Every two years, Bosch demonstrates a variety of products at its proving ground in Boxberg, Germany. The site includes a hair-raising high-speed oval, a white-knuckle handling course and a range of rough-road tracks peppered with potholes and other nasty surprises. All in all, the perfect location to allow 500 motoring hacks from across the globe put the very latest auto technology through its paces. Shaken but not stirred, Matthew Beecham reports.
As the world’s second largest supplier of automotive technology (behind Delphi Corp), Robert Bosch generated sales of €23.2 billion last year, with 144,700 workers. The German group is targeting automotive sales of €23.5 billion this year, a modest 1.9% growth over the year but its annual R&D budget has been increased by 7% to €2.2 billion. And most of that is being spent on three key areas of development: chassis, driver assistance and drivetrain.
Braking news
In his keynote speech, newly-appointed head of the group’s automotive business, Bernd Bohr gave a clear indication of the direction in which the group’s chassis department is heading. He said: “Having first introduced ABS and ESP [Electronic Stability Programme], we are the only manufacturer to produce the electro-hydraulic brake Sensotronic Brake Control in series [production]. We are fully aware of the fact that this, as a first step to realising brake-by-wire will only remain a high-end solution for the time being, not least due to the highly sophisticated on-board network infrastructures. We are therefore extending the scope of our ESP by a number of additional functions. We are also planning for an interaction with the active steering system which is being developed by our joint venture company, ZF Lenksysteme. Thus in the future, Bosch will not be offering just a single ESP, but a modular system which allows an almost free combination of desired functions tailored to individual markets. In the long run, however, the future belongs to brake by wire – combined with the advanced on-board network – and Bosch is already prepared for that.”
Bosch is expecting massive increases in the sale of ESP through this decade once customers appreciate their value. Although fitment rates of ESP have shown meteoric growth in Europe, American drivers need more convincing. As a result, Bosch has teamed up with Continental Teves to alert them of the potential benefits of fitting their cars with ESP. The company says ESP can save more lives than the airbag, improving stability and grip while cornering, setting limits for safe driving and preventing rollover accidents. Bosch reckons that ESP is currently fitted on one out of two new passenger cars in Germany, one out of five in France, one out of eight in Italy and one out of 12 in the UK. In North America, Bosch expects ESP fitment levels to reach 12% by 2005, up from 5% last year. To satisfy demand and maintain its market lead, Bosch will increase production from last year’s 3 million units to 3.6 million this year. Since producing its first ESP in 1995, Bosch has produced some 8 million units
A turn for the better?
While there has been much talk of steer-by-wire, it’s unlikely that we shall see it before the end of this decade. “[In 2001], we expected steer by wire to be introduced on a series production basis from 2005,” said Colin Carter, sales director of ZF Lenksysteme. “In the meantime, certain reservations have surfaced. The prognosis now is that the first genuine steer by wire system for cars will not be available until 2010 at the earliest. Because of its great complexity, the system requires a considerable outlay in order to guarantee the necessary safety — and this makes it very expensive: the kind of sums which are just out of the question at the moment in the very cost-conscious passenger car sector. On top of this, steer by wire is a system for the luxury car, whose owners place a very high value on safety. In general, this group of clients has no confidence in a technology which dispenses with a mechanical connection between the steering wheel and the road wheels.”
How well do you really know your competitors?
Access the most comprehensive Company Profiles on the market, powered by GlobalData. Save hours of research. Gain competitive edge.
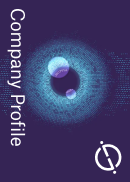
Thank you!
Your download email will arrive shortly
Not ready to buy yet? Download a free sample
We are confident about the unique quality of our Company Profiles. However, we want you to make the most beneficial decision for your business, so we offer a free sample that you can download by submitting the below form
By GlobalDataSensing growth
In the driver assistance arena, Bosch continues to develop its ‘sensitive car’ concept using surround ‘sensorics’. Bosch engineers reckon that the combination of ultrasonic, radar and video sensors all add up to extra benefits for the driver such as improved night vision, support for lane retention and automatic stop and go systems. Bosch says that the first products based on video sensorics will go on sale in 2005. Bosch currently employs 300 R&D engineers working on driver assistance, up from 100 engineers in 2001. “That is an indication of the push in growth we are expecting,” said Bohr.
Bosch sees the development of the drivetrain determined by three driving forces: reduction of exhaust emissions in Europe and North America; greater fuel economy; and ‘fun to drive’. Bohr said this final factor “is only ridiculed by those who, by focussing on solid technology, are overlooking the customer.” According to Bohr, ‘fun to drive’ is a factor which is most likely fulfilled by the diesel direct injection engine.
Figure 1: Bernd Bohr
Trade secrets: “The secret is to think of the future when you are at the height of success. So, we are asking ourselves what will determine the future of the drivetrain?”
Injecting some fuel efficiency
Bosch has profited from the fast growing diesel market in Western Europe. Its diesel systems business represented the automotive division’s largest activity last year, generating sales revenues of some €6.5 billion. Delphi’s acquisition of Lucas three years ago gave it a foothold in the European diesel injection system market. Until then, Bosch had a virtual monopoly of the European market. The move by Delphi and subsequently Siemens VDO served as a wake-up call for Bosch, prompting it to deliver more and more innovation. It recently introduced three new direct injection components: a new common rail system, a new unit injector system and a high-pressure distribution pump. These contribute to better fuel economy and more powerful, cleaner engines. Bosch made nearly 9.5 million diesel injection systems worldwide last year, of which 4.1 million units were the traditional inline and distributor injector pumps, 4 million were common rail systems and the rest were unit-injector and unit-pump systems. Overall, Bosch claims a 50% share of the global diesel injection market. Dr Ulrich Dohle, president of Bosch’s diesel systems division predicts the company will produce some 11 million diesel injection systems in 2006, of which over 7 million will be common rail, equivalent to 65%, while the classic injection pumps would lose half of their market share.
Figure 2: Bosch’s diesel injection system production forecast
![]() |
click the image to enlarge |
The share of new cars with diesel engines registered in Western Europe rose to 38% in 2002. Bosch expects the diesel share of passenger cars in Western Europe to grow to about 50% in the next few years, pointing out that there is good growth potential for diesel-powered cars in the US and Eastern Europe. But changing consumer opinions and perceptions of, dare we say it, ‘dirty diesels’ will take some time. In a bid to raise the profile of diesel engines and dispel a few myths among journalists, Bosch has held a string of ‘Diesel Days’ in the US, Japan, Korea and Russia. Bosch reckons its 3rd generation common rail system can cut diesel emissions by up to 20% compared to other systems using solenoid or piezo technology, thereby meeting the Euro 4 emission limits which swing into force in 2005 for diesel-powered cars of up to 1.8-tonnes. But larger cars will probably have to be fitted with exhaust gas treatment systems in order to meet even the Euro 4 limits. As a result, Bosch says it is ‘seriously considering’ starting mass production of diesel particulate filters from 2005. A final decision is due to be made in the next few months.
Turning to the US market, Bosch points out that an increasing number of sports-utility vehicles, vans and pickups are being fitted with its high-pressure direct injection systems. Bosch also reports growing interest in the US in engines which are low in fuel consumption and toxic emissions but high in torque. In 2000, Bosch began supplying common rail injection systems to the Duramax engines of GMC’s Sierra and Chevrolet’s Silverado pickup trucks. Bosch also supplies common rail systems for Chrysler’s Dodge Ram 2500/3500 pickups. Bosch’s diesel technology centre in Detroit looks after adapting common rail system for the local market. The common rails are made at the company’s facility in Charleston, South Carolina. Bosch has invested some $160 million in this plant and expects direct injection diesel engines to have gained a ‘significant’ market share by 2010.
Figure 3: Bosch’s 3rd generation common rail system
Source: Bosch.
Bosch says its gasoline direct injection (GDI) technology will also become a major seller, despite initially poor performance, and that average fuel savings will rise from the current 7 – 9% to as much as 15% by around 2006. “More and more car manufacturers are becoming convinced of the potential of gasoline direct injection,” said Dr Rolf Leonhard, vice president development in Bosch’s gasoline systems division. Bosch currently supplies injection systems for production engines between 1.4- and 6-litres with power outputs of between 77 and 327 kW.
In terms of market growth, estimates of the penetration rates of GDI vary from one manufacturer to another. Assuming that GDI remains a niche technology and applicable to larger displacement, higher performance engines, then just-auto.com forecast market penetration, reaching 10% by 2008. However, if the fuel economy benefits can be truly demonstrated and GDI is proven to be a better solution over competing technologies, the potential market could be much higher, says just-auto.
As the penetration rate of diesel and gasoline direct injection systems increases on both sides of the Atlantic, the main manufacturers see good opportunities to serve the aftermarket. Bosch has focused on increasing competence in servicing electronically controlled injection systems, particularly the diesel systems coming onto the ex-manufacturer warranty market, such as common rail and unit injection. The German group’s strategy includes offering the latest diagnostic test equipment and providing training not only for garage technicians but also for the intermediary businesses supplying them.
Figure 4: Jump in: Journalists go for a spin around Bosch’s proving ground in Boxberg.
Figure 5: Hold tight: The high-speed oval is complete with speed-measurement and display equipment.
Figure 6: Slip-sliding away: The site’s skid pan is arguably the most valuable facility, allowing evaluation of Bosch’s ESP and electronic braking technologies.