BASF’s Performance Materials division focuses on industries such as automotive, construction, electrics and electronics. Here, Matthew Beecham talked with Bernhard Rosenau, Segment Management Automotive, Engineering Plastics Europe, BASF SE about some of the division’s most recent PA and PU automotive applications.
As we understand it, BASF has helped Volkswagen to save weight and cost from the latest Golf’s front-end carrier. These structural injection mouldings are typically made from polypropylene with steel reinforcements yet this one has been designed entirely from glass-fibre filled polyamide…
The higher mechanical performance of PA compounds versus PP compounds not only made it possible to do without steel reinforcements but also to reduce the overall thickness of the structure, reinforcing ribs, etc. As a result, the new component is significantly lighter than its predecessor made from PP in spite of the higher density of the material.
I believe that there is a trend for switching from glass reinforced fibre PA66 to PA6?
There is a trend to replace the more expensive PA66 by PA6 in some applications where both can be used. In general, PA66 has higher heat resistance, crystallinity, chemical and hydrolysis resistance, absorbs less moisture and has mechanical properties less dependent from atmospheric conditions. PA6 however has somewhat lower stiffness and higher impact resistance, particularly in the conditioned state and is more easily processed due to its lower melting point. Applications loaded with high temperatures or hydrolytic conditions will therefore remain with PA66.
See Also:
Smart used the 2011 Frankfurt motor show display its green vision for the Fortwo. A notable feature is the bodywork: the concept has a special coating developed by BASF. The paintwork giant claims this production ready coating will keep the car’s surface up to 20°C cooler on a hot day compared to conventionally-painted vehicles. Could you comment on that?
How well do you really know your competitors?
Access the most comprehensive Company Profiles on the market, powered by GlobalData. Save hours of research. Gain competitive edge.
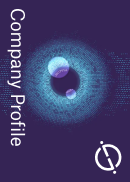
Thank you!
Your download email will arrive shortly
Not ready to buy yet? Download a free sample
We are confident about the unique quality of our Company Profiles. However, we want you to make the most beneficial decision for your business, so we offer a free sample that you can download by submitting the below form
By GlobalDataA black car heats up in the sun more quickly than a white or silver vehicle. But even surfaces coated with dark colours stay much cooler thanks to special colour pigments from BASF. They ensure that heat radiation is reflected rather than absorbed. This reduces the temperature of the coated surface by up to 20 degrees Celsius and of the vehicle interior by up to approximately four degrees. As a result, energy for air conditioning can be saved because the passenger compartment does not heat up as much. This benefits the passengers – who enjoy the more comfortable environment – and the material is subjected to less stress due to the lower temperatures. These coatings are not yet available for OEM finishing.
To what extent is bonding solutions (e.g. direct bonding with silicone) taking over from conventional fastening applications such as fixing screws?
Options to join different materials, [providing] good impact, crash and damping properties, integration of additional functions like sealing are particularly important in lightweight construction. But it is difficult to say if this kind of bonding has taken over strongly from classical joining with screws.
Do you think that the European Polyurethane industry should increase its efforts to promote the benefits of the material to the automotive industry? Or has the industry understood the benefits of the material and where it can be used?
We are properly linked with automotive OEMs and tier suppliers. The industry knows and appreciates the benefits of Polyurethanes in the case of existing applications. For new applications, e.g. structural parts, it could be beneficial to intensify the activities.