The pivotal role of logistics in the motor industry’s current development has been reinforced during the past year in line with the knowledge that those who are able to implement the most effective and efficient procedures in supply chain management will secure a substantial competitive advantage. In the interests of saving costs, operators in every facet of the automotive sector are looking to streamline functions and thereby reduce the duration between the receipt of an order and delivery to the final customer.
Component and system producers are under growing pressure to sharpen their supply chain practices as vehicle manufacturers seek to shift the burden of stockholding on to their suppliers and simultaneously demand progressively lower prices. In turn, vehicle manufacturers are looking to organise their assembly lines on a build-to-order basis and fulfil a customer’s order in a matter of days rather than weeks. As an example, Nissan and Renault aim to achieve an order-to-delivery time of 14 days within the next three years for their customers in Europe and Japan. Meanwhile, considerable headway in the direction of reducing stocks and speeding delivery has been made in the aftermarket.
Over the years the realisation within the motor industry that the logistics function has the potential to secure substantial cost reductions, together with an improvement in customer satisfaction, has resulted in a growing role for specialist logistics companies. This has linked neatly with the broad strategy towards outsourcing whereby vehicle producers have delegated an expanding list of operations to outside contractors.
The use of logistics companies has been important for a number of reasons, not least the ability to tap into their specialist expertise and take full advantage of fast moving developments in information technology (IT) which have transformed the warehousing and transportation functions. Also, substantial economies along with a high level of flexibility, notably in aftermarket distribution, have been possible through the increasing use of the shared user concept whereby trucks are not dedicated to a single customer.
“the deployment of web-based technology to deliver market leading logistics solutions to our customers remains a core element of our strategy”. Jonathan Fry,Chairman, Christian Salvesen |
As with so many aspects of the motor industry, the internet is assuming a rising importance. Indeed, the enormous potential for harnessing the net as an aid for the global motor industry’s supply chain will be one of the key themes to be discussed at Lyon, France in November at Odette 2000 – the annual conference of the Odette International organisation which links the logistics operations of many of Europe’s vehicle manufacturers and component suppliers.
How well do you really know your competitors?
Access the most comprehensive Company Profiles on the market, powered by GlobalData. Save hours of research. Gain competitive edge.
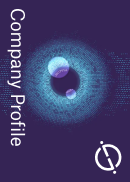
Thank you!
Your download email will arrive shortly
Not ready to buy yet? Download a free sample
We are confident about the unique quality of our Company Profiles. However, we want you to make the most beneficial decision for your business, so we offer a free sample that you can download by submitting the below form
By GlobalDataAt Christian Salvesen’s AGM in mid-July company chairman Jonathan Fry reported that “the deployment of web-based technology to deliver market leading logistics solutions to our customers remains a core element of our strategy”. In June Salvesen introduced officially two web-based systems – Stocknet and SHARPnet – which allow customers to enter orders and manage inventory and consignments from their desktop PCs. Already these systems have been adopted by several major companies including Dupont and Unipart.
As a further development, Salvesen is planning to use satellite positioning technology and on-board computers in its vehicles to provide information on deliveries and real time location of consignments with pinpoint accuracy.
In mid-September Logtek announced a new development in web-based logistics control systems which is claimed to be particularly suitable for motor industry applications. Described as “a new system to keep automotive industry logistics on track” and known as TRACE, the technology provides a real time method of keeping track in a cost effective manner of returnable transit equipment (RTE) throughout the supply chain. Logtek believes that this is likely to be increasingly vital as RTE replaces one-trip transit packaging. According to Ron Heaton, Logtek’s managing director, TRACE brings a new dimension to outsourced logistics management services because it “not only promotes supply chain efficiency but also eliminates costly over-population of RTE by significantly reducing losses. Estimates are that, by optimising use of such equipment, TRACE reduces a client company’s requirements for trays, stillages and other multi-trip containers by as much as 33%”.
The logistics sector as a whole has benefited during the past year from the generally high level of activity in the motor industry. Notwithstanding the widespread impression created by the popular media that the sector is flat on its back, so far this year car output and demand has held steady while commercial vehicle production and sales show an increase of around 5%. In addition, imports and exports remain at a high level.
Meanwhile supply chains are becoming increasingly complex due in large measure to two key factors: sourcing arrangements which are geographically more widespread; and product developments which result in vehicles being assembled with higher levels of technical equipment. With regard to the former, the high value of sterling against the euro suggests that a growing proportion of UK assemblers’ component requirements will be sourced from the continent.
A pronounced trend in recent years has seen logistics companies take responsibility for a widening range of functions rather than simply provide warehousing and transport. For example, car transporting groups routinely provide a range of services including pre-delivery inspection (PDI), vehicle preparation, storage, fitment of options and accessories, paint and body rectification and used vehicle refurbishment.
“The use of logistics companies has been important for a number of reasons, not least the ability to tap into their specialist expertise and take full advantage of fast moving developments in information technology” |
There have been numerous developments affecting individual companies. After a year of reorganisation, Seaking Automotive – the UK vehicle logistics and technical services business of Inchcape Group – announced in April that it had secured a major contract from Proton for handling around 6,000 imported vehicles a year at a dedicated facility in Portbury. The deal involves taking over the existing Proton Cars Import Centre and means that the company now has the capacity at Royal Portbury Dock to manage the PDI of more than 50,000 vehicles annually along with a paint shop throughput of 130 vehicles daily. According to Jeremy Shepherd, managing director of Seaking Automotive, the facility is “an important step in our strategic development and will enable us to continue to grow our client base, satisfy them with an integrated product and services portfolio and penetrate new market sectors”.
In August, Seaking also announced that it had won a contract with SEAT UK to provide a fully managed service for rental vehicles including initial liaison with rental companies, logistics management, PDI inspection and recall notification at the end of the term.
Earlier in the year, Axial – the automotive logistics division of Tibbett & Britten Group – won a contract from Motor Vehicle Industries (MVI), the importer of Tata, for the delivery of vehicles to Tata’s 60-strong UK dealer network. Axial collects the units from Portbury and transports them to MVI’s storage facility in north east England for onward distribution using dedicated Axial transporters in Tata livery. Geoff Warkup, MVI’s operations director, reports that Axial won the contract due to “their breadth of experience and willingness to grow with our business. They offered a faster 4-day turnaround from notification of arrival at the port to dealer delivery – a 33% improvement
on our previous arrangement”.
Axial is one of the largest automotive logistics companies in Europe and operates from 50 sites which account for 500 acres of dedicated vehicle storage. The company has more than 1,200 car transporters and 2,300 employees. In June the company reported that Daewoo had renewed its contract for three years for transportation services in the UK and Ireland. This involves deliveries of newly imported cars to retail outlets, collection and delivery of new and used vehicles between showrooms, and direct deliveries to fleets.
More recently, at the beginning of September, Walon UK announced that Fiat Auto had awarded a five-year extension to its delivery contract along with a major expansion of the services provided. As a result Walon will now supply a complete logistics service for the Fiat and Alfa Romeo marques until at least the end of 2004. During this period it is envisaged that Walon will receive, store, prepare and transport more than 100,000 cars a year for Fiat Auto. The enlarged contract stems from a review of operations by Fiat in Turin which has led to the “door-to-door” project whereby the number of suppliers on the route to market has been rationalised and concentrated on the most cost effective and reliable services. Walon’s managing director Tim Barber commented that the company was able “to demonstrate a clear benefit as part of the door-to-door review”.
In August Christian Salvesen released details of its continuing links as a provider of logistical services to General Motors. The company has won a four-year contract, valued at £60m, which includes the just-in-time collection of production parts from 360 UK suppliers for delivery to GM’s factories in Charlton (Bedfordshire), Ellesmere Port and Luton. Also, parts will be consolidated for delivery to GM’s nine factories in Belgium, Germany, Poland, Portugal and Spain. It is estimated that Salvesen will handle 80,000 UK consignments annually, representing 500,000 tonnes of parts, and the deal includes the return of empty containers to suppliers.
In the aftermarket, Salvesen will make 87,000 deliveries a year from GM’s distribution centre at Charlton by means of its through-the-night network which involves drivers making unattended deliveries to Vauxhall’s dealer network.
In the commercial vehicle sector, Hays announced a five-year contract from Iveco in June to handle the Italian company’s entire European parts and accessories distribution. Hays Logistics UK and the group’s counterparts in continental Europe will join forces to manage and co-ordinate distribution centres in five countries – France, Germany, Italy, Spain and the UK. In the UK the process started in January when Hays took over responsibility for Iveco’s distribution centre in Winsford which receives parts from across Europe and provides the UK dealer network with a standard three-day delivery service and 24-hour breakdown parts service. David Edwards, director of Hays UK automotive and industrial division, stated that the contract was won “on the strength of Hays’ European coverage”.
“For the future, it is clear that the internet will assume a growing role in the continuing attempt to strip time and cost from the entire vehicle manufacturing process, from ordering the individual parts for assembly to delivery of the finished product to the final customer.” |
This contract demonstrates two important points in the current logistics scene: the willingness of vehicle manufacturers to delegate their in-house logistics operations to specialist outside contractors; and the increasing need for these specialists to operate on a European-wide dimension. More and more it seems probable that it will become necessary to demonstrate a global competence.
The importance of scale and global reach was a major factor in the “merger of equals” between Exel and Ocean Group in February. The new grouping intends to become a world leader in supply chain management solutions and claims to be the world’s second largest supply chain company. Automotive logistics is an important business segment with major worldwide clients including DaimlerChrysler, Ford, Nissan, SEAT, Toyota and Volkswagen. In the UK, Exel now handles sea containers of packaged components from Nissan in Japan for delivery to Nissan’s assembly plant in Sunderland. In a typical week Exel receives and unloads almost 80 containers involving over 3,000 different product lines. From this around 250 just-in-time deliveries are made to Nissan’s assembly lines which are located about a mile away.
For the future, it is clear that the internet will assume a growing role in the continuing attempt to strip time and cost from the entire vehicle manufacturing process, from ordering the individual parts for assembly to delivery of the finished product to the final customer. However, it is important to realise that the implementation of lean logistics procedures in vehicle manufacturing and the concomitant aim to produce the 14-day car (or something faster) owes everything to reducing unit costs and achieving greater responsiveness in the marketplace and little to do with enhancing customer satisfaction. Anecdotal evidence, backed up by the findings of consumer panels, suggest that private buyers are not unduly concerned over having to wait a few weeks for the car of their dreams while, in the fleet market, buyers plan their replacement programmes well ahead.
Meanwhile, the huge permutations available on even a relatively simple model range means that the vehicle industry has made conditions in its supply chain more difficult than they need be. For the future, perhaps a pattern will emerge whereby vehicle manufacturers produce a standard range of models “off-the-peg” which will satisfy many consumers, while those who require a bespoke product will have to wait a bit longer and perhaps pay a higher price.
It is unlikely in the extreme, though, that the trend towards the use of outside logistics specialists will be reversed and, more than ever, vehicle manufacturers will depend on specialist skills to ensure the smooth running of their factories and the satisfaction of their customers.