Based in Dundee, Scotland, Axeon designs, develops and manufactures customised advanced lithium-ion battery packs and charging systems for a range of automotive and other applications, with its core business in developing and supplying such systems for use in electric and hybrid electric vehicles. In this interview, Matthew Beecham talked with George Peterson and Dr Allan Paterson of Axeon.
It appears that lithium-ion batteries are well suited to electric vehicles in respect of high energy content. What further advances could we expect with this technology for automotive applications?
There are several other key areas that li-ion materials and cell engineering are trying to address. These include increased power density, more efficient systems, cells that are easier to thermally manage, better lower temperature performance, more stable cell chemistry that leads to long cycle life and improved cell level safety.
In terms of battery configuration, to what extent is the market moving toward prismatic and away from cylindrical?
In certain applications, for example high power HEV systems cylindrical cells still offer advantages, particularly in terms of power capability and thermal management. However, there is a drive, particularly by the German OEMs, to standardize cell formats to a small selection with similar footprints that encompass enough variation to target EV, PHEV and HEV applications, all in a prismatic format. Standardization, commonality of parts across multiple vehicle platforms and modularization are then being used to drive down battery pack cost.
While the cost of lithium-ion batteries for electric cars is falling, there is some way to go. As we understand it, the cost of such batteries is approximately US$600 per kilowatt hour compared to US$250 per kilowatt hour for laptop batteries. Can batteries for electric vehicles get that low?
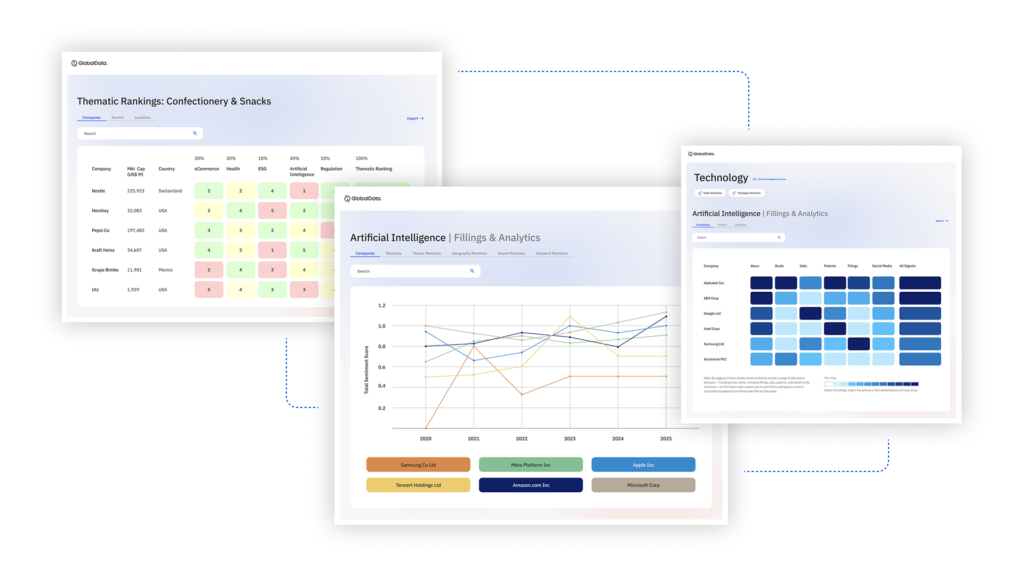
US Tariffs are shifting - will you react or anticipate?
Don’t let policy changes catch you off guard. Stay proactive with real-time data and expert analysis.
By GlobalDataIt is possible by 2020 that EV battery prices can reach this level but it is dependent on large volumes, i.e. 150,000 units per annum of a single design to be realised. If EVs still remain a niche then prices could struggle to get below $400/kWh.
If the cost of battery packs can be significantly reduced, where will the cost reduction come from? i.e. efficient factory management, cutting waste and other management-related expenses or from fundamental improvements in battery technology?
Improved cell yield, improved energy density which will require less materials per kWh, cost reduction in power electronics and battery management systems, higher assembly efficiencies with greater numbers and reduced overheads, standardised cell sizes and more modularity and exchangeability between manufacturers.
I guess that once the price falls, the emphasis will be on delivering higher energy density which could lead to smaller batteries?
The two may not be mutually exclusive and go hand in hand as the advanced high energy density systems are being developed with cost in mind, for example developing electro-active compounds that do not contain expensive rare earth elements, or use expensive and complex synthesis methods. For example the Si-Alloy based anode technology is potentially cheaper than the graphite material it may replace.
And I guess the average cell price is influenced by safety measures relating to cell/pack design and manufacturing processes? What other factors influence the price?
The remainder of this interview is available on just-auto’s QUBE research service