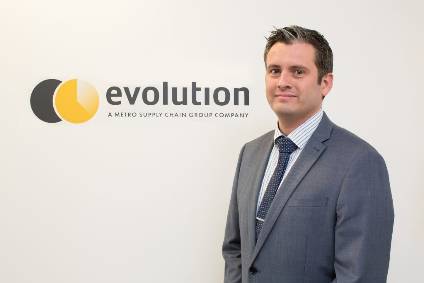
May we mention the B-word? UK automotive manufacturing is currently amongst the world's most efficient, relying on a tightly coordinated global supply chain to feed its production lines, with minimum capital employed and carefully-managed risk. Yet Brexit continues to concern the industry, including the ability of automakers and suppliers to maintain their just-in-time deliveries. We spoke to Graham Little, deputy managing director of logistics specialist Evolution Time Critical to understand what might happen, how manufacturers should prepare and why they should not plan to rely on trusted emergency techniques that have so far served them well within a joined-up Europe.
'Brexit' is shorthand for Britain exiting the European Union (EU). On 13 November 2018 the EU and UK reached an agreement on Brexit. It was endorsed by the UK government and the 27 remaining EU member states. However, the UK parliament has rejected this agreement in three votes. As a result, the date of Brexit has been postponed from 29 March until 12 April 2019. It is clear that the possibility of a 'no deal' Brexit has now increased. This interview with Evolution Time Critical took place on 3 April 2019.
Reports are circulating that air charter brokers are receiving more and more enquiries from freight forwarders about securing air cargo capacity to offset the potential repercussions of a 'no deal' Brexit on the supply chains of their shipper customers. Is this something that Evolution Time Critical can testify to of late?
Our business has grown and succeeded on the basis of reasoned analysis and evaluation, constantly updated and revised in the face of evolving situations. There have been particular challenges in securing accurate information around Brexit, but we've been very careful to avoid speculation and bandwagoning, focusing instead on verified government information. We've also been consulting closely with our manufacturing contacts and industry trade bodies, and while they all recognise air cargo to be a flexible, speedy and established solution in emergency logistics situations, most consider the current balance of factors doesn't suggest the mass adoption of air freight as an economically proportionate or necessary contingency. Instead, careful and proactive supply chain analysis and mitigation planning suggests the vast majority of production material will continue via road, with air facilitating smaller volumes of time-critical parts as it has done previously.
Have any customers come to you to pre-book charters over a prolonged period in anticipation of a hard Brexit, fearing gridlocks at Channel ports for trucked freight?
Some manufacturers are holding up to 14 days' supply of high-volume goods.
The recurring characteristic in Brexit planning by the vehicle manufacturers we work with – be they large volume producers or those at the more niche, luxury end of the market – is that they have been analysing their supply chain requirements, vulnerabilities, options and possible scenarios and remedial action from the outset. The consensus has been to continue with road freight, while mitigating against disruption by building contingency stocks. Some manufacturers are holding up to 14 days' supply of high-volume goods, a substantial increase on levels often associated with 'just in time' manufacturing.
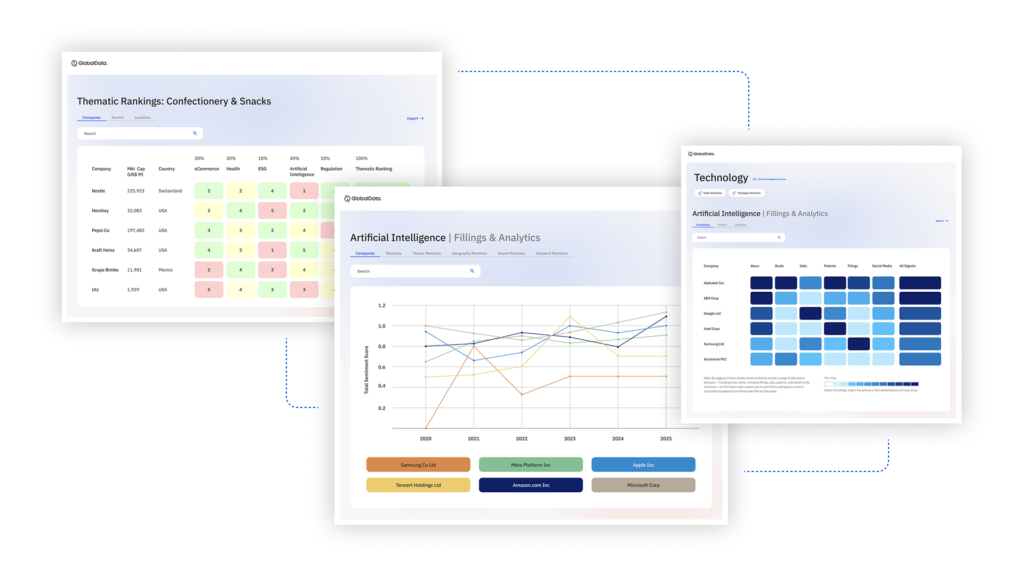
US Tariffs are shifting - will you react or anticipate?
Don’t let policy changes catch you off guard. Stay proactive with real-time data and expert analysis.
By GlobalDataWhile air cargo will always have its place in emergency logistics, whether it be a dedicated charter or onboard courier, we expect the vast bulk of components to still travel by road in the foreseeable future, without the need for a mass adoption of emergency logistics. Automotive is one of the world's most efficient manufacturing industries, with considerable logistics expertise, so the emphasis is on clever planning rather than expensive alternatives. Evolution have been an integral partner in this planning and analysis process for many manufacturers, with our depth of experience in optimising road transport solutions combined with a broad geographic network meaning we have the experience to anticipate and the flexibility to meet challenges as they arise. This is the greatest advantage of multi-modal offerings; road freight can be diverted to airports if delays are anticipated ahead, and cargos broken into smaller packages so only the material needed incurs the cost of airfreight, with the rest continuing by road through the delay. This flexibility ensures we can meet client's immediate needs without incurring unnecessary costs.
How well do you think cargo charter brokers will be able to cope if there was a sudden and sharp increase in demand for aircraft given that there is not too much slack in the market currently?
At times when there is finite capacity in a market it becomes even more important to work as smartly as possible, and that starts with analysing the most immediate requirements. Having worked with many of our OEM clients for nearly twenty years, Evolution has developed a unique understanding of their businesses and developed excellent working relationships where we are viewed not just as logistics provider, but as a trusted advisor. Accordingly, we're well positioned to advise when, for example, larger shipments can be broken down into smaller packages for transport by smaller aircraft or onboard courier. Similarly, our long relationship with both mainstream and more niche aviation providers means Evolution is well placed to quickly locate any surplus capacity.
It's more about rigorous analysis and planning than throwing money at air cargo that may not even deliver the required solution.
However, air cargo capacity is only half the equation. Perhaps more important is the form post-Brexit customs regulations will take as many of the smaller airports favoured for emergency logistics may not have implemented the required customs systems and infrastructure, meaning that flights must leave Europe via larger but more congested hubs. Evolution are used to managing complex customs processes, and it comes down to familiarity and preparedness. Again, it's more about rigorous analysis and planning than throwing money at air cargo that may not even deliver the required solution.
WLTP regulations and shifts in consumer buying patterns away from diesel towards gasoline have been cited by some major vehicle manufacturers as having dampened their 2018 financials. Is there a case that these represent a more immediate priority to vehicle manufacturers than a potential 'no deal' Brexit?
There were two issues at play here for OEMs. The first was the new WLTP standards and sharper than expected shift in consumer demand away from diesel and towards gasoline and electrified powertrains. This created a perfect storm in the automotive supply chain that underlined the industry's dependence on premium freight to enable lean manufacturing and kept us busy throughout much of the year. This resulted in a ripple throughout Tier suppliers who suddenly faced rapidly changing demand and lead time expectations, having either to ramp-up or rebalance production accordingly. The second issue compounding the situation were delays securing updated Certificates of Conformity (CoCs) for the revised models that would enable them to be registered to end users. The exposure of individual manufacturers to these issues has varied, as will their exposure to a potential 'no deal' Brexit, but while the severity and persistence of the pivot away from diesel was largely unexpected, we've been assisting OEMs in conducting careful and proactive supply chain analysis and mitigation planning around 'no deal' scenarios for some time, and their level of preparedness is accordingly higher.
Beyond the delivery of components, could supply chain disruption cause implications for other aspects of production?
A lot has been said about the impact of political uncertainty on investment and supply-side influences on production, but equally there's scope for some significant demand-led shifts in production. For example, the possibility of higher unit costs resulting from currency movements, changes to VAT and tariffs or politically motivated disruption such as strikes, could see a market pivot towards lower-spec vehicles, manifested either within a manufacturer's existing model mix, or at a market level by sales in one segment increasing at the expense of another. These changes in demand and their resulting procurement requirements could be unpredictable and difficult to forecast, meaning plants and their Tier suppliers may be asked to ramp, curtail or rebalance production and delivery schedules at short notice. Lower Tier suppliers would be least able to withstand and mitigate possible VAT and tariff changes, increasing the chance of failure and further escalating pressure on the remaining suppliers. An additional complication is the trend towards manufacturers reducing the number of option combinations offered on their vehicles by bundling equipment into packages, meaning more vehicles stand to be impacted by disruption affecting a single option than would previously have been the case.
2018 saw the pace of change and innovation in the automotive industry as unrelenting as ever. Looking back, did anything stand out as particularly unexpected?
During a review of 2018 booking trends, we saw manufacturers experiencing more issues around Start of Production (SoP). Exploring further, we found unprecedented demand for new models – electric, hybrid, SUV – is driving vehicle manufacturers to accelerate deployment of new virtual development techniques that create competitive advantage by bringing new models to market faster and with fewer costly prototypes. One of the few downsides is late-stage design changes that can only be revealed by whole-vehicle testing are often not discovered until tooling is already committed. This creates manufacturing and logistics challenges by increasing dependence on the ability to implement costly last-minute tooling changes and then accelerate component deliveries to meet fixed SOP dates. Accordingly, we are seeing a growing number of requests from vehicle manufacturers and Tier 1 suppliers to recover days, or even weeks, by dramatically compressing the manufacturing logistics component of their SoP schedules.
The difficulty that may be faced by UK plants is not having a full picture of what is and isn't logistically feasible in the coming months.
Our solution was to use emergency logistics to compress timescales for the delivery of tooling, which is often purchased from China, and then to use similar techniques to accelerate the delivery of components from suppliers to the vehicle production line. However, in order to de-risk this unexpected consequence of virtual development and allow even greater benefit to be released from these new techniques, planners must integrate a new approach to SoP logistics that is both global and ultra-responsive; a strategic time compression tool, not an emergency response to a last-minute change. The difficulty that may be faced by UK plants is not having a full picture of what is and isn't logistically feasible in the coming months, potentially causing planners to push back SoP dates and negating the competitive advantage derived from virtual prototyping and compressed model development schedules, at least for a period until greater certainty and operating norms can be established.
What innovations do you see as holding the most potential for the emergency logistics industry in the near future?
I'm particularly excited by the opportunities afforded by data, analytics and machine learning. Evolution has been investing heavily to enhance our capabilities in these areas, with a particular focus on smart service selection to provide clients with the right option the moment they require it, dynamic troubleshooting to minimise mid-route disruption, and real-time tracking with the option to seamlessly integrate with client systems. The development of our European and North American control centres, in particular, has greatly expanded the volume of historic and live data that can be fed into these global models, while simultaneously ensuring clients don't lose the individual, responsive and personable service they expect from Evolution. Such a reliable, robust and cost-effective solution can be used as a primary logistics service for high-dependency cargo, further reducing the risk of supply chain failure at an unusually turbulent time for the automotive industry globally.