Abstract
A survey has shown that in Germany alone,
car manufacturers and their 900 suppliers are using about 110 different CAD systems. This
heterogeneous system environment and the current lack of sufficient interface formats
necessitates expensive manual reworking of transmitted data. In the German automotive
industry alone the resulting costs amount to about DM 100 million per year [Hand-93]. One
way of improving the exchange of data is to use product data technology and
correspondingly powerful interface formats. This paper describes what is meant by product
data technology today and outlines a new ISO standard that supports this technology.
1 Product Data Technology
One essential factor of production in all
design and manufacturing processes is the checking or control of information processing.
In particular, the continuous availability and processing capability of product
information described by means of CAD/CAM systems has a decisive effect on both the
economy and flexibility, and therefore ultimately the competitiveness, of a company
[Zimm-93]. Especially at times of restructuring and cost-cutting in almost all sectors of
industry, the ability of CAD/CAM systems to communicate must be forcefully promoted as the
basis of measures that increase efficiency, such as simultaneous engineering or the
support of closer partnerships between manufacturers and suppliers with the aim of
reducing the depth of production. Communication in this context refers not only to the
exchange of information between the different CAD/CAM systems, but rather the ability to
access, interpret and subsequently process the information across the boundaries of
systems and companies throughout the entire computer-aided process in the development,
design, fabrication, maintenance and disposal of products and production facilities. The
objective must therefore be the:
- independence of CAD/CAM systems by means of
open selection of rival systems according to purely functional and economic criteria, - the ability to access, interpret and
subsequently process product data which is generated just once, throughout the product
life cycle by means of data sharing on the basis of international product data standards - and not least, to reduce costs and delays
incurred today during the exchange of data.
1.1 Product data is represented
by product models
The product life cycle comprises not only the generation of the product, in other words
the fields of development, design, and fabrication, but also includes functions such as
sales, maintenance and final disposal or recycling of a product. Product data therefore
describes all properties of a product and also includes the information required for its
manufacture. Since this data involves a virtual description of the product, this
description is termed “product model”.
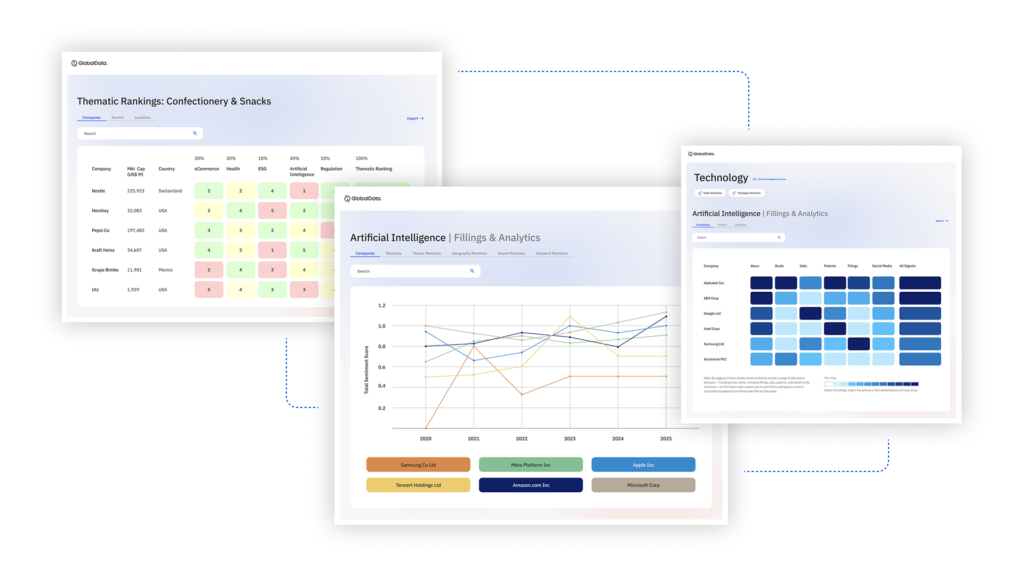
US Tariffs are shifting - will you react or anticipate?
Don’t let policy changes catch you off guard. Stay proactive with real-time data and expert analysis.
By GlobalData1.2 Definition of problem
In the context of computer-integrated production, the exchange of this product-defining
data is playing an increasingly important role. This data is generated and processed today
by CAD/CAM systems in predominantly incompatible formats and structures. The integration
of this data is a prerequisite for simultaneous engineering and complete consistency of
data within the various companies. The agreements (interfaces) between the various systems
that are necessary for the implementation of an efficient exchange of data must be equal
to this task. The exchange of product data is significant to companies both internally and
externally. The aim of internal product data exchange is to provide information technology
(IT) links between the various departments of a company such as design, project planning,
fabrication, assembly and quality assurance. External product data exchange is used for
transmitting product information between manufacturers and suppliers.
1.3 Product data interfaces
The above demands can only be met by open systems and appropriate interfaces. Open systems
permit the configuration of a CAD/CAM solution according to functional and economic
viewpoints. Since it is not practicable, in view of the high development costs, to develop
a specific interface for every possible system configuration, it is wise to use a
standardized interface for the exchange of product-defining data in order to minimize
development costs. In addition, standardized interfaces ensure the return on investment in
the area of information processing, despite the ever shorter life cycles of hardware and
software and the adherence to the stringent legal requirements for product liability
[Trip-93].1.3.1 Existing solutions are inadequate. The interfaces used thus far, such as
IGES, VDAIS, VDAFS or SET do not meet the requirements of an interface for product data
exchange as described above. They are suitable for the transmission of product information
in sub-areas of computer-integrated production in the form of technical drawings or simple
geometric models [And-89]. More detailed information such as tolerance specifications,
material properties, parts lists or even work planning information, however, can only be
transmitted incompletely, if at all.
2 STEP
The failings of existing interfaces have
been recognized by the International Standards organization ISO and have led to the
development of the STEP interface (Standard for the Exchange of Product Model Data). The
objective of STEP is: “an unambiguous representation of computer interpretable
product information through-out the life of a product” [ISO-10303-93]. Simultaneously
with the standardization of the actual interface, a draft methodology was developed in
order to eliminate the failings of existing standards, such as inadequate formal
description and non-prescribed test criteria.
2.1 STEP structure
The methods and principles used for the development of STEP are reflected in its
structure. STEP will appear as a series of the 10303 standards which, in addition to the
pure product model data, also define description methods, implementation methods and a
conformance testing methodology and framework.
2.2.1 Description methods
For the consistent, non-contradictory and semantically unambiguous description of the STEP
product model, the EXPRESS formal description language and its EXPRESS-G graphical
representation were defined. EXPRESS is not a programming language but a specification
language with object-oriented characteristics for the formal, unambiguous description of
the STEP product model in the form of information models. The integrated resources and
application protocols of STEP are defined in this language.
2.2.2 Implementation methods
An information model described in EXPRESS can be likened to a conceptual schema
description for databases. It thus remains independent of a specific implementation. It
is, however, available in a form suitable for computer processing. The specification can
therefore be simulated in different target implementations [And-92]. For transfer of a
model specified in EXPRESS into a special implementation form, various implementation
methods are used. Until now, the following implementations are supported:
- Physical file exchange for the exchange of
product data by means of a sequential file, - Data base implementation and
- An application programming interface for
database access of product data.
2.2.3 Conformance testing
methodology and framework
Basic principles and methods for verifying conformity were defined for the validation of
STEP supporting software. These describe general conformity criteria and test procedures
as well as methods for carrying out tests. An abstract test method is defined for each
method of implementation. Abstract test suites are developed accordingly for the generated
application protocols.
2.2.4 Integrated resources
The integrated resources constitute the core of STEP. These are information models that
describe the product data independently of a special application in EXPRESS [Grab-93,
ISO-10303-1-93]. They describe, for example, material, shape variation tolerance, form
feature and product structure configuration data of a product. It is also possible to
define parameters and rules for the visual presentation of product data. In addition, a
model (process structure, property and representation) has been defined for the imaging of
the logical sequence of process activities and their parameters (e. g. cutting speed).
2.2.5 Application Protocols
It is not practical to implement the entire scope of STEP for industrial use. On the one
hand, not all elements defined in the integrated resources are required for the support of
a special application (such as Application Protocol 214, numerical control process plans
for machine parts). On the other hand, a complete STEP implementation demands inordinately
high development costs. For this reason, application protocols have been standardized by
the ISO. These describe the extract from the partial models that is required for a
specific application. At present, 25 application protocol drafts are in the process of
being standardized.
3 Application Protocol 214
Automotive Design
In collaboration between the German
Automotive Association (VDA), ProSTEP and other international partners, the application
protocol “Core Data for Automotive Mechanical Design Processes” is currently
being developed as ISO standard 10303-214.
3.1 Scope of performance
AP 214 describes the product and production facilities data of development process chains
in the automotive industry. These include geometric and non-geometric data of parts,
assemblies, products and production facilities for mechanical parts and assemblies in
automobile manufacture. AP 214 comprises the following classes of product data:
- Product Structure Configuration
- Geometric and Topological Representation
(edge-, Face- and constructive solid models ) - Shape Variation Tolerance
- Part and Assembly descriptions by explicit
drawings - Kinematics
- Finite Element Analysis
- Material property
- Surface condition.
3.2 Benefits
AP214 represents a comprehensive information model for various process chains. Since it
describes all relevant data, it can offer both manufacturers and suppliers considerable
strategic benefits. These benefits, that can be transferred to almost all STEP
applications, include:
- system independence
- data consistency across the entire product
life cycle - redundance free product data description
- higher quality of the product data due to
unambiguous definitions - possibilities of long-term archiving
These advantages become very apparent on
considering that about 100 different CAD/CAM systems are in use by German car
manufacturers alone. This heterogeneous system environment and the lack of adequate
interface formats today, necessitates expensive manual reworking of transmitted data. In
the German automotive industry alone resulting costs amount to about DM 100 million per
year [Hand-93].
3.3 Current status
In the context of current development work a reference data model has been drawn up and
sent to the participating partners and national standardization boards for comment. At the
same time, the application reference model is being checked in detail on examples taken
from industrial practice in Germany, Japan and France. Furthermore proto-type conversions
of parts of the AP 214 were demonstrated in the form of data exchange processors and
database implementations on the occasion of an ISO working conference in Berlin in October
1993.
4 Industrial launch of STEP
As the first prototypes for application
protocol 214 sub-sets became available from major CAD vendors in 1993, the first
commercial pro-ducts will be available autumn 1994. In addition, it should be remembered
that STEP will be in use at BMW, Bosch, Mercedes Benz, Opel, Siemens and VW/Audi for the
CAD/CAM data exchange with their suppliers from 1995 onward. The industrial launch is
being supported by the foundation of ProSTEP Produktdatentechnologie GmbH, Darmstadt
[ProSTEP] which will develop solutions for improving the CAD/CAM data exchange and modules
for data integration. These are STEP processors for CAD-systems, methods for the
implementation of STEP-like product and production facilities databases and long-term
archiving, as well as STEP-conformant introduction of CAD/CAM systems in industry.
References
Literature
[And-89]: Anderl, R.; Das
Produktmodellkonzept von STEP; VDI-Z 12.1989
[And-92]: Anderl, R.; STEP-Schritte zum Produktmodell; CAD-CAM Report 8.1992
[Grab-93]: H. Grabowski, R. Anderl, A. Polly; Integriertes Produktmodell; Beuth Verlag
GmbH; Berlin; 1993
[Hand-93]: Handelsblatt vom 6.10.1993
[ISO-10303-1-93]: ISO-10303-1; Product Data Representation and Exchange-Part 1: Overview
and Fundamental Principles; ISO/IEC Schweiz (1993)
[ProSTEP]: ProSTEP Produktdatentechnologie GmbH, Julius-Reiber-Str. 15, D-64293 Darmstadt;
Tel +49-6151-928711
[Trip-93]: Machner, B.; Trippner, D.; ProSTEP: Der Schritt zur Datenintegration; CAD-CAM
Report Nr. 5; Mai 1993
[Zimm-93]: Zimmermeyer, G.; Mastering Product Data Technology as a Fundamental
Contribution to Competitiveness and Efficient Cooperation between Manufacturers and their
Suppliers; VDI Berichte Nr. 1096; VDI-Verlag; Düsseldorf; 1993
For further information contact:
Pro STEP Produktdatentechnologie GmbH,
Julius-Reiber-Str. 15
D-64239 Darmstadt
Tel +49-6151-92871-0
Fax +49-6151-9287-26