Over the last two decades, the popularity of sport utility vehicles, minivans and cross-over vehicles has steadily increased, prompting manufacturers to redesign their tyres. Matthew Beecham rolls out just-auto’s annual review of tyres, reporting on the ways in which manufacturers are improving tyre dimensions, weight, rolling resistance, noise, and fuel efficiency.
Running on flat
Perhaps the most dramatic innovation in tyre technology over the past decade or so has been the development of the run-flat tyre. Run-flat tyres are specially constructed enabling them to be driven on in the event of loss of air pressure. It means the driver can either drive home or to a garage to fix the tyre. Run-flat tyres allow a motorist with a puncture to drive the car up to 120 miles at a maximum speed of 50mph before repairing the tyre.
While run-flats have done a lot to improve vehicle safety, they still come with a high price tag. So could technological evolution bring run-flat into the cheaper mainstream? “To the best of our knowledge,” said Chuck Yurkovich, Cooper Tire’s vice president of global technology, “there is no new low cost material technology in the short term that can provide the material property performance requirements for stiffness and fatigue that can make run-flat technology affordable to the mainstream market. It should be pointed out that the current self-supporting, run-flat technology typically carries a 20-30 percent weight penalty for the additional materials used to make the run-flat, self-supporting (inserts).
“These materials are expensive,” continues Yurkovich, “and must be passed on to the consumer to maintain profitability for the tyre companies. In the longer term, non-pneumatic tyre technology, which takes a completely different approach, is continuing to advance due to new design concepts and the utilisation of non-standard tyre industry polymers such as polyurethanes and thermo-plastic elastomers. This technology, due to its lighter weight construction and potentially lower material costs, could one day become available at a price that is reachable to all consumers.”
Reducing rolling resistance–
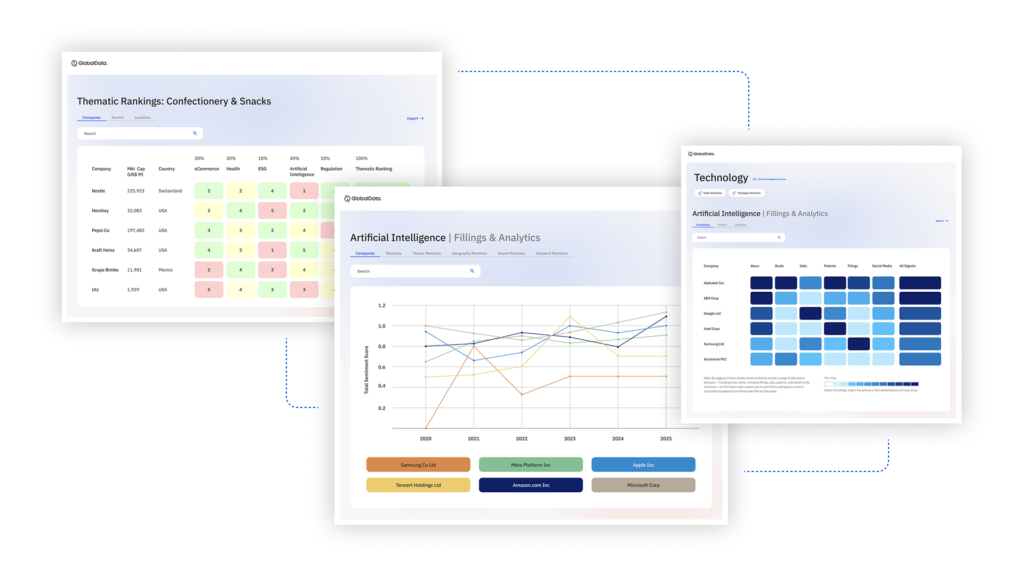
US Tariffs are shifting - will you react or anticipate?
Don’t let policy changes catch you off guard. Stay proactive with real-time data and expert analysis.
By GlobalDataIn addition to driver safety, the current focus is to find ways in which to reduce CO2 emissions. As 25% of all CO2 emissions are generated by road traffic and about 20% – 30% of a vehicle’s energy consumption can be attributed to tyres alone, measures to improve rolling resistance remains a top priority. “The energy consumption attributed to tyres cannot be eliminated, and will always be significant,” said Franco Annunziato, senior vice president, technology, Bridgestone Europe. “Nevertheless, tyre companies continue to make inroads to reducing the rolling resistance of tyres to contribute to reducing CO2 emissions. All tyre companies are faced with the same challenge whereby tyre performances are linked to each other.
“For example,” continues Annunziato, “it is possible to make a tyre with far superior low rolling resistance than current tyres, but the penalty would be that the wet braking performance of the same tyre would be unacceptable, and even dangerous. That is why the European labelling regulation includes both energy efficiency and wet braking performance on the same label. Our company has introduced nanoprotech technology in the tread rubber compounds, which lowers the rolling resistance coefficient by reducing energy loss in the top compound during rotation.”
The latest Goodyear EfficientGrip features the tyre maker’s so-called ‘FuelSaving Technology’, according to James Bailey, manager, corporate communications, Goodyear Dunlop UK. He told us: “This comprises several technology advances which directly affect the tyre’s rolling resistance: an improved construction with special lightweight materials; an enhanced building and manufacturing process and an innovative compound technology with a new material formulation that delivers excellent results in mileage, wet braking and rolling resistance. Using new materials and an efficient structure, the tyre’s weight has been reduced by about 10%. Less material with less heat generation leads to reduced rolling resistance levels. Compared to its predecessor, the EfficientGrip features a lower polyester ply end and a sidewall using less material, which contributes to the lower weight as well as to reduced rolling resistance.”
Continental executives told us: “We do not only look [at] rolling resistance but [at] the combination with all safety-relevant improvements on tyres. Therefore we would speak about our tyre for the blue technology cars from VW and other companies that are equipped for example with the ContiPremiumContact 2. This tyre combines safety and low rolling resistance at a high level. We can produce this tyre because we know the car and its driver assistance systems, such as ESC. With this knowledge, we can combine short braking distances — even on wet roads – with a lower rolling resistance.”
Last year, Cooper Tire introduced its GFE product line which stands for Greater Fuel Efficiency. Yurkovich told us that this low rolling resistance tyre takes advantage of the latest technology for design/materials and typically offers fuel efficiency improvements over conventional replacement tyres of 4 – 6 percent, adding: “This tyre features optimal tyre shape, traction compensating sipes, and ultra low rolling resistance tread formulation utilizing silica-silane with functionalised polymer technology. It should be noted as greater emphasis is placed on fuel efficiency in the future, this technology will eventually become the mainstay for all products in the industry.”
–and road noise
In addition to low rolling resistance, low tyre/road noise are requirements imposed on modern tyres for environmental and economic considerations. “Reducing tyre road noise is a challenge for all tyre manufacturers,” added Annunziato. “It has been proven that road surfaces and the materials used to make them can contribute more to the reduction of tyre road noise than the tyre itself. Also, the quietest tyre possible to make is a slick, that is, a tyre with no tread pattern at all. Slicks are not an option for normal cars as the lack of wet grip would be unacceptable. It is the grooves of a tyre’s tread pattern that contribute to creating external noise, but it is the same grooves that allow for water evacuation and directional stability, and grip on wet surfaces. By optimising tread design, it is possible to achieve the regulated noise limits, and this is where most of the advances have been made with regards to tyre noise.”
Yurkovich believes that, like many tyre characteristics, successfully reducing tyre/road noise often involves overcoming other performance trade-offs. He said: “Since a significant amount of the tyre-related portion of tyre/road noise is generated by the tread pattern, we spend considerable time and effort in determining proper tread groove placement, depth and pitch sequencing in order to optimize the balance of tyre/road noise and wet traction. To do this effectively, we’ve invested in development of both predictive and testing tools. For example, we have developed a tool that enables prediction of in-vehicle tyre sound quality characteristics from the test data of a single tyre in an indoor noise chamber. We are also developing methods to further extrapolate that indoor, single tyre test data to predict performance on the pass-by noise test specified by many regulations. This enables us to optimize tyre noise for both the customer and the environment.”
Based on the upcoming noise regulations, Continental executives say that the tyre type they have to focus on is the drive axle tyre. “Rib tyres — which are usually used on front and trailer axles — are already noise optimised because of their tread design structure. Due to the special demand on traction, drive axle tyres have to follow a certain tread design which makes some additional noise optimisation necessary. Therefore we are working with the German road association, BAST and some universities with the aim lowering these emissions. Within this co-operation we want to achieve a noise reduction of 3-4 dB for certain tyre types in order to meet the new regulation.”
Bailey points out that Goodyear’s tyres have tread blocks of different varying lengths specially designed to reduce noise and boost the ride comfort provided. The random block sizes break up the noise frequency as the tyre rolls, reducing road noise both inside and outside of the car.
Tyre labeling
In late 2008, the EU Commission presented the directive for the combined tyre label planned from 2012 specifying the criteria for braking performance, rolling resistance and rolling noise. The label comprises a concrete specification on the basis of seven classes (A – G) for rolling resistance (in kg per 1,000 kg wheel load) and for braking performance as well as precise details of the noise level generated by the tyre when rolling (in dB (A)).
Implementation of the tyre label regulation will be via self-certification by the tyre manufacturers, whilst the sanctions for misuse and infringements will be laid down by national law in each of the 27 EU states. Validation will occur in spring 2016, some 40 months after the obligatory introduction of the EU tyre label, and will take a critical look at whether the label is achieving its objectives, in particular the effectiveness of the requirements relating to point-of-sale communication.
Annunziato believes that the end consumer will be able to recognise the performances of each tyre before they purchase it, thanks to a performance label that must be displayed with the tyre, and on point of sale material. He said: “The label, inspired by the energy efficiency label which is currently displayed on refrigerators and other white goods, will show the wet grip grading of the tyre and the measured external noise in dbA as well as the energy efficiency rating on a seven grade scale. Thanks to the label information, consumers can make their choice depending on their own preference; maximum safety or maximum fuel economy.”
Continental executives say that consumers can be better informed about short braking distances, rolling resistance and tyre noise. “We expect motorists will find out that there is a general target conflict in short braking distances, low rolling resistance and low noise. The EU tyre label gives a short overview about the performance information regarding these criteria which is good – but it is still reflecting only three of more than ten tyre performance criteria.”
It is certainly true that the EU label focuses on three of the relevant tyre characteristics. It will be interesting to see whether individual tyre manufacturers will already use the EU tyre label in their advertising before national laws determine the sanctions to be imposed for misuse and infringements.
Tyre pressure monitoring systems
There are basically two main types of tyre pressure monitoring systems (TPMS) available on the market: indirect and direct.
- Indirect systems are those which use algorithms to interpret signals in ABS brake system. It uses wheel speed sensors and can detect a deflated tyre because it rotates more slowly.
- Direct are those which use separate radio sensors mounted in each wheel which detect deflation and then transmit that information to the driver via a radio frequency signal. As the transmitter is located inside the tyre, it requires its own battery power source, built to last up to ten years, or far beyond the tyre’s useful life.
With either system, warning lights, messages on the dashboard or audible warnings alert drivers to drops in tyre pressure.
By installing tyre monitoring systems, additional benefits include increased fuel economy, longer tyre wear, fewer crashes due to tyre blowouts, immobilised vehicles or poor vehicle handling from pressure loss and hydroplaning. It also means that motorists can instantly check their tyre pressure without touching the greasy tyre valve. Tyre pressure monitoring is also essential for run-flat systems.
Continental started supplying electronic systems for automatic monitoring of tyre pressure on cars in 2000. The tyre maker currently provides TPMS to 20 automakers worldwide. Continental says that the systems that are best accepted by drivers are those that, should there be an underinflated tyre, indicate which tyre is low and how much air it needs in order to be properly inflated. The TPMS that measure directly can then be supplemented with an additional pressure calculation based on the ABS sensors. This, says Continental, can further improve the quality of the sensor data thanks to the additional plausibility check, thus providing an even greater margin of safety.
In the early days of indirect TPMS development, it was said that the system had within it all the information required to create a vehicle ‘black box’ similar to that found on aircraft. Yet as we see it, this idea never really took off into mainstream vehicles.
Continental executives agree that black box functionality never really took off. “Next-generation TPMS systems are focusing on integrating the up-to-now fully mechanical tyres into the electronic control algorithms of modern vehicles. This concept is known as the intelligent tire system. It extends the scope of classic TPMS systems to electronically identify tire properties and even measure physical data at the tyre-road interface. Early applications will enable CO2 assistant functionalities to improve gas mileage and reduce greenhouse gas emissions. Load detection and filling assistant functions will help the driver in selecting correct target pressures and filling the tyres to the desired pressure levels. The ultimate target, however, is using tyre-related data to improve chassis algorithms, e.g. roll-over protection or brake distance, thus enhancing fun of driving and vehicle safety at the same time.”
Tomorrow’s tyres
People talk of the intelligent tyre as vehicles change. Yet with newer forms of propulsion, in what ways will the tyre change and adapt to such technology? “There have been, and still are, many research projects looking at various ways to bring information from the tyre to the vehicle,” said Annunziato. “As the tyre is the contact point to the road, dynamic feedback in real time of tyre/surface interaction could provide benefits to ESP, ABS and other systems reliant on knowledge of the level of tyre grip. Unfortunately, integrating electronics inside such a harsh environment, with high rotational and shock g forces, is not simple, especially as adding weight has a negative impact on vehicle dynamics. Many in vehicle sensing systems can already estimate grip levels quite well so cost/benefit is not high to have an in tyre solution. For future vehicles, whether fossil fuelled, electric or some hybrid form, the need to maintain safety and optimise rolling resistance will be increasingly important so TPMS should become a key vehicle component.”
Bailey concluded that, in the last decade, we have seen the emergence of technologies such RunOnFlat, TPMS, Fuel Saving Technology and Duraseal self-sealing technology for truck tyres. “The next decade promises to be even more exciting! I can’t share the detail of our secrets, but a great example of innovation is SmartWear Technology. Previewed on Goodyear OptiGrip, launched last year, SmartWearTechnology is designed to reveal a new tread design and compound as it wears, ensuring it achieves ‘as new’ levels of performance over its whole lifetime – without having to compromise on mileage. No-one thought this was possible a few years ago. It shows what is possible with a relentless focus on innovation.”