
Dutch-based industrial firm BioMCN has commenced operations at the largest second generation biofuel manufacturing plant in the world. It sees very positive prospects ahead in transportation applications for the bio-methanol it produces from glycerine – itself a by-product of biodiesel manufacture. Automotive applications are being readied, especially in the substitution of bio-methanol for bio-ethanol in gasoline blends. And the vision for more efficient energy utilisation and lower CO2 emissions does not end there, as BioMCN CEO Rob Voncken explains to just-auto editor Dave Leggett.
DL: What’s taking your time at the moment?
RV: This project began at the end of 2006 and we have now started industrial scale production of bio-methanol at our plant. There was a lot of preparatory work ahead of that and of course there is plenty of sales work that now comes with having a product to sell in the market.
DL: Can you briefly describe the nature of your company and its activities?
RV: We are the first company in the world to produce high-quality bio-methanol from renewable resources on an industrial scale and, after completion of the new plant, the largest second-generation biofuels producer in the world.
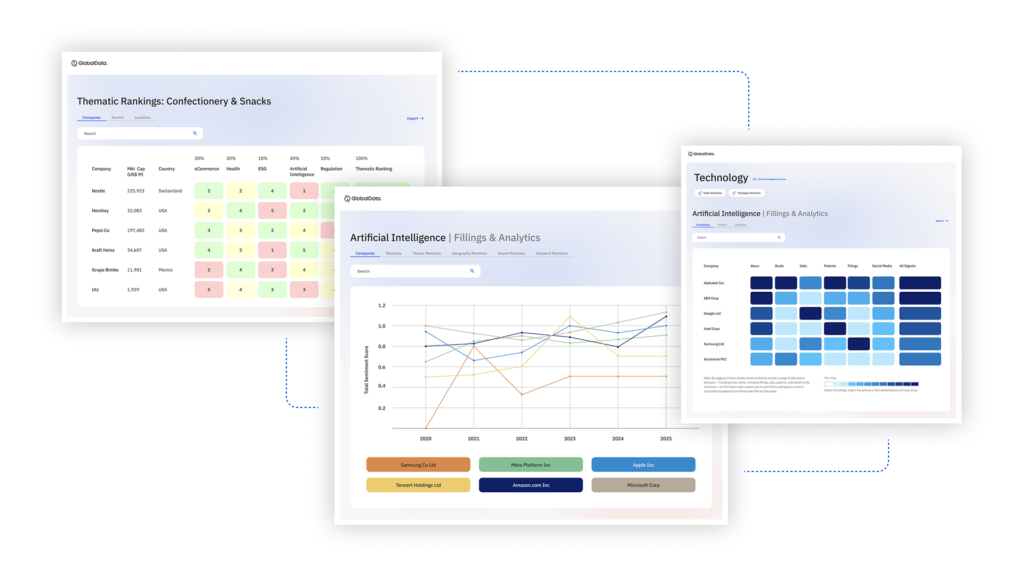
US Tariffs are shifting - will you react or anticipate?
Don’t let policy changes catch you off guard. Stay proactive with real-time data and expert analysis.
By GlobalDataBoth national and European policies encourage the use of renewable fuel in petrol and diesel. According to the targets set in the EU Renewable Energy Directive (RED), 5.75% of the energy value of transportation fuels must consist of biofuel by 2010 and 10% by 2020. That creates the opportunity for us.
March 2008 saw the successful start-up of the pilot plant, producing 20,000 tonnes of bio-methanol per year. The new plant – ten times bigger – enables BioMCN to purify and evaporate crude glycerine, thus making it possible to produce bio-syngas for making biomethanol.
The next step is to fully convert both existing production lines from natural gas to biogas. The transition will be performed in stages over the coming years, in steps of 200,000 tonnes capacity at a time. The first large unit is now operational. The site can accommodate another three such units, adding up eventually to a capacity of 800,000 tonnes a year of bio-methanol. Both national and European policies encourage the use of renewable fuel in petrol and diesel.
We have developed a process which enables us to convert crude glycerine – a by-product of biodiesel – into methanol. By converting glycerine into methanol, its full energy potential can be utilised, thus enabling further reductions in CO2 emissions.
Production of biodiesel is growing in response to demand for transport fuels with a lower carbon footprint. The main feedstocks for biodiesel production are vegetable oils or fats and methanol, with glycerine as a by-product. And we take that as input into our process.
DL: So how does the production process actually work?
RV: The crude glycerine from biodiesel plants is transported by ship, train or truck to the BioMCN plant, where it is stored in tanks. The crude glycerine is then purified, evaporated and cracked to obtain syngas (synthesis gas), which is used to synthesise the biomethanol.
Next, the bio-methanol is purified by distillation and is stored. Tankers delivering the raw glycerine can collect a return load of methanol, thus optimising the logistics in the chain.
The syngas used in the process can also be obtained from other forms of biomass such as wood or algae. In order to ensure sustainability, we use renewable feedstock exclusively derived from organic waste materials and crops other than those used for food consumption. Further to this we are also investigating the feasibility to use our own and other companies’ CO2 emissions as feedstock for sustainable methanol.
Our process closes the cycle by converting the by-product crude glycerine into methanol feedstock. This allows biodiesel production to become even more sustainable, while avoiding potential problems with the disposal of surplus glycerine.
DL: And where do the automotive applications come in?
RV: The main opportunity is to replace ethanol in the blending of ethanol and gasoline – currently to produce blends such as E85. Similar to ethanol, bio-methanol is also suitable for direct blending.
Ethanol production, as we all know, brings disadvantages in terms of incursion into the food chain.
Our bio-methanol is a second generation biofuel and we can reduce CO2 generation by as much as 70% in our production process versus liquid fossil fuel. On top of that, there are further tailpipe CO2 reductions derived from biomethanol in use by vehicles.
We also have a Bio-MTBE application. MTBE – an oxygenate created by a reaction between isobutylene and methanol – is mainly used to raise octane levels in gasoline. Thanks to higher oxygen levels, gasoline burns more completely, thus reducing tailpipe emissions.
Bio-DME is another application that we are studying. DME is used as a substitute propellant for chlorofluorocarbons (CFCs) in spray cans, whereas in Asia it is also blended with LPG (for heating). Thanks to its low self-ignition temperature and high cetane number, DME is also a suitable diesel engine fuel for use in heavy-duty vehicles such as trucks and buses.
DME cannot be blended with fossil fuel-based diesel and its volumetric energy content is lower – approximately half that of diesel. However, diesel engines can be easily retrofitted to run on DME – this is similar to retrofitting a petrol car to run on LPG. DME could be, in principle, a replacement for biodiesel. That’s a longer term proposition though.
The fuel component opportunity, to replace ethanol with methanol, is the major one that we are targeting right now. That is an existing market that we can tap into with our bio-methanol product. It could be used immediately in flex-fuel cars.
DL: How does methanol compare with ethanol on CO2 emissions?
RV: The tailpipe emissions of CO2 per kilometre are lower for methanol than for ethanol. There’s a higher energy efficiency for methanol which means you can increase the horsepower of a car.
Methanol produces a more than 10% CO2 emission reduction versus a petrol car and it’s more than 5% better than ethanol. If we look at energy consumption per kilometre, a normal petrol car comes out at approximately 3-4% higher than for methanol.
A disadvantage of alcohols – both ethanol and methanol – is the fact that their energy content per litre is much lower than for petrol, so you need to fill up your car twice as often. Because methanol produces more horsepower when burning, 25% more than petrol, the opportunity is to utilise that power gain – alongside other technologies, such as turbochargers – to get an engine size reduction for the same power output and in that way decrease CO2 emissions even further. When you combine technologies like that, you can potentially get a fantastic value proposition.
DL: Could bio-methanol be used in aviation engines?
RV: The interesting thing about methanol is that because it is so versatile, you can produce kerosene from it. So, yes, that’s a possible application.
There are lots of potential applications. Methanol is also a raw material used in the manufacture of a lot of plastics, such as polyesters. A lot of parts in a car are made from plastics, so that’s another potential area where bio-methanol could help reduce CO2 generation further.
DL: Would it be cheaper to make plastics from methanol rather than oil?
RV: No, not with energy prices where they are now. But in the long-term, as prices of fossil fuels rise, then the economics change and it may well be the case that using more methanol makes sense on simple cost grounds. At the moment there is interest from some customers who are specifically interested in plastics prepared with a bio-product as raw material and therefore prepared to pay a premium for that.
DL: Is bio-methanol expensive to manufacture, compared with fossil fuels?
RV: Yes, at this stage, compared with fossil fuels, our production costs are more expensive. Much, of course, depends on where fossil fuel prices are – and we have seen much volatility over the past year.
But we are very competitive against bio-ethanol.
DL: In terms of the timescale, how do you see the future for bio-methanol in cars? Do you have projections for penetration rates, for example?
RV: That’s a difficult one. You can see, even with a very strong ethanol lobby, just how slow the actual penetration of ethanol in the market is. When you have a separate product called methanol, it is going to be very difficult to get separate distribution via the oil companies.
What we are trying to aim at is perhaps replacing E85 with ‘A85’ – A for alcohol – and a situation in which it is left to the blenders to blend in different alcohols.
Our plant is a large-scale plant – the largest second-generation biofuel producing facility in the world – but our share is going to be small. Methanol enables lots of options and we are working on several projects that need years of refinement before going to the market. The potential is there, but I can’t give you numbers. It is also dependent upon the oil companies and how willing they are to change their existing infrastructure.
Closed circuits could be interesting – for instance with bus companies or courier companies, where they come to us to set something up.
DL: Ethanol and methanol can easily be mixed up then, in an ‘A85’ blend?
RV: Yes, they can easily be mixed.
DL: Are you working closely with the oil companies?
RV: They are our customers for the bio-methanol. We already have good relationships with them and we are building these further. Much depends on the companies, how they are branding their products, their distribution systems and so on. Different companies are interested in different products that we can offer.
DL: Looking to the very long term, how realistic do you think talk of a sustainable synthetic methanol cycle – involving the use of things like CO2 recycling from factories – is?
RV: We are working on this. The interesting thing is that synthesis gas – that we produce to make methanol – is a mixture of CO2, CO and hydrogen, H2. The bottom line is that CO2 is a feedstock to produce methanol. The potential is there to use CO2 from other sources as a feedstock in the future. We are working on projects in this area with partners.
Adding CO2 in the process can easily be done, so long as you have the right combination of the synthesis gas components. You need hydrogen, which could be produced, for example, by utilising the spare capacity of windmills to store energy at times of low electricity demand and high winds.
These kinds of concepts are possible and being evaluated. The most important thing is to have a hydrogen source. Hydrogen can be produced by electrolysis on water.
Another possibility is to produce bio-methanol using the fermentation process. In this concept, bacteria transfer CO2 and water into methanol and oxygen.
All of these things are in development and bio-methanol is potentially very important for the long-term future. People are looking at carbon capture and storage, but we believe we can potentially use that CO2.
However, it will take some years to be developed further.
DL: What do you see as the big challenges ahead for your business?
RV: The biggest challenge right now is to get bio-methanol fully introduced as a value proposition and accepted as an alternative to petrol or ethanol by the oil companies.
In the long-term, everyone has to look at how we make bio-methanol happen, so support for second-generation biofuels is important. If there was no EU Renewable Energy Directive, we would not be selling biofuels because fossil fuels are still cheaper.
And to further develop the technologies to further reduce CO2 emissions, bio-methanol is a fantastic starting point.
And of course, we have to get this company profitable so that we can reinvest and develop further.
DL: How was the company BioMCN formed?
RV: It’s a privately held company and was formed at the end of 2006 through the acquisition of the plant in the Netherlands, marrying that to the technology plan and some early-stage investors.
DL: What gives you the greatest satisfaction in your job personally?
RV: There are lots of challenges involved with an industrial start-up like this. But the most rewarding thing is the fact that we can make a contribution to a better environment by reducing greenhouse gas emissions. That is the really big challenge and we are extremely proud of the contribution we will be making.
Please note that this article first appeared in Lotus Engineering’s e-magazine proActive.
![]() |
Rob Voncken
Rob Voncken Rob Voncken (45) is the CEO of BioMCN. Before joining BioMCN he fulfilled several positions at DSM in the areas of business development, marketing and sales and general management and he was responsible for the management, of several outsourcing, divestment and acquisition projects.