
With two recently revised models launching on the European market, Toyota is upbeat over prospects for the plant that makes them at Burnaston, in the UK. Dave Leggett caught up with Toyota Motor Manufacturing UK Deputy Managing Director Tony Walker for an update on UK manufacturing operations.
DL: Burnaston turned out 172,000 cars last year, how is it looking this year?
TW: It should be more. Of course, we had the model changeover in May, which entails the run-out of the old model and start of the new model. This year’s total production will probably be around 180,000, and that’s a full-year ‘rate’ of around 190,000.
DL: And the Avensis/Auris split?
TW: It is very heavily Auris these days. It’s about 35,000 Avensis and 145,000 Auris. And some 55% of the Auris is hybrid, which is amazing. We are pleasantly surprised and it’s very good for us. It’s good for the plant also to have the hybrid so high in the mix; it gets the revenue up.
DL: What percentage of Burnaston’s output is exported?
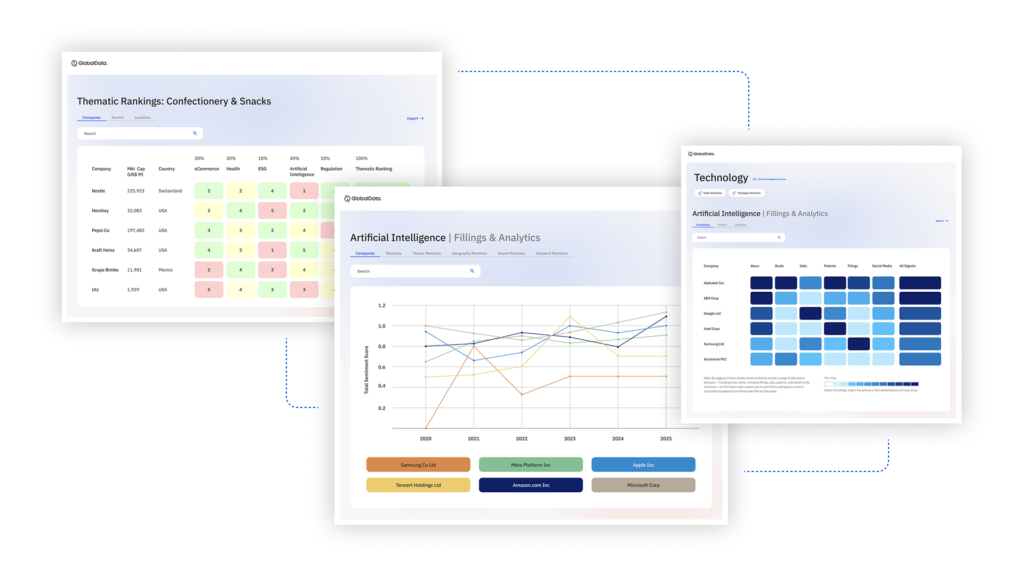
US Tariffs are shifting - will you react or anticipate?
Don’t let policy changes catch you off guard. Stay proactive with real-time data and expert analysis.
By GlobalDataTW: Last year it was 85%, the previous year was 89%. It was slightly down last year because the UK market was relatively buoyant, compared with the continental European market. I think with the European market recovering, it’s going to be 85% minimum this year and more likely towards 89%, but it is a bit early to be sure.
DL: So, you are seeing recovery in Europe, but it is slow?
TW: Yes, it is a very slow recovery and there are black spots like Greece, Russia, Ukraine, but elsewhere it’s a recovering market.
DL: Just looking at the Auris Hybrid, how much of that goes to the UK market?
TW: Auris sales in the UK last year were 19,109 units and just under 50% of that was hybrid. This year we are hoping to break 20,000 units, so around 10,000 will be the hybrid. So, that’s 10,000 units on Auris Hybrid of 70,900 in total last year. France is quite a big growth market for the hybrid at the moment; they like low emission vehicles in the Netherlands and the Nordics.
DL: Do you ship cars to markets outside of Europe?
TW: No, not from the Burnaston plant, with one exception: the Avensis Estate car which we export to Japan. In fact, the only vehicle sold by Toyota in Japan but not made in Japan is that car. We are very proud of that. The Japanese customer is so demanding in areas like paint and finish, that is actually a good challenge for us on quality standards.
DL: In the wake of the Greek debt crisis, the euro currency has lost value against sterling lately. Is the sterling-euro exchange rate a big concern for you as a major exporter to the continent?
TW: No, not really, because although most of our vehicles are sold in euros we also buy most of our parts in euros, even from our UK suppliers. A few years ago we underwent what we call ‘eurolisation’, which means we are effectively hedged on short-term exchange rate movements. The biggest cost for us is parts and materials, that we buy in euros. Most of the products we sell in euros. We are effectively hedged.
DL: What about the capacity situation at Burnaston? Can you do 200,000 units a year on a single line?
TW: Yes, it is possible. That would be our maximum capacity with maximum overtime and our fastest Takt* speed of 66 seconds. We are running at 66 seconds now, on two shifts and the maximum overtime we will schedule is an hour a shift and two Saturdays a month. That will get us over 200,000.
DL: How far over 200,000 units could you go?
TW: From an employee relations point of view, we can’t always work all that overtime. Theoretically, we are approaching a 210,000 units level, but practically we would not consistently run at that rate. It wouldn’t be reasonable. The real limit is between 200,000 units and 210,000 units.
DL: What about the second line at Burnaston, which was mothballed in 2010? Is that any closer to being reopened?
TW: We would love to reopen that second line if we could, but at the moment that is not planned. We do not have the demand or the volume to justify that. From an efficiency point of view, it is best to run a single line at its fastest and most productive speed.
DL: Is there a point, though, at which the complexity of assembling multiple models on a single line boosts the case for reopening the second line?
TW: You might think so, but there is a lot we can do to manage that complexity. The line at Burnaston is making 155 major variants and is one of the most complex production lines, in terms of numbers of variants, run by Toyota anywhere in the world. We have Avensis, wagon, sedan, Auris, wagon, hatch, petrol, diesel, hybrid, manual, automatic, LHD, RHD, high grade, low grade…anyway, it adds up to 155 major variants, which is extremely complex. And we can manage that.
There are no plans to restart the line.
DL: There is, though, potentially room to add another model to the plant in the future?
TW: We would love to. The ideal target would be something that is more premium. We don’t have anything particularly in mind. In the medium term we will be introducing the Toyota New Global Architecture (TNGA). It’s a completely new platform, simpler and with a much more modular design, lighter weight materials and we’ll be going to ‘simple and slim’ techniques on production. So, it’s also about new global production standards, which means slimmer and simpler production equipment that is more flexible – which can enable changing model more easily, with less need for new tooling.
DL: And TNGA spans different vehicle segments?
TW: Yes, there will be several TNGAs but we are talking about the C-segment version. There will be a partial introduction in Turkey with a new vehicle that will start production in 2016 and we will have the first full new C-platform introduction for the next generation Auris that will be between 2018 and 2020.
And by the end of the decade, half of Toyota’s global production will be on TNGA platforms. The modularisation means more commonisation of parts and lower costs.
DL: Because of the investment required, reactivating the mothballed line at Burnaston would be a big decision wouldn’t it?
TW: Yes, it would. The longer it stays mothballed, the bigger is the investment required to restart it. But as I say, there are no plans to restart the second line at the moment.
DL: Thinking about component sourcing, how much comes in from outside of Europe?
TW: It’s mainly on hybrid components – the battery, inverter, transaxles coming in from Japan. We are also importing automatic transmissions. European content is high though, with engines from Deeside, manual transmissions from Poland, medium-sized diesels from Poland (and some Euro 6 compliant diesels come from BMW) and a full range of parts and components come from suppliers in Britain and across the continent.
DL: Besides the engines, what sort of components can be easily sourced in UK?
TW: Seats, wheel and tyre, interior trim, stamped components (we stamp our surface panels ourselves, but there are things like stamped sub-frames that we source locally), exhausts, driveshafts. In general, it’s heavy and bulky parts that are made as close to the plant as possible.
There are nine Toyota plants in Europe with central purchasing in Brussels. So parts that are manufactured in the UK by suppliers are also going to plants across Europe. Toyota Motor Europe is spending around around GBP900m a year with UK suppliers and 30% of all TME suppliers are in the UK. The UK has the largest concentration of suppliers by country. TME plants have 70 UK Tier 1 suppliers and many more Tier 2 and Tier 3 suppliers.
The UK is holding its head up. Having said that, I am also on the UK Automotive Council [a UK government body setting strategic goals and policy framework for investment in the UK automotive sector]. A supplier sector initiative has seen the creation of the Automotive Investment Organisation (AIO) led by Joe Greenwell. One of its targets is the reshoring of first tier suppliers. Some of it is happening, but many of us feel it’s not actually happening as well as it might. As the OEMs in UK increase volume, an opportunity is being created, but we need some of the big European first tiers if we really want to improve our UK supply base.
And the recent experience with the Calais ferry strikers dispute also suggests that we need to think more about our security of supply. It’s a subject we have to think more about in the future, in my view.
DL: That French dispute caused you considerable disruption?
TW: Yes. It meant we stopped production for a day and a half in the Desside engine plant. The lost output is recovered now. We also had some delay at Burnaston. We are making 888 cars a day and the delay amounted to around 350 cars. We made it up with overtime, but there is a cost and there is disruption.
DL: I guess that’s an ever present danger with Just-In-Time manufacturing and potential bottlenecks in logistics. Can you hold some inventory in the UK to guard against such events?
TW: Yes, we can and we are reviewing that. But it’s a balance – the cost of holding inventory versus the risk or cost of disruption to supply. Holding inventory can also be quite complicated, because we are sequencing everything in manufacturing. Which bit of inventory do we hold? I can say it is something we are studying now.
DL: What do you see as the big challenges in manufacturing cars?
TW: The first big challenge we have as volume carmakers is cost itself. However, that is heavily offset by good productivity and labour flexibility. I don’t mean the flexibility to hire and fire, I mean the flexibility to work overtime, flexibility to employ agency (it fluctuates, 10-15% of the TMMUK workforce), for example. We have excellent flexibility.
DL: What do you mean by cost?
TW: Purchasing is in Brussels, so at plant level, cost is utilities, labour. The cost of labour is two-thirds of our plant cost. And then there is utilities as the next biggest element. Maintenance is next and things like safety. It’s a lot to manage.
DL: And other big challenges?
TW: The next big challenge is to compete inside Toyota for future models and investment. In order to compete, we are measured against a series of KPIs. Key KPIs are quality and productivity. Of course, we are also looking at things like safety and our environmental impact, but the real bottom line issues are quality and productivity. The competition is very tough; we are up against very good plants in places like Japan and China. We are roughly in the middle of the pack in terms of the global Toyota list of plants. And we are also measured twice, on Avensis and Auris.
DL: Is high cost of raw materials an issue?
TW: It is a concern because it’s always very difficult to pass extra costs on to the consumer – who is demanding more features at lower price. But it is, more or less, the same for all vehicle manufacturers. Managing cost – making the cars for less cost per unit – is an on-going issue.
*Takt time, derived from the German word Taktzeit, is the average unit production time needed to meet customer demand. Vehicles are assembled on a line, at a certain cycle time, ideally being moved on to the next station within the takt time so as to neither over or under produce.
See also: VEHICLE ANALYSIS: Toyota Auris adds clever small gasoline engine
Tony Walker
Deputy Managing Director,
Toyota Motor Manufacturing (UK)
Tony joined Toyota at Toyota Manufacturing UK, as General Manager, Human Resources in 1990. As one of the first employees of Toyota Manufacturing UK he played a fundamental role in the establishment and development of the company.
From 2001 to 2010 he worked at Toyota Motor Europe in Brussels, holding various positions, including European Human Resources Vice President and Director European Production Planning and Project Management.
Tony returned to Toyota Manufacturing UK in January 2010 to take up the role of Deputy Managing Director, with direct responsibility for the functions of Production Control, HR, Accounting & Finance, Corporate Planning and External Affairs. In April 2014 he also became Managing Director of Toyota Motor Europe London Office.
Tony is Vice President of the SMMT (Society of Motor Manufacturers and Traders), is Chairman of the Automotive Council UK International Competitiveness Workstream and Chairman of the Lowland Derbyshire & Nottinghamshire Local Nature Partnership.
Tony has worked for Toyota for 24 years and in the motor industry for 37 years.
He graduated from Newcastle-upon-Tyne University with a BSc Hons in Psychology in 1977, taking up a graduate trainee position at Ford Motor Company. In 2013 Tony was awarded an honorary doctorate of Business Administration (DBA) from Nottingham Trent University and in 2015 received an honorary doctorate from the University of Derby.
Tony is married with three grown up children.
Toyota’s European Manufacturing Plants
Country | Company name | Start of operations | Main products | Annual output |
(000s) | ||||
Czech Rep | Toyota Peugeot Citroen Automobile Czech, s.r.o. (TPCA) | Feb 2005 | Aygo | 203 |
France | Toyota Motor Manufacturing France S.A.S. (TMMF) | Jan 2001 | Yaris (Fitz) | 225 |
Poland | Toyota Motor Manufacturing Poland SP.zo.o. (TMMP) | April 2002 | Engines, Transmissions | – |
Poland | Toyota Motor Industries Poland SP.zo.o. (TMIP) | March 2005 | Engines | – |
Portugal | Toyota Caetano Portugal, S.A.(TCAP) | August 1968 | Dyna | 2 |
Turkey | Toyota Motor Manufacturing Turkey Inc. (TMMT) | Sept 1994 | Verso, Corolla | 130 |
UK | Toyota Motor Manufacturing (UK) Ltd. (TMUK) – Burnaston | August 1992 | Avensis, Auris, Auris Hybrid | 172 |
UK | Toyota Motor Manufacturing (UK) Ltd. (TMUK) – Deeside | August 1992 | Engines | – |
Russia | Toyota Motor Manufacturing Russia (TMMR) Limited | Dec 2007 | Camry | 36 |
Russia | OOO Sollers-Bussan | Feb 2013 | Land Cruiser | 14 |
Kazakhstan | Saryarka AvtoProm LLP (SAP) | May 2014 | Fortuner | – |
Source: Toyota