
Continuing just-auto’s series of research snapshots – pulled from its automotive research platform, QUBE – Matthew Beecham reviews some novel door component innovations, including the use of tropical plant material by Ford and a game changing latch from Magna.
The door is one of the most complex systems on a vehicle. It must look good, incorporate crash stability and, above all, be fit for the purpose, typically opening and closing more than 50,000 times during the vehicle’s life. It also hides a myriad of functional componentry such as the window lift mechanism, locks, electric motor to operate the wing mirror, wiring harness, various switches, loud speaker and a cable that connects the latch to the inner release handle.
Weightwatchers
Despite its complexity, shedding weight from car doors is continually under scrutiny by OEMs. For its part, Honda has developed a technology to join steel and aluminium that will enable the use of aluminium rather than steel outer door panels to reduce vehicle weight. Using the technology, the combined weight of the four door panels of the Acura RLX luxury sedan has been reduced by 11kg, or 17 percent.
Magna is supplying an expanded polypropylene (EPP) door panel for the BMW i8 plug-in electric sports car. This industry-first expanded formed single carrier is manufactured in a one-shot-process in which EPP material is combined with structural parts and fastening elements. The supplier claims that, due to its design and material combination, the carrier weighs about 22 percent less than conventionally injection-molded carriers.
Material matters
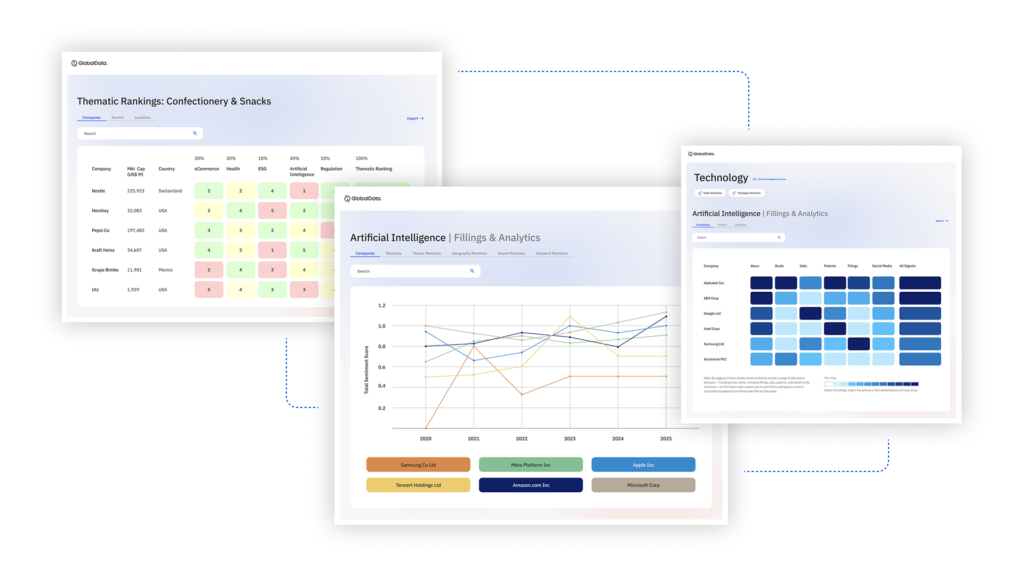
US Tariffs are shifting - will you react or anticipate?
Don’t let policy changes catch you off guard. Stay proactive with real-time data and expert analysis.
By GlobalDataWe are also seeing a number of interesting uses of different materials in car door construction that help protect the environment and further cut weight. For example, Brose is supplying the door module for the Porsche Panamera that features a magnesium window frame and aluminium door inner panel. The concept works on the principle of the supplier’s modular door with its wet/dry side separation.
While the use of organic materials in cars is not new, it remains a topic of interest. Ford is using kenaf, a tropical plant related to cotton and okra plants, to replace oil-based materials in the doors of the Ford Escape. The automaker claims that use of this material can reduce the weight of the door bolsters by 25 percent.
For its part, Faurecia designs and manufactures door panels using composite materials that combine wood fibres with polyolefin or polyester. These materials contain 63 – 73 percent of natural fibres. The use of natural fibres as reinforcement in plastic parts brings weight savings of 25 – 30 percent. Meanwhile, Johnson Controls is supplying door panels for the BMW 3 Series. The panels are made using a combination of natural fibres and plastic that are said to be 20 percent lighter than conventional components.
Sliding door innovations
Vehicle sliding doors can be difficult to open with unsightly lateral external guide tracks that spoil the look. In response, Dura Automotive has developed what it claims to be the automotive industry’s first power sliding doors for both front and rear entrances that can be featured in any vehicle segment. The supplier uses its so-called InvisiTrak technology to relocate the door opening and guide tracks into the inner section of the door structure. That means no modifications need to be made to the exterior of the car.
For its part, Aisin Seiki has developed a resin step power sliding door drive unit. This enables a lowered entrance step where the sliding door is 360mm above the ground thereby making it easier to get in and out for children and the elderly. This technology is already being supplied on the Toyota Noah and Voxy.
Lock trends
The apparent ease and speed in which car crime occurs puts increasing pressure on the major car lock manufacturers to introduce ever more complex locks with increasing amounts of electronics. The accent is on ‘value-added’ locking systems, which incorporate more functions to enhance comfort, such as central and double locking, child safety devices and keyless entry systems.
Keyless entry systems first appeared way back in 1996 on the Mercedes-Benz S-class. Since then, they have become almost universal in one form or another in the developed world, although most emerging markets still have a predominance of conventionally keyed locking systems. The trend from active to passive systems is unmistakable and has progressed furthest in Japan.
Keyless entry systems are not without their risks and disadvantages, however, especially that due to radio frequency interference and the associated risk from thieves blocking signals to be able to keep cars open when owners think they have locked them. Early keyless entry systems had simple, fixed code systems, while current systems have multiple code and response systems; even these are subject to interference and one of the biggest challenges facing the carmakers in coming years will be developing systems which cannot be compromised and convincing consumers that they have successfully done this.
Latching on to new ideas
Finally, we continue to see a development trend towards electrical latch systems. In this regard, Magna Closures has developed and now supplying its so-called SmartLatch for the BMW i8. “The SmartLatch is definitely a game changer,” said David O’Connell, Vice President – Global Engineering and R&D, Magna Mirrors & Magna Closures during an interview for just-auto’s automotive research platform, QUBE. “This extremely advanced latching system has been applied to one of the most technologically advanced vehicles to date – an excellent fit. SmartLatch requires no cables, rods or moving handles in the door. The benefits include significant weight savings and a reduced number of components, the flexibility to be used in any type of car or truck, and improved safety, sound quality and craftsmanship. Combined with the elimination of the lock rods, release cables and handles, SmartLatch provides an innovative, lower-cost door latching system to global automakers. This product will change the way vehicle latching systems are designed going forward.”