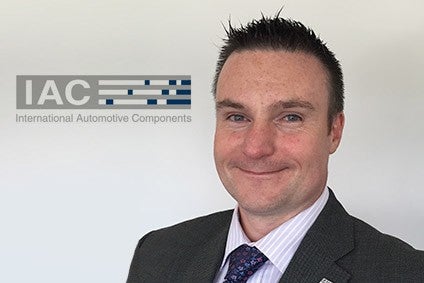
Designers are continually reinventing the interior to appeal to occupants of all shapes, sizes, ages, and cultures. Continuing just-auto/QUBE's series of interviews with tier 1 suppliers, we spoke to Mike Clowry, Vice President Advanced Development & Materials Engineering, Europe, International Automotive Components (IAC) Group about the continually evolving car interior as we move closer to the age of autonomous driving. Headquartered in Luxembourg, IAC Group is a global supplier of automotive components and systems, including instrument panels, console systems, door panels, headliners and overhead systems to automakers around the world.
IAC is highly vertically integrated. What advantages does this give you?
Vertical integration of development and production enables IAC to offer unique solutions to its customers and achieve superior control of quality, delivery, and economic efficiency. We see vertical integration as a main competitive advantage for IAC and will continue further with that strategy especially for those premium products we focus on. For example, for tailored interiors and cut and sew technologies, we are setting up an integrated centre of excellence for European premium customers within our IAC Opole, Poland facility.
We have seen quite a lot of consolidation in the automotive interiors sector over the past few years. Do you see more to come?
The next challenge for our business will be the functional integration of electronics into the interiors.
IAC has been a pioneer of consolidation in the interiors arena with its foundation over ten years ago, so we are now in pole position to offer reliable, premium quality across regions and product categories. We also have the financial and innovation strength to invest and grow in response to our customers' needs. The next challenge for our business will be the functional integration of electronics into the interiors. IAC believes flexible project partnerships and alliances will be more effective than consolidation to sustain the need for innovation speed in our industry.
A decade or so ago, certain car interiors appeared quite poor. To what extent are you seeing carmakers investing more on their car interiors in order to positively impact the customer's perception of vehicle quality?
How well do you really know your competitors?
Access the most comprehensive Company Profiles on the market, powered by GlobalData. Save hours of research. Gain competitive edge.
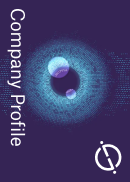
Thank you!
Your download email will arrive shortly
Not ready to buy yet? Download a free sample
We are confident about the unique quality of our Company Profiles. However, we want you to make the most beneficial decision for your business, so we offer a free sample that you can download by submitting the below form
By GlobalDataUpscale interiors are a major trend with all our customers for some years already. In the premium segment which is our main market in Europe, this is even more evident. We have seen a richer material mix like on the Audi Q7 doors. Tailored, cut and sewn instrument panels in both leather and artificial leather on the rise at Volvo and Jaguar Land Rover. Real stitches on challenging geometries are featured now on the instrument panel of the new VW Touareg. Also, headliners are also becoming more sophisticated with a rise in sunroofs as we see at Daimler and the vast use of luxury materials like Italian leather on the Range Rover Sport.
Reducing the weight of every car component is a necessity. Yet is there a danger of making interior parts look inferior?
IAC focuses on utilising low weight materials such as natural fibres and giving the customers the biggest flexibility in terms of appearance.
For structural applications, natural fibres are already a major trend that led IAC among others to develop FiberFrame, a sunroof reinforcement out of natural fibre that cuts 70 per cent of weight on the higher part of the vehicle which has a major impact on the overall centre of gravity and consumption.
Also with the IAC HybridFleece Molding technology, we can press a light natural fibre fleece and combine a laminated A-surface with the features the customer requires for a premium look with back-injected, molded reinforcement ribs and stiffening. Here too, we can cut parts weight by half.
Thinking about Level 3 and 4 automated driving, can you see certain traditional plastic parts disappear in favour of smart parts and surfaces?
Imagine being driven through Liverpool in November while seeing, hearing and smelling "Strawberry fields forever".
IAC has a vision of a 360°, seamless and free configurable interior with back projections, ambient light, sound, heating and even scent. Imagine being driven through Liverpool in November while seeing, hearing and smelling "Strawberry fields forever".
If tomorrow's mobility is about sharing cars, what does that mean for interiors in terms of design, surface materials, construction, flexibility, and ease of configurability?
IAC is working on materials with antiseptic features.
IAC is working among others on materials with antiseptic features and develops technologies and processes to produce premium interiors quickly and cost effective as we believe that new mobility patterns will lead to several interiors refurbishing in the life of a vehicle, similarly to hotel rooms.
One example of these technologies is IAC's Fastkast, our own slush technology development to produce skins that are particularly durable and high quality while cutting on the cycle times and environmental impact of the production process.
Non-traditional automakers appear to be changing the face of mobility. What are they asking for in terms of in-vehicle engagement that's different from traditional automakers?
For both non-traditional and traditional OEMs, the next challenge is functional integration in interiors. It's disseminating information from the cockpit only, wide into the vehicle as we move towards automated driving. Two IAC projects exemplify that development trend: the integration of selfdrive/automated drive change visual alarm in door panels for platoons of commercial vehicles and the integration again in the door panel of an electronic rear mirror.
We understand that for car manufacturers as well as their suppliers, individualisation is a growth market that offers great potential for differentiation. How is IAC responding to that?
IAC needs to have superior management of variants built into reliable and efficient processes. We are already benefitting from industry 4.0 flexible factory layouts with Automated Guidance Vehicles (AGVs) as we have for example in Halewood, UK. We have also deployed smart automation and quality control cobots as in Skara, Sweden.
Finally, we have a connected machine capacity real-time analysis tool implemented worldwide. Multi-materials production line design for cut and sew and wrapping are also fundamental to support individualisation, but they rely strongly on the craftsmanship of our employees. Even amidst its quick growth, IAC has been able to secure in all its new instalments a skilled and stable workforce who has enabled flawless launches and program delivery amidst variants proliferation of the European premium OEMs.