AWKnowledge’s Commercial Vehicles Newsletter investigates Europe’s largest truck plant and finds it is the latest example of a rapidly spreading trend toward supplier investment in a manufacturer’s assembly facility. Bill Diem reports.
DaimlerChrysler, which is leading the trend to bring suppliers and their capital into its automotive plants, has not forgotten its truck business. Delphi is among the newest suppliers to begin production at the industrial park attached to Europe’s largest truck plant at Worth am Rhein, where Mercedes-Benz has made trucks since 1965. The plant is getting larger, as Mercedes-Benz has moved production of the two Unimog lines of construction vehicles and tractors from Gaggenau to Worth, where it also makes the Actros, Atego and Axor on-road trucks.
Delphi chose to invest in the facility because it wanted the contract to develop the door module, and “expand to include logistics and managing the supply system,” said Jurgen Steupert, Delphi’s program manager for the project, “and DaimlerChrysler required Delphi to invest in a facility to make it happen.” Delphi invested “at least US$20m” in the facility, 140 kilometres south of Frankfurt, and on December 4th, 2002 began ramping up its operation there, joining several other suppliers in the industrial park.
Phase 1 began in 2001 when Grammer AG, Canada’s Intier and Fritzmeier Systems GmbH & Co. all joined the supplier park. Grammer manufactures seats, Intier produced beds and Fritzmeier makes the aerodynamic spoilers for the cabs.
Last year in Phase 2, Fritzmeier added facilities for making the storage compartments above the windshields and Intier added locker production. They also welcomed two new suppliers: the Norwegian Polimoon AS, which began furnishing storage compartments in the middle module, and Delphi, which supplies the door modules.
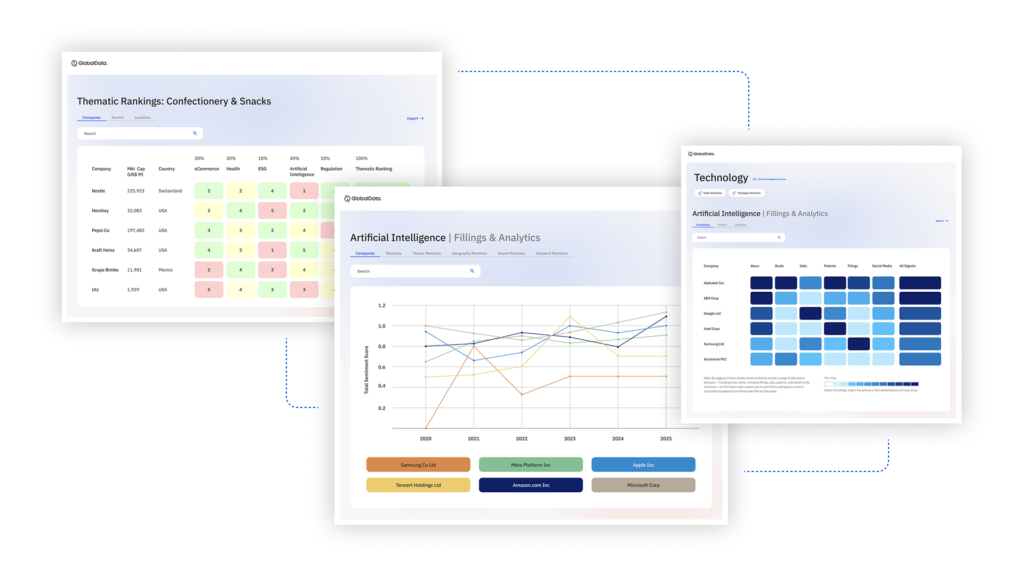
US Tariffs are shifting - will you react or anticipate?
Don’t let policy changes catch you off guard. Stay proactive with real-time data and expert analysis.
By GlobalDataPhase 3 in early 2004 will see the Finland’s Plastal Oy arrive to assemble the instrument panel module, including equipment for Mercedes-Benz fleet management and mapping unit, Fleetboard.
DaimlerChrysler’s Smartville, the French factory making the two-seat Smart cars, is the leading European example of supplier investment in an automaker’s plant. Seven suppliers invested in their own equipment to make major portions of the cars, letting DaimlerChrysler workers assemble the final product. In Brazil, Ford and General Motors have similar car factories, and Volkswagen goes even further in its Resende truck plant, where suppliers assemble the vehicles and VW workers do only quality validation.
At Worth, Delphi produces the inner door modules for the new Actros, which was introduced at the IAA last fall and which begins deliveries in spring. Delphi’s door module represents the work of more than 30 suppliers, and 85 percent of the value of the entire door. The module shipped to the DaimlerChrysler assembly area includes door handle, the pull grip, speaker grill and speaker, map pocket, the electronic control module, movable side glass, window lift and guidance system, interior and exterior latching, electric wiring and electronics including controls to heat and position outside mirrors, switches and climate control features.
DaimlerChrysler attaches the inner module in one step to the painted body-in-white door, and later the complete door is attached to the cab.
“We were given the contract to design and develop the compete door,” said Steupert, “with the understanding that we not make all of it. They have some suppliers in house and nominated others.” The door module, like seats and storage lockers and spoilers, is bulky, and like the cockpit to come it is complex. Both reasons support the idea of locating in a supplier park. “Once you get into A class surfaces, you need very sophisticated support. Shipping a piece that weighs 21 kilos over 900 km for in-sequence delivery is not logistically possible,” notes Steupert. “The deeper you get in the supply chain, toward the nuts and bolts, it makes no sense to be in a supplier park. Get to something as intricate as a door, where we have a large number of variants and component parts, and the shipping unit includes a lot of air, it makes sense.”
|
And there’s a strategic reason too, notes James A. Bertrand, president of Delphi Safety & Interior Systems. “Being close to our customer emphasizes our commitment to our mutual success.” Mutual success is the key.
“Supplier parks only make sense when both sides win,” said Steupert. “We don’t want to give our money away, we both have to be open and a partnership from beginning. The OEM must be open to cost benefits from giving more responsibility to suppliers, and the supplier must be open to a different approach than a mainstream plant.
DaimlerChrysler may have to pay more for a product, because we have to have more money for the building. They have to do a good benefit analysis. If they pay US$0.50 more for a part, but save US$1 internally, it’s good for both sides. “By developing the door module, even without full control over the choice of the supply chain, Delphi could design in savings.”
“I am a disciple of modularity,” Steupert said. Assembly of a module alone doesn’t justify such a project, “that’s prohibitive in trying to achieve cost synergies. I want responsibility for the functionality of a door, not just that it opens and closes. The technical specification might be hundreds of pages long.” With that responsibility, Delphi can find synergies, assure that interfaces all work, and make the part efficiently.
Still, to make the investment at Worth pay off, it had to rethink the way it makes factories. “You can’t build a factory like any other, with all the overhead. It would kill the financing,” said Steupert. “As a supplier we must be somewhat flexible in putting together an organization that is Lean with a capital L and minimizes overhead structure. We have only the number of employees and managers needed at the site.”
Services like payroll and human resources, a normal part of plant life, have been given to other Delphi installations in Germany that had resources available. Eventually, Delphi will probably install a supplier park headquarters. “We made a strategic decision to do this for others also,” said Steupert. “We could have 10 or 12 little units around Germany that you could manage from a central place.” Even with all the cost reduction possible, Delphi needs to protect its investment against the possibility that the Actros doesn’t sell. In the contract, “we have some flexibility to handle abnormalities that minimize the risk from a financial standpoint,” said Steupert. For example, if floorspace becomes available because Actros volume is below a certain level, Delphi can use the facility to make other parts.
The Mercedes-Benz Commercial Vehicles division is investing heavily itself in Worth and its products. In 2001, the plant workers built 80,000 Mercedes-Benz Actros, Axor and Atego trucks, and the new Unimog lines will add single-shift capacity of 3,500 units. The company counts heavily on the success of the revised Actros, which has a market share of about 20 percent in western Europe and is sold in 98 countries. More than 230,000 units have been produced. The first two models to be revised will be the 1832 to 2558 models for long-distance haulage, consisting of two-axle semi-trailer tractors and three-axle trucks mainly for use with demountable bodies. They will be followed by platform trucks, construction site and special-purpose vehicles with two, three or four axles. The new Actros trucks currently are being demonstrated to customers and deliveries will begin in the spring.
To discover more and download your free sample of “World Commercial Vehicles” newsletter, please click here.