There are three things a gasoline engine needs: air, fuel and spark. The spark plug ignites the air/fuel mixture, producing the combustion that powers the engine. Despite the fact that spark plugs have featured in vehicles for more than a century, manufacturers are still pushing back the technical boundaries. Matthew Beecham reports.
The technical development of the spark plug has been quite marked over the last 20 years. Copper core electrodes became widespread during the 1980s. While NGK had developed such a product almost a quarter of a century before, it was not until 1984 that Champion, under pressure from Bosch, launched its own copper core range. It followed this in 1988 with the introduction of double copper spark plugs with copper core centre and earth electrodes. Platinum plugs were the next development, with Bosch launching its version in 1994. Ranges became more diverse with features such as V-grooves and multi-ground electrodes being introduced.
Today, the main technical drivers of spark plugs are long service life and functionality, protection of the catalytic converter and cold-start reliability. “I think that you will continue to see a trend toward smaller spark plugs as the automobile manufacturers try to use what little precious space they have in the engine compartment,” said Dave Sholtis, vice president, Autolite brand. “I think that you will see the trend continue toward precious metals. We will probably see some new alloys out there, too. There is a lot of work being done on different geometries and enhanced ceramics. So I think that we shall see some interesting new products coming out over the next few years as we continue to drive to figure out how we can make the engine run better in the limited space.”
“In larger engines with poor accessibility and the need to cover distances of more than 90,000 km between spark plug changes, a precious metal plug is the answer,” said a Bosch executive. “When shorter exchange intervals are accepted and the cost for the original and replacement spark plugs have to be moderate, the non-precious metal plugs are still a good option. For example, the Bosch spark plug with Yttrium alloy lasts up to 60,000 km.”
New spark plug designs are still emerging. Sholtis added: “A couple of years ago, we introduced an innovation that really revolutionised spark plugs. Our HT plug features a high thread design, allowing for superior cylinder head seating, better compressive seal, improved heat transfer. It has a 10mm spark plug versus a standard 12mm. That allowed the engine manufacturers to incorporate an extra valve. The HT spark plug is currently being fitted into the Ford F150 and Ford Mustang engines. We are in discussions with other OEMs.”
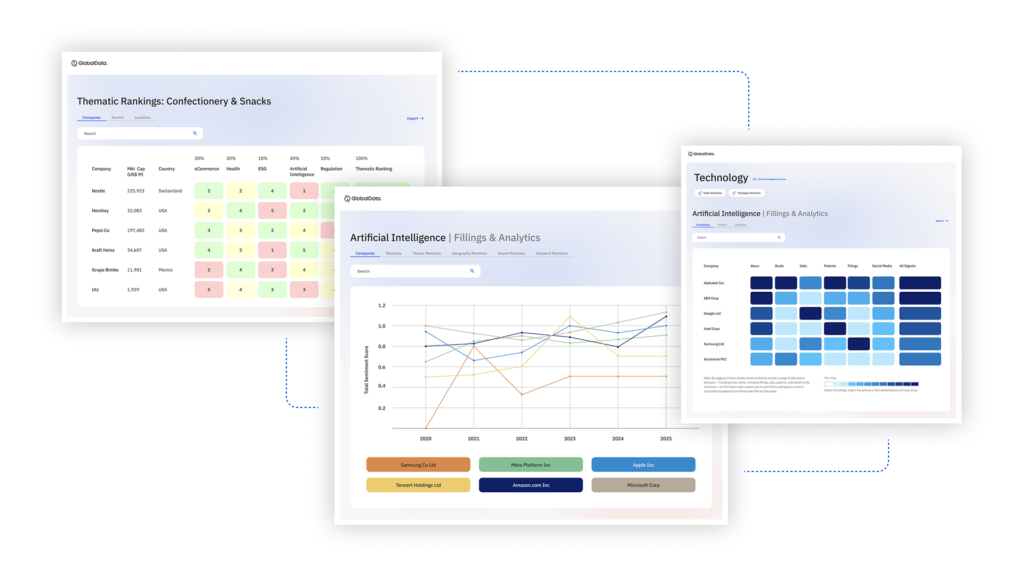
US Tariffs are shifting - will you react or anticipate?
Don’t let policy changes catch you off guard. Stay proactive with real-time data and expert analysis.
By GlobalDataAnother technological trend is the move toward a longer sled. “The standard length of a conventional sled was 19mm, but recently there has been more demand for longer sleds such as 26.5mm lengths,” said Toshikazu Shimizu, chief engineer of the Ceramics Engineering Department at Denso Corp. “The reason for this change is that longer sleds ensures more pathway for engine coolants in the engine head to reduce the temperature of the engine head, thus, leading to the reduction of knocking.”
Even though spark plug technology is improving, can it really catch-up with engine life, i.e. is a ‘life of engine’ spark plug a possibility? A Bosch executive said: “Although a wear resistant spark plug for an engine life of 200,000 km is theoretically available, the large amount precious material requires pushes the manufacturing cost to a level that is not acceptable for the engine manufacturer.”
As far as the spark plug aftermarket is concerned, most manufacturers concede a shrinking market. A Bosch executive said: “The market volume for spark plugs in the aftermarket is declining mainly due to longer service intervals and the fact that fewer gasoline-powered vehicles are being built in Europe.” The same forces apply in North America, as Sholtis added: “The overall number of units sold in the North American aftermarket declines every year. As the [service] change intervals increase, people expect the spark plug to last 100,000 miles instead of 30,000 miles. So to get people to change their spark plugs, we have very active advertising campaigns to remind people. While we do see the number of spark plug units declining, the interesting phenomenon is that people are increasingly using the premium precious metal product. So while the units have declined by about 4% year on year, the overall revenue is actually increasing by about 2%. The benefit to the consumer is that they are getting a spark plug that will last longer. From a green perspective, that means fewer plugs ending up in land fill sites.”
Another factor dampening the European spark plug aftermarket has been the popularity of diesel engines in passenger cars. Glow plugs assist in fuel auto ignition as a heat source when starting diesel engines. This contributes to reducing smoke and odour, improving economy and limiting battery consumption. “The main influences on the design of glow plug [centre on] the design of the diesel engine itself,” said Dr Rainer Podeswa, member of the executive board, responsible for R&D with Sales OEM, Beru AG. “Over the last ten years, there has been a trend toward smaller and longer glow plugs which have come about from the technology change from the indirect injection diesel engine to the direct injection common rail diesel engine. But this trend is maturing – I do not see a general trend toward even longer and smaller glow plugs. The smallest glow plug that we produce in series production has the diameter of just 3.3mm. So we have reached a certain limit. I do not rule out that in the future we might have a glow plug with a 3mm diameter but this is really not a major technology change. What I see in the next 3 – 5 years is certain engines with rather low compression ratios might need ceramic glow plugs. That is clearly a technology change, which will influence the glow plug market, even though this is not [yet] a general trend. As ceramic glow plugs are roughly twice as expensive as the metal glow plugs, we see this new technology will only be used if it is absolutely necessary, applicable to some engines but not for all. The other trend, which we see, is the additional function to the glow plug. We know that sensor functions will be integrated into the glow plug combustion chamber. This will be seen in the market in cars next year but it will have rather slow growth. It will become, however, a major trend with the next level of emission regulations.”
Manufacturers say stringent forthcoming exhaust regulations will spur further demand for more environmentally-friendly automotive parts. More specifically, the introduction of Euro 5 environmental regulations will make it nearly impossible to satisfy with conventional metal-type glow plugs as of mid-2009. That is the main reason why manufacturers are developing ceramic glow plugs. The temperature of such plugs rises much faster up to about 200ºC – hotter than the maximum temperature possible with steel glow plugs. In addition to the more efficient cold-start function of these glow plugs, engine designers expect product solutions providing the required heat energy when the engine would otherwise generate high exhaust emissions due to running too cold.
“Ceramic plugs are starting to gain a major foothold,” said Philip Jeynes, marketing manager for NGK UK. “From our viewpoint, there is a lot of OE development that we will see coming to fruition in the next 12 – 18 months.” Last year, NGK began supplying its third generation ceramic glow plugs as original equipment to the VW Group, marking the first time that a European carmaker installed such plugs. NGK’s latest generation ceramic glow plugs feature a long element with a small diameter, which heats up quicker than earlier generations, reaching 1000ºC in less than two seconds. This effectively improves cold starting and reduces emissions.
Meanwhile, Beru has developed a glow plug system incorporating an electronic control unit, which allows instant starting of diesel engines, without the usual five second wait for the plug to heat the cylinder even in extreme weather conditions. BMW was the first OEM to use Beru’s diesel instant start system (ISS). It means that diesel engines can start just as fast as gasoline. The glow plugs are made from steel, but the control unit is mounted on a ceramic substrate, directly onto the engine, thus reducing the length of the cables running to the glow plugs and reducing losses due to resistance. The ceramic-mounted control unit can withstand temperatures from -40 to +125ºC and vibrations of up to 40g, and the complete system allows starting of the engine without a delay at temperatures as low as -25°C. Beru’s third generation ISS is now on the market.
Matthew Beecham