The Singular World of the
Automotive Industry
Suppliers to the automotive industry are
faced with a distinct environment. To stay competitive, an automotive supplier must react
to a complicated and ever-changing set of rules developed by the customer. These rules
describe the exact methods that product and order information moves through the supply
chain. The world’s leading automakers literally reach out and touch their suppliers
in a moment’s notice to broadcast these mandates and changes in demand.
The automotive industry is unique, since
most business rules differ between trading partner as well as by the operating division,
plant, and component. Moreover, trading partners continuously issue changes to these rules
and business practices.
This concept is captured by the term
release accounting. It is release accounting which sets the automotive industry apart from
any other.
A supplier’s ability to manage the
release accounting process plays a critical role in determining whether they are able to
respond to customer changes rapidly and profitably. Those suppliers who have automated and
integrated the release accounting segment are positioned for growth in the supplier
community of the future. They also report an increase in supplier ratings.
As a high-volume automobile supplier, your
first step is to understand what release accounting really is, and how it impacts your
organization. The next step is to locate the best solution to automate and integrate the
release accounting process into your organization.
How well do you really know your competitors?
Access the most comprehensive Company Profiles on the market, powered by GlobalData. Save hours of research. Gain competitive edge.
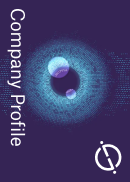
Thank you!
Your download email will arrive shortly
Not ready to buy yet? Download a free sample
We are confident about the unique quality of our Company Profiles. However, we want you to make the most beneficial decision for your business, so we offer a free sample that you can download by submitting the below form
By GlobalDataA Working Definition
A high level definition of release
accounting is the set of rules mandated by the customer for the exchange of information,
product, and money related to the movement of finished goods and raw materials throughout
the supply chain. Part of what makes this so complex is that these business rules vary by
customer, division, plant, and commodity shipped. In addition, automotive industry rules
and business practices are constantly changing.
As an example, automotive industry release
accounting rules mandate:
- the methods used to receive RFQs and bid on
contracts. - the process to track and manage demand
coming in from the customer. - the content of firm and planned
requirements. - the items expected to ship and delivery
schedule. - the format of shipping documents.
- the methods used to notify the customer of
goods in transit. - the methods used for payment.
In many cases, Electronic Data Interchange
(EDI) and electronic commerce play an integral part in this process. Yet translating the
EDI document into human-readable form is just the beginning. How the data is used, and
understanding how these unique requirements should be processed, is the essence of release
accounting.
Examples of Automotive Release
Accounting
The significance of the release accounting
process becomes clear when examining real-world examples faced by high-volume automotive
suppliers.
For instance, it is typical for separate
divisions of a major original equipment manufacturer (OEM) to send a supplier planning and
shipping schedules via EDI. Each division has its own set of rules as to the type of EDI
transmission (ANSI X.12, EDIFACT, Odette, proprietary, etc.); the version level used (ANSI
3060, 4010, etc); the transaction sets or messages used (850, 830, 862, 866, 855, DELFOR,
DELJIT, DESADV); and finally the segments and elements required.
It is also common for individual plants
within a single division to use different rules regarding ship schedules, shipping
documents, CUM tracking, manifest numbers, purchase orders, prices, engineering revision
levels, effectivity dates, expiration dates, retro-active pricing and billing, model year
changeover, and more.
Once each distinct transaction set is
received, the associated rules must be applied. For example, one division within an OEM
stipulates that suppliers track CUMs – a measurement of the total quantity of a
particular part number that is shipped or required from the beginning of a model year up
to a certain point in time. The supplier is asked to transmit a CUM figure back on the ASN
(856/Advanced Ship Notice) at time of shipment. However, the CUM total tracked and
reported can vary by customer as well as division. Some trading partners may want that
figure to represent the total CUM shipped as of the last shipment made, as of the previous
shipment, or including current shipment.
Trading partner rules also vary in regards
to bar coding. Plant-specific bar code scanning mandates set the details on label
information, as well as the process for scanning to verify shipments with ASNs.
Suppliers must meet OEM mandates regarding
rounding the requirement to a standard pack quantity or adjusting if ahead or behind
schedule. Suppliers need to track shipments in transit, arrival-based ship dates and
shipment-based dates.
Additionally, the dates and quantities
pulled in by an EDI package cannot be passed directly into a sales order module or into
production scheduling. This is because type and frequency codes are transmitted along with
many other pieces of information. For example, when a supplier receives a planning
requirement asking for a set number of units, most scheduling modules will plan for a
shipment of that quantity to go out on the date indicated on the order. However, the codes
imbedded within the EDI may indicate that demand must be spread over weeks or days within
a given month, according to rules established by the trading partner.
Other unique rules include instituting
pay-on-production or pay-on-consumption for parts shipped. That is, you cannot bill your
customer until they actually use your product. Consequently, you must maintain your own
in-house inventory as well as keep track of what you have shipped to the customer but has
not been used by your customer. Only when they notify you-typically via EDI-that they have
consumed your material can you invoice that customer.
In another example of a release accounting
function, many OEMs use special order numbers to track parts and shipments. You may be
asked to track by kanban numbers, receipt authorization numbers (RANs), delivery order
numbers (DONs), KD order numbers, and manifest numbers on your invoices. This means you
need to carefully track these unique numbers along with your own internal coding for
payment.
This is just a small portion of unique
requirements that make the management of release accounting a cumbersome process.
The Release Accounting Solution
High-volume automotive suppliers will
thrive in the years to come by automating the application of complex release accounting
rules and integrating the data with business systems.
All too often, the automotive release
accounting process is still manual which makes it difficult to respond immediately to
changes in trading partner schedules.
In order to make automated release
accounting systems practical, they must be updated constantly, flexible, and easy to use.
Moreover, the systems must handle the unique environment of the automotive industry.
Developed specifically for automotive
suppliers, Future Three’s integrated release accounting systems set a standard for
excellence in supply chain management. Future Three’s AutoRelease, VendorRelease,
AutoScan and related applications enable suppliers to automate EDI, shipping and release
accounting and integrate with production scheduling, MRP, inventory and financial modules.
The company offers the expertise to solve virtually all release accounting tasks.
Future Three systems keep you up-to-date
with your customers ever changing requirements – automatically processing customer
releases into business systems, MRP and production scheduling modules. This enables each
department to access data where they need it. At ship time, Future Three applications
notify what is due and available to ship, then create documents necessary for delivery and
automatically generate an ASN. The applications then update inventory, accounts receivable
and general ledger modules.
Besides easily handling all release
accounting tasks, Future Three works closely with OEMs and the AIAG to stay at the
forefront of industry electronic commerce standards. In fact, OEMs often involve Future
Three in innovative solutions that continue to improve the order-fulfillment process. This
means that current release accounting data, and every update made in the future, is
automatically processed.