Despite the global economic downturn putting a damper on vehicle production, Matthew Beecham finds out how shock absorber manufacturers are thriving.
The term ‘shock absorber’ is a misnomer because the device doesn’t, in the strictest sense, absorb shock at all. The shock absorber is designed to dampen the movement of the springs – be they coil, leaf or torsion bar – limiting the road shock transmitted through the tyre, wheel, hub and spring mount. Bushings absorb the rest.
From a technical perspective, the main forces driving the engineering of conventional shock absorbers include weight reduction (through the diameter size reduction and the use of more performing materials and light alloys), noise reduction (through the use of valves performing a progressive damping), and reduction of rod sliding friction (through the use of sealings having new design and materials).
Weighty issues of the day
In summing-up some general trends in the shocks market, Sven Arend, Member of the Management Board, ThyssenKrupp Bilstein Suspension GmbH, told us: “Recently, the big issue has been weight reduction. Consequently, the question of whether aluminium could be a good material to reduce the weight of shocks has been debated. I doubt that will happen at large scale as it is too costly. But we can go with high stress steels in order to get some weight out of the shock. Yet in the current economic climate, the question is: Where do companies focus now? In terms of general weight savings, we had a lot of activities aiming to save weight in the car. For example, to save a kilo in the car, companies were willing to spend between €2.50 and €20, depending on the car manufacturer. Customers are now saying: can we really afford to spend that much money on all components or should we just concentrate in some areas?”
How well do you really know your competitors?
Access the most comprehensive Company Profiles on the market, powered by GlobalData. Save hours of research. Gain competitive edge.
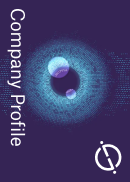
Thank you!
Your download email will arrive shortly
Not ready to buy yet? Download a free sample
We are confident about the unique quality of our Company Profiles. However, we want you to make the most beneficial decision for your business, so we offer a free sample that you can download by submitting the below form
By GlobalDataElectronics is also assuming a prominent role in shock absorber (damper) product development. Electronic dampers allow a large range between maximum and minimum damping levels and adjust instantly to ensure ride comfort and firm vehicle control. By integrating mechanical and electronic functions within a vehicle, automakers improve handling and reduce costs. Such technology can also help lift revenues for manufacturers.
Economic downturn fails to dampen shock innovation
Yet one of the challenges facing shock manufacturers is adding features for very little money. Mike Howarth, managing director, KYB Europe GmbH, told us: “New features of course come at a price, and without investment major new features will not be possible. However, we are continually improving our existing features which in turn provide increased benefits for the motorist. For example, improvements to individual components can increase durability and overall product performance.”
Dr Stefan Sommer, executive vice president of ZF’s Suspension Components division, says that with conventional shocks, the company is seeing an increasing demand for additional features to help OEMs deliver perceivable customer benefits without too much on-cost. He said: “Generally we take the approach to work out mechanical and hydraulic solutions for add-ons to dampers in order to avoid the leap in on-cost of electronic systems. ZF Sachs Sensitive Damping Control is a good example of a system of amplitude selective damping which offers more ride comfort without having to sacrifice safety. An extra valve in the damper provides exactly the right damping force fitting to the actual driving situation: lower damping forces for minor stimulations, such as road bumps, or higher damping for large stimulations, e.g. lane-changes or cornering. This simple and inexpensive system without electronics ensures optimal road contact and makes it possible for the driver to enjoy sporty driving with a constantly high level of ride comfort and safety. In addition we also have the Vario shock absorber in our product portfolio.”
For the last decade or so, the high-end technical emphasis has been on developing shock absorbers in which the damper rate can be varied according to the road conditions, to avoid the compromise in which damping is soft enough to feel comfortable on rough road can create a nauseous “floating” sensation on near-smooth but slightly undulating surfaces. Most designs have concentrated on computer-controlling the opening and closing of valves which bring additional damper orifices into operation, thus the firmest rate exists with all valves closed.
In terms of the possibilities for adaptive damping systems, David Hunt, general manager, Vehicle Dynamics Division, Chassis Systems, Light Vehicle Systems, ArvinMeritor, believes that adaptive damping systems offer an improved safety element in addition to the comfort factor that most manufacturers tout to the consumer. “These systems can change the tyre contact patch loads for improved handling and stability working in conjunction with the ESC and ABS systems. When adaptive damping is integrated with our Active Air System this will further increase vehicle stability and handling.”
Howarth says that, similar to semi active suspension, a unification control system will control all the devices of an electronic system. “The shock absorber will always provide the most suitable damping force by adapting to the road conditions in real time. This type of system has already demonstrated its ability to provide dynamic handling.”
Executives at Magneti Marelli told us that it has been demonstrated that the idea that adaptive damping can improve driver and passenger comfort is only one of the possible advantages. “Adaptive damping can also give a synergic contribution to traditional safety system like ABS and ESP. The key to achieving that is to integrate the adaptive dampers at a system level, including sensors, ECU and mainly control strategies. As a global supplier, Magneti Marelli is focused on this approach and the new Lancia Delta is the first series example of that.”
National differences in shock replacement remain unchanged
While the market for OE shock absorber is clearly linked to vehicle production, the aftermarket can be counter cyclical to the OEM market. Demand for aftermarket shocks is determined by a mix of miles driven, number of vehicles in operation and length of vehicle ownership, which now about eight years – within the prime six-to-ten year vehicle age range for replacement parts. Although more vehicles are on the road than ever before, the aftermarket has experienced longer replacement cycles due to improved quality of OE parts and increases in average useful lives of automotive parts as a result of technological innovation. As a result, the global aftermarket has not grown as fast as the number of vehicles on the road. Consequently, a shock absorber manufacturer’s future viability in the aftermarket will depend, in part, on its ability to reduce costs and leverage its advanced technology and recognised brand names in order to maintain or lift sales revenues.
National characteristics can also affect the aftermarket: at one stage the French shock absorber aftermarket was twice the size of that in the UK despite both countries having approximately the same size of car parc. This is attributed largely to material differences in driver awareness, tolerance and expectation levels.
In explaining certain national differences in driver attitude to replacing shock absorbers, Arend said: “Germans have different driving expectations [to other Europeans]. Most German manufacturers like Audi and BMW therefore differentiate themselves from other manufacturers through high performance ride control. However recently they are putting more emphasis on ride comfort. Other manufacturers are realising that if they really want to gain new customers then they can achieve that by offering a better ride. Yet in markets like the US, France or Japan, ride performance is not a significant criteria of differentiation. A shock you put in the vehicle has to be low cost and durable. The big difference here in Germany is that due to the high speeds requirements for the vehicle ride are high and drivers will quickly notice when shock performance deteriorates. So Germans will typically have the shock replaced more regularly than in other countries. In some other markets, drivers would drive their shocks until they are totally worn out before they replace them.”
Magneti Marelli executives report that the replacement rates in various countries reflect different factors, such as specific standards, the motorists’ tendency to replace worn parts and the quality of the roads. “For example, in Germany, generally speaking, a lot of attention is paid to the efficiency of the vehicle and the quality of products used for replacement and maintenance purposes. The rate of replacement in this country is close to 8%, while in France it is less than 6%. In order to make motorists increasingly aware of the topic of safety, French legislation has recently introduced mandatory checks, at least visual, to be carried out during the servicing phase. Another important aspect to take into account is the number of parts per replacement. For example, if in Greece motorists tend to replace the complete set of front and rear shocks, in Italy the national average is only 2.3 parts per replacement.”
Great potential
Despite the potential of such technologies, it is hard to ignore the gloom in the auto industry at the moment. Mike Howarth prefers to put a more positive spin of today’s situation. He told us: “No matter how bad the condition of auto industry, it is so large and so important an industry, that there will always be enormous opportunities to generate sales and profit by meeting the needs of one’s customer, and ultimately the end consumer. The issue is that this process just became a lot more difficult, and therefore we all have to re-examine what we are doing and how we are doing it, and quickly make changes and continuous improvements. If we can do this, we can survive and prosper and there is no need to be gloomy.”
Matthew Beecham
‘Beechy’
See also: Global market review of shock absorbers – forecasts to 2016 (download)