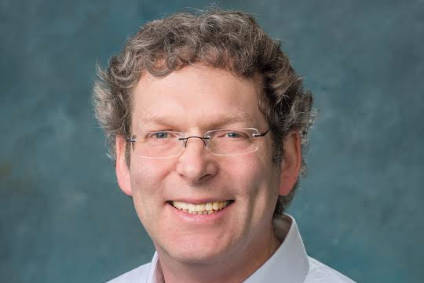
Lightweight materials is a hot topic in automotive manufacture in the battle to reduce carbon emissions. Now a technical partnership between engineering consultancy, Drive System Design (DSD) and international chemical and advanced materials company, Solvay SA, is exploring the potential for large-scale use of plastic composites in transmissions and drivelines. To find out more, we spoke to DSD’s president, North America, Shaun Mepham.
How did your technical partnership with Solvay come about?
The partnership began when we worked together on a plastic transmission housing to improve the NVH [noise, vibration and harshness] of an electric vehicle. It’s always good practice to work with a materials supplier from the earliest stage of design but, when the material properties are as different as polymers and metals, it is absolutely essential. The results of our collaboration were so effective that we decided to work together on an ongoing basis to explore wider opportunities, with DSD contributing the transmission know-how and Solvay the materials expertise.
What are the benefits of using plastic materials in transmission and driveline applications?
There is an immediate weight saving from substituting plastic materials for conventional metal castings but, equally important yet less obvious, is the potential to improve efficiency. The greater inherent damping provided by polymeric materials makes the transmission quieter, which allows us to use more efficient gear tooth geometry that would have unacceptable noise characteristics in a conventional aluminium casing.
How does that help the vehicle manufacturer?
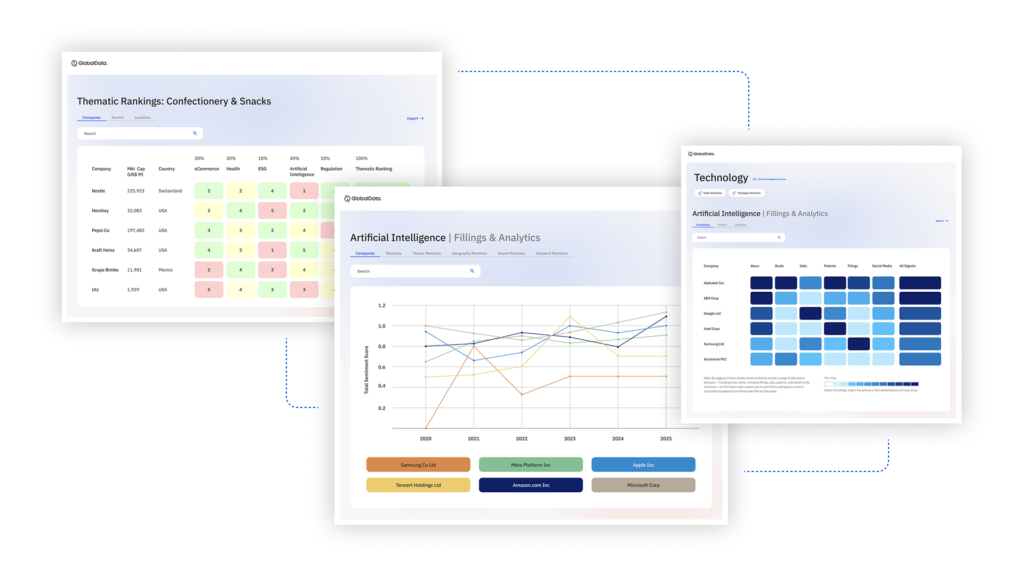
US Tariffs are shifting - will you react or anticipate?
Don’t let policy changes catch you off guard. Stay proactive with real-time data and expert analysis.
By GlobalDataManufacturers are trying to cut CO2 emissions by reducing vehicle weight and improving efficiency so that better use is made of all the energy consumed. This technology scores on both counts; by reducing vehicle weight, the energy required for propulsion is lower and, by improving efficiency, the energy wasted between the power unit and the wheels is reduced.
How big are the potential improvements?
Full implementation could produce savings of up to 25 percent in terms of the casing weight for a typical passenger car transmission although with an NVH ‘skin’ included this reduces to 10 percent. Efficiency improvements could be up to 0.5 percent per gear mesh, which is more significant than it sounds because the losses at each mesh are typically around 2 percent, so we are in fact reducing them by a quarter.
How will you overcome the perceived disadvantages, such as cost?
Cost is being driven down by the emergence of suppliers with the capability to produce plastic composite components in the quantities necessary to support vehicle manufacture. The cost equation for comparing plastic casings with metal castings is also becoming more favourable because it is now common industry practice to factor in a cost-per-kg allowance for weight reduction. When calculated on this basis, we believe a plastic transmission casing can be competitive with a conventional aluminium one.
Are there other challenges in applying this technology? What are you doing to address them?
New and unfamiliar materials bring pitfalls for the unwary because of the subtleties of the mechanical properties, which can change considerably over the operating temperature range due to non-linear behaviour. Polymers soften above their glass transition temperature (Tg) which can significantly affect mechanical properties: even the moisture absorption of polymers can influence properties.
Durability prediction has been greatly enhanced by effective FE [finite element] analysis, backed by proven data on mechanical properties and good appreciation of the influence of parameters such as mould flow characteristics and fibre orientation (for composites). Our preferred approach for a transmission casing is composite construction involving over-moulding a polymer around a structural frame to provide a continuous barrier against any ingress of oil which could otherwise infiltrate the composite layers and cause delamination.
Where do you expect the first applications to be? What vehicle types?
The potential exists for shafts, casings and hydraulic cylinders to be made from plastic, suitably reinforced where appropriate. The first applications will be those where good refinement and maximum efficiency are crucial, such as premium electric vehicles.
Currently, the technology is in the development phase to optimise the most suitable materials and processes; we anticipate a five- to ten-year timescale before the first applications come to market. As manufacturing volume increases and economies of scale reduce unit costs, mid-market hybrid vehicle applications could follow. Ultimately, the technology will be used on volume passenger cars.