deflation.
A direct TPMS measures the internal pressure of the tyre with a sensor and transmits this to a receiver in the vehicle. The electronics can then display and follow the real internal pressure of the tyre.
The EU regulation will be a major driver to bring TPMS to all users; however it is not yet certain which TPMS type will become mandatory.
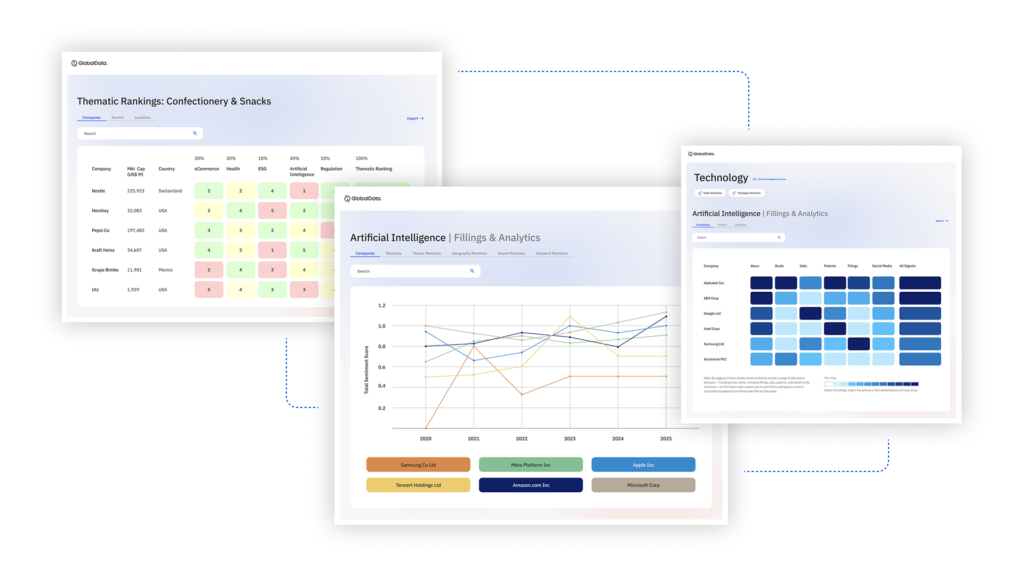
US Tariffs are shifting - will you react or anticipate?
Don’t let policy changes catch you off guard. Stay proactive with real-time data and expert analysis.
By GlobalDataj-a: As I understand it, TPMS technology is evolving to the point where one scenario could be this: As soon as the TPMS tells you that your tyre needs servicing, the nearest licensed service station will be automatically alerted through your car’s GPS, giving you directions to a site where qualified personnel will be awaiting your arrival. How far away are we from achieving this?
FA: Most high-end vehicles have now a GPS system as standard equipment; its navigation software often contains the locations of approved service centres. Linking vehicle faults, such as low tyre pressure, and service centres is the next logical step in such a system. Adding in the communication from car to service centre is also becoming possible as manufacturers add internet connectivity.
Such systems could therefore be implemented relatively soon if the car manufacturer sees a requirement.
j-a: Run-flat tyres have also done a lot to improve vehicle safety yet come with a high price tag. Do you see technological evolution bringing run-flat and self-inflating tyres into the cheaper mainstream?
FA: SSR features a side-supported rubber aiming to support the load of the vehicle when the tyre deflates.
Therefore, in principle the cost of a RFT will be higher than a regular tyre, because of the side-supported rubber.
However SSR system means ‘spareless’ which could result in eliminating a full spare tyre or temporary spare tyre or sealing kit. So we believe it could be possible to equal or even improve the cost of a regular tyre when we consider it as a complete system.
j-a: In addition to driver safety, the current focus is to find ways in which to reduce CO2 emissions. As 25% of all CO2 emissions are generated by road traffic and about 20-3% of a vehicle’s energy consumption can be attributed to tyres alone, measures to improve rolling resistance remain a top priority. Could you draw on an example of a recent tyre innovation which demonstrates how your company has reduced rolling resistance?
FA: First, I would like to emphasise that although the figures you quote are correct, the energy consumption attributed to tyres cannot be eliminated, and will always be significant. Nevertheless, tyre companies continue to make inroads to reducing the rolling resistance of tyres to contribute to reducing CO2 emissions.
All tyre companies are faced with the same challenge whereby tyre performances are linked to each
other. For example, it is possible to make a tyre with far superior low rolling resistance than current tyres, but the penalty would be that the wet braking performance of the same tyre would be unacceptable, and even dangerous. That is why the European labelling regulation includes both energy efficiency and wet braking performance on the same label.
Our company has introduced nanoprotech technology in the tread rubber compounds, which lowers the rolling resistance coefficient by reducing energy loss in the top compound during rotation.
j-a: As we see it, most tyre manufacturers offer a low rolling resistance tyre in their range yet few currently advertise the use of the silica-silane technology in their commercial vehicle ranges. Why is that?
FA: The use of silica silane is a feature. Communication tends to focus on the benefits rather than the features that actually bring those benefits.
j-a: In addition to low rolling resistance, low tyre/road noise are requirements imposed on modern tyres for environmental and economic considerations. Could you draw on an example of a recent tyre innovation which demonstrates how your company has reduced rolling tyre noise, perhaps highlighting certain new processes or developments?
FA: Reducing tyre road noise is a challenge for all tyre manufacturers. It has been proven that road surfaces and the materials used to make them can contribute more to the reduction of tyre road noise than the tyre itself. Also, the quietest tyre possible to make is a slick, that is, a tyre with no tread pattern at all. Slicks are not an option for normal cars as the lack of wet grip would be unacceptable. It is the grooves of a tyre’s tread pattern that contribute to creating external noise, but it is the same grooves that allow for water evacuation and directional stability, and grip on wet surfaces. By optimising tread design, it is possible to achieve the regulated noise limits, and this is where most of the advances have been made with regards to tyre noise.
j-a: In what ways will information on the new EU tyre regulatory standards provide a better service for the end-consumer?
FA: The end-consumer will be able to recognise the performances of each tyre before they purchase it, thanks to a performance label that must be displayed with the tyre, and on point-of-sale material. The label, inspired by the energy efficiency label which is currently displayed on refrigerators and other white goods, will show the wet grip grading of the tyre and the measured external noise in dbA as well as the energy efficiency rating on a seven-grade scale. Thanks to the label information, consumers can make their choice depending on their own preference; maximum safety or maximum fuel economy.
j-a: In your view, what tyre regulatory information needs to be communicated to the consumer?
FA: We consider safety to be of paramount importance. The only contact that a tyre has with the road is through its tyre footprints. In the interests of road safety, customers need to understand safety performances.
As end-users are increasingly seeking ways to reduce their impact on the environment, the fuel efficiency of their vehicle has become the first criterion when choosing their new car. Tyre performance also affects the fuel efficiency of a vehicle. Therefore, communicating this value to consumers is very important.
j-a: As I understand it, truck tyres are included in the requirement for tyre labelling. Would you agree that, given the importance of truck tyres to the economy of fleet transport, purchasers of truck tyres should receive greater clarity through the use of labelling?
FA: We agree that fleet operators also need information on tyre performance. However, our experience is that purchasers of truck tyres are usually well informed professionals with real data available to them showing the economic effect of their tyres on their operations. This data includes many additional performances that are not considered in car tyre usage. For example, the durability and life of the tyres, and their suitability for reuse as retreaded tyres, thereby saving both money and environmental impact.
j-a: Ultimately, I guess if the information on the tyre sidewall was easier to read, it could be a better method of communicating information instead of sticky pictogram labels which could be dirty, incorrect or even missing at the point-of-sale. Would you agree?
FA: The regulation foresees that the label information will be communicated by several other methods such as on websites, and printed material available at points of sale, so it is not at all confined to sticky labels. Incorporating the information on tyre sidewalls has several disadvantages. It is often difficult to read and understand sidewall printed information. The information is basically only needed before the tyres are purchased, and has no meaningful role once the tyre choice and purchase has been made. The actual physical tyres being purchased are often not seen by the customer until after they have been fitted to the car. They are chosen from catalogues, website information and the advice of sales staff using sales brochures.
j-a: In the medium term, is RFID a better solution?
FA: Not for informing customers before they make their purchase decision. RFID is good for identifying and tracking the performance of tyres once they are in operation.
j-a: People talk of the intelligent tyre as vehicles change. With newer forms of propulsion, in what ways will the tyre change and adapt to such technology?
FA: There have been, and still are, many research projects looking at various ways to bring information from the tyre to the vehicle. As the tyre is the contact point to the road, dynamic feedback in real time of tyre/surface interaction could provide benefits to ESP, ABS and other systems reliant on knowledge of the level of tyre grip. Unfortunately, integrating electronics inside such a harsh environment, with high rotational and shock g forces, is not simple, especially as adding weight has a negative impact on vehicle dynamics. Many in-vehicle sensing systems can already estimate grip levels quite well, so cost/benefit is not high to have an in-tyre solution.
For future vehicles, whether fossil-fuelled, electric or some hybrid form, the need to maintain safety and optimise rolling resistance will be increasingly important so TPMS should become a key vehicle component.