For many years, power steering technology was focused on hydraulic systems but demand is now favouring electric power steering (EPS) mainly due to fuel consumption and logistical benefits. Matthew Beecham reports.
EPS systems effectively eliminate the traditional hydraulic system’s power steering pump, hoses, hydraulic fluid, and drive belt and pulley on the engine. TRW Automotive believes switching to electric can save vehicle makers US$5-US$10 per car because the units are quicker to install, eliminate complex set-up engineering and have less moving parts.
At a global level, just-auto estimates that about three-quarters of all new passenger cars and light trucks worldwide are equipped with power rack and pinion steering while EPS makes up 15% of the global market. EPS could easily exceed 35% of the global market by 2011.
While EPS has made significant inroads in Europe and Japan, US vehicle makers have been reluctant to replace their proven hydraulic systems with the more costly electric ones because they claim the benefits are largely unnoticeable and the added cost unjustifiable to customers.
“North American OEMs continue to be very, very cost conscious,” said Charlie Cregeur, Product Business Director, Steering Systems, TRW Automotive. “The roll-out of the heavier cars with these technologies is bound to come but it is probably going to be more toward the 2010 or beyond time horizon. We would expect that the behaviour in the North American market to mirror that of Europe where the smaller B and C segment cars get it first and then migrate its way up.”
How well do you really know your competitors?
Access the most comprehensive Company Profiles on the market, powered by GlobalData. Save hours of research. Gain competitive edge.
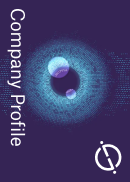
Thank you!
Your download email will arrive shortly
Not ready to buy yet? Download a free sample
We are confident about the unique quality of our Company Profiles. However, we want you to make the most beneficial decision for your business, so we offer a free sample that you can download by submitting the below form
By GlobalDataGenerally speaking, steering manufacturers see electrically assisted steering systems going up the vehicle front axle load/weight, gradually appearing on larger vehicles. TRW’s column drive EPS systems are in production on Renault, Nissan and Fiat models already. “We are in discussions with a number of customers regarding our rack drive technology that will deliver EPS for D segment vehicles,” said Ken Lowe, product manager, steering systems, TRW Automotive. “We are also working to develop enhanced power output for our column drive EPS system for upper C segment models.”
Cregeur added: “If the OEMs have given added functionalities on their B and C segment cars then they can’t really orphan their D or E segment vehicles can they? That is what is going to drive the OEMs to figure out creative ways to get that same functionality in the upper car segments.”
In the meantime, electro-hydraulic steering appears to be sticking around despite the early assumptions that this was a ‘transition technology’ before it went to full electric. Eberhard Kübler, Chief Engineer, Car Steering Systems, ZF Lenksysteme, told us: “It is certainly true that this transition phase lasted longer than we had anticipated five years ago. Back then, everyone in Europe predicted a direct transition from hydraulic to electric steering system with electro hydraulic being seen as a short term solution. We have since seen some OEMs applying second generation systems. Given that this technology works well in some cars, it makes sense to stay with that design for another generation. In the mid to long term, however, I am convinced that the transition will go to fully electric. We also see that new applications of energy saving steering systems go directly to EPS and no longer consider EHPS.”
In pushing back the technical boundaries, Delphi has joined the Active Steering business (started by BMW and ZF Lenksysteme on the new 5-series), and launched its own version of the technology. Delphi’s Active Front Steering (AFS) uses a planetary gearbox like BMW’s that varies the steering ratio from 7:1 to 15:1 depending on the driving situation. Central to the Delphi design has been the elimination of friction and the incorporation of its so-called Magnasteer valve, which provides variable torsional rate in the steering gear using magnetic principles. Specially designed gears have also minimised the amount of friction inherent in the planetary gearbox design. AFS does not require OEMs to upgrade existing hydraulic steering pumps or systems, making it more likely to appeal to customers who have pre-existing hydraulic systems.
Brian Murray, manager of Delphi Corp’s Innovation Centre, said: “We continue to do a great deal of work in rear steering. And there continues to be customer interest in that technology which offers the opportunity to modify the dynamics of the vehicle and provide many of the benefits that you see with the active front steering.”
Delphi’s Active Rear Steering is a low angle rear wheel steering system, specifically designed for the European market. In addition to help balance rise and handling performance, Delphi claims it can be integrated with controlled braking to provide a better solution to stability control than brakes alone. The system basically reduces the vehicle’s turn circle for added manoeuvrability during city driving or parking.
Ashok Chandy, also a manager of Delphi Corp’s Innovation Centre, added: “The two active systems are extremely similar in many ways. But the distinguishing point between front and rear wheel steering is that a rear steer system has a significant impact on vehicle handling.”
“Much of the issue relating to these technologies – in addition to potential cost – is packaging,” added Murray. “Some vehicles will be able to package an active front steering technology better than a rear wheel steering technology and vice versa.”
Meanwhile, Continental AG used the 2005 IAA Frankfurt motor show to launch a new type of four-wheel steering, which it says will significantly aid handling and stability when combined with electronic stability control systems. The design uses a tie-rod at each rear wheel and a multilink rear suspension and has been specially designed to make the technology affordable.
“The main benefit of our system is that we use two independent actuators on each wheel thereby minimising packaging,” said Steffen Linkenbach, manager, New Components, Advanced Engineering, Continental Automotive Systems. “Our system also means there is no need to modify the complete axle unlike competitors’ designs which position a large actuator in the middle of the rear axle requiring a lot of modifications to accommodate it. The net result is that our system allows for the maximum stabilisation of the car. It also allows SUVs and large vehicles to reduce the turning circle by nearly 1-metre. It is possible that our system could enter production by the end of 2009.”
Despite its promise, EPS is really the stepping stone to tomorrow’s full steer-by-wire (SBW) directional control. The theoretical benefits of SBW are compelling. SBW will dispense with all mechanical linkages between the wheel and the steering, freeing-up even more space in the engine compartment. The only quasi-SBW system thus far offered in a production car is BMW’s AFS system, which combines an SBW input with a conventional manual steering input. The system works well but the option cost is high and the proportion of customers specifying it has been low. It was once anticipated that practical SBW, like EPS for large luxury vehicles, would have to await the arrival of 42/36V electrics. Now it seems as though the advent of SBW, which was anticipated by 2008-2010 may be delayed.
What’s the hold-up? Is it to do with considerations of electrical power, legislation, concerns about failure-case safety issues or simply cost?
“All of the above,” said Linkenbach. “The first is the safety because for SBW you don’t have the [mechanical] connection linking the steering wheel and road wheels. That means you need two complete steering systems for only one function. These systems also need 36 or 42 volts to power it, which requires two independent safe board nets. On a cost basis, it is impossible to realise such a steer-by-wire system within the next five to seven years.”
ZF Lenksysteme’s Kübler believes that a real steer-by-wire wire system has at least two issues to solve and therefore will not be introduced in the market within the next ten years. One is the cost of such systems; they are very expensive and will remain so for at least two generations. Second is safety. When you interrupt the steering system and go fully by-wire, the safety requirements are comparable to that of an aeroplane. He said: “From that point of view, I do not really see a broad application of such systems. Another point relates to the fact that normal steering systems are being introduced with more and more features e.g. active steering. Already these additional features more or less resemble a steer-by-wire system.”
Lowe has the last word: “I think people are waiting to see what happens in terms of legislation and public acceptance. In the meantime, there are still some technical issues to be resolved. I believe that, as with a lot of EPS technologies, the Japanese market will be the first indication of what is going to happen with by-wire. Just lately, we have had quite a lot of interest from OEMs on the use of EPHS as part of their hybrid strategy. In fact, they are far more interested in this technology than steer-by-wire.”
Matthew Beecham
|