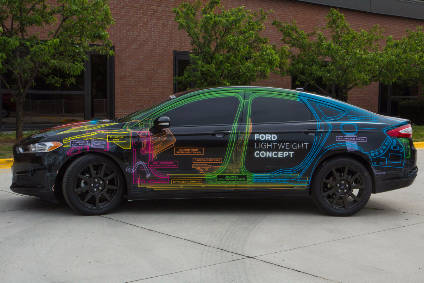
Continuing just-auto’s series of research snapshots – pulled from its automotive research platform, QUBE – this one takes a closer look at some approaches to vehicle lightweighting.
Carbon fibre looks more promising
Until recently, the use of carbon fibre in vehicle manufacture has been confined to high-end, low-volume vehicles. Joe Laux, Magna Exteriors director advanced engineering, tells just-auto why demand from OEMs for the lightweight material is now growing: “Carbon fibre use continues to grow very rapidly for a number of reasons (primarily strength versus weight ratio) in multiple industries. The first uses of carbon fibre were materials designed for the aerospace and racing industries. However, these initial offerings were not focused on cycle times because they were designed for low volume applications. For this reason there is a tremendous opportunity to develop materials focused on improved process time and that is where we place considerable focus. This, in combination with improved material costs, will grow the use of carbon fibre applications in the automotive industry.”
Borealis Automotive is also active in this arena. The company offers material solutions engineered to enable the automotive industry to achieve greater cost efficiency, higher performance and improved sustainability in vehicle components. Nicholas Kolesch, head of marketing, Borealis Automotive believes that as the number of end applications employing carbon fibre has grown, its supply has increased, therefore improving affordability. He told just-auto: “There are a number of technical challenges that need to be overcome when a new material is brought to market and the automotive industry rightly takes time to ensure its performance in high volume production.”
Lighter together
Partnering between OEMs and the supply base to develop lightweight solutions remains a popular approach to meet the increasing fuel efficiency requirements. For its part, Nissan has made a commitment to shed the pounds on its passenger car range for the whole of 2016 and beyond. The automaker’s ‘lightweighting programme’ will produce a pioneering prototype material structure designed to be used in the floor of the vehicles of the future. Working closely with the UK supply chain, Nissan is drawing on the materials and techniques used in the motorsport and aerospace industries, including the materials used in space travel. Nissan says that this programme will improve performance, fuel consumption and counteract the weight of the increasing amount of technology being built into vehicles.
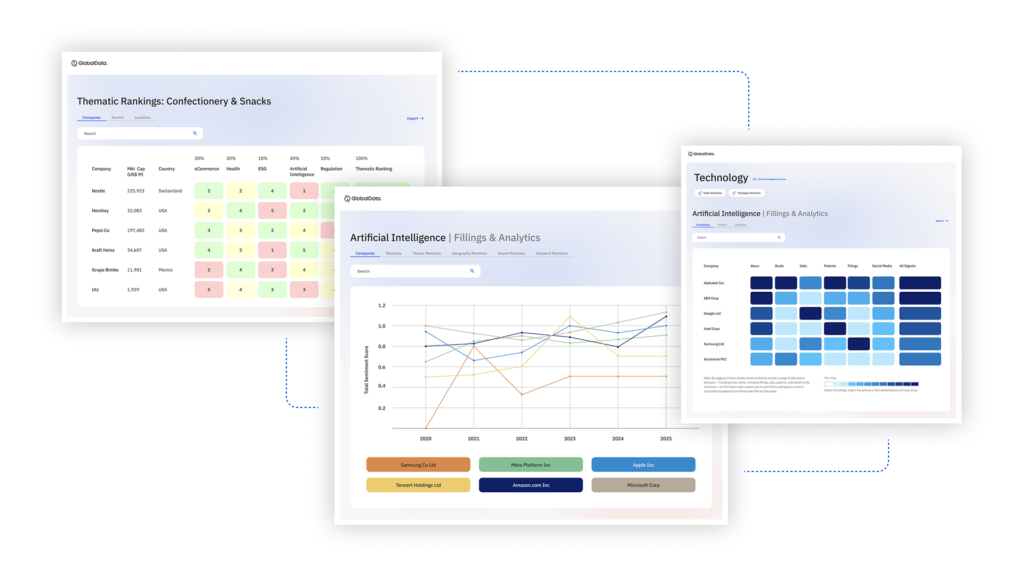
US Tariffs are shifting - will you react or anticipate?
Don’t let policy changes catch you off guard. Stay proactive with real-time data and expert analysis.
By GlobalDataFor some time, we have seen how using lightweight composites to replace certain metal parts or structures is enabling automakers to meet ever stricter regulations to reduce fuel consumption and CO2 emissions of their vehicles. In pushing back the technical boundaries, Solvay, Renault Trucks and its partners have used a thermoplastic composite material to build a front structural module of a truck, called the firewall. This new high performance composite material is based on Solvay Evolite thermoplastic resin reinforced with continuous glass fibre. The module weighs 25 percent less than a similar metal model.
Lighter car seats –
In developing its seating products, Faurecia aims to be a technology leader in lightweight. Geoffroy de Grandmaison, marketing director of Faurecia, explained its so-called Lightweight & Roominess seat concept. He told just-auto: “This seat features our short term proposals to improve lightweight and roominess. We have selected as a reference the driver seat of a Nissan Rogue (SOP 2013). The complete seat is a six way manual seat, mid height point, that weighs 18 kg, which is a best-in-class performance. It features our CMF1 frame, which weighs just 12 kg, which is a 20 percent improvement compared to the previous generation. It features our own acclaimed mechanisms and mechatronics. We have been able to achieve weight reduction while complying with the most stringent safety regulations. The frame is produced on our generic lines installed across the world which allow producing specific frames for different automakers on the same line.”
– and steering systems
In the steering department, Tedrive Steering Systems has developed a steering gear that is 30 – 40 percent lighter compared to a conventional part. While we peered closely at this gear on display at the most recent IAA, Peter Heimbrock, director engineering Tedrive Steering Systems GmbH explained: “This one [is] designed for eMobility vehicles hence those with very low front axle load. We have developed a similar technology for a column EPAS powered vehicles in the A, B and up to C class segments. For such cars, we have designed a mechanical steering gear with plastic housing that offers a reduction in weight of about half a kilogram. So saving half a kilo on the front axle becomes quite interesting for the OEMs.”
Steel focus
Reducing total cost of ownership and ensuring that new lightweight steels are strong enough to protect vehicle occupants in a crash are key challenges for materials and car designers alike. “The concept of Tata Steel’s Total Cost of Ownership (TCO) is that vehicle lightweighting must be cost effective,” states Chris Wooffindin, Tata Steel’s product marketing manager for automotive. “The automotive industry is a competitive one and our customers constantly face the paradox of achieving optimum performance at lowest weight and at lowest cost. The adoption of non-steel material to achieve lightweighting often comes at a significant cost premium.”
The supplier has developed a new engineering service called TCO scans. This service enables Tata Steel automotive engineers to work with the customer to prove where the application of its advanced steels sit in the balance between performance, cost and weight.
Wooffindin also believes that increased formability is a key enabler to achieving lightweighting. He added: “A common way of achieving lightweighting is to use the so-called upgrade – down gauge principle. This is especially applicable for components that are strength dominated such as safety cell reinforcements or chassis components such as the lower control arm. By using higher strength material, the engineer can achieve equivalent strength whilst specifying a lower thickness, which leads to a lower component weight. However, in general terms, higher-strength material, especially conventional high-strength steels, have lower formability. This means that the final component shape might be challenging to produce without material rupturing. The steel industry continues to develop new steels offering both high strength and improved formability to address the need for lightweighting whilst reducing the impact at the press shop.”
Meanwhile, we continue to see more use of high tensile steels. The trend in the increased use of higher strength steels such as 600 and 800 MPa material and ultra-high strength steels such as boron steel is clear, as are the weight-saving benefits.
The challenge for the auto industry is for better collaboration of OEMs and their supply chain to exploit these materials for further lightweighting opportunities.