Times have truly changed since Henry Ford offered his Model T in 1914. DuPont pioneered the first fast-drying lacquer paint in 1923, giving consumers their first colour options beyond black for mass-produced vehicles. Paint manufacturers, such as BASF Coatings and DuPont, now offer some 150 new colour shades each year. Today, the vehicle exterior is a vitally important element in the brand differentiation of vehicle makers and a kind of business card for its owner.
Although people spend huge sums of money on their cars, wanting to see and be seen from inside them, their choice of colour for the bodywork is still conservative. Subdued colours appear to be the order of the day across the globe. Shades of silver, grey and blue are the preferred choice, worldwide.
Defining the market
There are basically three markets for automotive coatings:
- Coatings applied to vehicle bodies;
- Coatings used on automotive plastic components; and
- Coatings for aftermarket applications.
Coatings applied to vehicle bodies
After pre-treatment of the vehicle body to remove grease, oils and dust, four generic types of finish are typically applied, i.e. electrocoat, primer-surfacer, basecoat (or colourcoat) and clearcoat. This process is unlikely to change, as an auto executive told us: “The layering structure will remain the same but the key is finding ways of delivering it with less waste.”
Electrocoat provides corrosion protection. Electrocoating is performed by dipping the vehicle body into a tank filled with electrically conductive electrocoat solution, which then coats the internal and external surface of the vehicle body by electrodeposition.
How well do you really know your competitors?
Access the most comprehensive Company Profiles on the market, powered by GlobalData. Save hours of research. Gain competitive edge.
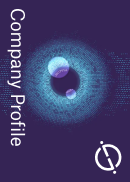
Thank you!
Your download email will arrive shortly
Not ready to buy yet? Download a free sample
We are confident about the unique quality of our Company Profiles. However, we want you to make the most beneficial decision for your business, so we offer a free sample that you can download by submitting the below form
By GlobalDataThe next layer is the primer-surfacer, a polyester film that ensures a smooth layer on which to apply subsequent coatings. It provides chip resistance and gives additional rust protection.
The basecoat and subsequently the clearcoat are the visible layers of the automotive coatings. Basecoat adds colour and, in case of metallic colours, a metallic finish. Basecoat may contain acrylic and/or polyester-based resin and may be either solvent- or water-based. Toyota reports that about 70% of its vehicle line-up features metallic finishes.
Clearcoat protects the basecoat, provides a glossy finish and acts as the outward protection for the paintwork. It protects the vehicle body from ultraviolet light, chemical attack such as acid rain, abrasion and damage such as that caused by stone chips. In some applications, mainly to create plain colours such as white and black, a single finish, referred to as monocoat performs the functions of basecoat and clearcoat.
All of the above coating products are produced by using the same four principal ingredients, i.e. resins, pigments, solvents and additives. In essence, the different ingredients are mixed, the result is quality tested and then filled into containers. The properties of the various coating products are determined by the chemical composition and characteristics used in the production process.
The European coatings market is characterised by the replacement of conventional solvent-based paints with waterborne systems. The European VOC (volatile organic compound) legislation triggered this migration path, as the directive is now being implemented in all national laws in Western Europe. By 2007, all body shops must use water-based products. It is estimated that waterborne basecoats account for just 23% of the total Western European basecoat market. BASF claims leadership with a 30% share of that market.
Coatings used on automotive plastic components
Coatings for plastics are produced using the same basic manufacturing processes that are used for other automotive coating products. There are, however, certain differences between products used to coat plastic components and those supplied for coating vehicle bodies. In particular, a coating product such as electrocoat is not used to coat plastic components.
Plastic components, furthermore, often cannot withstand the high temperatures used in coating vehicle bodies so the finishes must be formulated accordingly. Plastics may require special properties. Coatings used to coat non-rigid plastics must withstand flexing and they must be specifically formulated to adhere to different types of plastic.
Some argue that this market should be divided into coatings for interior and exterior plastic components. It is further estimated that, on average, 2 kg of finish are needed to coat the internal plastic components of a vehicle, and 3.2 kg to coat the external plastic components.
Coatings for aftermarket applications
Automotive finishes are used mainly for repainting used cars and repairing accident damage. The principal aftermarket customers are independent bodyshops (accounting for 55% of aftermarket sales to motorists) and vehicle maker franchisees. Coating products supplied for the OE and aftermarket constitute different relevant product markets. Six principal products are supplied to the aftermarket: primer, basecoat, clearcoat, thinners, activators and putty. Primer, basecoat and clearcoat perform the same basic functions as the products used by the vehicle makers. Thinners are high-volume, low-value solvents used to enhance the fluidity of products for handling and application, and to clean spraying equipment.
Thinners are supplied by a large number of companies, including firms who are not active in the supply of other coating products. Activators are isocyanate-based polymers used in all stages of the aftermarket refinishing process to encourage refinishes to react with the vehicle surface to enhance adhesion and to ensure rapid drying at low temperatures. Putty or stopper is a paste-like material used beneath a primer in order to fill deep dents, scratches or rippling in the car body.
Colour trends
Although people spend huge sums of money on their cars, wanting to see and be seen from inside them, their choice of colour for the bodywork is still conservative. Subdued colours appear to be the order of the day across the globe. Shades of silver, grey and blue are the preferred choice, worldwide.
|
According to researchers at PPG, although a silver medal is often associated with a second place finish, the colour silver was the number one vehicle colour worldwide for the 2002 model year. The annual survey of consumer preferences, conducted by the Global Design & Colour Marketing Team at PPG, found approximately one-third of the vehicles produced in the leading automotive markets – North America, Europe and Japan – were silver. “The technology orientation of consumers in North America, Europe and Japan, as well as the use of silver in home interior, fashion and architectural design, has helped boost the global popularity of silver for vehicles,” said Lorene C. Boettcher, manager, global design and colour marketing for the automotive coatings business unit of PPG. “In addition, silver is a very versatile colour that is attractive across all vehicle lines.”
Consumers’ preference for silver and other neutral shades continues to grow, Boettcher said. They have exceeded white in North America and blue in Europe, and matched the perennial popularity of white in Japan for the 2002 model year. Advances in coatings technology have also helped to drive silver’s popularity ?by generating a wide spectrum of special effects and appearances.
“Silver can highlight the hard edges and soft lines of a vehicle’s design and can take on several different effects – from very bright and reflective to subtle and sophisticated – based on the size and type of metallic flakes contained in the coating,” said Jerry R. Koenigsmark, manager of colour design, North America for the automotive coatings business unit of PPG.
“Globally, for the 2002 model year, we saw very bright silver shades, which are often more appropriate for hard-edge, modern or high-tech vehicle designs.”
Based on data compiled by PPG, the most popular vehicle colours for the 2002 model year for the three leading automotive markets were:
Figure 1 Vehicle colour popularity in Europe |
![]() |
Figure 2 Vehicle colour popularity in North America |
![]() |
Figure 3 Vehicle colour popularity in Japan |
![]() |