
It is said that commercial vehicles are the most difficult to electrify and likely to be the last to migrate from IC powertrains. Continuing just-auto/QUBE’s series of interviews, we asked David Kelly of Drive System Design why this is the case and what can be done to make battery electric trucks (BETs) more attractive.
Why should commercial vehicles switch to electric powertrains?
Commercial vehicles make up just five per cent of the vehicles on the road but contribute 25 per cent of the CO2 produced by road transport.
Regulators are recognising that commercial vehicles are a significant source of CO2 emissions that must be addressed. In Europe, for example, they make up just five per cent of the vehicles on the road but contribute 25 per cent of the CO2 produced by road transport, the largest single source in this sector. Following the trend set by the US, Japan and China, future EU limits will aim to cut CO2 emissions from trucks by at least 30 per cent by 2035. At the same time, concern over urban air quality in cities around the world is leading to plans for a ban on diesels in some metropolitan areas by 2025. For example, London recently announced a £48m investment to encourage business owners to scrap diesel vehicles for newer, greener alternatives. These pressures mean manufacturers must find practical, commercially viable solutions for the electrification of trucks within challenging timescales.
What makes the design of a practical BET so difficult?
A BET must compete with existing IC-engined vehicles that have highly optimised powertrains with relatively low cost and weight, immense range and rapid refuelling. Market concerns regarding higher initial investment, range limitations and charging infrastructure must be overcome before significant sales volume can be achieved. The battery pack remains the dominant cost of any BET; for example, a 207kWh battery to provide a 200km+ range for a medium duty truck would cost approximately $58,000 and have a battery cell weight of 1.25 tonnes. The cost inevitably increases the purchase price of the vehicle, while the weight reduces the useful payload, making the vehicle less profitable to operate.
So can a BET ever be competitive with an IC alternative?
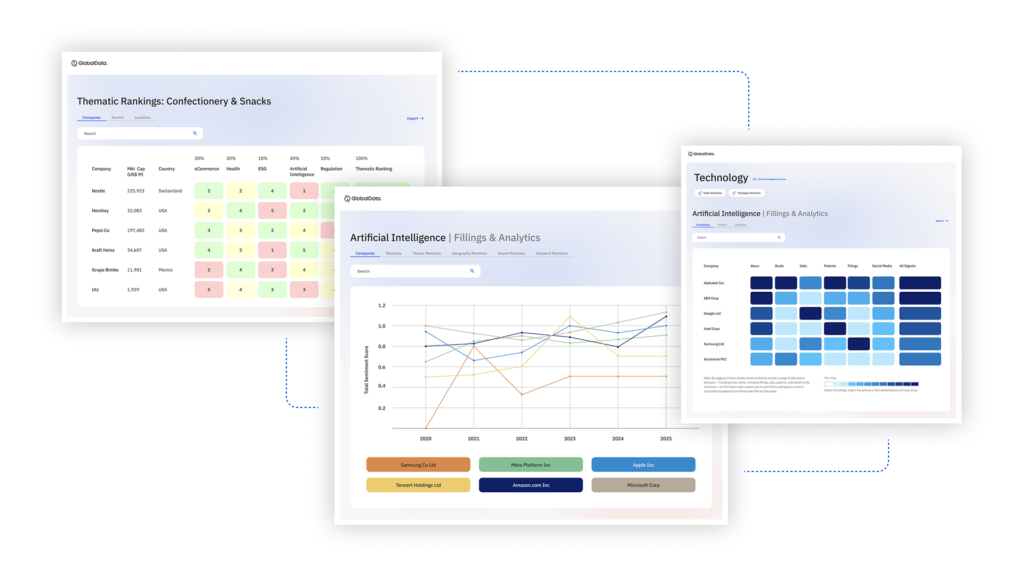
US Tariffs are shifting - will you react or anticipate?
Don’t let policy changes catch you off guard. Stay proactive with real-time data and expert analysis.
By GlobalDataThe lower charging costs and higher efficiency, compared to a diesel powertrain, present an electrified powertrain with the opportunity to offset the initial cost of the battery through lower running costs. Because the industry uses Total Cost of Ownership (TCO) to drive procurement decisions, a BET can make sound commercial sense, provided the initial battery costs are minimised, and the range before recharging is not compromised. This would allow users to meet more demanding emissions restrictions without impairing profitability or operational flexibility. The challenge then shifts to establishing a robust design procedure to create powertrain designs that minimise TCO for a given vehicle application, and this requires a comprehensive system level approach.
How does using a system level approach to design help?
A conventional design approach typically aims to match optimised powertrain components, such as the eMotor or transmission, but this can overlook the synergies and interactions that can occur between these separate sub-systems. A systems approach means optimising the entire powertrain at a whole system level, which often exposes beneficial trade-offs that would never have been revealed otherwise. In such cases, it isn’t uncommon to make significant cost savings by investing in more advanced subsystems and materials, spending more in certain areas to make savings several times over elsewhere in the system.
In one study, by investing in a higher efficiency eMotor the energy consumption was significantly reduced, enabling the use of a smaller, less expensive battery pack. So great were the savings on the battery that, overall, the powertrain cost was reduced by $1800. In this case, the increased eMotor cost was more than covered by the system level benefits.
These studies were undertaken using an in-house developed powertrain simulation process that enables the evaluation of an extensive range of possibilities quickly during the concept design phase. In a recent study using the powertrain optimisation process, over 4000 different powertrain permutations were evaluated to find the optimal configuration.
How does the process work?
Specifications of the powertrain are derived by computing the vehicle resistive power during a variety of operational use cases. Individual powertrain components are then analysed in simulation to achieve these vehicle level specifications.
Range can be evaluated by calculating the energy consumption during a drive cycle in which the vehicle is subjected to a range of accelerations and decelerations. Based on the battery capacity and regeneration opportunity, the range of the vehicle can be obtained.
The battery voltage and required eMotor current drives the inverter specification. Gear ratio selection allows the manipulation of the operating efficiencies of the eMotor, inverter and transmission to reduce energy consumption and minimise the required battery capacity.
Are there pitfalls in the systems approach?
The key to successful application is a thorough understanding of the operational use cases in order to specify power and torque appropriately.
A systems approach involves extensive modelling and, like any simulation, is only useful if the right conditions are applied and the input data is reliable. In practical terms this means distinguishing between what is important and what isn’t. The key to successful application is a thorough understanding of the operational use cases in order to specify power and torque appropriately. An optimised powertrain can then be identified, that maximises energy efficiency at minimal cost while ensuring all functional requirements are met. To give an example, when modelling a medium duty BET with high vehicle mass, any likely gradient changes during the drive cycle must be included, otherwise peak power and energy usage requirements will be significantly underestimated.