One of the themes that dominates
conversations in the car industry at present is that of lightweighting. There has been
growing concern over the weight increase of each new model over its predecessor, while the
proliferation of comfort and safety items as well as emissions control systems have added
yet more weight. However, the new and lighter vehicle structures and complex new
manufacturing systems required to reverse this trend may prove too costly an upheaval for
the low-margin automobile industry to contemplate.
In simple terms, weight increase means an
increase in fuel consumption and this in turn means an increase in carbon dioxide
emissions. It is the expected clampdown in the CO2 area that is now driving the
weight reduction agenda. However, this concern should really be considered within the
wider context of the future of the industry over the next few decades.
Two major factors will determine
developments in the car industry in the early decades of the 21st century:
- how to overcome the chronic lack of
profitability in volume car making; - how to cope with the increasing
environmental pressures on the industry, especially mandated reductions in CO2
emissions.
On the face of it, these two factors seem
obvious drivers. However, few observers appear to have acknowledged that these
developments have the potential of fundamentally changing the car industry – for
ever.
Lack of profitability
Despite impressive headline profit figures,
once the costs of car making are taken into account the industry survives on very thin
margins. Apparently healthy returns made in the good years have to sustain a growing
product development budget and help the company survive through the lean years that
inevitably follow. Operating margins of more than 3% are a distant dream for many
manufacturers. Even at the distribution end, dealer margins – if they exist at all
– rarely exceed 3%, with 1%a more typical figure. The economics of the industry are
such that even a relatively small decline in demand can take the production system below
its breakeven point and operating losses result almost immediately.
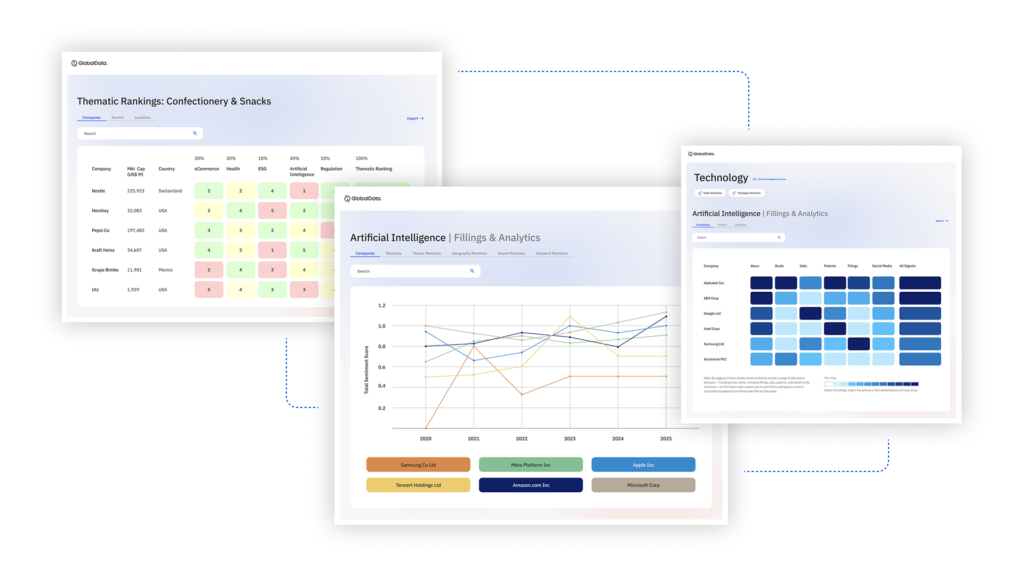
US Tariffs are shifting - will you react or anticipate?
Don’t let policy changes catch you off guard. Stay proactive with real-time data and expert analysis.
By GlobalDataThe common response by the industry is to
keep feeding the production system and then to force the products into the market at a
discount. The idea that the car industry is market-driven is still a large fallacy.
Simply, the demands of the market and those of the car production system are difficult to
reconcile.
The reason for this tension between
production and market lies in the technology used for mass car production. The all-steel
welded body that forms the core of the modern car was first developed by E G Budd in the
US between 1910 and 1920, and led to the development of the structural monocoque or
unibody from the 1930s onward. It requires very high initial investments in press
technology, including tooling, body build and paint plants, but once installed allows cars
to be made in high volumes at relatively low unit cost.
Although Ford believed that his Model T
would fulfil all automotive needs for ever, other manufacturers soon realised that the
market was made up of subdivisions with different requirements. This market segmentation
created a level of differentiation that clashed with the standardisation favoured by
Budd-style body-making. Although in the 1950s and 1960s demand still outstripped supply,
allowing manufacturers to put their production requirements first, since the 1970s market
demands for differentiation have increased, which left many car makers with a
proliferation of model platforms.
Market demand for visible differentiation
is expected to increase further. This will lead to more variants and lower volumes of each
variant being produced, which in turn jeopardises the return per model. The cost of
tooling alone per model can amount to £60m-£100m, and it is already the case that many
if not most models in a volume car maker’s range are not contributing to profits. In
fact, recent data for the high volume US car producers suggest that even here money is
only made on light trucks (see Table 1) and upmarket saloons. European and Japanese volume
car producers only make money on their high volume products, while the specialists too
cross-subsidise much of their ranges. The smallest of the volume specialists, Saab, has
consistently been unable to make a profit on volumes of around 80,000-100,000 a year.
The current trend shows low profitability
with declining per-model volumes and rising product development costs. It is clear that
the industry is facing problems, particularly in Europe where relatively small firms are
trying to sustain relatively diversified high quality product ranges. Some of the
specialists are able to practice a cost recovery strategy through premium pricing which
the customer accepts in return for a prestige badge. However, the scope for this is
limited and cannot be used by volume producers. The current strategy for escaping from the
downward spiral centres around a number of approaches:
- globalisation to increase per-model volumes
and recapture economies of scale; - reducing the number of platforms in order to
reduce cost and complexity; - ’leaning’ the industry by reducing
wastage of all types in the existing Budd system.
Table 1: US Big Three profit contribution vs volume contribution, 1996/97 average (%) |
||
Segment | Volume contribution | Profit Contribution |
Small | 13 | -20 |
Lower middle | 16 | -8 |
Upper middle | 16 | 0 |
Sporty | 0.3 | 0 |
Luxury | 7 | 7 |
Van | 10 | 20 |
Pickup | 19 | 40 |
SUV | 15 | 60 |
(Source: adapted from J D Power and Associates) |
Environmental pressure
The other major pressure identified is
environmental. This takes many forms. Clearly each new wave of emissions legislation
constitutes a cost to the manufacturers which can only in part be passed on to the
customer who did not necessarily demand it in the first place. This is one of the reasons
for the rising cost of product development. In addition, social and political pressures
are beginning to affect the whole auto mobility paradigm, making car use increasingly
onerous for many average motorists. This too is likely to grow.
However, possibly the greatest threat comes
from the prospect of a so-called carbon tax, a system for penalising or taxing cars on the
basis of their emissions of carbon dioxide. After the Rio conference of 1992, the European
Commission committed itself to the introduction of such a tax. From the start, the car and
oil industries have been lobbying against it. The recent Kyoto conference came up with
some more binding commitments and the EC and the industry through its trade body ACEA are
currently engaged in a negotiating process with the aim of coming up with a set of
proposals that both sides can live with.
A number of car makers have already
announced a commitment to a unilateral reduction in CO2 output from
their cars. Volvo for example will reduce the CO2 output from its new cars by
25% between now and 2005, while the German car makers have made a similar commitment.
Apart from further improvements in engine combustion efficiency, the technical focus will
be on weight reduction. The average weight of European cars has grown dramatically over
the past 30 years or so and some manufacturers – recognising the problem– have
already started to curb this development in their own ranges. This thinking has led to
products such as the all-aluminium Audi A8. A further impetus has come from the German
‘3-litre car’ programme whereby all local car makers are aiming to introduce a
car with a fuel consumption of no more than 3 litres/100km in the next few years.
Lightweighting has already become a major
driver in the industry – at least in Europe. Developments in steel body construction
under the Ultra-Light Steel Auto Body (ULSAB) programme suggest that current steel
technology can accommodate a reduction in body weight of around 25%. If a greater
reduction is needed – which seems likely as the body only represents around 20%of
vehicle weight – then alternative materials and alternative methods of making cars
may well have to be contemplated. In fact, to move towards a more sustainable product and
industry it may well be necessary to adopt some of the ‘Hypercar’ ideas promoted
by Amory Lovins of the Rocky Mountain Institute in the US. It is quite possible that the
European Parliament may wish to drive the industry in this direction. If this happened,
the current way of making cars would eventually become unsustainable.
It is not always appreciated that cars can
be made in a number of different ways. Many small low volume specialist car makers and
kit-car producers do not use the Budd method. This includes such famous names as Lotus,
TVR, Morgan and Ferrari. As a result these firms have breakeven points an order of
magnitude lower than volume producers. The UK-based specialist sports car makers TVR and
Morgan are profitable on volumes of less than 1,000 per year. In fact, alternative body
technologies have also been adopted by volume producers for some of their lower volume
niche products (see Table 2).
Table 2: Examples of alternative body technology in volume makers’ niche products |
|||
Manufacturer/ Badge |
Model | Introduction Year | Features |
Matra/Renault | Espace | 1984 | Plastic over steel |
Pontiac | Fiero | 1984 | Plastic over steel |
Saturn | All models | 1990 | Plastic outer panels |
Audi | A8 | 1994 | All aluminium |
Renault | Sports Spyder | 1994 | Plastic over aluminium chassis |
Plymouth | Prowler | 1997 | Aluminium |
MCC | Smart | 1998 | Plastic with steel frame |
Fiat | Multipla | 1998 | Steel spaceframe |
Further products will follow; however, the
extent to which such alternatives will penetrate mainstream vehicles and the speed of
their introduction will depend crucially on the final outcome of the energy tax
requirements.
In the long term a dramatic change is
clearly on the cards. Even on the most optimistic estimates oil reserves will run out in
40-50 years. By around 2020 a significant amount of oil would come from areas where it is
more expensive to extract and oil prices would start rising. However some form of
motorised transport is likely to remain. It all depends on how we define ‘a
car’. The current offerings are heavy, using only a fraction of their energy input to
move the occupants. Both the dwindling oil reserves and the – generally less energy-
dense – alternatives require the development of considerably lighter vehicles. In
addition, the high car density and the resulting congestion in many locations, as well as
the increasing longevity of cars, means a reduction in overall car production is needed in
order to move towards sustainability.
Steel is unlikely to be able to accommodate
this degree of lightweighting, at least not in its present form. ULSAB’s
solution is not nearly radical enough, while aluminium is not the answer either, at best
it can be considered as ‘lightweight steel’. As we argue in our book, The Death
of Motoring? Car Making and Automobility in the 21st Century*, plastic and composite
materials are the only route to the level of weight reduction that is required in order to
make the automobility paradigm anywhere near sustainable – it is better to use oil in
this way rather than burn it. However, this would require a wholesale abandoning of the
existing car production system at enormous cost both economic and in terms of jobs.
The change is inevitable and it is time we
started planning for it now. This way a gradual and relatively soft transition can be
engineered. If we postpone the inevitable, a much greater crisis will result. Several
manufacturers are taking the threat seriously and the fact that alternative-bodied niche
products start to appear at the margins of their product ranges reflect their thinking.
The transition from mass-market production-led cars to small-scale market-pulled products
will affect suppliers, dealers and many other elements of the automotive supply chain.
Traditional players will clearly resist the change which could see a shift from an
industry dominated by large monolithic corporations to one consisting of groupings of
smaller product development, design, marketing and possibly assembly outfits, which source
their generic powertrain items from large, highly automated and low-cost central
suppliers.
Alternative products could take many
different forms. Lovins favours the carbon fibre monocoque. However, some form of modular
construction would give greater flexibility and adaptability to fashion and markets as
well as new technologies. A steel or aluminium spaceframe with thermoplastic or composite
cladding would appear to provide such a solution. It is significant that the MCC Smart
follows this approach – could this be the car of the future?
Paul Nieuwenhuis and Peter Wells
The Centre for Automotive Industry
Research,Cardiff Business School
* Nieuwenhuis, P, and Wells, P: The Death
of Motoring – Car Making and Automobility in the 21st Century, John Wiley, 1997.