The trend in both Europe and the US is toward increasing complexity of door componentry, adding more electronic functions and, in some cases, the glass itself. There are, however, still some significant hurdles to cross before the industry sees the complete door in volume production. Matthew Beecham re-opens just-auto’s annual review of door systems.
Next time you open your car door, take a closer look. Sure, car doors are becoming slimmer to provide more cabin space. But the trend has caused an increase in demand for smaller and lighter power window motors. In fact, space limitations inside the door make narrow drive units imperative. As new cars are increasingly fitted with remote control, automatic operation and other value-added power window functions, more cars require anti-pinch protection systems. This has resulted in a growing trend for smart motors with built-in circuit controls.
While more and more electronics are packed inside car doors, automakers are increasingly outsourcing their requirements for door modules. In outsourcing a door module, an automaker could typically gain in the region of 5%-10% weight savings, 10% for parts and 10%-20% in cost savings. Of course, the actual cost saving depends on the vehicle programme and materials used in the module, i.e. a steel door module carrier is typically cheaper than a plastic one. A door module typically consists of a rubber-sealed carrier made from either plastic or metal. A variety of door components are then fitted onto the carrier, forming a ‘cassette’, such as the window lift mechanism, locks, electric motor to operate the wing mirror, wiring harness, various switches, loud speaker and a cable that connects the latch to the inner release handle. The carrier plate is then tested and sealed to the outer door.
Latching onto new innovations
Most of the major suppliers pitching for door module business have their origins in either window regulators or plastic interior trim. ArvinMeritor, for example, has a strong tradition in the window regulator business. The company’s Light Vehicle Systems business group has been awarded a multi-year contract to supply Hyundai North America with a plastic door module and accompanying corporate latch product for the new Hyundai Sonata. Production is scheduled to begin in March 2010. The so-called highly integrated plastic (HIP) door module will replace the current steel version, and is part of ArvinMeritor’s Smart Systems product strategy to combine electronics and controls with heritage mechanical components to enhance vehicle systems performance. The HIP uses a composite construction to integrate the electro-mechanical and modular components, saving up to 25% in weight and representing the first application of plastic door module technology at Hyundai. It is also the first such ArvinMeritor product to appear on the North American market.
ArvinMeritor has also developed a so-called Low Energy Release (LER) door latch which it describes as a “solution for tomorrow’s vehicle safety and door closure requirements”. The LER uses proprietary electronics and software controls coupled with a mechanical solution to greatly reduce release efforts without compromising strength or safety. The company claims its LER improves passive entry functionality, releases at far higher seal loads, provides silent locking operation and offers increased resistance against theft tools. “ArvinMeritor’s original software locking logic means the same latch system can operate under a multitude of different regional and customer specific functional demands across all vehicle platforms,” said Aziz Aghili, vice president and general manager, Aperture Systems, within ArvinMeritor’s Light Vehicle Systems business group. The latch employs a failsafe override mechanism that, in the event of vehicle power failure, allows the latch to revert to fully mechanical operation. The product is smaller and lighter than current designs and contains up to 50% fewer parts, says the supplier. The range of application includes side door latches, power locking, electrical release and powered closure, as well as variants for sliding doors, boots and tailgates.
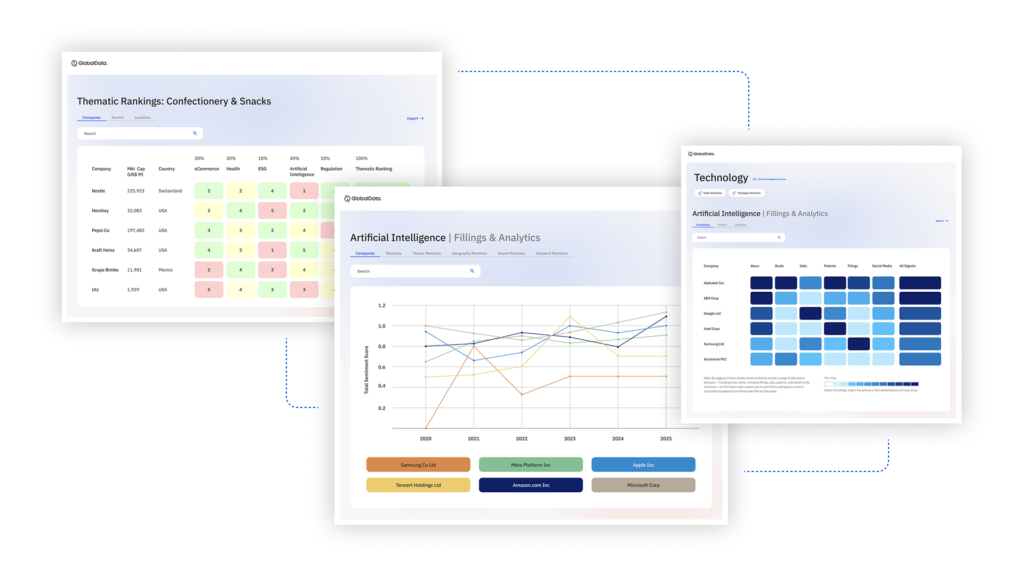
US Tariffs are shifting - will you react or anticipate?
Don’t let policy changes catch you off guard. Stay proactive with real-time data and expert analysis.
By GlobalDataArvinMeritor has also opened new markets in Asia with its New Asian Latch (NAL) products. These products are a range of modular door latch designs developed with a footprint concept specifically customised for Asian vehicle applications. With a compact size and high longitudinal strength, the company says the range is also aimed at optimising the sub-components for local supply and the assembly process for local manufacturing. ArvinMeritor says its NAL products are scheduled to launch on an unnamed Chinese domestic platform during summer this year. The company also used the 2008 Beijing motor show to unveil a new sliding door latch system for Asian applications. The system features a closure system comprised of a controller, rear latch, hook latch, power closure actuator and all linkages and strikers. The company says the new latch will appear in the Asian market this year.
For its part, Kiekert has developed a platform solution for side door latches, dubbed Alpha (which stands for Advanced Latch Philosophy with High Applicability.) “The challenge of developing a manufacturer-independent modular system lies in coming up with an economical end product with as few variants as possible yet a maximum of application potential,” said Dr Ulrich Nass, executive vice president, product development, Kiekert. “You have to find a compromise between the high complexity requirements and diverse market-specific functional distinctions“. As part of a benchmark exercise, Kiekert filtered all the OEM-specific characteristics from some 40 latches with 200 different properties. The company pointed out that defining these identifying features with an exceptionally high degree of precision was especially important for the design – and competitive potential – of the end product. The net result is a side door latch meets all the necessary market specifications along with the globally required functionality and interfaces. Moreover, the basic design can be extended from simple mechanical latches to units with central locking, double lock, keyless features and power closing aids.
New materials are also finding their way into vehicle doors. For instance, Continental is using BASF’s Ultradur S4090 G4 LS High Speed material for a door control device in the Audi A4 and A5. The move marks the first serial automotive electronics application for the 20% glass reinforced PBT/ASA (which stands for polybutylene terephthalate acrlonitrile-styrene-acrylate copolymer) blend. The door control device is located inside the doors and is connected to the central electronic unit through the vehicle’s electrical system. The device is responsible for opening and closing doors and windows and it controls safety functions such as the squeeze protection and other electronic modules located inside the doors.
Sliding open new doors
Although the minivan market is not increasing, the sliding door module market is growing. With a higher level of complexity on a sliding door compared to a conventional hinge door – with front and rear latching systems, the power sliding door system and now with window systems – most automakers have either already introduced a module or are considering it for the next-generation vehicles. But there are, of course, technical challenges to address. As a rule, says Dura Automotive, automotive sliding doors are difficult to open, with unsightly lateral external guide tracks that spoil vehicle design, and they can generally be deployed only for large transport vehicles or vans. In response, Dura Automotive used last year’s Paris motor show to unveil the automotive industry’s first power sliding doors for both front and rear entrances that can be featured in any vehicle segment. The company uses its so-called InvisiTrak technology to relocate the door opening and guide tracks into the inner section of the door structure. That means no modifications need to be made to the exterior of the car. “With our new generation of power sliding doors, we made it clear that our solution can be adopted for all automotive concepts without any limitations or concessions in terms of construction and visual design”, said Gerd Heuel, director of engineering, Dura Automotive Europe in Plettenberg, Germany.
Finally, Faurecia has developed a pre-crash vehicle safety system, as part of its APROSYS (Advanced PROtection SYStems) project. The system is able to predict an on-coming collision and activate a side-impact protection system that can reduce the risk of injury. The pre-crash sensor system is integrated into the vehicle body. This is able to predict a collision a split-second before impact and decide whether or not to activate the safety system. The safety system itself, which was developed by Faurecia’s experts in Scheuerfeld, Germany, is designed to reduce structural intrusion into the vehicle by up to 70mm. To achieve this, Faurecia’s engineers developed a system that, once activated, forms a continuous metal tube that runs from the exterior chassis of the door, under the seats and through the opposite door. Faurecia says this allows the energy of the collision to be transferred right across the vehicle thereby reducing the force in the impact zone. The actuator that makes this system possible involves technology that Faurecia developed with the Fraunhofer Institute. Once the pre-crash sensors give the signal, a wire switch made of shape memory alloy releases a spring-loaded bolt that effectively extends the metal tube from the seat to the door on each side of the vehicle. Another actuator closes the gap between the door’s exterior shell and interior trim. The result is the creation of a continuous metal tube within 60 milliseconds of the initial signal that redirects the forces of the collision away from the b-pillar.
Matthew Beecham
‘Beechy’
See also: Global market review of door modules – forecasts to 2016