Bosch.jpg” align=right vspace=5 border=0>A petrol engine needs three things in order to function properly: air, fuel and a spark. The spark plug ignites the air/fuel mixture, producing the combustion that powers the engine. In January 2002, Robert Bosch celebrated a hundred years since it was awarded the patent for the first spark plug.
Designed to be combined with a high-tension magneto ignition system, the spark plug solved what Carl Benz had described as the most ‘fundamental obstacle’ to early motoring. Together with improvements in production technology, the spark plug laid the foundations for the rapid increase in vehicle production over the decades that followed.
Early version spark plugs, used in low-speed, low-compression petrol engines, had a life of just 600 miles as compared to the modern copper-nickel spark plug, which lasts up to 18,000 miles. The spark plug is a key engine system component, playing a major role in fuel economy, clean, efficient combustion and the reliable operation of engines and catalytic converters. A typical spark plug will spark up to 100 times per second or more than 20 million sparks over its useful life.
Although the useful life of a spark plug has been extended, its basic function has not significantly changed since the early 1900s. What has changed, however, are the requirements for emissions and service life.
Prior to 1974 in the US, for example, the main concerns which influenced the plug’s design were that it fitted properly, operated at the correct, self-cleaning temperature and that it minimised demand on the ignition reserve. Nickel-chromium was the material most commonly used. In 1974, the US government imposed fuel mandates and regulations to reduce emissions. These required the use of unleaded fuel and led to the introduction of smaller engines and new engine designs, all of which prompted changes in spark plug design. From this point, two factors drove spark plug design: first, since unleaded fuel has a higher burn-off temperature, the plug’s heat range needed to be broadened, enabling it to reach the self-cleaning temperature at lower loads and to avoid overheating at higher loads. Secondly, the spark plug needed to perform consistently in order to prevent damaging the catalytic converter.
How well do you really know your competitors?
Access the most comprehensive Company Profiles on the market, powered by GlobalData. Save hours of research. Gain competitive edge.
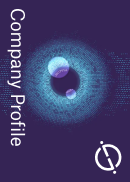
Thank you!
Your download email will arrive shortly
Not ready to buy yet? Download a free sample
We are confident about the unique quality of our Company Profiles. However, we want you to make the most beneficial decision for your business, so we offer a free sample that you can download by submitting the below form
By GlobalDataAs a result, new materials offering improved corrosion and erosion resistance and providing greater capacity to transfer heat were integrated into the design. One such material was copper, used for the plug’s core and surrounded by nickel-chromium. Introduced in the early 1980s, this design provides excellent heat transfer, a wider heat range and improved anti-fouling. By the end of the 1980s, most spark plug makers had switched to using copper core, which remains the standard today.
Yet copper isn’t the only material that has been combined with nickel chromium to improve performance. In 1960, Bosch recognised the value that platinum added to automotive spark plugs, providing improved corrosion and erosion resistance and a longer performance life than found with the standard copper core plug. Bosch then introduced the first platinum tipped plug. The company later advanced the use of platinum in spark plugs when it converted the platinum tipped plug design into a spark plug featuring a centre electrode that is 99.9% pure platinum. This plug, the Bosch Platinum, was introduced to the North American market in 1985. It features a centre electrode made entirely of platinum that is sintered, or heat fused, into a ceramic insulator.
In Europe, spark plug manufacturers talk of precious metal plugs lasting between 55,000 and 80,000 miles, compared to a copper alloy multi-ground electrode plug which lasts up to 35,000 miles. A precious metal plug typically retails at €13 on the aftermarket, double that of its copper alloy counterpart.
Platinum can withstand temperatures of up to 1,600 degrees Fahrenheit and so less metal is lost during firing. It is also more resistant to corrosion and pitting than traditional copper and nickel alloy electrodes. In early 1984, Bosch became the first manufacturer to agressively market a platinum-tipped plug. Driven by federal legislation, the fitment of platinum-electrode spark plugs has risen dramatically since the mid-1980s. Industry estimates suggest that around 95% of cars sold in North America come equipped with platinum-tipped spark plugs. The majority (90%+) of GM, Ford and Chrysler vehicles have platinum or double platinum spark plugs. The Japanese vehicle makers based in North America are at similar fitment levels. Overall, about one-quarter of the North American car parc is currently equipped with such precious metal plugs.
Following the US trend, many of the luxury cars that are sold in Europe, such as the Mercedes-Benz C-class and Jaguar S-type, were fitted with platinum-tipped spark plugs designed to last 100,000 miles. In Europe, industry sources estimate that about 10% of new cars are currently fitted with longer-life platinum electrode spark plugs, rising to 25% by 2005.
Until a year ago, a life-of-car trend in operational longevity forced suppliers to look to the premium-priced precious metal OE spark plug sector to secure their profits. Plug manufacturers, however, now say that the emphasis has changed, as an auto executive for a plug maker said: “The cost pressures that the American vehicle makers are now facing is causing them to question whether they actually need a premium-priced, precious metal spark plug or would they be better off with a conventional spark plug that is technically the same but the durability is half or maybe a third of a platinum plug.”
|
Inevitably, however, as more new cars are fitted with longer-life platinum electrode spark plugs, the knock-on effect is a reduced replacement market. The consensus among plug manufacturers is that the European aftermarket is declining by 7-8% in volume terms each year while in North America, plug manufacturers talk of 4-7% annual slippage. Another factor dampening the European spark plug aftermarket has been the popularity of diesel engines in passenger cars. Instead of spark plugs, glow plugs are used for diesel engines to pre-heat each cylinder prior to starting.
A glow plug is used in the ignition system for a diesel engine. Instead of a spark-ignition system, the glow plug is used to ignite the fuel in the engine. When a glow igniter is attached to a glow plug, it causes the glow plug’s coil to ‘glow’ white-hot. This ignites the air/fuel mixture in the cylinder when the engine is started. When the engine is running, the heat generated during compression and combustion keeps the glow plug’s element hot enough to continue igniting the fuel mixture on its own without the help of an external power source.
Manufacturers estimate that the European market for glow plugs is rising at a rate of 5% annually. Cars with fewer cylinders per vehicle are also cause for concern amongst spark plug manufacturers. Emissions requirements will drive the market in the future.
Future trends
Future spark plug designs will evolve in response to changes in ignition and fuel injection systems, decreases in engine size, the addition of multi-valved heads, the push by vehicle makers to design for longer replacement intervals, and pressure to increase fuel economy and to further decrease emissions.
Honda’s i-DSI (intelligently controlled Dual and Sequential Ignition) system used in its Jazz model, for example, uses a twin-spark design for the next generation i-series of petrol engines. A pair of spark plugs installed diagonally opposite in each of the four cylinders within a high-swirl combustion chamber helps to achieve low emissions and fuel consumption and complies with EU2005. The twin-spark design accelerates the propagation of flame, which results in intensive, rapid and highly efficient combustion for generating higher pressure and output. The i-DSI units offer improved packaging and rapid heating of the catalytic converter by including a rear-mounted exhaust manifold in addition to the friction reduction technology. The R&D division of Honda suggests that the fuel consumption level for 1.2 litre and 1.4 litre engines is 53mpg and 51.7mpg respectively.
Spark plugs for direction injection engines require special characteristics, too. The direct-injection (DI) petrol engine has drawn considerable attention recently for energy savings and emission reductions. Compared with current port fuel injection (PFI) engines, DI engines are designed to have high specific power output, low fuel consumption and low emissions at the same time. A significant feature of the DI petrol engine is its capability to freely alter the state of combustion from homogeneous to stratified combustion at different load conditions. Engines with high power density such as the DI engine, are also prone to knock. To suppress engine knocking a flexible and precise combustion control mechanism is required. Some of the characteristics required for spark plugs used in DI petrol engines include: the firing point is set slightly deeper in the combustion chamber; the plug has increased temperature resistance; the fuel mixture is stratified for low and medium engine speeds; and the plug has anti-carbon fouling properties with self-cleaning capability.