
Continuing just-auto’s series of interviews with tier one suppliers at the 2015 IAA show, Matthew Beecham talked to Tim Jackson, Executive Vice President Technology, Strategy and Business Development, Tenneco Inc and Ben Patel, Vice President, Clean Air, Global Research and Development and Systems Integration, Tenneco Inc.
Could you tell us about some of the technologies that Tenneco is highlighting this year here at the IAA and your message?
Ben Patel – On the Clean Air side of our business one of the central themes of our display here at IAA is the new Euro 6c regulations for light vehicles. Many of the technologies on display whether at a component level or system level are designed to effectively provide higher temperatures at the catalyst for quicker light off.
Tim Jackson – We no longer have the luxury of taking 10 – 12 minutes after an engine cold start to get the temperature up and running. So with today’s architecture it is not uncommon to see a distance of 6/10th of a metre between the back of the DPF and front of the SCR. But in the future, that will shrink to about 0.1 metre. We have to go to more innovative shapes in order to get those catalysts closer to the engine or the turbo outlets in order to get the heat there quickly. Ultimately, we are going to get these systems up to temperature in 80 – 180 seconds in order to meet the emissions performance of the new certification cycles. Certainly WLTP [worldwide light duty test cycle] adds both low temperature as well as a high driving cycle and so if you take a system that was designed to meet the New European Driving Cycle (NEDC) and test it against WLTP, the emissions could double. So thermal management is the key, more use of electronic exhausts valves, more use of compact mixing. These are the megatrends and certainly the introduction of gasoline particular filters.
Could you comment on how developments in aftertreatment are affecting the choice of engine management strategy?
Ben Patel – The first thing that occurs to me is the demand for ultra high efficiency SCR systems. Customers want maximum fuel economy. They want to run the engines hot which means they will produce higher levels of NOx. If you look at NOx conversion efficiencies today, between 90 and 95% will not cut it; conversion efficiencies are going to have to move from 95 to 98%. Many of the technologies that we have on display will enable those higher efficiencies and demonstrate that we are already to meet the needs of our customers today. For example, our new mixer products are designed to give higher uniformity of urea at the face of the SCR catalyst which ultimate drives higher NOx conversion efficiencies. We have compact designs to help our customers which their packing challenges. We have improved thermal management strategies like the use of air-gap pipe. Our dosing system, XNOx TM, also on display produces a spray with sub 60 micron droplet size. All of these product solutions are driven by the need to have ultra high conversion efficiency in SCR.
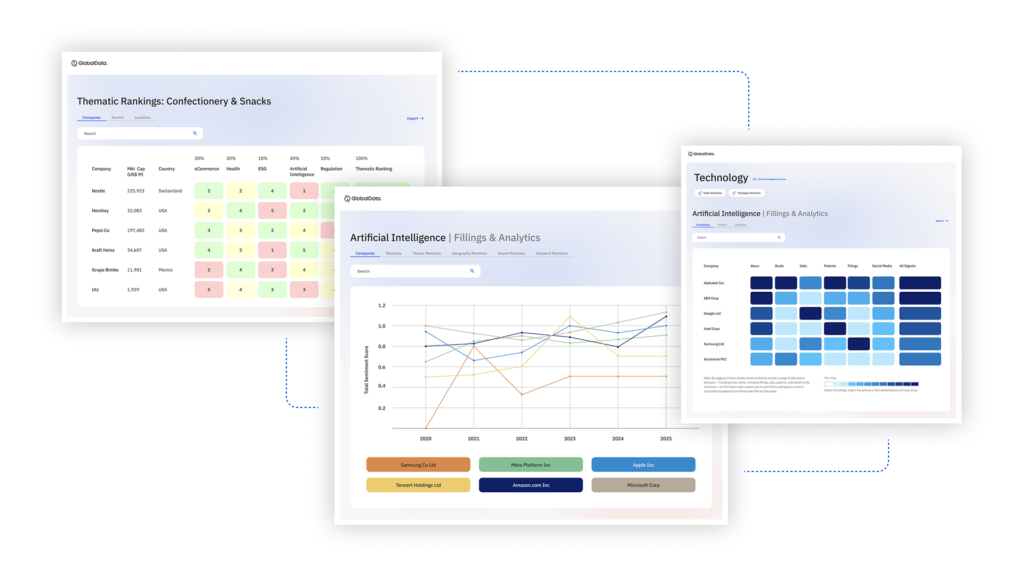
US Tariffs are shifting - will you react or anticipate?
Don’t let policy changes catch you off guard. Stay proactive with real-time data and expert analysis.
By GlobalDataTim Jackson – I would add that the mainstream strategy for diesel platforms in the past was to use a relatively high amount of high pressure exhaust gas recirculation and then clean up what’s left with the selective catalytic reduction systems. And that the desire for better engine efficiency, lower fuel consumption has really led to a reduced use of high pressure EGR and, as Ben said, either a more efficient SCR system or a more efficient SCR system plus the use of low pressure EGR.
To what extent is the electrification of the vehicle driving more actuation as well as new sensor technologies?
Tim Jackson – Let’s deal with electrification first. In the case of using a range extender, you will go through more engine start cycles and so the use of the engine manifold converter where we move the converter closer to the engine and integrate it directly into the exhaust manifold. The Chevrolet Volt is a good example of that. So that has created new opportunities for Tenneco. Again, the thermal management challenges are even greater for hybrid powertrains since you have the engine cooling off during the driving and you have got to maintain that thermal energy for the catalyst to work properly so that really causes us to do some unique packaging solutions to get as close to the engine as possible.
Tim Jackson – Sensors are an interesting topic. Frankly, what we are being driven toward is the use of many more multi-function sensors where you would sense, say, temperature and pressure inside the same sensor. Even in our urea delivery systems, we are being challenged to be more accurate with our dosing in order to get to these 98 percent efficient SCR systems. So we have to move pressure sensing right up to the point of injection. We have to concern ourselves more about urea temperature because the dosing coefficient and viscosity of the urea changes with temperature. So more use of multi-function sensors, and moving them closer to the point of injection, will result. Even the sensors for diesel particulate regeneration are still delta-p sensors so the use of nontraditional sensing technology to improve the accuracy of DPF regeneration and reduce the occurrence of active regeneration and the fuel that is consumed in active regeneration is a big priority for the industry.
Could you comment on the ways in which the megatrend for alternative fuelled vehicles is driving innovation in sensors?
The remainder of this interview is available on just-auto’s QUBE light vehicle OE exhaust and emissions aftertreatment systems research service