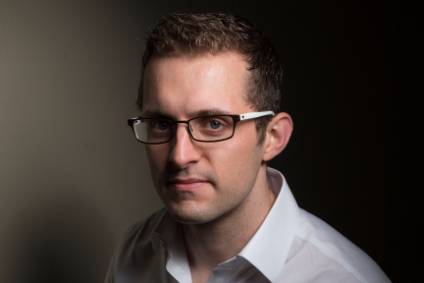
As pressures to improve air quality intensify, it is becoming harder for automakers to find new, affordable ways to improve fuel economy through established measures such as engine downsizing. Not yet high on the industry agenda but of growing importance, sustainability in fast-growing new markets must also be addressed. Continuing QUBE/just-auto’s series of interviews, we spoke to Dr Oliver Taylor about a new approach to engine lubrication that could address both issues. Dr Taylor is chief engineer with Nexcel, an innovation business within BP’s Castrol subsidiary.
Why do you think the time is right for a new approach to managing engine lubrication?
There are three reasons. First, in parallel with a continuing need to dramatically reduce emissions, there is a growing understanding that measured tailpipe emissions must have a much closer correlation with real world emissions. With the length of real-world journeys continuing to fall, warm-up is becoming an increasingly important operating condition for almost every engine.
Second, the fast growth of car ownership in developing markets means that there is a rapidly growing volume of used oil to dispose of, and where there is no infrastructure to do that responsibly and easily, it is often returned to the environment in a way that can be damaging, especially to water supplies. The Nexcel system reduces warm-up times, allowing engines to operate more efficiently for the majority of the miles travelled and, by containing the oil within a cell that has value when returned, ensures that used oil is captured.
The third benefit is that returning used oil in the cell, rather than mixing it with used oils of other grades, allows a very high proportion to be reprocessed back to its original performance.
How do the numbers for real-world journey times compare with the World harmonised Light vehicle Test Protocol (WLTP) cycle to which vehicles must now be homologated?
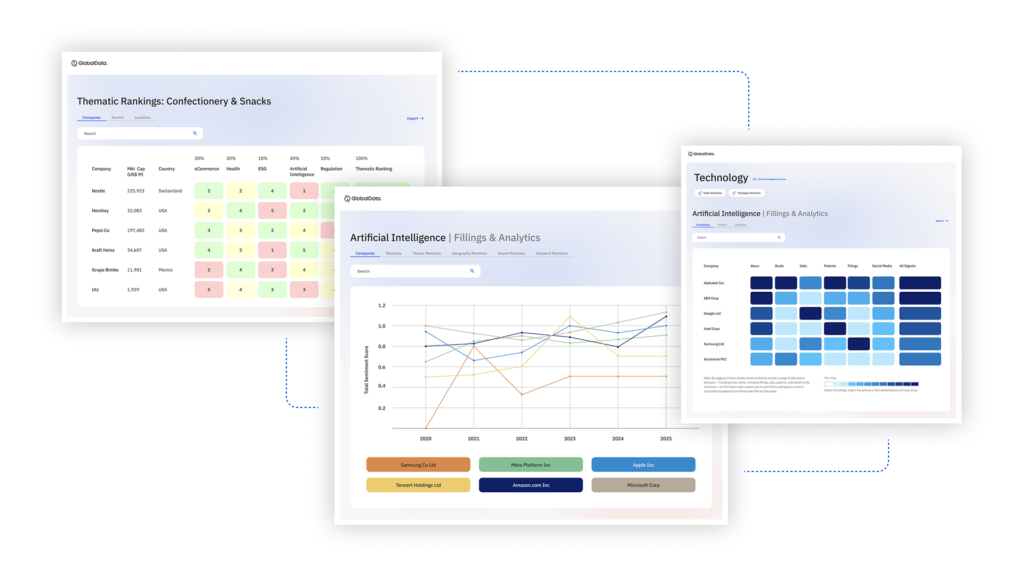
US Tariffs are shifting - will you react or anticipate?
Don’t let policy changes catch you off guard. Stay proactive with real-time data and expert analysis.
By GlobalDataSaving 3.0 litres of oil is equivalent to shedding 6.4 kg from an aluminium block, so reducing lubricant volume helps an engine to warm up quicker.
Though the WLTP cycle represents real world driving more closely than the old NEDC procedure, up to 20 percent of the fuel energy is still ‘lost’ into warming up the metal parts, coolant and oil of a typical current-generation engine. The contribution to warm-up time due to heating the oil within the engine is often under-estimated because the specific thermal capacity of oil is substantially higher than that of the metals used for the high-mass engine components. Saving 3.0 litres (approximately 2.6 kg) of oil is equivalent to shedding 6.4 kg from an aluminium block, or nearly 12 kg from an iron block, so reducing lubricant volume helps an engine to warm up significantly more quickly.
Real world statistics underline the importance of achieving a faster warm-up. The UK’s recently-published National Travel Survey showed that the average car journey time has fallen to just 22 minutes and the average journey length to only 7.5 miles. The same survey also showed that most mileage occurs in urban areas. Although ten minutes longer than the NEDC that preceded it, the WLTP cycle is still only 30 minutes.
How does the system work?
Nexcel is a self-contained, sealed cell containing the correct quantity and grade of oil and appropriate specification of filter. Designed for flexible installation anywhere in the engine bay via a docking station, it is managed by a dedicated electronic control unit that communicates with the vehicle via the standard databus. An integral electric pump controls the flow of oil between the engine sump (oil pan) and the remote cell. Reduced warm-up time is achieved by managing the volume of oil in the sump at all times, which means the volume can be minimised during start and warm-up.
With a traditional engine lubrication architecture, the oil volume has to be sufficient to cater for a number of extremes such as safe operation when inclined at up to 30 degrees; sufficient settling time to allow de-aeration when the engine is working hard; and sufficient volume to remain within specification throughout today’s increasingly long drain intervals.
Nexcel is a self-contained, sealed cell containing the correct quantity and grade of oil and appropriate specification of filter.
Nexcel retains sufficient volume of oil within the remote cell to satisfy all these conditions when required, leaving just the optimum amount within the sump. Such precise control is comparable to modern intelligent cooling systems and enables lubrication to become the final major vehicle system to benefit from electronic control.
Does this open doors for further engine downsizing and other optimisation?
It removes several barriers. With effective lifetime control of the lubricant specification, engine designers can make further advances in areas like bearing loads and peak temperatures while retaining robust durability margins. Optimisation no longer has to be compromised to allow for the potential use of inferior lubricants during some future service.
There is also potential for increasingly bespoke oils, optimised for the engine design as any other critical component would be. We may also be able to reduce the additive content of the oil circulating in the engine, which would further reduce viscosity and the related parasitic losses.
Powertrain engineers often ask about the packaging implications, because a space roughly equivalent to the 12v battery must be found close to the engine. One solution is to move the battery to the rear of the car. Packaging is, however, a complex equation as the Nexcel system also releases space where it is most needed for aftertreatment systems, close to the engine, because it removes the need for both a separate filter and for the access space necessary to reach, unscrew and withdraw the filter. We have also had conversations with vehicle manufacturers about the system’s potential to reduce engine height, which they see as positive for aerodynamics, styling and especially for pedestrian impact which requires space between the bonnet and the highest hard points.
How much of the oil can be re-used?
Because the Nexcel system keeps individual oil types protected within their cells up to the point of re-refining, it eliminates cross-contamination, which is the usual obstacle to cost-effective recycling. Independent research suggests we can produce up to 34 gallons of high-quality lubricant from 42 gallons of used oil; this compares to just half a gallon from today’s lubricants.
The hidden truth behind these numbers is the volume of used oil that is currently disposed of indiscriminately, damaging the environment in the process. This problem affects both established markets and developing regions; for example, a recent article in The Economist claimed that Americans pour 200m US gallons (750m litres) of oil into ‘trash cans’, onto land or down the drain every year.
Because the Nexcel system uses a plug-in replacement cell, there is both an incentive and an opportunity for the vehicle operator, or service shop, to return the old one and claim the return discount on a replacement. Widespread use of such a system has the potential to greatly reduce inappropriate disposal.
Garages make good money from oil changes and from using oil changes to attract customers into their service operations. How can you convince them that Nexcel is a good thing?
As the global vehicle parc increases, pressure is growing on garages to reduce turn-around times and offer greater convenience to customers.
Nexcel can reduce the time taken for an oil and filter change from around 20 minutes to just 90 seconds.
Nexcel can reduce the time taken for an oil and filter change from around 20 minutes to just 90 seconds, and it can be carried out equally effectively on a hot or cold engine. It doesn’t tie up an expensive vehicle lift, which can then be used for more lucrative jobs, and it eliminates the need to reach hot and inaccessible parts; an oil and filter change can be accomplished entirely from above.
There is also a significant convenience benefit. Garages currently need dedicated systems for collecting used oil and it can be messy. Nexcel cells simply lift out and can be stacked for return, with no mess, no risk of spills and no specialist equipment.
What do you think will be the driving force behind the adoption of Nexcel?
The introduction of Nexcel by a vehicle manufacturer is likely to be a high-level decision because the benefits are shared by so many aspects of the business. The powertrain and vehicle engineering offices support the cost-effective emissions reductions; the customer service function appreciates the increased convenience for both dealer networks and customers; the corporate and social responsibility function recognises the environmental credentials. We are also finding significant interest coming from fleet sales functions, who recognise how attractive the sustainability benefits are to metropolitan authorities placing fleet orders, or influencing the vehicle choices of their contractors.
It is this combination of factors that makes the Nexcel active oil management system a very attractive, low-cost route to emissions, service and sustainability benefits. Compared with many other options for increasing engine efficiency, it’s more affordable, less disruptive and brings so many additional benefits. Once the technology becomes established, people will wonder why they did it any other way.