At first glance inside Toyota Motor Manufacturing Canada Inc., there appears to be no chance at all that the first Lexus vehicles to be built outside Japan will roll off the assembly line in September. Report by Greg Keenan.
Contractors are erecting robots and buzzing about in forklifts. Team members are sequestered in a room full of computers designing their workstations. The body shop is unfinished, as are the final lines and other key assembly areas.
But even as the assembly line for the Lexus RX330 sport utility vehicle begins to spring to life, the focus on quality as Job One-to borrow a phrase from an old ad campaign at another auto maker – is constant. Toyota is seeking rigid attention to quality from its employees, its suppliers and their employees as it gears up for the most important vehicle launch in its history and arguably the most important for the auto maker in North America since Toyota began making cars here in the
1980s.
That’s evident from a 90-minute conversation with Toyota Motor Canada resident Ray Tanguay and couple of his key people in a mundane boardroom at the plant in Cambridge, Ont., an hour west of Toronto. Tanguay politely dismisses the current Lexus ad campaign in North America that extols the relentless pursuit of perfection. Instead, he refers to “the passionate pursuit of perfection.” “’Relentless’ doesn’t have enough energy,” he says.
He’s well aware that the eyes of Toyota Motor Corp. in Japan are gazing steadily at his operation and that success is essential for the $650-million investment in the company’s only Canadian assembly plant. “This is a real feather not only for TMMC, it’s a real feather for Canada,” Tanguay says. “There’s not a better compliment that we can get.”
How well do you really know your competitors?
Access the most comprehensive Company Profiles on the market, powered by GlobalData. Save hours of research. Gain competitive edge.
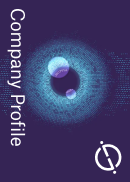
Thank you!
Your download email will arrive shortly
Not ready to buy yet? Download a free sample
We are confident about the unique quality of our Company Profiles. However, we want you to make the most beneficial decision for your business, so we offer a free sample that you can download by submitting the below form
By GlobalDataThat view is echoed by Al Power, president of Decoma International Inc. and one of the suppliers Toyota Motor Canada is counting on to provide quality, first time, every time. “We know we have a world-class industry here in Canada,” Power says. “This kind of reaffirms it.”
It’s not an experiment. Toyota has anointed its Canadian plant to assemble the first Lexus model outside Japan and chose the highest-selling Lexus vehicle in North America, not a niche car with sales of 10,000 or 12,000 a year.
Toyota’s luxury Lexus division sold 73,000 RX300 models last year – the name for the previous generation of the SUV. The RX330 – versions made in Japan are already on sale in Canada – sells for between $49,900 and $62,295 in Canada.
There’s a three-month wait for the fully loaded version, which comes with a DVD-based navigation system and DVD player and a rear-mounted camera that shows drivers what’s behind them as they back up.
An RX330 will come off the line every 3.5 minutes once the 700 TMMC employees crank the assembly line up to full production of 60,000 vehicles a year late this fall.
“It’s a full-fledged investment in Canada,” says industry analyst Koji Endo, who follows Toyota for Credit Suisse First Boston in Tokyo. “It’s very important.”
Tanguay and other TMMC executives have spent much time in the past few months visiting suppliers, assessing their plants and procedures and making sure they will be ready. “Is the building up? Are the tools in place?” asks Dave Nicolle, assistant general manager of supplier preparation. “Are you ready for the various milestones?”
Nicolle has urged suppliers to make their Lexus work areas stand out from the rest of their operations. Suppliers take extra care of the tools they’re using to make Lexus parts, he says, so one supplier will put its Lexus tools on a clean rack and cover them with a curtain.
The Cambridge operation is also making sure its own house is in order, from the body shop to the paint shop to final assembly.
Employees who work in the paint shop face some of the strictest rules in the entire plant. They can’t use Snuggle or Downy fabric softeners on their clothes. English Leather colognes are forbidden. Fumes from any of those items can contaminate the paint and cause craters in the final coat.
Forklifts used in the paint shop can’t go anywhere else in the plant. Cardboard is banned in the paint shop to reduce airborne fibres.
Toyota has also found a way to make the paint shop more environmentally friendly. The traditional way of sending vehicles through a paint shop is in batches of 30 or 50 or more. Fifty vehicles will go through and be painted white. The next 50 will be painted blue.
The sprayers have to be flushed with solvent each time the colour changes, causing an environmental headache and waste if the colours are switched for each individual vehicle.
But Toyota will paint the SUVs individually. It has developed a system where a robot will grab a cartridge filled with one colour, spray the SUV, put the cartridge back and pick up another cartridge to spray the next vehicle. That drastically reduces the need to flush the sprayers.
“We don’t find too many customers who want to buy 50 cars,” Tanguay says. Toyota is trying to develop a more customer-driven assembly process, so that vehicles are assembled as soon as possible after customers order them.
In the body shop, billboards advise team members about processes where extra care needs to be taken, the rear suspension mounts, to cite one example. Banks of video monitors will sit near the assembly line so workers can examine specific elements of a job close-up. Touching will be kept to a minimum.
That’s particularly critical in the interior, where the wood trim in each vehicle will come as much possible from the same tree, so any damage to one piece means all the trim has to be replaced. And it’s real wood – walnut from U.S. forests and bird’s eye maple from Canada. The wood is sent to Switzerland for cutting, then to Germany for storage and distribution, and to Romania where it’s manufactured into the trim for centre and rear consoles and door and seat trim. Then it goes back to Germany and from there to parts plants in Ontario for installation into the components that will go in the vehicle.
Tanguay says the goal is to infuse the entire TMMC operation – Corolla sedans and Matrix crossover utility vehicles are cranked out on another assembly line – with the attention to quality that is essential for Lexus.
“We want to make a Lexus plant,” he says.
When asked if that means converting the entire plant to Lexus production, he points out that any discussion of that is premature since “we haven’t produced anything yet.”
But Endo, the Credit Suisse analyst in Tokyo, says it makes a lot of sense to turn the plant over completely to Lexus, perhaps by adding production of the ES300 sedan, which shares a platform with the RX330.
If the market share losses in North America experienced by the Big Three U.S. auto makers continue, he says, they may force the U.S. government to place tariffs or quotas on imports, which would hit Lexus hard, since most of the division’s vehicles are imported from Japan, even with production of the SUV starting here. “It’s kind of essential to make Lexus in North America,” he says.
Note: All dollar figures are Canadian $.