Road wheels have been constantly re-invented to the point where the main development trends are moving beyond bigger, lighter and brighter wheels toward scale and flexibility in design. Matthew Beecham rolls out just-auto’s latest review of road wheels.
Reinventing the wheel
Over the past 100 hundred years or so, road wheels have been made from a variety of materials including wood, steel (casting, sheet or wire), aluminium (casting, forging or sheet), magnesium, composites and a combination of the above. During the early days of motoring, steel was seen as the preferred choice for producing wheels; from the 1930s through to the 1980s, steel wheels dominated the market. By 1935, steel wheel diameters had decreased from 36-inches to 16-inches while rim widths increased from 3-inches to 6-inches. The process of stamping the centre (disc) and rolling the rim was well suited for high volume, low cost production. Hot rolled, low carbon steel grades were predominant for wheels prior to the 1970s and continue to be used, mainly on rims, today. The early- to mid-1970s brought the need to reduce weight and led to the introduction of higher strength steels into wheels.
During the 1980s, with the growing emphasis on fuel economy and the need to reduce vehicle weight, automakers turned to alloy wheels. Hurt by the loss, steelmakers enlisted the help of wheel manufacturers and automakers to launch a campaign to create new wheel styling and explore the use of new steels. Using bright materials like stainless steel that attach predominantly to the wheel and modifying disc and rim designs to enhance styling, wheel makers managed to satisfy consumers’ desire for a decorative styled wheel.
Although the North American and European alloy wheel market has grown over the past decade, the pace of growth has slowed recently and, just-auto believes, is set to decrease slightly over the next few years. Advances in the use of steel, supported by industry groups such the American Iron and Steel Institute (AISI), has meant that manufacturers of steel wheels can meet alloy wheel designs head on. According to the AISI, steel wheels are making a comeback as automakers realise they can save up to US$200 per vehicle without sacrifice to quality or performance. Ford, Chrysler and General Motors are among those switching to steel wheels thanks to the development of new high-strength steels and improved design and simulation technology, says the AISI.
Among the reasons for the comeback of steel wheels are high strength steels and new designs that offer large ventilation openings that mimic the thin-spoke appearance of some alloy wheels. More specifically, the use of high strength steel, plus high-ventilation area wheels design, increases steel wheel market opportunities. Lighter weight, high-strength steel has opened up increased opportunity to mimic the thin-spoke appearance of some alloy wheels. In addition, the use of high-strength steel has drastically reduced the weight penalty normally associated with steel wheels.
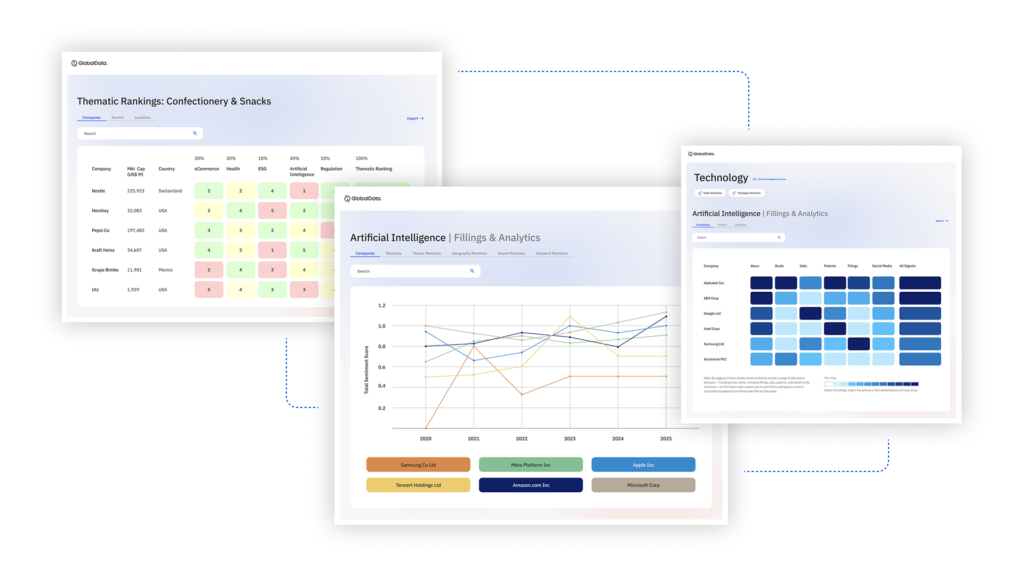
US Tariffs are shifting - will you react or anticipate?
Don’t let policy changes catch you off guard. Stay proactive with real-time data and expert analysis.
By GlobalData
Material is immaterial
Jim Cran, project manager of the AISI’s Wheel Task Force, told us: “Since 2005, the Big Three have significantly reduced the percentage of aluminium wheels they use. Cost was a huge driver. Also, the Big Three have recognised people want good looking wheels. Material is immaterial. The large vent area steel wheel has received excellent acceptance. It gives a styling that is competitive with aluminium and cost savings over aluminium. The use of permanently bonded facia has also been a factor. The same base steel wheel can be used on different makes and models. Only the fascia needs to be changed. Significant development and tooling savings result in lower cost steel wheels. Yet another factor is the fact that the ratio of car to light truck sales is increasing. The trend to a higher percentage of cars means a higher percentage of steel wheels because the use of aluminium wheels is greater on light trucks than on cars.”
On balance, just-auto estimates that in North America, about 62% of newly assembled passenger cars in 2008 were equipped with alloy wheels, up from 55% in 2000. Alloy wheel installation rates have increased to this level since the mid-1980s, when it was only 10%. Now that aluminium has replaced steel in over half of new vehicles built in North America, competition has intensified as new gains are hard fought. In Western Europe, we estimate that about one-third of newly-assembled passenger cars come equipped with alloy wheels, up from one-quarter in 2000. Given our view of the recent slowdown of the alloy wheels market and the global economic downturn, we predict modest decline in demand for alloy wheels across North America, Western Europe and Japan through 2016.
There are a number of other benefits of steel wheels over aluminium. Along with lower costs, steel wheels offer better pothole resistance and improved corrosion resistance in the bead-seat area.
Although the stamping process used in manufacturing steel wheels has some limitations in terms of design, manufacturers are working hard to have designs that allow it to address wheel designs and styling cue needs. “Our research indicates consumers like good looking wheels,” added Cran. “It also indicates consumers prefer steel wheels for safety and strength reasons. Unfortunately for steel, the automakers bundle aluminium wheels into option packages. In reality, the consumer takes the wheel assigned by the automaker. Our Task Force wishes to address this issue and is planning to promote steel wheels to the public in 2009.”
Weighty wheel issues
Other trends in wheel design include larger diameter wheels. There are two main reasons for that. The first is appearance; people like the highly styled wheels with low profile tyres. There has been a steady tendency, during the last 10 – 15 years, for cars to be fitted with wheels which are both larger in diameter and wider than those seen in cars of 1990 and earlier. At that time, the average wheel rim diameter was around 13-inches for B/C segment products, increasing to 15- or 16-inches for high-end and luxury models. Today the equivalent figures are 15- to 16-inches in the C-segment and up to 20-inches in luxury models. Although larger wheels are a mixed blessing for chassis engineers, they are welcomed by brake engineers as they offer more space for larger discs.
“Wheel designs have been a focal point in car styling for many years,” said David Yates, commercial and marketing manager, Europe, for Alcoa Wheel Products – Forged Speciality Wheels. “As a result, in the last decade conventional cast wheels have become larger and, thus, a lot heavier. Alcoa’s forged aluminium wheels are much lighter allowing the OEM to have a larger wheel without adding weight. In fact, our forged wheels are usually lighter than the smaller cast wheels they replace. This not only reduces weight but also helps to reduce the mass moment of inertia, giving engineers more options regarding braking and suspension. In addition, a lighter wheel will reduce un-sprung weight on a car, increasing vehicle performance and feedback to the driver on steering and braking.”
Styling flexibility, reduced weight and high quality are just some of the requirements automakers expect from their wheel suppliers today. To enhance wheel appearance, Alcoa has developed Dura-Bright technology, now available for its automotive forged aluminium wheel customers. Alcoa’s Dura-Bright technology surface treatment has been offered on commercial vehicles since 2003 and more recently on passenger cars. The first to launch in Europe is Audi on its new A6 model. The company points out that traditional alloy wheels rely on lacquer as a finish and protection against the elements. During heat cycling, brake dust and grime can penetrate the lacquer to create a yellow discolouration or black specs that cannot be removed. The company claims that its Dura-Bright penetrates the surface of the wheel to become an integral part of the aluminium itself. It resists peeling, cracking and corrosion while offering a premium finish. “Our customers have stated that the discolouration of wheels is one of the most common complaints by consumers,” sates Yates. “This is caused by brake dust and other particulates becoming trapped in the clear coat applied to wheels. Once this happens this dust can never be cleaned off and the wheels will always look dirty. Dura-Bright technology eliminates this problem making the wheel completely resistant to dirt, brake dust, oil and road grime. Additionally, the wheels are very easy to clean and have superior corrosion performance and so stay looking great for a long, long time.”
See also: Global market review of road wheels – forecasts to 2016 (download)