Although the electric starter motor and alternator has remained virtually unchanged since it was first invented over 80 years ago, the quest for weight and fuel reduction has triggered a raft of refinements. Matthew Beecham reports.
The main drivers of innovation of conventional alternators are the requirement to produce more electric power, more efficiently with smaller sized, lighter units. According to Jim McCaughey, Marketing Manager at Lucas Electrical, the most obvious change over the past ten years is the fact that units are getting smaller, whereas the ampere outputs are getting higher. He said: “Typically, the output of a unit ten years ago was 55A, whereas today a typical unit is nearer 90-100A. Some top-line car alternators are now topping 180A units.”
Mineo Hanai, Managing Director of Denso’s Electric Systems Business Group, added: “In recent years, vehicle power consumption has increased with the emergence of information and communication products such as navigation systems and electronic control products to improve comfort and safety and make vehicles environmentally-friendly. To meet the demand for additional power, alternators must produce electric power more efficiently with smaller size and lighter weight. In 2000, we introduced the world’s first SC [segment conductor] alternator using a rectangular conductor for its stator coil. By raising the winding density [space factor] from 45% to 70%, we made the SC alternator 20% lighter and increased the output to 50% higher than a conventional alternator.”
Turning to consider the main advances in starter motors, size, weight and output performance are also key. “Traditional pre-engaged starters made way for gear reduction units to enable the size and weight to be reduced,” added McCaughey. “The main shaft is separated from the pinion by a small gear reduction unit built into the starter body. The reduction unit enables the motor to rotate much faster than the pinion, and hence requires less power per turn of the motor to produce the necessary engine cranking speed. This allows smaller key components and less lasting material, thus reducing the weight and overall dimensions.”
Hanai added: “Starters have been required to be smaller, lighter and quieter while maintaining high output. In 1989, we launched an external-gear deceleration RA [reduction A type] starter that was smaller and lighter than our conventional external-gear deceleration reduction starter. In the same year, we launched our first internal gear deceleration starter using a planetary gear. It is easier to reduce the size and weight for the internal gear deceleration type than the external gear reduction type. In 2001, we introduced the world’s first internal gear deceleration PS [planetary reduction segment conductor] starter featuring a square conductor in the armature coil.”
How well do you really know your competitors?
Access the most comprehensive Company Profiles on the market, powered by GlobalData. Save hours of research. Gain competitive edge.
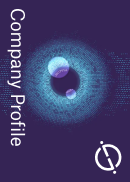
Thank you!
Your download email will arrive shortly
Not ready to buy yet? Download a free sample
We are confident about the unique quality of our Company Profiles. However, we want you to make the most beneficial decision for your business, so we offer a free sample that you can download by submitting the below form
By GlobalDataThere are also some subtle differences in terms of OEM requirements between Europe and North America. “In the US, vehicle engines are typically running at lower idle speeds, which makes them easier to start,” said Nik Armistead, Account Manager, Robert Bosch UK Ltd. “That means that the starter size – even for something as large as a 5-litre gasoline engine – could be around 1.1 to 1.4 kW which is the average size required for a 2-litre in Europe, where we’re also seeing continued pressure to reduce the actual size of starter motors due to the cramped space available in the engine compartment. Over the past 20 years, the weight of an average starter motor has fallen from 10kg to 2kg for the same output power.”
According to recent research studies, vehicles are at a standstill for one-third of the time while in urban areas. Stop-start systems could help make cities quieter, boost fuel efficiency and reduce exhaust pipe emissions. Stop-start systems operate by cutting the engine when the driver comes to a complete standstill. The engine is switched back on when he/she releases the brake pedal.
A few years ago the push for 42-volts appeared to be the main reason for introducing integrated starter-alternators. But, for many reasons, the momentum of the 42-volts power-net brigade has been reduced. These days, the issue of fuel economy has become a major promoter of integrated starter-alternator technology following the European carmakers’ association decision to self-regulate CO2 emissions down to a fleet average of just 140g/km by 2008.
Integrated starter-alternator systems aim to balance out irregularities in the running engine and in the drivetrain, providing more comfort. Clever electronics do the trick here. They help to control the starter-alternator operating state, depending on the load and battery charge status. There are two main design concepts:
· Belt-driven ISG device – shaped like an alternator, this electronically controlled machine replaces the starter motor and alternator, providing an instant stop-start function for fuel savings up to 5%. Various refinements of this belt-driven device can boost economy further – such as brake energy regeneration and mild engine boost.
· In-line units – mounted directly on the crankshaft between the engine and gearbox. Although the in-line systems are more expensive, they offer more power, regenerative power from braking and even engine-assist ability under heavy load.
Although both solutions have certain advantages, there are still a number of hurdles to cross before ISG technology is rolled out across car segments. “The biggest obstacle of the current ISG, including both the belt-driven and in-line type, is high cost,” said Hiroaki Kajiura, senior manager responsible for overseeing the development of ISG technology at Denso Corp. “The main reason for the high cost is that the ISG needs to have an inverter for driving. To solve this problem, we are working to increase the output power of the ISG so that it can perform not only stop-start but also regenerative braking and acceleration. However, these capabilities of the current ISG are not enough to compensate its cost. In addition to larger output power and lower cost, other obstacles driving the development of ISG include higher power generation efficiency, smaller size and lighter weight and higher reliability.”
ZF Sachs agrees that the main issue is cost. Frank Finzel, head of account management for ZF Sachs’ Electric Drives business, said: “The question is whether you can find new customers. I think they are reluctant to pay more for it. The fuel consumption alone cannot justify the extra expense of the system in the consumer’s eyes. I think the important step for introducing it divides into two areas. On the one side, there will be hybrids introduced into the market very soon which have more power and are fun to drive. It will cost more than the standard car but offers more power, acceleration and more fun. The other point relates to fuel consumption. If you only go for fuel reduction, then the customer will not feel anything better in the car so will look for support from the government, either in the form of a tax reduction or some other fiscal measure.”
The Citroen C3 was the first European production vehicle to offer stop-start via a 14-volt belt-driven starter-alternator in a market that is increasingly concerned with CO2 emissions and fuel economy. Citroen claims overall fuel economy improvements of 6 – 10%, depending on the drive cycle. The unit is supplied by Valeo.
Hyundai’s ECO Getz 1.1 CRDi concept car also features Valeo’s belt driven stop-start system, marking the first time that the device has been officially presented on a diesel engine. The system is also called ISG by Hyundai Motors, or ‘Idle Stop and Go’. “We believe that such technology will help enhance the image of the Hyundai brand and improve customer satisfaction, particularly with customers who drive in heavy traffic metropolitan areas,” said a spokesman for Hyundai. “We see the system as one of numerous different technologies designed to meet EU’s fuel consumption regulations and this stop-start technology will help us reduce emissions and lower fuel consumption, factors which are so important to European customers.” Hyundai do not foresee any problems in getting customers acquainted with this technology. “Some features of the system resemble technology used on hybrid as well as petrol vehicles, and the only uniqueness of this new stop-start system is how it works technically.” In terms of the Korean carmaker’s plans to roll out this technology across its entire range, the spokesman added: “As a first step, it will be introduced to diesel models exclusively. We are aware that our competitors are developing similar systems. After checking out feasibility of mass production, we will make a final decision.”
Ford recently unveiled what it describes as a ‘micro-hybrid’ version of its Fiesta model, basically a mild-hybrid version of the small car, with an integrated starter-generator replacing the starter motor and alternator and offering stop-start fuel-saving performance. The Fiesta offers a very modest amount of energy regeneration at 2kw, and this is available only when a gear is engaged, as the recovery path is via the transmission, engine, drive belt and finally the ISG. A spokesman for Ford told us: “Ford will continue to develop this technology to the point where it can be implemented into serial production.” Ford would not be drawn on how this technology could be rolled out across its model range, preferring the tight-lipped response: “We will discuss this in more detail as soon as the time has come.”
General Motors is now using Continental’s ISAD system on its hybrid 2005 model year Chevrolet Silverado and GMC Sierra full-size pick-ups. The ISAD is the first of its kind in production on a North American vehicle. Continental reports brisk business. Uwe Moehrstaedt, senior manager, sales and marketing for Continental Automotive Systems’ hybrid drives business, said: “We have good feedback from the customer. We have been requested by GM to produce more than we are currently able to do. We are trying to improve that situation. The market demand is better than expected.”
Although ISG technology represents a radical break from conventional rotating electric designs, it should take some time before its effect is felt in the aftermarket. “Any technical advancement will always take time to wash through to the aftermarket,” added Jim McCaughey. “With the advent of three and even five year warranties from vehicle manufacturers, sales of replacement parts are further delayed. It will be many years before serious demand for these items will be seen through the independent network.”
![]() | Expert Analysis | ![]() |
This 2nd edition global market review of starter motors and alternators extends and updates the analysis of the first report. It provides you with both historical data and forecasts of OE rotating electrics across North America, Europe and Japan to 2011. Exclusive interviews with top industry executives offer insiders comments on costs, market trends, market forecasts and new technical developments. Find out more here. |
![]() | ![]() |