just-auto spoke with Dr Thomas Heckenberger, VP engineering for Delphi Thermal Systems at its Thermal Systems European headquarters in Luxemburg to understand the latest product developments and innovations from Delphi in relation to interior HVAC systems.
just-auto: Could you outline the main drivers that are influencing the HVAC market?
Thomas Heckenberger: When looking at what is driving the market it is important to understand that we are very much a customer focussed organisation and the main drivers come from the vehicle manufacturers and legislation. One of the most significant drivers is legislation and the quest for reducing fuel consumption and CO2 emissions. Current legislation offers efficient HVAC systems a credit which is very important. For example in the US, from 2016 we will have a 19.54 gCO2/mile credit available for passenger cars comprised of 13.8g for reducing leakage and 5.7 for energy efficiency. For trucks, the numbers are 17.2 and 5.7 to give a total available credit of 22.9. Delphi is focussing very much on energy efficiency and works in very great detail on each component to offer customers the possibility to take advantage of the full 5.7g CO2/mile credit. Similarly with leakage, which is largely related to the connectors, hoses, seals and the amount of refrigerant charge in the system.
j-a: What other drivers are influencing the market?
TH: In addition to legislation we also have noise requirements. As the demand for quieter cars increases, especially in the premium and upper segments then we need to find solutions for making the HVAC systems much quieter.
Weight reduction is also very important and here we are looking at ways to make the condenser lighter, which also improves the dynamics of the vehicle by taking mass away from the front axle overhang. There is a trend to smaller compressor systems and this is becoming even more important today as we are competing for package space in the vehicle with the infotainment system and driver assistant safety systems. However, reducing this size of the compressor brings additional challenges. For example if we reduce the size of the compressor ducting the velocity of air is increased and it results in a higher noise resulting in conflicting aims between noise and size.
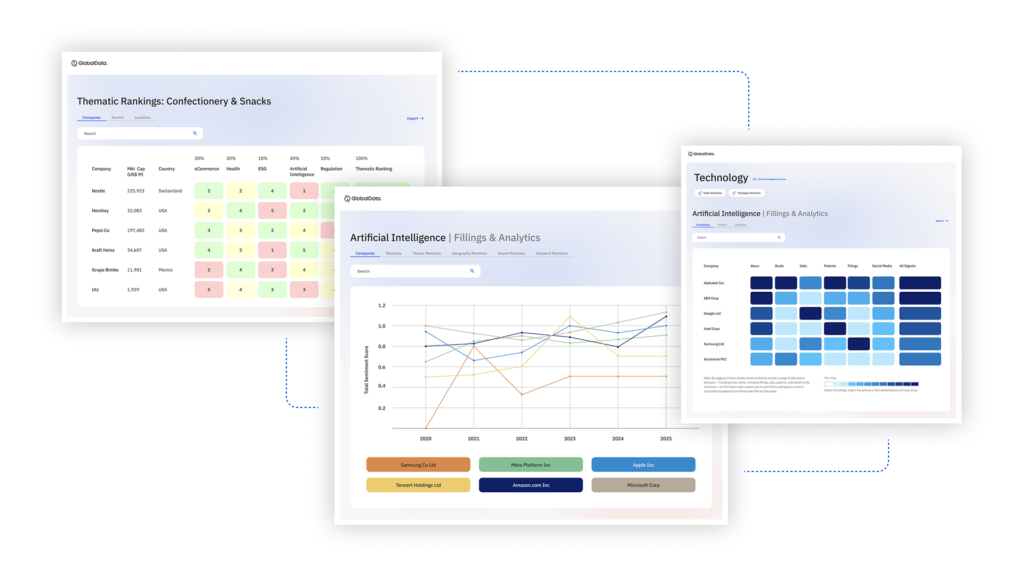
US Tariffs are shifting - will you react or anticipate?
Don’t let policy changes catch you off guard. Stay proactive with real-time data and expert analysis.
By GlobalDataj-a: Can you relocate the HVAC unit elsewhere in the vehicle to relieve this pressure on space?
TH: No. There is no physical reason why not but experience suggests it is already in the optimum location. A halfway solution for larger vehicles is to provide two smaller units, one at each end. This helps reduce the packaging challenge and provides very good comfort, but it is costly. That is why we are looking at new control solutions for larger vehicles using a front system only. Additionally, we have been working on the Unitary HPAC (Heat Pump and Air Conditioner) which takes the refrigerant system and contains it within a lunch-box sized container. This system cools/heats coolant which can then be delivered to any point in the vehicle. This HPAC unit can be located anywhere in the vehicle.
j-a: What are you doing to address the conflict of noise versus size of compressor?
TH: Delphi is developing silent, quieter blowers using smaller, more efficient motors/blower designs. We are working in conjunction with research establishments and other partners to address this requirement. We have launched some developments for this technology and will introduce new blower modules for future vehicle RFQs. These reduce noise emissions and can reduce the overall noise by 3-5dBA, which is a significant improvement in refinement.
j-a: How long before we see this innovation on a production model?
TH: We expect that within two years it will start to appear on the market in series production.
j-a: We hear a lot about the difficulty of developing HVAC systems for Electric Vehicles (EV). Can you outline what Delphi is doing for this application?
TH: There is a lot of work going on in the EV field. A lot depends on how people are seated in the vehicle. Occupants are seated while in the vehicle and their back is covered by the seat back. Therefore to be effective the air that is introduced into the cabin has to be channelled in front of the passenger or above. This provides thermal comfort with less air and thus less energy for heating or cooling the air.
As the vehicle gets bigger then a rear HVAC unit is placed in the rear of the car as well. This is typically found in luxury/premium segment vehicles. Delphi offers a range of zonal options but it is costly to have more than one HVAC unit. We are working on a system which works off the central HVAC module in the cockpit and which operates with a split airstream. This technology takes the air and channels it to the driver and front passenger and then another tube takes air to the rear seat space. By adopting this approach we can save cost and weight as well as space. This innovation is going into series production.
Additionally, we have developed the HPAC, which I talked about earlier. Delphi’s HPAC increases the range during the winter conditions by using a heat pump that delivers heat at COP (Coefficient of Performance) above 2. That basically means for 1W of electricity you get 2W of heat.
j-a: What other innovations have you announced recently?
TH: We recently won the Premier Automotive Suppliers Contribution to Excellence (PACE) award in the US for Delphi’s folded tube heat exchanger. We have developed a folded tube with micro-channels in aluminium which we braze rather than weld. This gives us a solution that is based on less weight, better heat transfer performance and gives us more value added since we do not buy in the components. This design is unique to Delphi. Others are doing similar things but they are slightly different. We have patented this technology and approach. HVAC is a mature industry and it is a big step to move away from a welded (extruded) tube to brazing technology. This is why we won the PACE award.
j-a: What other developments have you been working on in the components area?
TH: We offer a well sorted range of externally controlled variable compressors from a 5 cylinder 100cc mini unit that is very successful in emerging markets to 7 cylinder 185cc units. The size of unit depends on the size and value of the car.
There is also a lot of development work going on in the electrical compressor market. While the pure electric vehicle market is not growing as rapidly as everyone expected we are working on ways to provide HVAC in both small and larger electric vehicles. Driving range limitations pose a real challenge at present and it gets worse when there is a need to heat and cool the cabin. Since you do not have very much waste heat in a small electric vehicle we need to have another solution for the HVAC system to work efficiently. The battery needs to generate more energy so that the HVAC unit provides the in-car environment demanded by the customer and the end users. This is a real challenge and we need to see significant developments in battery technology before this problem can be overcome at a cost that is affordable.
j-a: Is the situation the same for hybrid vehicles?
TH: No, it is easier in hybrid vehicles as they have a combustion engine varying in size depending on the car. This brings electric compressors into the game for the HVAC system. The move to high voltage batteries ranging from 48 up to more than 300 V and a high voltage infrastructure means we can drive an electric compressor. It is very important for us as a supplier to offer an electric compressor. Delphi was the first to offer this technology in 1996 when we developed one for GM’s EV1. We have been building on this technology ever since and we are following the trend in this market segment.
j-a: Have you been doing any development work in relation to the evaporator?
TH: Yes – we have developed a wax material with a melting point of 5-8 degrees that utilises phase change material encapsulated in the evaporator of the module for use in HVAC systems in vehicles with stop start technology. With a traditional evaporator, if you want to maintain cooling comfort in the vehicle you cannot turn off the cooling system when the vehicle is stopped at traffic lights or in heavy traffic. Since the compressor is engine-driven, it turns off when the engine is turned off. This results in warm air being delivered to vehicle occupants. Additionally, you can also get a smell from the evaporator if the vehicle is stopped for too long as the surface of the evaporator warms up. We have developed a system that can maintain the comfort for up to one or two minutes, or even more when the car has stopped. This is possible as we freeze the phbase PCM material when the vehicle is moving. It is this and the frozen material that cools the air when the car is temporarily stopped. Using this technology also contributes to savings in fuel consumption. Our system provides cooling for the longest time compared to any similar system on the market.
j-a: When will this technology be available on the market?
TH: We have got joint programmes with customers for this technology which is now in concept development but it will lead to series production. This development is important in that customers can get CO2 credits with this approach. It also only needs a small space within the evaporator which is very beneficial given the space constraints that we operate under. Additionally, in the future we can see the HVAC system combining with the navigation system. For example this will enable the driver to see where the road gradient will change and plan to recharge the system when going down hill. The whole issue of the connected car is becoming more and more important and the vehicle manufacturers will have to connect all the infotainment and navigation systems in future with other systems such as HVAC.
j-a: Are you involved in any other developments for the electric vehicle sector?
TH: We have developed an HVAC system that increases the vehicle range while cutting CO2 emissions. As mentioned earlier, the Unitary Heat Pump Air Conditioner (HPAC) integrates a refrigerant heat pump and coolant distribution system to provide cabin comfort. In addition to drawing heat from the ambient air, this system can also scavenge available waste heat and provide this heat to the cabin. This will reduce battery drain so that range can be extended for electric vehicles. This system is constructed without rubber A/C hoses, reducing emissions of the refrigerant to nearly zero. The system is suited to a number of refrigerants and is therefore very flexible in terms of cost and supply. Because the refrigerant is contained entirely within the engine compartment, the refrigerant choice is also less compromised by flammability constraints. This HPAC technology is expected to enter production for the 2015 model year.
j-a: You have mentioned some very specific product developments. Are there any other more general areas that you are looking at?
TH: Noise is a very complicated area that is not yet fully understood. We have been working in this area to develop new approaches. We need simulation methods to work with here. This is very important. We are looking at a holistic approach and combine experimental work with math based simulation methods such as CFD (computational fluid dynamics) and FEA (finite element analysis) to reduce noise in the cabin and we are working with research institutes and partners in this critical area.