The automotive industry is facing a revolution in steering technology. For many years, power steering technology was focused on hydraulic systems but demand is now favouring electric power steering mainly due to fuel consumption and logistical benefits. By 2003, Delphi expects that 10% of all passenger cars sold worldwide will have electric power steering.
Koyo Seiko also anticipates exponential growth for electrically assisted steering systems; predicting that electric power steering systems will be fitted to more than 30% of new cars built worldwide in 2005, equivalent to 20 million vehicles. Looking further ahead, TRW forecast that by 2010, 50% of cars produced worldwide will incorporate some form of electrical assistance integrated into the steering system.
The main reasons for strong growth in electric steering, as opposed to hydraulic, are that electric systems are more economical to run, lighter, recyclable and easier to package and install. TRW’s electrically assisted steering (EAS), for example, is a power-assist system that eliminates the connection between the engine and steering system. Its migratory product, EPHS (Electrically Powered Hydraulic Steering) replaces the customary belts and pulleys with a brushless motor that drives a hydraulic power steering pump in a conventional rack and pinion steering system. EPS (Electrically Powered Steering) takes EAS technology a step further, eliminating hydraulic fluid and the accompanying hardware completely. An EPS module includes the motor, torque sensor, electronic control unit (ECU) and control/diagnostic software.
EAS systems are delivered to the vehicle maker’s plant fully assembled, pre-tested and ready to bolt on. In contrast to a traditional hydraulic system, an electric steering system eliminates the need to install the pump, pulley drive and various hoses. There is also no need to fill the system with hydraulic fluid.
Since a variety of components such as pumps, hoses, pipes and brackets are no longer needed; storage and assembly times are reduced. TRW research indicates that, on average, it takes at least seven minutes to fit all of the above on a conventional hydraulic rack and pinion steering assembly system. The assembly time for an EAS system, however, is reduced to just 30 seconds.
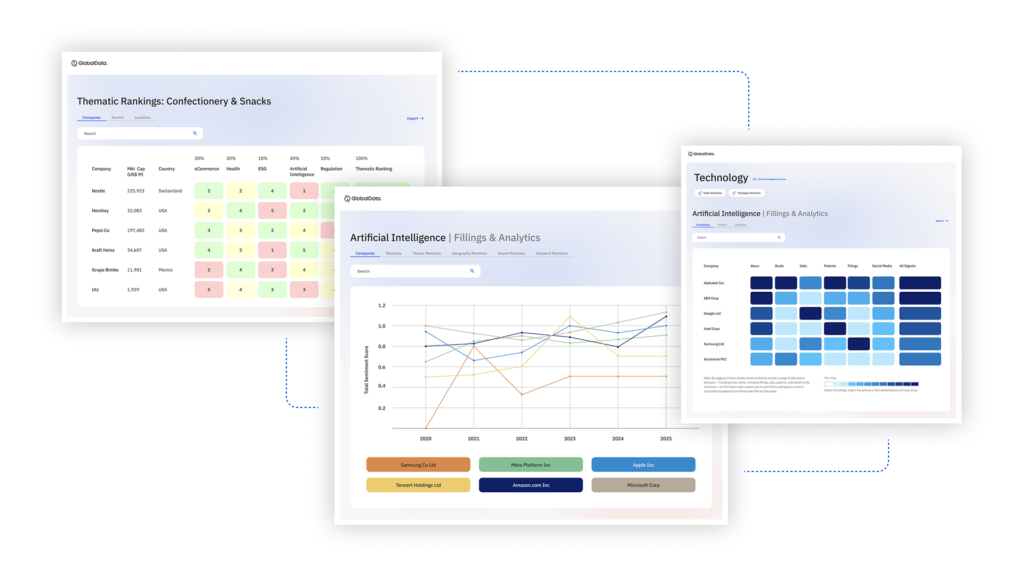
US Tariffs are shifting - will you react or anticipate?
Don’t let policy changes catch you off guard. Stay proactive with real-time data and expert analysis.
By GlobalDataA typical hydraulic system also requires a continuously operating pump run by the engine and uses about 0.3-litres of fuel every 100km.
By eliminating hydraulic fluid, the savings to the vehicle maker are clear. TRW estimate that a vehicle maker will save 50,000 gallons of hydraulic fluid for every 100,000 vehicles produced, equivalent to more than $110,000 annually for the average car line.
The need to develop and fit a different hydraulic pump for every engine type is also eliminated. EAS provides the vehicle maker with a one-size-fits-all advantage, meaning simplified purchasing.
Manufacturers estimate that electrically assisted steering delivers a 3% fuel saving over hydraulic systems. That is the same sort of result vehicle makers’ would achieve by reducing the car’s weight by 50kg. By eliminating the hydraulic pump, the noise level in the cabin is reduced. In addition, given that electric steering systems do not contain fluid or rubber for subsequent disposal, they are 95% recyclable as opposed to hydraulic systems which are 85% recyclable. Another benefit of electric steering over hydraulic relates to its tuneability. It is said to take a week for a vehicle maker to tune the electric system to meet the specific vehicle handling requirements, compared with typically nine months to tune a conventional hydraulic system. Electric steering systems can also be customised to the driver’s personal requirements.
The next development, steer-by-wire, will dispense with all mechanical linkages between the wheel and the steering, freeing up even more space in the engine compartment, allowing greater design flexibility, more selectability for the driver, and (especially for the UK market) easier conversion of cars to right-hand drive.
There are three types of steering system:
- Muscular energy steering systems in which the steering force is produced exclusively by the driver. The steering box itself is either a rack and pinion type or a recirculating-pinion type.
- Power steering systems in which the steering force is produced exclusively by an energy source in the vehicle.
- Power-assisted steering systems in which the steering force is produced by the driver and by an energy source. The energy source consists of a pump (usually driven by the engine), an oil reservoir and corresponding hoses and pipes.
Electrically power-assisted steering systems are headed for the mass-market worldwide, helped by their potential to save manufacturers money, reduce customers’ fuel bills, save designers valuable space, and possibly save lives as well. TRW believes switching to electric can save vehicle makers $5-$10 per car, because the units are quicker to install, eliminate complex set-up engineering and have fewer moving parts. TRW’s EPHS module is fully filled with hydraulic fluid and takes GM about 30 seconds to install and connect the module to the vehicle’s electrical system. Delphi estimates its own system cuts four minutes off the assembly time of a vehicle and reduces component parts stocked from 15 to only two. Delphi also believes that its system can deliver fuel savings of .21 to .41 kilometers per 100km, because it draws less power from the engine. Electric steering could also be safer, as it still works if the engine stalls, unlike hydraulic systems. Electric power steering is already widely used in Japan, and GM was the first US user in 2001 with its Saturn Vue SUV, followed by a high-volume vehicle in 2002.
Four types of EPS
There are basically four types of electric power steering:
- Column-assist type: the power assist unit, controller and torque sensor are attached to the steering column. It can be applied to fixed steering columns, tilt-type steering columns and other types.
- Pinion-assist type: the power assist unit is attached to the steering gear’s pinion shaft. The power assist unit is outside the vehicle’s passenger compartment, allowing assist torque to be significantly increased without causing more interior noise.
- Rack-assist type: the power assist unit is attached to the steering gear rack. Its high reduction gear ratio enables very low inertia.
- Direct-drive type: the steering gear rack and power assist unit form a single unit, enabling low friction and inertia.
Electrically assisted steering systems, such as EPHS or EPS rack-, column-, pinion-, and belt-drive configurations, eliminate the need for the engine to provide mechanical power for the steering system, providing cost and performance benefits. The technologies accommodate the needs of manufacturers as they migrate vehicles from hydraulics, through semi-hydraulics to fully electric systems. EPHS eliminates belts, pulleys and all direct connection with the engine, combining an advanced brushless motor, hydraulic power steering pump, electronic unit and reservoir into an easy-to-install unit. In addition, all electric steering systems offer enhanced fuel efficiency because they consume power only when steering assist is required. Column-drive EPS is a cost-effective design for many vehicle platforms because it locates the EPS motor in the passenger compartment. This arrangement enables lower requirements concerning temperature and sealing in comparison to systems that mount the motor in the engine compartment.
The latest advances in steering systems include BMW’s so-called active steering and VW’s servotronic as well as some interesting developments in four-wheel-steering systems. All the major steering system manufacturers are developing steer-by-wire systems (SBW) for use in cars, though such systems are still not legal in Europe. However, the European Union is expected to allow them by 2004 and systems could be in low-volume production in Europe the year after. Eventually, suppliers hope to completely eliminate the steering column, creating more space and more design possibilities in the vehicle interior.
Active steering from BMW
BMW recently introduced its Active Steering, a new system controlling the position of the front wheels precisely according to the driver’s commands. The system was developed with ZF Lenksysteme.
|
In contrast to the systems developed by other manufacturers working on steer-by-wire systems, BMW’s Active Steering still incorporates a mechanical steering column that permanently connects the steering wheel with the front wheels of the car. The vehicle maker points out that this not only guarantees full maintenance of all steering functions – even if one of the assistance systems is not operating properly or breaks down altogether – but is also the prerequisite for the authentic ‘steering feel’. The system will be introduced in one of BMW’s next model generations.
The core element of its Active Steering system is the steering override function provided by a planetary gearbox integrated into a split steering column. Acting through a self-inhibiting gear wheel, an electric motor intervenes as required in this planetary gearbox, either increasing or taking back the steering angle of the front wheels. A further component is the individually controlled power steering (similar to BMW’s Servotronic) controlling steering forces as required. Interacting with one another, these two components adjust the steering angle of the front wheels and the steering forces on the steering wheel to the respective situation on the road and the driver’s requirements.
Under normal driving conditions, Active Steering varies the steering transmission particularly at low and medium speeds. In critical situations, Active Steering changes the steering angles of the wheels, thus stabilising the car faster than the driver would be able to himself. At higher speeds, the steering transmission ratio becomes increasingly indirect up to the level of a conventional steering system. The level of steering forces increasing at the same time prevents any unwanted movement of the steering.