At
‘AM&P’, we are not what you might call “neat freaks.” We work in offices that
often have but a single path between door and desk – the floor being the only
available space in which to stack press kits, papers, reports, photos, notebooks,
and all other manner of information from which we assemble this magazine. Occasionally,
we determine that our working conditions might be bordering on the hazardous and
we attempt to clean up.
This month, we found the
following cool stuff about materials buried amidst copies of European car magazines,
machine pamphlets, and briefcase bags emblazoned with corporate logos. Which
is not to disparage the importance of this information, but to state that this
is not a tidy little article that sticks to one topic. (In fact, there’s something
here about each of the big three materials: aluminum, composites and steel.)
But why draw attention to this haphazard creative process? To make the point
that in this day and age, regardless of your discipline, neither the information
that you use nor the solutions that you seek come in nice orderly packages.
Beware of anyone with a
clean desk.
Glückwünsche
For five years now, Stahl-Informations-Zentrum,
a German steel industry organization, has been awarding Steel Innovation Prizes.
This year, two such awards were given to subsidiaries of ThyssenKrupp AG (Düsseldorf)
for developments in automotive components. A new catalytic converter substrate
garnered an award for Krupp VDM GmbH, while a new multi-link suspension system
design landed one for Thyssen Umformtechnik und Guss (TUG) GmbH.
To explain the significance
of the new catalytic converter substrate, first consider this: according to
Krupp VDM, 70% of all pollutants emitted from a conventional catalytic converter
are produced when the engine is started, before the catalytic converter has
warmed to its ideal operating temperature. So the obvious key to reducing pollutants
is to heat the cat faster. But how? Krupp VDM’s solution is to reduce the thickness
of the steel substrate, the honeycomb-shaped surface that’s coated with the
expensive metals (platinum and rhodium) that act as the catalysts.
How well do you really know your competitors?
Access the most comprehensive Company Profiles on the market, powered by GlobalData. Save hours of research. Gain competitive edge.
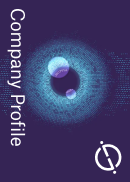
Thank you!
Your download email will arrive shortly
Not ready to buy yet? Download a free sample
We are confident about the unique quality of our Company Profiles. However, we want you to make the most beneficial decision for your business, so we offer a free sample that you can download by submitting the below form
By GlobalDataSeems pretty simple. So
why hadn’t anyone thought of this before? Well, they probably did. But metallic-substrate
converters are made from corrugated and wound metal foils, and according to
Krupp VDM, inadequate heat resistance has limited these materials to a thickness
of no less than 30 µm. But a new alloy called Aluchrom 7Al Yhf – developed in
conjunction with the Fraunhofer Institute for Applied Materials Research (Bremen),
the University of Wuppertal, and Emitec GmbH (Lohmar) – can be manufactured
in a thickness of just 25 µm and still withstand the 1100°C exhaust temperatures.
The alloy is created by first and foremost increasing its aluminum content.
This improves heat resistance, as the aluminum oxidizes under heat exposure,
forming a protective coating. This necessitates adding reactive elements yttrium
and hafnium to the alloy to slow the aluminum depletion, thereby achieving a
similar life span to that of conventional 50 µm foils. Furthermore, the low
electrical resistance of the material allows catalytic converters using it as
a substrate to be electrically preheated, further reducing light off times.
While using chemistry to
save the environment is a noble endeavor, ThyssenKrupp’s other award-winning
idea may be nearer and dearer to the hearts of many, as it involves saving cash.
Even better, the new suspension design can facilitate high-end handling performance
in decidedly less-than-high-end vehicles.
The crux of the multi-link
design is a stamped wheel knuckle. Rather than employing a cast and machined
part like a traditional multi-link suspension, TUG uses two stampings joined
by shielded arc welding; the inner piece also acts as the trailing arm. Main
advantages include a 30-40% weight reduction, while manufacturing costs are
said to be 50% lower. Since this design is more compact and less costly, it
also allows for multi-link suspension systems to be fitted on smaller vehicles.
Tests of the same system with high strength steels show even further weight
reduction potential.
Glückwünsche Zwei
Speaking of German awards…it
is worth noting that Dow Automotive (Auburn Hills, MI) was the only North American
supplier to pick up a corporate supplier award from Volkswagen AG. Dow Automotive
received the 1999 Leading Edge Award. There were a total of 45 suppliers awarded
based on their meeting VW’s requirements for flexibility, innovation, quality,
service, and competition.
(We get flooded with announcements
about companies winning such things as awards from GM and other automakers,
but this curious distinction vis-à-vis a North American company and a German
company piqued our attention.)
Dow Automotive’s resins
are used in a variety of applications – interior trim, consoles, and instrument
panels among them – on VW vehicles including the Golf A IV, Bora, Jetta, Passat,
Seat Toledo, and Audi A6.
Bumpin’ Around
According to GE Plastics’
automotive group in Southfield, Michigan, the 2001 Chrysler and Dodge minivans
that have just started rolling are the first in their class to feature a thermoplastic
bumper beam that exceeds the 2.5-mph federal impact standard. Mark White, GE
Plastics market development manager comments, “We’ve integrated the functions
of the traditional steel or aluminum beam and impact-absorbing foam into one
high-performance, lightweight, injection molded system that not only meets the
required 2.5-mph federal impact standard but passes the federal impact test
at 5 mph.”
The bumper was developed
by GE Plastics along with Nascote Industries. It is being molded with xenoy
1103 resin, a blend of polycarbonate/polybutylene (PC/PBT), which means it combines
the performance strengths of both amorphous and crystalline materials, a high
flexural modulus, high tensile strength, good chemical resistance, and good
low-temperature impact.
Benefits of the bumper system
include the aforementioned impact resistance, as well as significant weight
reduction: it weighs 11.4 lb., which is 8 lb. less (or 41%) than the stamped
steel bumper it is replacing.
HOWEVER…the Bumper Project
Group of the American Iron and Steel Institute has conducted a study that shows
that the material that is presently dominant in the production of bumper systems
– steel, of course – will actually gain strength within the next few years,
marketwise, that is.
According to the study,
it looks like this:
- Steel: 76% of the market
in 1997; projected growth to 91% in 2004. - Aluminum: 6% of the market
in 1997; projected decline to 1.4% in 2004. - Plastics: 18% of the
market in 1997; projected decline to 7.6% in 2004.
A reason why steel is having
such a strong showing is because manufacturers are increasing their use of high-strength
(minimum yield strength > 35 ksi and a minimum tensile strength < 100 ksi) and
ultra high-strength steels (minimum tensile strength > 100 ksi). The study also
examined 11 bumper systems. Included:
- 2000 Ford F150 pick-
up front face bar. Stamped high-strength steel features a 22-in. depth-of-draw
for an aero advantage that facilitates fuel economy. - 2000 Ford Crown Victoria
and Mercury Grand Marquis front reinforcing beam. Roll formed with an ultra
high-strength steel. - 2000 T300 Dodge Ram pickup
front face bar. Stamped from high-strength steel. Blank designed so that 65%
of the finished trim line incorporated, thereby reducing scrap.
- 2000 Chevy GMT 800 pickup
front face bar. High-strength steel stamping features integrated brackets.
- 1998 Volkswagen Jetta
front reinforcing beam. Stamped from a high-strength steel tailor welded blank:
80,000 psi yield strength in the middle of the blank and 45,000 psi at the
two end portions, thereby providing strength and formability. - 2000 Toyota Avalon front
reinforcing beam. Roll formed ultra high-strength steel part mounts to the
rails with minimal bracketry. - 2000 Ford Ranger pickup
front face bar. Stamped high-strength steel part uses an energy-absorbing
mounting bracket. - 2000 Ford Taurus and
Mercury Sable front reinforcing beam. Roll formed from ultra high-strength
steel: actually 190 ksi tensile strength martensitic steel, which is said
to be the highest strength automotive sheet in production in North America.
- 2000 Chrysler Voyager
rear reinforcing beam. Ultra high-strength steel drawn to a 6-in. depth. - 2000 Toyota Camry front
reinforcing beam. Ultra high-strength steel roll formed with a large sweep
(35 sweep number) for a double box section. - 2000 Chevy Cavalier and
Pontiac Sunfire front reinforcing beam. Roll formed ultra-high strength steel
with a 50 sweep number, but this is a box section.
All of which goes to say
that there are a lot of steel bumpers out there now, and their number is expected
to grow.
Rollin’
Speaking of increases, this
from the Automotive Bright Product Association (ABPA; Troy, MI): in 2004 more
than 4.5 million aluminum chrome-plated wheels are expected to be produced.
This is in contrast to five years ago, when less than one million were produced.
The expectation is that the OEMs will have platers provide 2.5 million aluminum
chrome-plated wheels in 2001. Comments J. Patrick Billinge; “Consumers prefer
the look of chrome-plated wheels and consider them one of the top three options
when buying or leasing a new vehicle.” Billinge is the ABPA’s executive committee
spokesman, who went on to remark, “We fully expect consumer demand will drive
increased production well past 2010.”
![]() |
![]() |
This
photo is supposed to be a cutaway of a hot catalytic converter. Don’t stare at it too long or you might have flashbacks. |
That
yellow piece of metal that resembles a banana is actually the trailing arm of this multi-link suspension system. It’s also the same stamping that forms the inner piece of the wheel knuckle. |
To link to a related report
in our Knowledge Store, please click here.