Continuing just-auto’s series of interviews with tier one manufacturers, Matthew Beecham spoke to Bill Presley, Vice President Engineering, Wire/Terminals & Connectors, Lear Corp about the forces pushing innovation in the automotive wiring harness industry as well as some alternatives to traditional wiring.
To what extent has greater functionality led to complex architectures in modern vehicles?
Greater functionality is actually what’s driving complex architectures. What I mean by that is, in the past, more functionality meant more circuits. Functions were “hard switched”. However, emissions standards are getting tougher so vehicles need to get lighter and everyone wants to maximise space utilisation. That means engineers need to be able to fit more functionality into the same amount of space or less space than vehicle engineers had in the past.
As a result architectures have had to become far more intelligent than they were in the past. A multitude of functions can now be controlled through the use of electronic modules, control strategies and communication strategies.
What makes Lear unique is that we are one of the few suppliers that have technical expertise in all of the building blocks of the architecture, specifically electrical centres, electronic modules, terminals and connectors and wiring. In addition, Lear has a state of the art tool suite known as the Lear Virtual Proving Grounds which allow us to optimise the design in the virtual world. We can iterate the design very rapidly to optimise the entire system prior to building any physical parts.
In what ways has Euro 6 led to Lear to design the engine harness differently?
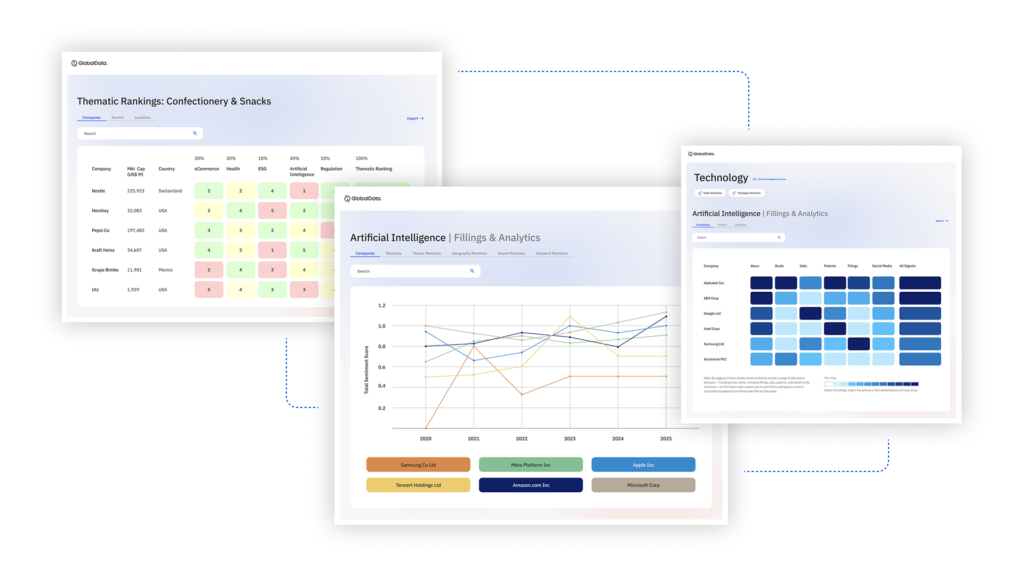
US Tariffs are shifting - will you react or anticipate?
Don’t let policy changes catch you off guard. Stay proactive with real-time data and expert analysis.
By GlobalDataThe addition of more sensors and components to meet the emissions requirement has led to more circuitry. It largely depends on the OEM strategy to meet the emissions requirement but in general it adds more content and circuitry which makes routing more challenging. Strategies differ amongst the OEM’s on how they want to measure emissions and control the output. But as an example, adding UREA tanks, Exhaust Gas Heaters and NOx sensors to a vehicle can mean an additional 50 circuits to an engine harness. Going back to what we said earlier, the vehicle can’t get heavier, so we’ve had to find more innovative ways of reducing size and weight while increasing the content.
So could you talk us through an example of how Lear has reduced engine harness weight?
Let me start by providing a little backdrop. Approximately 70-80 percent of the loads found on a vehicle are less than one amp. However, 80 percent of the wire volume purchased is between 0.35-0.5 mm2 which means 70-80 percent of the circuits on the vehicle are over gauged for the actual load they carry.
Wire suppliers are constantly developing alternative materials that meet impedance requirements but also have superior mechanical strength when compared to a copper wire of similar size. This allows us to substantially downsize the wire to shed size and weight.
It’s important to understand that backdrop because it gives perspective to the methodology.
Lear starts with a thorough load analysis to insure that the right cross sections are assigned for the actual load requirement. Lear Engineers will use Lear’s expansive alternative conductor catalog to pick the smallest wire size possible while still meeting the impedance requirements.
We might use copper clad steel in an instance where we need strength but we can tolerate a higher level of resistance. If impedance is a factor, like in a communication bus, we might choose copper-tin to reduce the size. Lear’s alternative materials can be used to replace 0.35 mm2 circuits with circuits in the range of 0.13mm2 to 0.08 mm2 while maintaining the strength and impedance requirements associated with a larger copper wire.
Once the analysis is complete for the smaller gauge wire we shift our focus to the heavy gauge copper cables, and when I say heavy gauge I’m talking about 0.75mm2 or greater copper cables. Circuits of those sizes are a prime candidate for aluminium conductor utilisation because the aluminium provides about a 40 percent weight reduction when compared to copper. Take an instance where today’s vehicle package has the battery in the back but the alternator and starter are still on the front end accessory drive of the engine. That battery cable in copper might weigh 30 pounds or more but you can do it with less than 20 pounds of aluminium. That’s a significant weight savings that translates into fuel economy.
Once the Lear Engineers have optimised circuit size, they move into the mechanical optimisation by utilising the mechanical tools in Lear Virtual Proving Grounds. The Lear Virtual Proving Grounds allows Lear Engineers to predict the physical routing on the engine with a high degree of accuracy utilising Finite Element Analysis and Lear proprietary algorithms. This allows Lear to develop a custom protection and covering solution for the harness to insure we are applying coverings and protections only in the required areas as opposed to penalising the weight of the entire harness system with a generic covering solution.
In terms of “low-cost architecture” what does that actually mean in reality?
Sometimes people tend to think about the vehicle as a series of components. Let’s take the electrical system as a subsystem. They might think of that as a series of components – controllers, wires, terminals, connectors. In a low cost architecture approach you don’t want to think about it as simply optimising each component individually, you need a holistic systems approach, meaning an architecture should be thought of as a total system and not just connecting various things together.
The OEMs are concerned with four things: they want lower cost, lighter weight, smaller package size and higher quality, so by optimising the entire architecture and optimising that equation you’re delivering the lowest cost architecture possible with maximum functional integration. When Lear talks about a low cost architecture we don’t mean low cost components, we mean if you look at the whole system and add up the total cost of the system, there’s an optimal way to achieve the goals that the OEMs have through an efficient architecture.
Again, that’s where a company like Lear has a significant strength to bring to the marketplace because we do total system design. Lear can provide a service and evaluate those trade-offs. As stated earlier, Lear has expertise in all of the building blocks of the architecture. Specifically, electrical centres, electronic modules, terminals and connectors and wiring.
How do you see pre-formed engine harnesses evolving? Is it limited to certain niche applications or a mainstream technology?
It has always been mainstream technology if you think about it. Since the first wire harness was put on a vehicle there have been brackets to control the routing. That is “preformed”. So pre-formed has always been mainstream, but the question is now: how can we do it more efficiently? Where exactly is it needed and what is the best solution to implement it while you minimise size, cost and weight.
It goes back to what I talked about in the Lear Virtual Proving Grounds. We design the wiring harness in 3D utilising the customer data of the engine and engine bay. We then simulate the manufacturing environment of the wire harness itself which introduces a series of stresses and impacts how the wiring can be bent, routing and contoured in the vehicle. We utilise the stress curves introduce in the manufacturing simulation coupled with the materials library that Lear has compiled to enable Finite Element Analysis utilising Lear proprietary algorithms to predict how the harness will actually fit on the engine.
Once the actual fit of the harness is simulated we calculate the degrees of freedom in the harness. What I mean by degrees of freedom is all the places that the harness can move, because it’s a flexible animal between the fixation points on the engine. We then put the model representing the degrees of freedom back into the vehicle environment in order to determine where exactly the routing needs to be strictly controlled or pre-formed. This provides for a very efficient solution.
I guess there will always be alternatives to traditional wiring – such as fibre optic, wireless and multiplexed systems – yet the challenge comes with those alternatives to compete on cost, quality and reliability on a consistent basis?