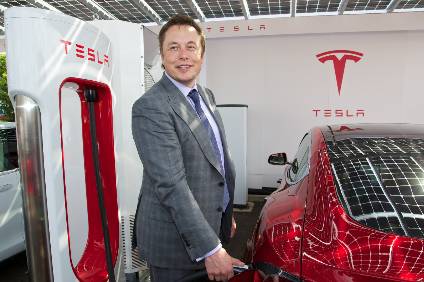
Tesla’s CEO, Elon Musk recently sat down with auto engineer Sandy Munro to take a deep dive into some of the tech secrets that will underpin Tesla’s range over the next few years. The discussion ranged from the ‘hell’ of moving to full-scale production, to material science breakthroughs, to streamlining both hardware and software through each new vehicle iteration. This briefing will look at critical revelations from the discussion to get an idea of what Teslas of the future will look like.
Paint quality improvement
While Tesla is rightly praised for the quality of its electric-vehicle-specific components, criticism has occasionally been levelled at the company for the quality of its core automotive product. One such area of concern was the quality of the paint applied to new vehicles, with some users highlighting minor visual imperfections such as rippling or ‘orange peel’ but others reporting serious issues including paint wearing away around wheelarches.
In response to these criticisms, Musk acknowledged the difficulty in achieving a high-quality, flawless paint finish on a production line. While stating that paint problems with specific vehicles could be caused by a number of factors, Musk noted that the race to ramp up production had affected the paint process – “one of the things that was happening…the paint wasn’t necessarily drying enough…[before we ramped up] the paint had an extra minute or two to dry, now it doesn’t have that so it became more prone to issues”. He stated the automaker had made improvements to the paint process throughout December 2020 to address this issue.
FSD rollout
Talking about his experience with a recent Model 3 equipped with Tesla’s Autopilot semi-autonomous driving system, Munro described a close call in which the car attempted to take a decommissioned highway off-ramp after seemingly becoming confused by incorrect road markings and a temporary traffic management system.
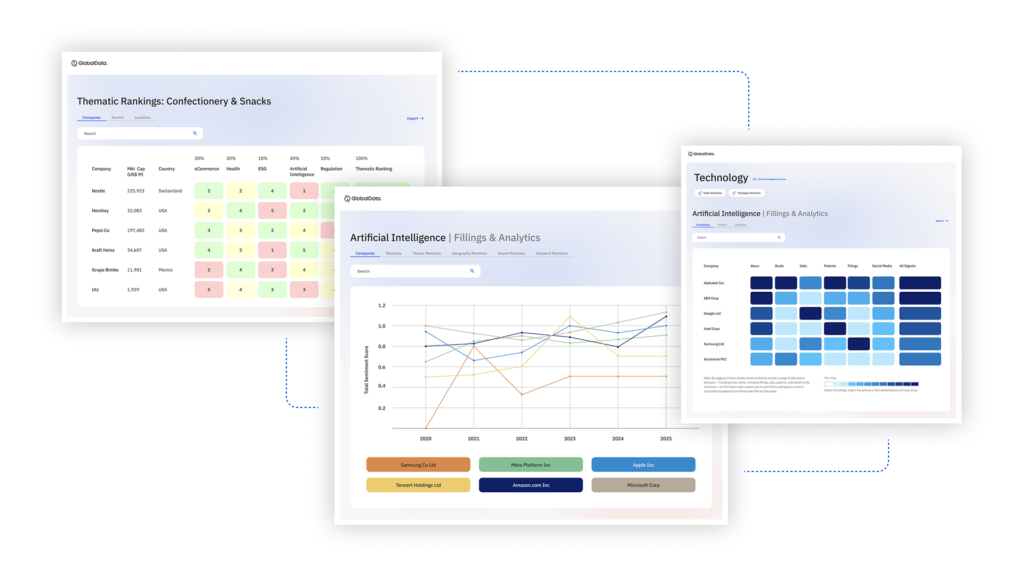
US Tariffs are shifting - will you react or anticipate?
Don’t let policy changes catch you off guard. Stay proactive with real-time data and expert analysis.
By GlobalDataWhile Munro questioned whether legislation would be required to ensure roads are prepared in such a way as to work within the parameters of Autopilot, Musk suggested that Tesla’s system needed to be sophisticated enough to be able to respond well to these unpredictable edge cases. He noted that “for self-driving, even if the road is painted completely wrong and a UFO lands in the middle of the road, the car still cannot crash, it still needs to do the right thing…it can’t be dependent on road markings…even if someone tries to trick the car”. Musk points to Tesla’s decision to design both the hardware and software in its vehicles as a key factor in its ability to tackle the rollout of self-driving features.
Lines of code
“I don’t think lines of code is necessarily a metric of goodness.”
The discussion of Tesla’s software strengths led Munro to question roughly how many lines of code were used in Tesla’s vehicles. To this Musk states “I don’t think lines of code is necessarily a metric of goodness…I would consider a large number of lines of code to be bad, not good…I would generally give two points for deleting a line of code and one point for adding one…we haven’t necessarily counted but I would think it’s maybe a few hundred thousand”. Considering many self-driving systems currently in development could well have seven-figures worth of code or more, Tesla’s focus on streamlining its software fits with its wider program of optimising the design of its cars, both in terms of hardware and software.
Wider introduction of mega-castings
Sticking with the theme of optimisation, Musk and Munro also discussed Tesla’s plans for expanding its mega-casting technology across its production lines. Tesla’s mega-casting is a pioneering method of improving both production processes and vehicle quality through the use of very large cast-aluminium parts. So far, Tesla has introduced a rear mega-casting on the Model Y production line in the US, and is preparing to roll out the technology to all its new and existing plants.
In the Model Y, the mega-cast part is a rear subframe that used to be made of many different small parts that would be welded or bonded together in a laborious process that would produce a part with less-than-ideal structural properties. The cast subframe is made in an enormous high-pressure mould and saves weight and complexity by being one single piece – this also reduces the number of production steps needed to produce the part and increases its structural rigidity, while also reducing weight, bringing knock-on performance and efficiency benefits.
Musk explained that the development came about thanks to the development of high-pressure ‘Gigapress’ moulds manufactured for Tesla by Italian company IDRA, but also thanks to Tesla’s work in material science. Musk pointed to the new aluminium alloy the company had developed specifically for the mega-casting process and the fact that it doesn’t need to undergo a heat-treating stage after being cast, cutting both production steps and process time. Musk estimated that the introduction of a rear casting for the Model Y production line could reduce the size of the factory body shop by 30%.
In practice, the new alloy’s material properties make it resistant to the warping that can be exhibited by very large cast parts as they cool, while also providing the kind of strength and resilience needed for crash safety. In addition, the move to a single large cast part reduces issues that arise from bonding different materials together including ensuring tight external sealing and resisting galvanic corrosion.
In terms of prospects for Tesla’s mega-casting technology, Musk said he expected the company to make more use of it but indicated that he was more focused on ramping up production at its new factories in Texas and Berlin. For the Model 3 and Model Y, Musk notes that he foresees future versions with be made up of a large rear casting and a large front casting which will be mated together around a structural battery pack – another critical development.
Introduction of the structural battery pack
As mentioned, the mega-casting technology is intended to work in concert with Tesla’s latest battery pack development – a structural pack. Announced at its Battery Day event at the end of 2020, the structural battery makes use of Tesla’s in-house designed 4680 cylindrical cells as a structural element in the pack construction. Where previously, battery packs would form a protective case for the battery cells, adding weight and complexity, the new pack physically bonds the batteries in place between the top and bottom housings, with the cells’ casings forming a structural part of the pack.
This significantly improves the pack’s strength with the cells acting as a honeycomb internal structure for shear transfer. In addition, the new method of bonding the batteries means less material is needed to protect the cells and resist external twisting forces, reducing weight and complexity, and subsequently improving performance and range. In addition, it draws more of the pack’s weight into the centre of the vehicle, improving its polar moment of inertia and making the car feel more agile and quick to change directions.
End of the road for 12V systems
Another area that Musk highlighted for improvement was the ‘vestigial’ attachment to 12-volt systems in vehicles. He revealed that, for the heavily updated Model S announced at the start of 2021, the company had finally moved to a 12V lithium-ion battery in place of the heavy and bulky lead-acid ones used by the majority of the automotive industry. He noted how the Li-ion cell has greater energy storage capacity and is also lighter, but bemoaned the continued use of 12V systems in modern vehicles where many consumer applications have since adopted higher voltages.
When pressed, Musk was keen on the idea of moving vehicle systems from older 12V standards to the new 48V standards that have emerged in a handful of vehicle applications. Increasing system voltage would allow power-hungry applications such as in-car infotainment or HVAC systems to run well while also significantly reducing the size of wire needed to operate them. A reduction in wire size with a move to 48V systems would reduce vehicle weight, thus improving performance.
EV crossover point
Ultimately, the discussion moved to the question of when EVs would take a dominant position in the new car market, leaving combustion-powered vehicles to edge use cases. Musk gave a ballpark figure of ten years for EVs to account for the majority of new light vehicle sales. This tallies with countries such as the UK that have explicitly stated that they will outlaw the sale of combustion-powered vehicles after 2030.
GlobalData’s forecast data is marginally less optimistic. Taking into account battery-powered electric vehicles along with hybrid-powered models, we expect 46.1% of all new vehicles to be electrified in some form by 2030. If Tesla can ramp up global production quickly while maintaining high levels of interest in its products then this figure could be revised upwards as we approach the end of the decade.
This article first appeared in GlobalData’s Automotive Intelligence Center.