It is no accident that as the twenty-first century dawns, car manufacturers have stepped up the pace of diesel engine development to a speed not seen in the century or so since Rudolf Diesel patented his internal combustion engine. Like so many other technical developments in automobile history, the current progress in diesel technology is the result of several seemingly unconnected developments.
Firstly, engine technology has reached a stage where the diesel could be dragged out of the dark ages and its full potential realised. Secondly, our finite resources of liquid fossil fuels are unlikely to last for the rest of this century, barring unexpected discoveries and we need an effective swift means to slow consumption. Finally, legislative pressure around the world on vehicle emissions and in particular the need to curb greenhouse gas emissions has never been greater.
The diesel engine is more efficient than any spark ignition engine – up to 25% more so than an equivalent petrol engine, and far more so than liquefied petroleum gas (LPG) engines. These efficiency gains directly translate into reductions in carbon dioxide emissions, so has the diesel’s time come?
Not if these were the only advantages that diesel could offer. Noxious emissions from diesel engines have been documented well enough over the past decade, but recent developments show that it is possible to deal with the most serious issues. With the search on for alternative fuel sources, it also seems that bio and synthetic fuel are likely to yield higher quantities of diesel than petrol fuels, while the quest for the holy grail of the road-ready hydrogen fuel cell continues.
Until now, the development of the diesel car has been largely in European hands. That’s partly because the engine was a European invention, with engineers and automotive historians arguing to this day over who invented it, either the German Rudolf Diesel or the Englishman Herbert Ackroyd-Stuart. It’s also partly because the lack of a domestic oil supply for many European markets has forced them to consider energy use carefully. Diesel’s relative efficiency is undoubtedly a factor here.
The near invisibility of diesel cars in markets such as the United States and Japan is for a combination of reasons including emissions, cost, fuel quality and legislation.
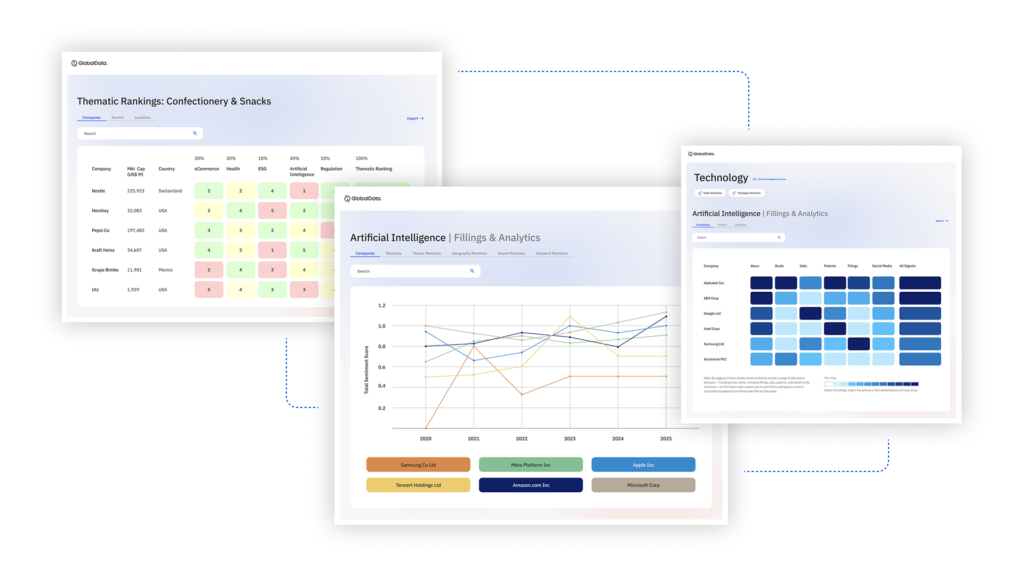
US Tariffs are shifting - will you react or anticipate?
Don’t let policy changes catch you off guard. Stay proactive with real-time data and expert analysis.
By GlobalDataNot surprisingly then, European manufacturers have led the advances in technology that have taken place over the past decade.
It’s clear that these advances have been considerable. After sixty years of comparatively little development in car diesel engine technology, the 1990s saw engines advance through three distinct development phases in less than ten years.
Diesel vs petrol
The motivation for this is clear. With global warming rising up the environmental agenda in all major markets, diesel engines offer a simple and highly effective means of reducing carbon dioxide emissions from motor vehicles in a relatively short time scale. That fact has not been lost either on the motor industry or legislators. This is particularly important for luxury carmakers whose vehicles would have the most difficulty in meeting any proposed average carbon dioxide emissions targets of around 140g/km.
We’ve already discussed the lower carbon dioxide emissions from diesel engines, compared with petrol engines. In addition to this, diesel engines produce much lower levels of hydrocarbons and carbon monoxide.
Against these emissions advantages, diesel engines have traditionally posed three distinct drawbacks, notably emissions of particulate matter (PM), sulphur dioxide and nitrogen oxides (NOX). That said, it should be noted that research in the 1990s by both Lucas and Volkswagen indicated that the NOX disadvantages of diesel engines are reversed after around 12,000 miles (20,000km) in operation. From that point, the research suggested, NOX emissions from petrol cars would exceed those from diesels.
The drawbacks, particularly those relating to PM emissions, caused big falls in diesel penetration in all European markets in the 1990s, but advances in engine design, exhaust after-treatment systems and fuels mean it is possible to more or less eliminate the problems.
With emissions objections effectively removed, the diesel car seems poised to tackle markets where diesel has traditionally not been accepted, notably the United States and Japan. Is it yet realistic to suppose that the US is ready for that change, while oil prices remain relatively low?
Diesel development
The principal difference between a petrol and diesel engine is in how ignition takes place. Whereas a petrol engine draws in a mixture of air and petrol to the cylinder, compresses it and ignites it with a spark to provide the energy to drive it, a diesel draws in air alone, compresses it, raising the temperature to the point where the fuel will spontaneously ignite when it is injected. It is this principal which gives the diesel its superior efficiency. No matter how sophisticated petrol engines become, it is impossible for them to match the efficiency of a compression-ignition engine. The best car diesels have a thermal efficiency of around 43% compared with around 30% for petrol engines.
Because this process causes more vibration – simply because the air is compressed to a much higher degree than a petrol engine, the engines must be stiffer and heavier to withstand it. This is also why diesel engines tend to last longer than petrol engines.
The higher compression ratio also means that diesel engines produce higher torque output than equivalent petrol engines. The torque, or pulling power of the engine is what provides rapid overtaking. On the other hand, diesel power output tends to be lower than for an equivalent petrol engine, simply because diesel engine speeds are lower than petrol engine speeds.
The type of diesel engine favoured by both the 1930s diesel pioneers, Citroen and Mercedes-Benz, was the same type used in European passenger cars until the 1990s. The indirect injection (IDI), or pre-chamber design suited passenger cars best. Even now, IDI engines are still used in some European cars and light CVs.
Anyone who has travelled in an older diesel car will know that one of its principal drawbacks is noise. Because the fuel literally explodes on contact with the hot air in the engine, the force of that explosion gives rise to the traditional diesel rattle. Without the sophisticated electronic control systems used in modern diesels, the best way to control that explosion was to inject the fuel into a small chamber in the cylinder head, known as the pre-chamber, connected to the main combustion chamber directly over the piston. Combustion would spread rapidly into the main combustion chamber where the explosive force would act on the piston and force it down. The price of this more controlled combustion was lower efficiency, but this didn’t matter because indirect injection (IDI) diesels still had a significant efficiency advantage over petrol engines.
The involvement of Ricardo Consulting Engineers with Citroen for the 1935 Rosalie is also an important factor in the history of diesel development. It was Sir Harry Ricardo who devised the most efficient design of the IDI cylinder head, patented as the Ricardo Comet in 1931. Because it was such an effective design, practically all diesel car engine manufacturers used the Ricardo design for their engines, throughout the life of the IDI diesel engine, earning Ricardo royalty payments to this day. Ricardo has remained a significant force in diesel engine design ever since.
Efficiency could be further improved by injecting the fuel directly into the main combustion chamber and eliminating the pre-chamber. But before the introduction of control electronics, this type of engine was not best suited to cars. Fiat introduced the first direct-injection (DI) car engine in the Croma in 1988. The drawback to DI engines was greater combustion noise than IDI diesels. While they used up to 15% less fuel than indirect injection engines, the staccato metallic sound that combustion produces was not guaranteed to have potential buyers queuing at their dealers. It is one reason why premium brands such as Mercedes-Benz and BMW were late adopters of DI engines. Diesels needed to be smarter if they were to be taken seriously.
Electronic control systems had already appeared on some 1990s engines, notably the 1.9 litre TDI engine first used by Audi, then subsequently by other Volkswagen Group models. Such systems meant that injection timing could be tightly controlled as required. Smarter diesels would also need higher injection pressures to burn the fuel more efficiently. In simple terms, the higher the fuel pressure, the better the fuel mixes with the air, completely burning more of the injected fuel in the process. That means not only more efficiency, but also cleaner emissions. Engineers devised four ways to pump up the pressures and while two of these have fallen out of favour, principals from both are either currently in use or are likely to be seen on future engines.
The method favoured by most fuel injection suppliers is known as common rail. The very first common rail system was patented by Vickers as long ago as 1913, but that system differs significantly from modern systems. The system gets its name from the thick tube or rail, which holds the small quantity of pressurized fuel. The rail is also the common supply to all injectors, linked by short metal pipes. Since the fuel is pressurised at anything up to 1,800 bar (some 26,000psi) in current common rail systems, although 1,600 bar (23,000psi) is more typical today, roughly equivalent to water pressure on the seabed 12 miles below sea level, sealing common rail systems is critical.
This inevitably means that manufacturing tolerances are equally critical and therefore expensive. The same is true of the injectors themselves, whose feed pipes inside the injector are around the thickness of a human hair. The manufacture and assembly of modern fuel injection systems takes place under clean room conditions.
The common rail operating principal is fairly simple. A high-pressure pump produces and maintains the pressure on the fuel in the rail. An electronic control unit (ECU) then controls the opening and closing of the injectors, delivering a precisely metered quantity of fuel in the process. The principal advantage of common rail is that fuel pressure is independent of engine speed, which will become more critical as emissions regulations tighten and take more account of start-up emissions, traditionally an engine’s dirtiest emissions point. The other advantage is that the common pressurised fuel supply lends itself readily to “pilot” and “post” injection sequences. These are also important for emissions reasons. Pilot injection is the principal means of controlling diesel combustion noise and the reason why modern diesels have become so much quieter. By injecting a tiny amount of fuel before the main injection pulse, combustion can begin more slowly, producing smoother combustion, with lower noise and pressure levels inside the engine. Some current injection systems provide two pilot injection pulses. Post injection pulses will also become more important as emissions legislation tightens. We will discuss that further when considering future diesel technology.
Common rail has been the most widely adopted modern diesel fuel injection system, now favoured by all motor manufacturers, except the Volkswagen Group. In its place, VW has adopted electronic unit or pump injectors (EUI). In this case, fuel is fed at low pressure to a pump and injector combined in a single unit in the cylinder head. The pump is driven off the camshaft and the injector controlled electronically by the engine ECU. This means that compared with common rail, the pump has to pressurize a very small quantity of fuel, barely a millilitre. The principal advantage is that using a steeply profiled cam; the plunger type pump can provide far higher injection pressures, currently up to 2,050 bar (almost 30,000 psi). Pilot injection can be provided with the system, but fuel pressure is relative to engine speed – the lower the engine speed, the lower the pressures produced.
Although modern EUI systems have become smaller, they must take up space within the cylinder head, which means that the cylinder head must be designed to accommodate them. By comparison, common rail systems are largely external, with only the injectors and supply piping taking up space in the cylinder head. This has made it easier for engine manufacturers to adapt existing DI engines to common rail and is another reason for the relative popularity of common rail.
Ricardo highlights new markets for diesels
With the potential for specific powers of 80-100kw/litre in the near future, Ricardo predicts a growth market for sports performance diesel products as well as developing long-term demand for diesel vehicles in the USA and approaching market dominance in Europe With the rapid development of diesel technology the 2004 Ricardo diesel report indicates that the specific power of automotive diesels is set to grow and hence open up an entirely new market segment. According to Ian Penny, Ricardo director of diesel engines, “Despite the fast approaching introduction of the Euro IV emissions limits, the upper limits of specific power output of new diesels are set to increase further over the next few years. With 60kW/litre already in production we believe that the latest developments in diesel technology will ultimately enable peak ratings of 80-100kW/litre. This is likely to lead to a rapid growth in the sports diesel market which is currently in its infancy.” In the United States the report predicts that while a number of new diesel models have been introduced in 2004, the introduction of the California LEVII emissions standards will mean that diesel sales volumes remain flat at least until low sulphur fuel is introduced in 2006. Beyond 2006 further new product introductions are considered likely and with diesel acceptance growing particularly in the light truck sector, Ricardo predict a diesel market penetration in the region of 6 per cent by the end of the decade. In contrast to the US, the report indicates a rapidly developing diesel market share in Western Europe with demand at record levels in all countries and all major automakers increasing their diesel to gasoline sales ratio. In particular, French automakers PSA Peugeot Citroën and Renault have now joined their German counterparts VAG and DaimlerChrysler in selling more diesel than gasoline powered cars in the region. Against an overall fall of 1.3 per cent in the total market for new vehicles, consumers increasingly showed their preference for diesel cars with an increase in sales of 6.5 per cent to a total of 6.3 million. This is nearly double the sales volume of 5 years ago and represents a total of 44 per cent of the total new car market. The country by country picture is more varied with France, the largest market for diesels in Western Europe, posting diesel sales at the previous year’s record level, but against a substantial fall in demand for gasoline vehicles. As a result the demand for diesel cars in France is now double that for gasoline vehicles. |
|