Continuing just-auto’s series of interviews at the 2015 Equip Auto show, Matthew Beecham caught up with with Franck Cama, Country Manager France & Benelux for Henkel AG & Co. KGaA’s General Industry market segment and Head of Vehicle Repair & Maintenance Steering Unit – Western Europe.
What are the limitations of adhesives for automotive aftermarket applications?
Within the automotive aftermarket applications market in general (known as VRM = Vehicle Repair and Maintenance) and specifically for Henkel Adhesive Technologies there are various challenges that need to be addressed, such as process temperature, environmental conditions and application processes/equipment. The car repair workshop environment in the automotive aftermarket is fundamentally different to the OEM production line as the manual handling allows for certain liberties in comparison to the automatised processes in the production line. As a leading solution provider for adhesives, sealants and functional coatings worldwide we tackle these variables by continuously improving product performance/properties and allowing easy and reliable application. Apart from that, common challenges of both environments (workshop and OEM) are surface contamination (e.g. oil and grease on metal surfaces due to raw material production environment), different fixture and curing times based on specific applications (e.g. Direct Glazing products need to ensure fast drive-away times).
Is it a challenge when bonding new materials together to have the designers consider the adhesive before the design is locked in?
Yes, this is indeed a market challenge that all market participants are faced with. Henkel closely aligns with OEM customers or technical institutes that we cooperate with. This allows us to firstly, comprehensively assess the task at hand by thorough analysis and thereby in a second step, provide innovative solutions to fit the designer’s requirements. This enables innovation both in terms of product performance as well as design.
To what extent is it a technical challenge that the surface conditions of some new materials require a certain amount of surface preparation for adhesives to be used optimally?
How well do you really know your competitors?
Access the most comprehensive Company Profiles on the market, powered by GlobalData. Save hours of research. Gain competitive edge.
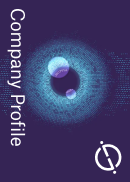
Thank you!
Your download email will arrive shortly
Not ready to buy yet? Download a free sample
We are confident about the unique quality of our Company Profiles. However, we want you to make the most beneficial decision for your business, so we offer a free sample that you can download by submitting the below form
By GlobalDataThe main technical challenge for all adhesive producers of newly developed materials such as composites, plastics, metals etc. is that these might show low energy surface properties. In effect this means that a pre-treatment (e.g. priming, mechanical and/or plasma treatment) is needed in order to create a bondable surface (or activated surface). As we are aware of this problem, Henkel provides a wide range of pre-treatment products and solutions, and additionally, supports with proven know-how of practical applications where needed.
I guess part of your company’s role is to anticipate trends far enough in advance so that you have a portfolio of adhesives that can be used with new materials. Is that correct?
Yes, this is correct. Henkel, with a worldwide scope in both Sales & Marketing teams as well as in Production and R&D sites, has all what it needs to serve customers around the globe. We have 169 manufacturing and 17 major R&D sites around the world that allows for both global reach as well as local market know-how. In Vehicle Repair and Maintenance our product solutions for maintenance, repair and refurbishment are designed with the aim to make every repair reliable and long lasting, and to achieve the same degree of quality as in the production process. The global cooperation with leading vehicle manufacturers enable innovative repair and maintenance solutions in the present as well as for the future. This puts us in the position to foresee future needs together with our customers and foster innovative developments, ultimately providing our customers with a competitive advantage in the respective market.
As we understand it, vehicle recycling is another major challenge for the adhesives industry with respect to disassembly. Carmakers are looking for adhesives that will cure within minutes (preferably seconds), retain that bond for years and then fall apart at the end of the vehicle’s life.
Yes, this is a major challenge within the adhesives industry. The combination of ‘Bond and dis-bond on command’ is an existing challenge that is not adequately solved within the market yet, even though fast bonding is possible in certain standard applications already.