
America’s Steel Market Development Institute (SMDI) is a business unit of the American Iron and Steel Institute (AISI). Founded in August 2008, the SMDI was previously known as AISI’s Market Development programme.
SMDI’s objective is to grow the markets for steel in the automotive, construction and container industries and for value-added long products, as well as in non-traditional steel markets such as energy. The SMDI also influences local, State and Federal officials concerning the benefits of steel to ensure legislation that provides a level playing field for steel products and practices.
Lawrence Kavanagh – president – is responsible for developing and executing strategies to advance the competitive position of steel in multiple markets. Prior to his appointment in 2009, he served as American Iron and Steel Institute VP of Environment & Technology. Mr. Kavanagh came from Davy International’s Automation Services Division – now doing business as Kvaerner and Voest-Alpine -where he was responsible for all phases of steel and aluminium industry capital project execution.
Ronald Krupitzer is VP Automotive Market for the Steel Market Development Institute. He manages the research, education, and technology transfer work of the Automotive Applications Council (AAC), an organisation of major North American automotive steel producers.
The AAC’s work focuses on the development of new steels and related technologies to satisfy the needs of automotive customers. Previously, he held both engineering and manufacturing management positions at Chrysler and at Republic Steel (now ArcelorMittal) and joined AISI in 2001.
Krupitzer’ s recent work has focused on the increasing role of advanced high-strength steel in vehicles to improve mass efficiency, lower cost and reduce environmental impact. His recent work on life cycle assessment as applied to automobile greenhouse gas emissions and the role of materials is relevant to design considerations for today’s environmentally friendly vehicles.
Both spoke to Simon Warburton from Washington DC and Detroit respectively with regard to their take on the booming US market and the role of steel in the current debate concerning aluminium.
How well do you really know your competitors?
Access the most comprehensive Company Profiles on the market, powered by GlobalData. Save hours of research. Gain competitive edge.
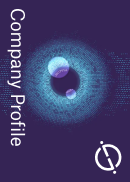
Thank you!
Your download email will arrive shortly
Not ready to buy yet? Download a free sample
We are confident about the unique quality of our Company Profiles. However, we want you to make the most beneficial decision for your business, so we offer a free sample that you can download by submitting the below form
By GlobalDataj-a: How would you characterise the US automotive market currently and was the recent North American International Auto Show – where you exhibited – proof of an American resurgence?
LK: There are a lot of exciting technologies going into different vehicles, most completely on the engine and drivetrain side as everybody works towards meeting the new fuel economy standards.
Whenever there is new technology being discussed and introduced, that is a great positive and that is [why] we were there [Detroit] to talk about all of the steel making manufacturing techniques and new materials.
We had examples of steel parts equivalent in weight to aluminium and cost.
j-a: The US has mandated its Corporate Average Fuel Economy (CAFE) of 54.5mpg (23.2km/l) regulations for the end of the 2025 model year. Is this realistic?
LK: Each year there is about a 4% increase going to 54.5mpg as a fleet average and obviously [how] that is going to be done is getting your biggest increase in fuel economy from engine and drivetrain advancements.
That is where we contribute to the fuel economy equation. We have stated this several different ways, especially using the same models that EPA [Environmental Protection Agency] and NHTSA use to set the rules.
Even if you fall short by 10%-15%, you can still meet your fuel targets with steel. Suspension parts is where we had the show and tell [in Detroit] – the same as aluminium but 34% less cost. We are [also] working on doors, wheels and body-in-white.
The [54.5mpg agreement] was made between carmakers and the US government. We argued regulations should be considered on lifecycle emissions, not just on driving emissions.
That was too big a bite for them. Whether it is doable will come out in the mid-term review in 2018.
Right now we enjoy a significant advantage over materials like aluminium and carbon fibre. If we are able to match the weight of an aluminium part or even get close to it, it blows up the aluminium business case.
We are working on vehicles with our customers to 2017/2018/2019, to achieve their lightweighting costs with our materials.
j-a: There was much talk of Ford’s new F150 pick-up at the Detroit show shaving considerable weight using lightweight materials to yield a saving of 700lbs versus the current model.
The use of high-strength steel in the F-150 frame has been increased from from 23% to 77% to save up to 60lb of weight, while the ‘military-grade’ aluminium-alloy body in combination with the high-strength steel frame, is also used. What’s your view?
LK: Ford is a great customer of our industry and recently [there was] the contribution of advanced high strength steel in the F150. Their decision was made a long time ago.
We are focused on the future and there is a long history in automotive for parts to go to one material and then changing back to steel.
Cars are multi-material vehicles and they have been for several years. Steel is plus or minus 60% of the average weight of an average vehicle on the road today.
In the end, when you are building these vehicles in 2019, they are going to be on the road in 2025. They are going to be steel-intensive vehicles because that is the most cost-effective for our customers and for consumers.
As people begin to understand the environmental impact of material selection, they are going to understand the lowest emitting vehicles on the road are steel vehicles when you consider life-cycle.
j-a: How do you characterise the evolution of steel?
RK: We are going to see this period of experimentation, followed by some aluminium remaining, but [also] some transferring back to steel.
We are going to have a whole new collection of steel products that will be affordable. We predict this period of experimentation will last five to six years.
j-a: How do you view the electric vehicle debate?
LK: Unless you live in California, these are not selling. US$8 is not happening and we have not even tapped into shale gas. This whole thing may get stood on its head in 2018.
j-a: How does the SMDI work with the various regulatory authorities in the US?
RK: We have a good working relationship with the Environmental Protection Agency, so our engineers are working in concert with them. They have published a number of papers together with NHTSA showing the cost effective weight reduction of steel. Steel can do an amazing amount of weight reduction.
We do have a Washington DC presence, which is the leadership group and we also have an engineering group out here in Detroit.
We are trying to convince the regulators and the car companies to stay with steel, because we have only just begun the best weight reduction possible. We have a distinct advantage working with the car companies.
j-a: Is the SMDI apolitical?
LK: It [does not] matter whether we are talking to a Democrat or Republican [politician]. Our job is to develop technologies to advance steel application.
j-a: Do you see the automotive market in the US maintaining its present rate of recovery? Some have even mentioned 17m or even 19m as a figure – is that possible?
RK: The North American automotive market is kind of unique – not racing to the old numbers but very steadily growing – it has been one of the strengths of the steel recovery too. We are very happy automotive has recovered as quickly as it has.
The number of 19m would be North American production by 2020 – it is a very steady incremental rise. It is buoyed by continued demand and by the fact the average age of vehicles is 11 years old now.
j-a: How do US drivers view environmental concerns when it comes to automotive?
LK: I would like to believe our fellow citizens care about the environment and it will become more and more of an issue. There is a segment of customer that considers that more widely as a factor [which] influences purchases.
We did a detailed survey of SUV and truck buyers and a very high percentage of them thought materials were a big factor, especially when they found the majority of vehicles today are made from steel, which they associate with safety.
j-a: How many people does the steel industry employ in the US and how do you view Free Trade Agreements?
LK: The steel industry directly and indirectly supports more than 1m US jobs, employs nearly 153,000 people and produces US$95bn in shipments.
Right now, North America, particularly in the US, we are among the low cost producers in the world, due to our raw materials and level of automation of our facilities.
What we say in the US is we can compete with any steel company in the world, but we can’t compete with governments. One of our top priorities is to maintain the strength of our trade laws, that Free Trade Agreements [are] fair trade.
As long as trade happens in accord with the rules, we feel we can compete.
j-a: What is your membership?
LK: Our membership represents more than 80% of the steel makers that supply the construction market. More than 90% supply the container and automotive markets.
The value of working collaboratively is strong, especially in automotive, where the pooling of resources allows you to not repeat mistakes.
Just imagine ten to 15 companies trying to individually develop the next generation of lightweight. You do that all together, you get there faster.
According to the SMDI, during the past decade, advanced high-strength steels (AHSS) have become the fastest growing material for vehicle use. AHSS are stronger, lighter, and have low emissions, helping automakers decrease a vehicle’s life-long carbon footprint.
The Life Cycle Assessment (LCA) approach takes a vehicle’s entire environmental impact into account by looking at greenhouse gas emissions from each phase of its life.
LCA shows steel, which currently makes up about 60% of the average North American vehicle, with the SMDI claiming it generates fewer emissions than other automotive body materials.