
Denso‘s thermal systems division represents its second largest segment, accounting for approximately one-third of the company’s annual turnover. The division produces climate control products and engine-cooling systems. Continuing just-auto’s series of interviews with tier one suppliers, Matthew Beecham spoke to Tibor Gyoeroeg, Senior Manager at Denso Automotive Deutschland GmbH and Matteo Biglia, Director at Denso Thermal Systems Italy about the supplier’s cooling system technologies.
We understand that in João de Deus & Filhos SA in Portugal, Denso has more than 102 years of thermal experience, specializing in intercoolers for car and truck manufacturers. In what ways has the scope of thermal management changed over the past decade and how has the trend for increasing use of turbochargers and superchargers influenced intercooling?
The company is indeed 102 years old, and our experience with intercoolers started in the mid-1990s. In the last 20-plus years we have seen engine downsizing and the effect of emissions regulations affecting the intercooling function.
Engine downsizing, especially for gasoline, has increased the need for intercoolers as larger displacement engines were being replaced by smaller, turbocharged units.
Emissions regulations, especially for diesel, have introduced the need for LPL-EGR, a system which injects some exhaust gas back to the compressor inlet and thus recirculates it through the intercooler where its temperature can drop below the dew point, potentially creating very acidic condensation. This condensation can corrode not only the EGR cooler but also intake related parts such as the intercooler.
Both instances have accelerated the advent of water-cooled charge air cooling.
How well do you really know your competitors?
Access the most comprehensive Company Profiles on the market, powered by GlobalData. Save hours of research. Gain competitive edge.
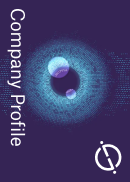
Thank you!
Your download email will arrive shortly
Not ready to buy yet? Download a free sample
We are confident about the unique quality of our Company Profiles. However, we want you to make the most beneficial decision for your business, so we offer a free sample that you can download by submitting the below form
By GlobalDataIn the case of downsizing, smaller displacement gasoline engines with relatively low torque at low engine speeds can benefit from improved transient response (reduced “turbo lag”) due to the reduce air volume in the intake system which is a direct consequence of a water-cooled charge air cooler adoption.
In the case of LPL-EGR, water-cooled charge air coolers offer the possibility to control the cooling effect of charge air. By switching the electric water pump, charge air temperature at WCAC outlet can be controlled to avoid dropping below the dew point thus greatly reducing the amount of condensed water forming in the system when EGR gas is re-circulated.
What role did Denso play with the thermal energy system for the battery-electric vehicles?
In electric vehicles, no waste heat from a combustion engine is available for heating of the passenger compartment. The electric heater must be operated using the electric energy from the traction battery. This reduces the driving range of the electric vehicle drastically because less electric energy is available for vehicle drive from the battery.
Denso developed a unique heat pump system which is simple, robust and efficient.
The Denso heat pump system reduces the use of electrical energy significantly, since it can draw a great part of the required energy from the environment thus raising the driving range of the electric vehicle.
H/P system – Cooling mode
The compressor installed in the heat pump actually requires electric energy but significantly less than the heating capacity supplied by the heat pump. Typically, the heat pump is producing 2-3 times more heat than it is consuming electric energy – a major advantage for electric vehicles. A complex cycle ensures a comfortable temperature in the passenger compartment. This system consists of different components, such as condenser, evaporator, outside heat exchanger, compressor, accumulator and valves, which are connected with refrigeration pipes.
Inside the system a refrigerant flows, which adopts various states in gaseous and liquid form on its way through the system. As a gas, the refrigerant in some parts of the system is compressed to 20bar and 150°C, in other parts it is expanded down to 1 bar and -25°C. Depending on whether the system is to cool or to heat, valves ensure the correct way of the refrigerant through the closed system.
H/P system – Heating mode
One system with two functions. Two valves and a damper inside the air conditioning unit allow main components to be used both for heating and cooling. During cooling, a damper separates the inner condenser from the air flow into the passenger compartment. The condenser is only used for heating. An on/off valve allows the bypassing of the expansion valve which is used for heating only. The outside heat exchanger in the front area of the vehicle works as an evaporator in heating and as a condenser in cooling mode. For cooling mode, an additional expansion valve is needed to provide cold and liquid refrigerant to the evaporator. In heating mode, the evaporator in the air conditioning unit is not used. The refrigerant reaches the compressor directly through the 3-way valve and the accumulator. Denso´s Heat Pump is in series production since several years.
We understand that Denso developed and supplies the internal heat exchanger technologies for various German car manufacturers. Could you explain the unique features of those technologies?
Denso developed a “double-pipe internal heat exchanger” for efficiency improvement in automotive air conditioning systems. This double-pipe internal heat exchanger can improve cooling performance of the evaporator without increasing the compressor power consumption.
How it works? The hot, high pressure refrigerant, which leaves the condenser, is cooled down by the cold, low pressure refrigerant, which leaves the evaporator. This internal heat exchange happens in the double-pipe heat exchanger which integrates two pipes into one pipe with inner and outer pipes. Our main unique feature is the spiral grooves on the inner pipe wall, which enables enhanced heat exchange between the hot and cold refrigerant. The effect: in the evaporator the heat exchange is more intense, increasing the cooling performance of the entire refrigeration cycle.
Structure of double-pipe internal heat exchanger
Denso´s unique double-pipe internal heat exchanger is capable to increase the cooling performance by a remarkable 5 to 12% at the same power consumption level of the compressor and in the same space as conventional air conditioning systems.
The Denso internal heat exchanger is in mass production since January 2006.
In terms of commercial vehicles, what are the challenges / opportunities as far as engine cooling is concerned?
Commercial vehicles operate many diversified missions, from urban door-to door delivery, to highway driving courier, to high load carrying operations. This implies diversified responses to achieve optimized performance and cost balance within the boundaries of a sound modularization strategy that allows fitting each vehicle to its most probable mission. This applies for differentiated powertrain options (diesel ICE, CNG ICE, HEV and BEV even) but also within the same engine option. For instance, adoption of engine-driven fan for high load operations could be substituted with brushless electric motors in case of a fleet of urban delivery vans.
The challenges of emissions restrictions, combined with the robustness needed for high mileage operations, for the, mostly, diesel powertrains on light commercial vehicles will require similar answers to passenger vehicles, with WCAC and EGR combinations.
We believe that cooling will be more and more important with electrification, as there will be multiple cooling circuits to manage independently. How do you see the cooling the alternative powertrain evolving?
A clear distinction is needed between HEV or even PHEV and BEV. The former (HEV, PHEV) must keep separation between the high temperature loop for cooling the internal-combustion engine (ICE) and the low temperature loop which is needed for the electric/electronic components of the hybrid powertrain. The latter (BEV), not having the cooling need of an ICE to deal with, can open the doors to an integrated thermal management system which allows for a combination of cabin and powertrain comfort level to be achieved with the least energy dispersion to the ambient.
In terms of emerging markets, do they differ from other markets when it comes to the dimensioning and design of engine cooling technologies?
Sizing is influenced by climate, and many emerging markets seem to show presence of extremes (hot in India and Brazil, cold in Russia). Road conditions can determine the need for a more robust construction of mechanical fixations. Difficult availability of de-mineralized water for mixing of coolant can provide challenges to internal corrosion resistance of heat exchangers. Different regulations for quality of fuels, in the case of EGR cooling, can also create challenges in the corrosion resistance of parts in contact with exhaust fumes condensates.