US Tier 1 supplier giant Delphi is backing diesel’s long-term growth with an EUR10m investment in its expanded advanced diesel and combustion centre in Bascharage, Luxembourg. For the first time it is bringing together expertise in both petrol and diesel injection systems and technology under the same roof. Ian Adcock heard about Delphi’s strategy from John Fuerst, Delphi’s president powertrain systems.
Whilst Mazda, with its SkyActiv engine development teams, employs a similar technology strategy to Delphi it would be inaccurate to read too much significance into this move, says John Fuerst, Delphi’s president powertrain systems. “When you’re tackling thermodynamic problems at the spray laboratory where you’re modelling 300 or 1800 bar, a lot of the fundamental analysis and FEA is the same; it’s more mathematical so it makes sense to have people together and sharing. But as you move from product design to manufacturing I think there are significant divergences.
“From a Delphi powertrain perspective we see parts of gasoline and diesel where’s there is important sharing to do here in Luxembourg and that makes sense. But, by the time we get to designing a high pressure diesel pump in Gillingham or high pressure GDI pump in Rochester, the extent of co-operation there is periodic technical reviews and round table workshops where the discussions are about materials, lubricity, tribology and what our customers are doing – it’s a technical exchange.”
However, with the growing adoption of GDI, Fuerst predicts that 80% of petrol engines will be running it by 2025, with pressures upwards and in excess of 300 bar, the expertise and knowledge gained engineering injector nozzles for 2000 bar diesel systems will offer the potential for the exchange of ideas and processes between diesel and gasoline. “That gas injector wall is getting thicker and at some point we may need to do something similar [to diesel]. On the other hand when we talk about deposits there’s a little more commonality; admittedly, gas and diesel chemistry are different, but you have a combustion chamber and you’re concerned about deposit and stress corrosion and things like that, so there are more deep technological questions, as well as mathematical, engineering and material issues, where you get some value from that exchange.”
As Delphi’s headquarters for advanced petrol and diesel fuel injection and combustion development, the Luxembourg facility is one link in a chain of global centres that includes technology sites in France, UK, Romania, Turkey, India, China and the USA. Whilst Fuerst says Delphi “aspires” to a global development programme, he adds that, “I would be stretching it to say we are 24/7 around the world. Once upon a time there was an image that you could spend eight hours designing this widget in Luxembourg, then send the file to Shanghai for eight hours development, then it would go to Rochester, but that’s crap. It doesn’t work because you need continuity, where you left your work when you go home at night – nobody can pick that up, only you the next morning when you start working on it.
“Nevertheless, there are parts of designing a product, say the material analysis, some Finite Element Analysis (FEA) that are computer based. And where you have changed design at the end of the day and you need an FEA turned round on that, you can send that to Bangalore and the next morning have the results. That sort of partitioning works, so overnight you can be doing the modelling and algorithms and by day at Luxembourg you’re doing hardware design.
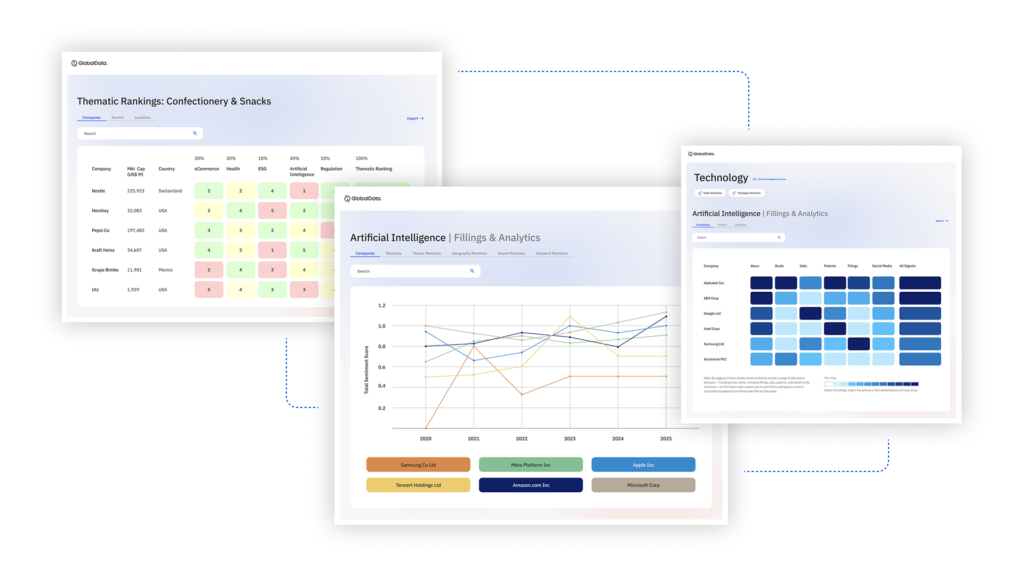
US Tariffs are shifting - will you react or anticipate?
Don’t let policy changes catch you off guard. Stay proactive with real-time data and expert analysis.
By GlobalData“There is value being in multiple time zones, but sometimes you need the continuity of one brain following one issue and keeping it organised.”
Fuerst is also bullish about diesel’s long-term prospects, not just in Europe but also in the USA, Brazil and China, although he concedes that the latter trio are moving at an “unpredictable” rate in their appreciation and evaluation of diesel.
The nervousness some diesel engineers had about achieving future emission levels he says are unfounded and he likens it to the time in the early 1990s when, as a gasoline engineer, he thought they would never achieve ULEV never mind SULEV requirements. “Back then gasoline people thought we wouldn’t get there with platinum at $10,000 a troy ounce; noble metals generally were going out of sight. But people buckled down to it and today we have ULEV and SULEV, whilst SCR is a powerful chemical tool against NOx in diesels, but I couldn’t go along with those that say diesel is a goner because of emissions.
“It’s our job to worry about how we get to 95 g/kms CO2, our job to take it seriously and figure out how to do a really good job so we don’t fail.”
Long-term, says Fuerst, there will be a cost gap between petrol and diesel that will always affect the lower end of the market where there is greater price sensitivity, especially in times of economic hardship when the additional EUR1,000 for a diesel is often beyond many customers’ pockets, even though the long-term fuel efficiency gains even out the net spend.
“There are fundamental things about diesels that drive the cost: fuel injection equipment costs more as you inject at 1800 bar instead of 200 bar GDI; you have to spend money pressurising the fuel and once you’ve done that, there are higher compression and combustion pressures; there’s the block, head, gasket, stronger con-rods and so on.”
Looking to the future, he says the next big stumbling block is to achieve “better injection control over a wider range of operating parameters.”
“How much wider can we control the dynamic spray of a fuel injector? The bigger that spread is the more capable we are to help the OEM deliver peak power where we have to put in a lot of fuel really quickly to be atomised. But, then, can we also come all the way down to idle performance and minimum pilot injections? By expanding that range, emissions and power are improved.
“If we can have a variable speed fuel pump using a brushless motor linked to intelligent injectors that feed back real time data on precisely how much fuel is required under all operating conditions, we will achieve more responsive and efficient engines, diesel or petrol.
“And if we look at the ideal thermodynamic efficiency to where we are now, I guess we’re in the range of two-thirds of the way there. We’ve got decades of work in front of us with good business cases.”