With supercomputers becoming more and
more powerful, the magnitude of the simulations and analyses car manufacturers can perform
to test new model concepts and designs is rising dramatically. The results include reduced
vehicle development times and better optimised solutions, as Anna Kochan reports.
The more powerful a computer, the faster it
solves problems. The car industry has been among the first to take advantage of each new
generation of more powerful computer to arrive on the market. Initially, crash test
simulation was the main application. More recently, as their power has increased,
supercomputers have taken on new roles in simulating fluid dynamics, in and around both
the car and the engine. The growth rate in the use of these techniques has been phenomenal
and new applications are expected to appear in the future.
‘Ford has increased its use of
supercomputer resources by 50% every year for the past 20 years and will maintain this
growth for the foreseeable future,’ comments Dr. Gerhard Zellerman, supervisor for vehicle
CAD systems at Ford in Cologne. Today, 60% of time spent on computer simulation at Ford
relates to safety issues, and the remainder is split between durability and stiffness, and
noise and vibration testing.
By the end of the 1970s, Ford had installed
its first supercomputer and now operates four at its Cologne, Dearborn and Dunton sites as
well as at Jaguar. ‘In the beginning, we introduced a supercomputer because the software
was available to do CAE (computer aided engineering) simulations which could not be
performed any other way,’ adds Dr. Zellerman.
The type of CAE simulation to which Dr.
Zellerman is referring concerns, for example, a crash test. Historically physical crash
testing has been the only way to investigate how a new design behaved during an impact.
Today, due to major progress in computer technology, many crash tests can now be performed
in the virtual world. This is a major advantage to the automotive industry as ever more
stringent safety regulations are imposing greater demands on car companies to test out
different forms of impact. The list of tests now includes front impact, side impact, rear
impact, oblique impact and car-to-car impact.
The software to perform crash simulation
has been available for at least 15 years. The limiting factor has always been computing
power. The volume of computation involved in some CAE simulations is so high that the time
to complete the simulation becomes too long for it to be worthwhile. With a higher power
computer, which is essentially what a supercomputer is, the simulations can become more
complex, more detailed and faster. ‘When the first crash analysis was done in 1986, the
simulation model was very crude because so many assumptions had to be made to keep it
within a manageable size,’ says Kevin Fox, applications analyst at Silicon Graphics. The
models that can be handled today are 60-100 times more detailed, he estimates.
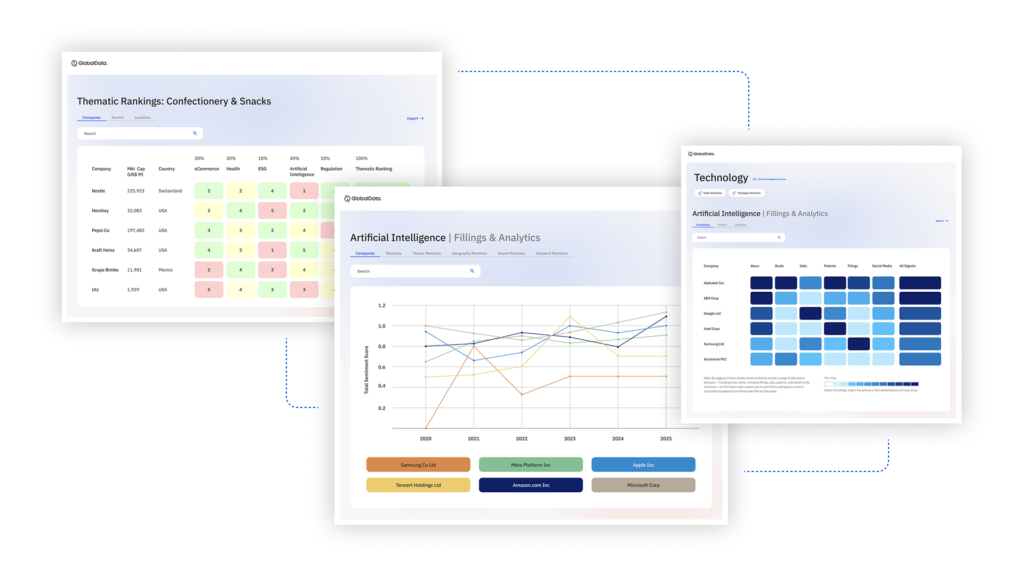
US Tariffs are shifting - will you react or anticipate?
Don’t let policy changes catch you off guard. Stay proactive with real-time data and expert analysis.
By GlobalDataThe supercomputers of today are so powerful
that they can analyse the fluid flow inside an engine compartment whereas previously it
would have been too time consuming to look at anything more complex than a simple duct,’
adds Dr. Anthony Baxendale, head of fluid dynamics engineering and research at the UK’s
Motor Industry Research Association (MIRA) in Nuneaton.
Most large car companies have already
invested in supercomputers. In fact, among the top 500 supercomputers in the world today,
11 are installed at sites belonging to car manufacturers. All except two were supplied by
Silicon Graphics. Top of the automotive league is Toyota, followed by Audi, GM, BMW, Ford
(2) and Nissan, in that order. According to the list, which can be found at
www.top500.org, the remaining four are in Japan at un-named companies.
Over the past five or six years, vehicle
manufacturers have assessed the usefulness of supercomputers in their research on future
techniques departments. It is, however, only recently that they have started to
incorporate supercomputer-based analysis into the vehicle development process because it
is only recently that simulation run-times have become short enough.
‘Car companies want to be able to simulate
very large problems early on in the development cycle, and to do it quickly. The only way
is with supercomputers. If they can simulate a problem accurately and quickly enough, they
can take a lot of cost and risk out of the whole development process,’ MIRA’s Dr.
Baxendale believes.
As a result, the vehicle manufacturers are
now re-engineering their whole development process to give simulation techniques an
integral role, he comments. While most of the large manufacturers are advanced in this
area, Dr. Baxendale says that some have recognised its role in the development process
more than others. He highlights GM and Ford as being among the leaders. ‘GM has just
reviewed how simulation should be integrated into the development process,’ he reports.
Rover is currently carrying out a similar assessment, he adds.
The benefits a vehicle manufacturer can
expect to obtain from the latest computer simulation techniques are varied. It is,
however, difficult to assess whether the ability to crash test cars in a virtual world
actually reduces the need for physical crash tests, which at an estimated $500,000 a
smash, is a very expensive process. Pierre Culière, product manager for design products
at French software company ESI, believes that at least the number of generations of
physical prototypes is falling. ‘In a three-year vehicle development cycle, there is no
time for building prototypes and crashing them throughout,’ he says. However, the average
car company is still crash-testing cars at the rate of at least one a day, he estimates.
Ford’s Dr. Zellerman talks of claims that computer simulation cuts down the number of
physical prototypes by 30% on a vehicle programme compared to the planned number but he is
extremely sceptical about them. ‘You don’t know how they arrive at the planned number,’ he
says.
More important to the car manufacturer is
the benefit the computer simulations bring to design optimisation. ‘We analyse ten times
more different designs than if we did not have computers,’ Dr. Zellerman states. In
addition, the actual task of developing the theoretical model that is going to be
subsequently simulated by computer leads to a better understanding of how the design works
and performs, which is quite an advantage in the long term, he believes.
MIRA’s Dr. Baxendale also suggests that
advanced computer simulation techniques lead to a greater potential for innovation.
‘Before using such techniques, car companies used to evolve new designs from old designs
that they knew worked. It was quite a successful approach but did not allow for
innovation. The market leaders have to do more than just evolve if they are to maintain a
competitive position.’
Simulation can also lead to time savings.
‘Without it, vehicle companies would not achieve the timescales they are currently
targeting,’ adds Culière. For the three supercomputers Mitsubishi has installed in Japan
over the past six years, the major advantages claimed are improved product quality and
faster product development.
While crash testing is the most widespread
application of high level computer simulation today, one of the fastest growing areas is
in the modeling of fluid flow. ‘A very interesting simulation to do is the air flow within
the engine compartment to help develop the cooling system,’ says Dr. Baxendale. Another
application is the simulation of the air and fuel mixing process inside the engine to
improve the combustion process, adds Dr. Kent. These calculations are more complex than
those involved in crash test simulation because they are non-linear and very dynamic. As a
result, they are pushing even today’s supercomputers to their limits.
Ford’s current hot supercomputer topic is
advanced airbag simulation. ‘We have simulated airbag deployment for many years. What is
new is to simulate the interaction of the airbag with its environment,’ says Dr.
Zellerman. The goal of this work is to be able to tune the power of the airbag and the
force of the seat belt restrainers to the size and weight of the passenger, and thereby
minimise injury. Solutions are currently in development.
Also under development are simulation
models for assessing pedestrian impact. This is the subject of new legislation being
introduced and all car companies are having to look at ways of dealing with the issue.
A growing interest in using high level
computers to optimise forging and metal forming processes is reported by Dr Tony Kent,
business development manager (UK) at MSC (MacNeal-Schwendler Corporation). He says that,
until recently, the mathematical technology was not available to simulate the flow of
metals but that the first applications to optimise con rod and crankshaft production
processes are being implemented. ‘These are non-linear, transient dynamic processes which
require the power of a high level computer to model. Car companies are looking to model
the forging process in order to minimise the quantity of material in the initial billet
and also to better master the flow of the material to ensure that it goes to where it is
needed, and only there,’ Dr. Kent explains.
MSC/Superforge, the software package MSC
has recently developed for 3D simulation of forging operations, is currently being
evaluated by a number of major engine manufacturers, Dr. Kent says. By replacing the trial
and error methods traditionally used for process and die design, Superforge is designed to
help manufacturers reduce time to market and increase profitability.
The pressing of body panels is another area
that Ford’s Dr. Zellerman anticipates new developments in computer simulation. ‘It would
be helpful to use computer models to better understand the material flow that takes place
during the pressing of a flat blank into a shaped panel. The benefits would mainly be in
tool design,’ he says.
While Ford continues to develop
supercomputer applications in new and varied areas, Dr. Zellerman is still concerned about
the time that some of the existing applications take to run. ‘Our target is to do
simulations that can be completed within a day. However, many of the noise and vibration
models are complex and may take a whole weekend to run. If it is longer, we cannot use the
application on a production basis,’ he says.
Flow simulation is the application which
most frequently comes up against this time limitation. The applications which suffer are
therefore vehicle aerodynamics, engine cooling and combustion. The solution could be found
by replacing the supercomputer with a workstation clustering system which has been
developed through a European Community Esprit project. Workstation clustering is not yet
mature technology. Software is not yet available for it because of the few number of
users. Dr. Zellerman believes it will take up to another two years to become a practical
viability. Meanwhile, Ford is to investigate what the benefits would be. ‘We have not yet
looked at the cost implications but we are really mostly interested in saving time. If we
could do in a day the type of flow simulations which would otherwise take three or four
days, then it would be worthwhile,’ he concludes.
Meanwhile, high level computer technology
and applications software are also evolving to improve the viability of complex
simulations. ‘Crash simulation techniques still need to become faster,’ says Pierre
Culière. ‘The overnight run-times we can achieve today are quite good. However, this is
still quite long if a company wants to do multiple simulations covering a range of
designs,’ he says. As a result, ESI is developing massively parallel versions of its crash
test software. Last month, the company announced a new parallel version of PAM-CRASH, a
software that ESI claims is already used by 80% of automotive manufacturers worldwide.
With this new version of the software, it will be possible to cut down the simulation
run-time by using more processors. ‘With 16 processors instead of one, the speed of the
simulation can be increased by a factor of more than 12. So, with 100 processors, a really
significant improvement can be achieved,’ Culière expects.
This article was kindly provided by World Automotive Manufacturing, an FT Automotive publication.
World Automotive Manufacturing provides
clear, concise, impartial and up-to-date intelligence on the entire vehicle-making process
every month. With up to 32 pages of highly informed analysis and expertly selected
material in each issue, World Automotive Manufacturing will help you anticipate trends,
improve productivity and reduce costs, saving you hours of researching through less
focused publications.