Bayer MaterialScience has developed solutions based on polycarbonate (PC) which can be used for car glazing. Here, Matthew Beecham talked with executives of the company about trends in the application of PC glazing.
In what ways has Bayer MaterialScience’s Makrolon PC been advanced in recent years?
In the process of window production, our customers are using for the majority of transparent applications the two-component injection moulding process. That means using a transparent coloured polycarbonate material for the outer skin and a non-transparent PC-blend material for the frame, which is back-moulded onto the transparent polycarbonate.
The material of choice for the transparent component is Makrolon AG 2677, which is produced in a variety of transparent colours and offers a virtually unlimited range of options to create a colour tone optimised for individual needs. The choice of colours is made possible by both the more flexible production process and the colouring technology used for the polycarbonate. Special measures in production ensure the exceptionally high purity level of the material coloured in a compounding phase. The additive package has also been optimised to meet the strict requirements. An important development step has been finalised recently for the Makrolon AG 2677: Bayer MaterialScience has developed a broad range of special colours, which are capable of absorbing a high portion of the infrared light. These colours are preferably used for panoramic roofs. The additional benefit for the car manufacturer is that they do not need to use a roller blind anymore, offering more space in the car interior and reducing manufacturing cost of the roof system.
For second component materials, preferably PC+ABS blends or PC+PET blends, Bayer MaterialScience has carried out different material optimisations: In order to meet all requirements of a window system, especially with respect to low optical distortion, high surface quality and good mechanical resistance, Bayer MaterialScience has developed and further optimised the properties of second component blend materials, like higher flowability, adapted shrinkage and further improved impact resistance.
In terms of applications, where do you see the opportunities for PC glazing on passenger cars?
How well do you really know your competitors?
Access the most comprehensive Company Profiles on the market, powered by GlobalData. Save hours of research. Gain competitive edge.
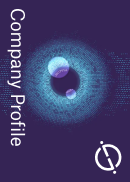
Thank you!
Your download email will arrive shortly
Not ready to buy yet? Download a free sample
We are confident about the unique quality of our Company Profiles. However, we want you to make the most beneficial decision for your business, so we offer a free sample that you can download by submitting the below form
By GlobalDataWe are seeing very high potential in polycarbonate glazing on short- and mid-term view in transparent panoramic roofs, non-transparent roof bezels with black glass-like appearance, fixed side windows and rear windows. We are quite optimistic to bring polycarbonate into further applications such as movable side windows and windscreens in the long term.
PC suffers from a lower stiffness compared to glass. How does Makrolon deal with this problem?
The tensile modulus of polycarbonate in general is for sure much lower than the modulus of glass, hence the rigidity of a polycarbonate panel is lower than the rigidity of a glass panel, based on the same dimensions of the panel. Since polycarbonate can be processed in the injection moulding process, there is nearly no limitation to create a three dimensional design or increase the rigidity of the entire system by higher section modulus.
Can PC glazing be used to meet the increasingly stringent EC regulations, for example concerning pedestrian safety?
Pedestrian safety in terms of vehicle windows is relevant mainly for windscreens. The use of polycarbonate for windscreens is not yet allowed, based on current international regulations. The automotive industry, however, together with Tier suppliers and raw material companies are working on a further amendment of the existing ECE regulation, in order to allow the use of windscreens made from plastic materials. Based on these ECE regulations, several tests with windscreens made from polycarbonate have demonstrated that this material doesn’t break in case of an accident and is capable of meeting the requirements in terms of pedestrian safety, depending on the specific design of the part.
What are the technical challenges that BMS still face with PC glazing?
For the automotive industry coatings are of crucial importance for the quality of glazing components. They need to fulfill a series of surface requirements such as weathering, chemical, scratch and abrasion resistance. One major challenge for coated polycarbonate is still to meet outdoor weathering performance of more than five years without showing any defect.
Presumably the relative cost of plastic glazing compared to glass is still a major concern for carmakers when considering its widespread adoption?
The remainder of this interview is available on just-auto’s QUBE research service