
Continuing just-auto’s series of interviews at the 2015 IAA show, Matthew Beecham met with Jean-Francois Berard, Vice President, R&D, Strategy, Marketing and Industrial, Auto Inergy Division, Jean-Bernard Lepage, Marketing Director, Auto Inergy Division, and Jerome Vidalie, Product Line Director, Structural Parts, Plastic Omnium Auto Exterior.
In terms of the automotive fuel tanks market, what is the big picture?
Jean-Francois Berard – The big picture includes PHEVs, the LEV3 in North America with the Chinese emission legislative requirements catching-up. All of our Chinese customers and global customers producing in China are asking us to evolve towards this new Beijing 6 type regulation. This is very interesting for us because we have the competence – through our US operation – of this type of technology as both are close.
What about other BRIC countries?
Jean-Francois Berard – The Indian market is not moving as quickly but will eventually introduce more stringent regulations. We don’t know when but it will happen.
What does that mean for Plastic Omnium?
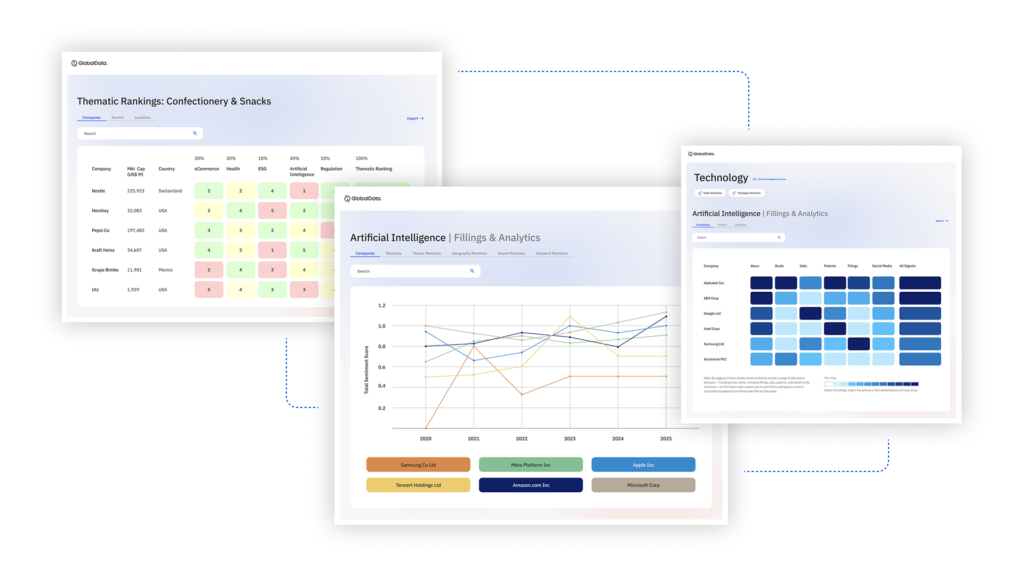
US Tariffs are shifting - will you react or anticipate?
Don’t let policy changes catch you off guard. Stay proactive with real-time data and expert analysis.
By GlobalDataJean-Francois Berard – It means more complexification of the technical solution. As technology leaders, we can supply any BRIC country with the solution it needs today. So for us it is not a threat but huge opportunity to add value to a customer.
We understand that Plastic Omnium is currently developing a technique to reduce NOx emissions from diesel vehicles called SCR. Could you tell us more about this development and what stage you are it?
Jean-Francois Berard – SCR is a necessity now, particularly in the US and becoming more common in Europe, Japan and Korea. That’s why we invested in this technology ten years ago by developing a SCR solution which brings the tank, pump and sensing technology in order to inject the correct quantity of Adblue into the system as required by the OEM engine control unit (ECU). We initially created our own solution, called an AdBlue Delivery Module (ADM) and we are now offering our fourth generation system. We have mastered this technology to the point where we expect to have a 35 percent market share of the Adblue market in Europe by 2019, making us number one.
In terms of hybrid vehicles, we have heard that ‘fuel slosh’ noise reduction is receiving a greater focus. This is especially needed for start-stop vehicles where the car becomes very silent – while standing at a traffic light for example. Is this an observation that you share?
Jean-Bernard Lepage – Your observation is correct. That is why we have developed a family of noise reduction solutions, called Inbaffle, that soften the slosh impact and introduce fuel damping. This enables us to comply with the more stringent noise requirements of hybrid vehicles and increase passengers’ comfort. We can integrate the Inbaffle on the assembly line – using spring loaded or clipped baffles – or during a patented blow-moulding process known as TSBM [Twin Sheet Blow-Molding].
Jean-Francois Berard – As the CO2 prediction is pushing carmakers to install start-stop in cars so when you stop the car, you can hear the fuel slosh hence we need to break the energy inside the tank in order to reduce the noise. It has gradually become a bigger issue. The challenge is to simulate and evaluate the energy of the noise and true noise. Hence, we have developed a number of simulation tools to ensure that the solution is correct very early on in the car’s development.
Could you tell us more about your solution developed with PSA to replace the traditional steel underbody with a self-supporting thermosetting resin floor reinforced with fibreglass?
Jerome Vidalie – One of the notable aspects of this design is that it reduces the number of parts to be assembled from more than 30 to just 4 main components thereby giving a weight reduction of 8 Kg for a mid-range model. That means we can reduce the tooling investment quite significantly, which is especially beneficial for low car volumes such as electric and hybrid vehicles. The weight saving is 30 percent compared to a comparable steel floor. This technology is compatible with the systems used to assemble car bodies and can be used for a multi-material approach with steel.
Another Plastic Omnium lightweighting innovation is a front impact beam for Hyundai Motor Europe that is 43% lighter. How did you achieve that?
Jerome Vidalie – The goal was to reduce the weight at the front of the car. So we replaced the steel solution with our composite solution. It represents a weight saving of 3.7 kg compared with the same part made of sheet steel. By combining a pultruded fibreglass and carbon fibre reinforcement overmoulded with a thermoplastic resin makes it possible to achieve high levels of performance at a competitive price. Its construction also means we can manage the pedestrian impact better.