The main pressures on vehicle designers and engineers continue to be safety and exhaust emissions, together with fuel economy (except in North America). However, intense competition, especially towards the top of the market, means that comfort and sheer ease of driving are also important considerations. They can make the difference between winning and losing the customer. Consequently, a great deal of engineering effort has lately been devoted to the chassis – in its modern sense of suspension, brakes and steering – in a search for unparalleled levels of ride comfort & quietness, control and dynamic safety. Jeff Daniels reports, in this extract from an exclusive just-auto research report.
Historical
In the early days of vehicle design and manufacture, the chassis was the frame above which the body was mounted, and below which the axles were mounted by means of their springs, together with any associated steering and braking systems.
During the 1920s, pioneers including Budd in the USA and Lancia in Europe began to study the implications of eliminating the chassis frame, attaching the wheels – whether mounted on axles or independently – directly to the body. It quickly emerged that to achieve similar orders of stiffness in bending and (especially) in torsion, a load carrying body could be made lighter and more compact than an unstressed body mounted on a chassis frame. By the 1950s the stress-carrying “unitary” body had become the industry standard. The terms “chassis” had not disappeared, but had rather been transferred to those systems between the body and the road surface – the suspension linkages, springs and dampers, and the wheels themselves – together with the closely associated steering and braking systems essential for control of the vehicle.
Some observers regard chassis systems and suspension systems as synonymous, but this disregards the interdependence of suspension, steering and braking systems and the fact that they are integrated to an increasing degree, especially at the electronic level. It may also be argued that even in the early days of motoring when complete chassis were delivered to coachbuilders for body installation, the steering and the brakes (such as they were) were already installed.
Current scope
In present-day terms, therefore, the terms “chassis engineering” or “chassis systems” embrace a hierarchy of technologies and features that may be outlined as follows:
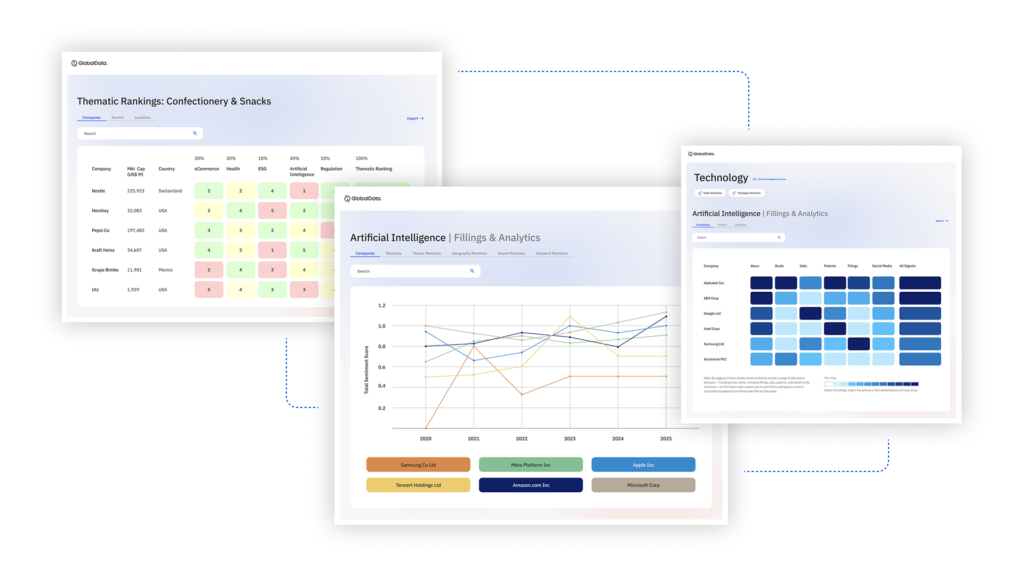
US Tariffs are shifting - will you react or anticipate?
Don’t let policy changes catch you off guard. Stay proactive with real-time data and expert analysis.
By GlobalData- Suspension: embracing the choice of basic geometry for optimum wheel location, the mounting of suspension members to the body (including the use of sub-frames), the springing medium and the provision of damping of vertical wheel movement.
- Steering: the optimisation of front suspension geometry for steering, the choice of steering system, the provision of power assistance, the satisfaction of safety requirements, and the provision of “augmented stability” through interaction with the braking system.
- Braking: the choice of friction system, the design of the operating linkage, the provision of servo assistance, the satisfaction of safety requirements, the provision of anti-lock braking and other enhancements such as emergency brake assist.
- Wheels and tyres: choice of wheel and tyre size, choice of wheel material and tyre configuration, choice of spare wheel configuration or “run flat” technology.
Other engineering constraints
As noted in the outline above, chassis engineering is subject to many legislated safety requirements with profound engineering implications. Two examples are provided by the requirement (in almost all markets) to “split” the braking system in such a way that a single failure will not compromise safety, and the requirement that all steering systems (except in specialised vehicles with a low maximum speed) should consist entirely of mechanical linkages. In this latter respect, revised legislation will be needed, certainly within the EU, if “steer by wire” is ever to be acceptable.
While the main engineering considerations in the area of chassis systems are as outlined above, design is also subject to the “universal” constraints of cost and weight. Reducing chassis engineering cost is especially difficult in the light of consumer demands for ever better refinement and ride comfort, and for higher vehicle performance (placing greater demands on the quality of steering, handling and roadholding). Electronic systems today play an increasing role in chassis systems, and this trend will continue into the foreseeable future. Most electronic systems add new capabilities, but also cost.
The saving of weight in chassis system components, as discussed later, has more value than merely reducing the vehicle’s mass and therefore improving its performance. Reducing the weight of wheels, tyres, suspension components and most brake system components also reduces the unsprung mass – the total mass of all components between the road surface and the springs – and this improves both ride comfort and roadholding. Therefore much work has been done on reducing the weight of both suspension and brake system components, although to some extent these efforts have been negated by the recent tendency to fit ever larger and wider (and therefore heavier) wheels and tyres.
Significance to vehicle
Chassis systems determine many of the fundamentals of vehicle behaviour and “character”, in particular ride comfort and (to a considerable degree) noise levels on one hand, and the quality of steering, handling and roadholding on the other. These are not, by and large, the qualities that influence the decision to buy, which (leaving aside questions of manufacturer reputation) is largely dependent on external appearance, visible features and price. They are, however, aspects that (together with reliability) play a large part in determining customer satisfaction during vehicle operation – which may in turn influence the decision for or against a repeat purchase.
Especially in recent years, chassis engineering has provided one of the most effective means of determining the “character” of a vehicle. It has been shown that measures as simple as stiffening the suspension mounting bushes can significantly alter the subjective impression of steering response and handling, for example. This provides an easy and cost-effective means of differentiating between versions of a single model to match a range of customer expectations.
In the medium term, the increasing use of electronic systems in chassis engineering may provide an even easier means of adjustment.
Manufacturing and supply considerations
There is a clear division in chassis engineering between suspension, for which the VM usually retains total design and development responsibility, and steering and brakes, for which a significant degree of responsibility is passed to Tier-One suppliers.
Components for the suspension – mountings, arms and links, springs and dampers – are either made in-house (sometimes in specialised facilities) or more often, bought from highly specialised Tier-Two suppliers. This is especially so in the case of springs and dampers – although it is worth noting that Peugeot, which regards damper quality as crucial to chassis quality as a whole, still makes its own dampers in a special section of its Sochaux works.
Steering and braking systems, by contrast, are more often engineered by specialist suppliers working in close collaboration with the VMs. Many of these specialists, for example Akebono, Bosch, Delphi, Teves, Valeo and ZF, are extremely large operations in their own right (with interests extending well beyond chassis engineering), have a wide range of VM customers, and have helped to pioneer the adoption of modern technologies, from ABS to electric power steering to ESP.
The size of the market for OEM chassis systems may be gauged from the fact that 50 million light duty vehicles are manufactured, worldwide, every year. In chassis engineering terms that is 200 million “corners” since there has been a tendency, ever since independent suspension became well-nigh universal, to regard each wheel as being linked to is own chassis system (linkage, spring, damper, brake, and – at the front of the vehicle – steering). A modern trend is for “corners” (less wheels) to be supplied by Tier-One operations as complete sub-assemblies.
As the volume manufacture of light-duty vehicles has spread beyond the three main industrial areas, so these Tier-One suppliers have tended to expand their own operations, or to licence their technology, to extend their coverage to match. It is difficult to see how any new operation could now be created in serious competition with these existing and very powerful players. The Tier-Two operations associated with suspension parts, including springs and to some extent dampers are another matter altogether. Although this tier has seen some amalgamation in recent years, myriad small suppliers still exist and new ones are being created (or existing companies are adapting their product ranges) to satisfy demand in the emerging vehicle manufacturing areas.
|