Ride control is basically governed by a vehicle’s suspension system, including its shock absorbers (dampers) and struts. For the last decade or so, the high-end technical emphasis has been on developing dampers in which the damper rate can be varied according to the road conditions. Matthew Beecham runs the rule over the latest designs.
NOTE FROM THE PUBLISHER: Since our last review of shock absorbers was published in October 2007, the outlook for the automotive industry has significantly changed. Given the current state of the industry, just-auto has completely revised its estimates and forecasts of the OE shock absorber market volumes and values. Our revised forecasts for shocks are based on JD Power & Associates’ forecasts for passenger car vehicle assembly in North America, Western Europe and Japan from 2005 through to 2013.
Given that our in-house component forecasts set out the next seven years, we have extended JD Power’s predictions by a further three years to 2016. In addition, and given the sheer volatility of the global economy at present, we have set out ‘expected’, ‘best case’ and ‘worst case’ scenarios applied to OE passenger car shock absorbers and electronic shock absorbers. On balance, we believe this will provide readers with a more realistic framework for our component forecasts.
Technically speaking, the term ‘shock absorber’ is a misnomer because the device doesn’t, in the strictest sense, absorb shock at all. The shock absorber is designed to dampen the movement of the springs — be they coil, leaf or torsion bar — limiting the road shock transmitted through the tyre, wheel, hub and spring mount. Bushings absorb the rest. The spring must also support the weight of the vehicle. The sole purpose, however, of the more accurately named ‘damper’ in any suspension system is to control the spring’s oscillations. If they are damped, the tyre is able to stay in contact with the road surface. The net result is a more comfortable ride, precise handling, efficient braking and smooth acceleration.
There have been some advances made to shock absorbers which may be referred to as trends. To improve ride comfort without adding to cost, manufacturers are creating a longer shock absorber movement. Another clear trend in the shocks sector is integrating more and more electronics.
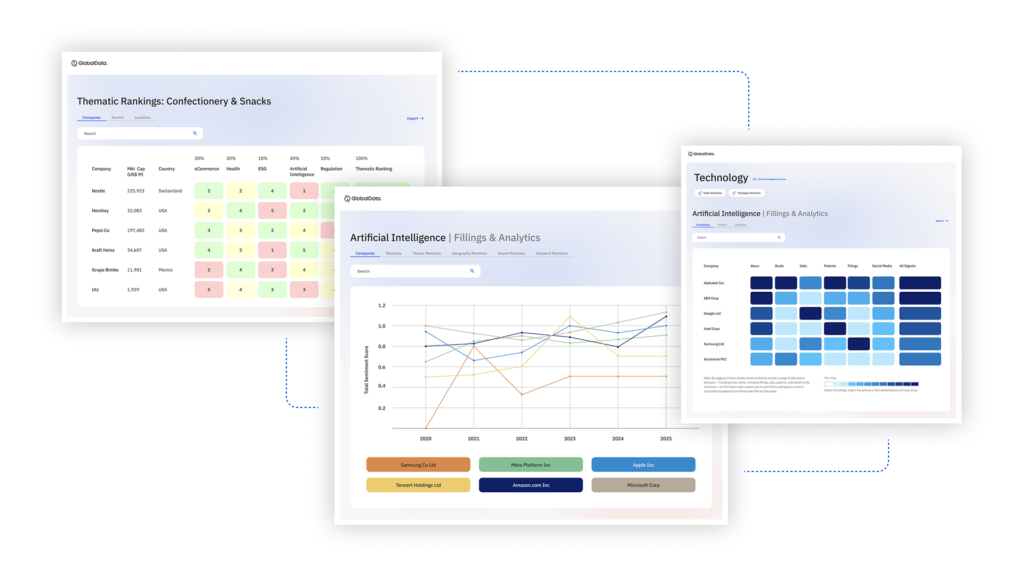
US Tariffs are shifting - will you react or anticipate?
Don’t let policy changes catch you off guard. Stay proactive with real-time data and expert analysis.
By GlobalDataElectronic dampers allow a large range between maximum and minimum damping levels and adjust instantly to ensure ride comfort and firm vehicle control. By integrating mechanical and electronic functions within a vehicle, automakers improve handling and reduce costs. Such technology can also help lift revenues for manufacturers.
The main competitors offering such technology include:
- Delphi — MagneRide which is currently fitted to a number premium vehicles in the US and Europe, such as Audi (TT and R8) and Ferrari;
- Tenneco — Computerised Electronic Suspension (CES) now supplied to certain Volvo, Mercedes-Benz, Ford and Audi models; and
- ZF Sachs — Continuous Damping Control (CDC) supplied for certain Audi, Opel, Porsche, Bentley and BMW models.
Most designs have concentrated on computer-controlling the opening and closing of valves which bring additional damper orifices into operation – thus the firmest rate exists with all valves closed – but Delphi has devoted much effort to developing its Magneride concept in which a magneto-rheological fluid passes through an orifice which can be “restricted” by applying an electric field across it. The fluid consists of magnetically soft particles suspended in a synthetic fluid. When current is applied to an electromagnetic coil inside the damper’s piston, the resulting magnetic field changes the rheology (or resistance of flow) of the fluid, which produces a mechanically simple but very responsive and controllable damping action without any valves. The company’s engineers continue to develop Magneride.
“We are working on a step change in the capability of ride control systems. Within one vehicle generation we will virtually eliminate the need to choose between ride and handling performance,” said Dr Alex Alexandridis, Delphi’s chief engineer for chassis technologies. To increase the performance of the system, Delphi’s engineers are focussing on delivering a higher dynamic range (or as the company puts it: “a softer soft and a harder hard”) and a faster transient response. The engineering team believes that this will allow MagneRide to take more control of the suspension so that the authority of the roll bar and springs (which create ride compromise) can be reduced and transient body motions can be controlled without additional systems. In looking beyond the capabilities of MagneRide, Delphi is investigating how vehicle dynamics, particularly response to emergency situations, can be improved by sharing data with other vehicle systems.
Tenneco Inc’s CES product increases the company’s content revenues seven-fold compared to a standard shock absorber. Tenneco’s engineers reckon that novel valve technologies, anti-roll suspensions and fluid-filled elastomers (rubber bonded to metal) that reduce noise and vibration, are “highly influential” is automakers’ buying decisions. “Although our technology seems similar to some competing technologies, it performs better because the system allows the damping characteristics to be changed in milliseconds, i.e. ensuring the occupant a smooth transition between comfortable ride and a safe handling,” said Koen Reybrouck, global ride control technology manager, Tenneco Europe NV. “Tuneability is also important. And, of course, driver comfort has improved, too. When we compare our current systems with those we introduced in 2003 then that has also significantly improved. In looking ahead in terms of the pure damping evolution over the next five years, I think we shall see even more tuneability and better damping curves. The electronics behind it is also very important.”
At an industry-wide level, Tenneco sees the good growth prospects for such continuous damping technology by the OEMs. “We can say that the markets are more than tripling over the next three years,” said Sandro Paparelli, vice president sales and programme management for Ride Control Europe, Tenneco Europe NV. “We are also working on system cost reduction in order to make continuous damping technology available for C segment vehicles. That is our objective. If we can achieve that, we expect to see the market further grow considerably.”
Reybrouck added: “When we talk about the ‘tripling of the market’, that is basically with the current technology. The technologies which are under development focus not only on performance improvement but also on cost reductions which will allow further growth. The trends we see there for those future systems is further application of electronics into the shock absorber itself, allowing the system cost on the vehicle to be dramatically reduced.”
Given that much of this continuous damping technology is initially only available as optional equipment, it is up to dealership staff to sell its benefits. For its part, ZF Sachs has joined forces with Opel to launch a dealership initiative in Germany. During coaching and training sessions, sales teams from dealerships learn how ZF Sachs’ CDC improves driving dynamics and safety. CDC uses a stepless approach to chassis damping, avoiding the previous compromise between hard and smooth damping. The ECU takes signals from the sensors and interacts with the anti-lock braking system and electronic stability control system while also taking information from steering wheel angle, brake pressure and engine torque. For the driver, who just has to push a button on the dashboard, CDC makes the car safer and easier to drive, prevents nose dive on braking and ‘squat’ on acceleration and allows driving on ‘sport’ or ‘normal’ damper settings. ZF Sachs’ Dr Nowak told us: “After successfully establishing CDC in the upper-class segment, more and more cars in the mid-range segment are also relying on continuous damping technology from ZF Sachs.”
His colleague, Dr Eickhoff added: “With conventional shocks, we see an increasing demand for additional features to help OEMs deliver perceivable customer benefits without too much on-cost. ZF Sachs Sensitive Damping Control e.g. is a system of amplitude selective damping, which offers more ride comfort without having to sacrifice safety. An extra valve in the damper provides exactly the right damping force fitting to the actual driving situation: lower damping forces for minor stimulations, such as road bumps, or higher damping for large stimulations, e.g. lane-changes or cornering. This simple and inexpensive system without electronics ensures optimal road contact and makes it possible for the driver to enjoy sporty driving with a constantly high level of ride comfort and safety.”
Like Tenneco, ZF Sachs’ predicts strong demand for continuous damping technology. Nowak added: “It is estimated that more than half of Europe’s new vehicles are now taking advantage of some degree of electronic control system to enhance vehicle stability. The market share at the moment for ESP for example is definitely higher than 50% in Europe. The market proportion across Europe for electronically controlled suspension systems like our CDC, compared with conventional shocks, is significantly smaller. Passenger cars featuring advanced chassis systems still make up less than 10% in Europe, but a strong increase of the market share in the near future is expected.”
Over the past few years, ArvinMeritor has gradually moved up the food chain, and now concentrates its efforts on designing, engineering and building complete suspension modules and systems although it still designs and makes shock absorbers and struts. “We are seeing integrated systems with chassis hardware (dampers, airsprings, actuators, etc), controllers, sensors, control software all included into integrated vehicle dynamics systems,” said David Hunt, senior director, Global Chassis Systems Engineering, ArvinMeritor Inc. “ArvinMeritor is specifying and developing all aspects of the system, including chassis hardware, controller hardware, sensors and most importantly, control software. The ride and vehicle dynamics will be as much determined by software as physical hardware in the future.”
ArvinMeritor has invested significantly on new suspension system designs, namely active air suspension, active roll control and active damping systems. Hunt added: “[Our] Active Air operates on the principle of a variable geometry air spring piston changing the area on which the air spring sleeve acts. This allows the spring rate to be varied by as much as 300%. We are developing methods of actively controlling this spring rate within the frequency response range of the vehicles primary bounce, pitch and roll modes. We look for the technology to be application-ready by the end of calendar year 2008 with advanced customer development projects currently in progress. The most unique aspect of our Active Roll Control system is its hydraulic power source; we use an electric servo motor pump power pack to meter oil to the actuators. Here the pump doesn’t need to be operating during strait line driving eliminating the parasitic power draw from a conventional FEAD mounted hydraulic pump. Our Adaptive Damping system is designed to provide a better vehicle package environment by integrating the hydraulic control valve into the piston rod assembly. This design offers better noise control and flexibility to the OEM customers in addition to a lower system cost compared to the current systems in the market.”
Suspension corner modules include brakes, struts, strut mounts and bearing elements as well as suspension bushings and vibration control elements. Ed Frutig, vice-president and general manager, Chassis Systems, ArvinMeritor Inc, believes that for most customers, corner modules are here to stay. “Of course the level of supplier engineering responsibility will vary greatly depending on customer development philosophies. We are involved in projects ranging from assembly and light integration to full coil over module development programmes. We also have several cross-car chassis modules in production with several new projects at various stages of development. Our current modules business is North American based, however many of the new projects are in Europe and China. China, in particular, has some very different market dynamics when compared to Europe, Japan or North America and offers some unique opportunities to chassis suppliers. The more aggressive Chinese based OEMs are looking for integrated chassis design and production services. This is especially so for the OEMs desiring to export or those planning to rapidly modernize their product lines. They are looking to accelerate their speed-to-market and require a supplier with complete chassis and suspension expertise that can step in and ensure that their next generation vehicle can meet global safety, reliability and ride performance standards. Through our joint venture with Chery in China, we will have the capability to supply damping technology to the Chinese OEMs as well as expand into complete corner modules and chassis systems.”
While shock absorber technology is becoming more and more important in the OE world, it is increasingly perceived as a commodity in the aftermarket. Yet the shock absorber continues to play an ever more important role in a new vehicle, especially given the increasing fitment of electronic devices like ABS and ESP.
Tenneco believes that too few drivers are aware of the dangers of worn out shock absorbers. Tests have shown that driving with 50% worn shocks can increase emergency braking by 2.6 metres. In addition, worn shock absorbers can increase a driver’s reaction time by up to 26%, cause uneven headlights – which can dazzle oncoming drivers – increase the risk of the vehicle aquaplaning by nearly 10% and can cause the vehicle to lose control when cornering or caught in a cross wind.
In an effort to ‘educate the motorist’ about the dangers of worn-out shocks, Tenneco has a number of initiatives underway. “We try to communicate by giving the press an opportunity to drive vehicles with worn-out shock absorbers and compare them to vehicles fitted with new shocks,” said Paparelli. “We also offer a lot of training activities. For example, we have a ‘testing van’ which travels to European cities which shows consumers how to diagnose a worn-out shock absorber. The van has the latest diagnostic equipment. Its purpose is to educate the market and advise on the dangers of driving on worn-out shocks.”
Is it easier to get that message across to the Germans than it is to, say, the British? “We very often have this discussion about British motorists,” concluded Paparelli. “Although I feel that the people in the UK are real motorists – they like cars – they don’t replace their shocks quite as often as their German counterparts! Vehicle inspections also vary from one country to the next.”
See also: Global market review of shock absorbers – forecasts to 2016